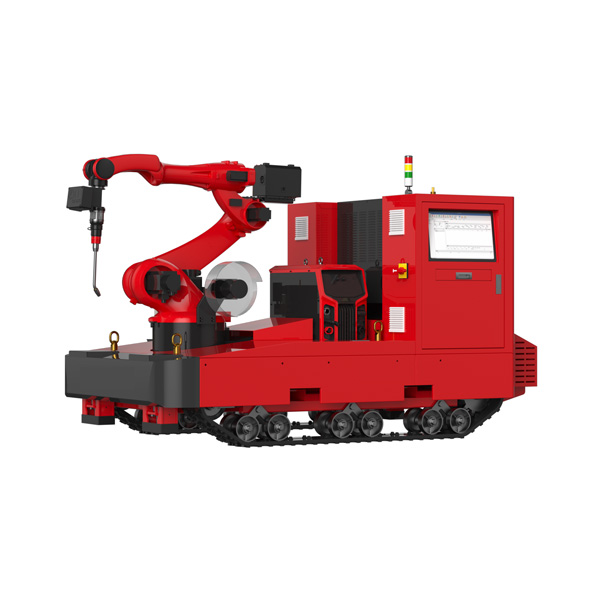
Mobile welding robots are changing how industries work in 2025. These smart machines offer great accuracy and speed. Look at these amazing facts:
- AI-powered cameras help weld with a precision of ±0.2 mm.
- Pipeline projects across countries finish 30% faster than before.
- A shipbuilder in Norway saves $2.8 million yearly by fixing fewer mistakes.
These robots boost work output and make jobs safer.
Key Takeaways
- Mobile welding robots work faster and make fewer errors. This helps industries complete tasks quickly and correctly.
- AI makes welding more accurate. Robots can adjust to materials and conditions for better work.
- Tools that check in real-time give quick updates. This ensures good welds and avoids expensive mistakes.
1. RoboWeld X5
Key Features
The RoboWeld X5 is a top-notch mobile welding robot built for accuracy and speed. It has an AI-powered camera system that makes precise welds, even in tough spots. Its small size helps it move easily in tight areas. The robot’s multi-joint arm can handle tricky welding jobs with great flexibility. It also has a cooling system that stops it from overheating, so it works smoothly for long hours.
Pros and Cons
Pros:
- Very accurate with AI-guided welding.
- Small and easy to move, perfect for tight spaces.
- Strong build for lasting industrial use.
Cons:
- Costs more upfront than regular welding tools.
- Needs trained workers for setup and care.
Unique Innovations
The RoboWeld X5 has a special feature: it finds and fixes mistakes while welding. This uses smart learning to cut down on errors and wasted materials. Another cool feature is its ability to switch between welding types like MIG, TIG, and arc welding. This makes it useful for many industries. Its simple controls make it easy to program and adjust for different tasks.
2. EVS Mobile Intelligent Vision Welding / Cutting Robot
Key Features
Flexible placement of workpieces
The workpiece can be placed freely without the need for fixture positioning.
Good product mobility
More precise omnidirectional movement, suitable for working environments with flat and hard surfaces.
Dual mode of autonomous navigation and manual remote control, easy to operate.
The range of arm extension lifting is expanded, suitable for welding higher workpieces (lifting version).
3D Visual Recognition
No programming or teaching required, independently scan the workpiece model and extract weld seam information.
AI technology
AI technology utilizes machine vision and deep learning to achieve “welding as soon as possible”, accurately identifying weld seams and autonomously adjusting parameters, improving welding intelligence and automation, and adapting to complex scenes and high difficulty tasks.
For more information about this product, please visit: https://www.evsint.com/product-category/mobile-intelligent-vision-welding-cutting-robot/
3. AutoArc Mobile 3000
Key Features
The AutoArc Mobile 3000 is a dependable mobile welding robot. It has two arms that can weld at the same time. This saves both time and materials. Its smart path-planning helps it move through tricky spaces easily. The robot uses a thermal imaging system to check heat levels while welding. This stops materials from getting damaged. Its small size and strong wheels let it move in tight or rough areas.
Pros and Cons
Pros:
- Two arms make work faster.
- Small and easy to move in tight spots.
- Heat-checking system ensures safe welding.
- Built tough for hard conditions.
Cons:
- Needs frequent software updates to work well.
- Setting it up takes extra time.
Unique Innovations
The AutoArc Mobile 3000 has smart adaptive welding intelligence. It changes settings based on material type and thickness. This keeps the welds high-quality. Another great feature is its self-diagnostic system. It spots problems early, so repairs happen before breakdowns. These features save time and improve work efficiency.
Did you know? The AutoArc Mobile 3000 cuts welding mistakes by 40%. It’s a big help for industries needing accuracy and saving money.
4. FlexiWeld 360
Key Features
The FlexiWeld 360 is a flexible and useful mobile welding robot. It works well in tricky industrial spaces, thanks to its smart design. You can program it fast using the ‘teach-by-demonstration’ programming method, which doesn’t need much training. Its collision detection sensors and emergency stop buttons keep workers safe. The robot’s accuracy helps save time, materials, and energy during welding.
Here’s a simple breakdown of its key features:
Feature | Description |
---|---|
Flexibility | Adjusts to different layouts, making it great for tight spaces. |
Easy Programming | Uses a ‘teach-by-demonstration’ method for quick setup. |
Safety Features | Has collision sensors and emergency stops for safety. |
Efficiency | Cuts weld time, saves materials, and uses less energy. |
Pros and Cons
Pros:
- Works well in different spaces and setups.
- Easy to program with simple controls.
- Keeps workers safe with advanced safety tools.
- Saves money by using less energy.
Cons:
- Battery life is shorter than other robots.
- Needs frequent checks to stay accurate.
Unique Innovations
The FlexiWeld 360 has a 360-degree mobility system. This helps it move easily in tight or rough areas. Its smart material recognition changes settings based on the material type. This ensures every weld is high-quality. These features make it a great pick for jobs needing precision and flexibility.
Pro Tip: Want a robot that’s safe, efficient, and flexible? The FlexiWeld 360 is a smart choice.
5. SmartWeld AI
Key Features
The SmartWeld AI is a high-tech mobile welding robot made for accuracy and flexibility. Its AI-driven welding system checks materials instantly to make perfect welds. The robot’s compact design helps it fit into small spaces easily. With self-calibration technology, it sets itself up, saving time. It also has cloud connectivity, so you can control it from anywhere.
Feature | Description |
---|---|
AI-Driven Welding | Checks materials instantly for accurate and clean welds. |
Compact Design | Small size makes it great for tight workspaces. |
Self-Calibration | Adjusts settings on its own, cutting setup time. |
Cloud Connectivity | Lets you monitor and control it remotely with ease. |
Pros and Cons
Pros:
- Super accurate with smart AI adjustments.
- Small and works well in many setups.
- Saves time with self-calibration and remote controls.
Cons:
- Needs steady internet for cloud features to work.
- Costs more upfront than older welding robots.
Unique Innovations
The SmartWeld AI has predictive maintenance alerts that warn about problems early. This reduces breakdowns and keeps it working longer. It also supports multi-material compatibility, so it can weld different materials without extra setup. These features make it a great choice for industries needing reliable and efficient tools.
Did you know? The SmartWeld AI cuts welding mistakes by 50%. It’s perfect for jobs needing high precision.
6. WeldBot Navigator
Key Features
The WeldBot Navigator is a mobile welding robot made for tough jobs. It uses autonomous navigation with LiDAR sensors to map and move easily. This helps it find the right spot for welding every time. Its dual-camera vision system makes welding more accurate by spotting points clearly. The robot’s rugged design lets it work in very hot or cold places and rough areas.
Feature | Description |
---|---|
Autonomous Navigation | LiDAR sensors help it move and position itself correctly. |
Dual-Camera Vision | Finds welding spots with great accuracy. |
Rugged Design | Works well in extreme heat, cold, and tough conditions. |
Long Battery Life | Runs nonstop for up to 14 hours. |
Pros and Cons
Pros:
- Moves through tricky spaces without trouble.
- Very accurate welding with dual cameras.
- Strong and works well in bad conditions.
- Long battery life for all-day use.
Cons:
- Needs skilled workers to set it up.
- Costs more to fix because of advanced parts.
Unique Innovations
The WeldBot Navigator has real-time obstacle avoidance to stay safe in busy areas. Its adaptive welding algorithms change settings to match materials, keeping welds perfect. You can also use its remote monitoring feature to check on it from far away.
Pro Tip: Need a robot for hard jobs and exact welding? The WeldBot Navigator is a great pick.
7. OmniWeld Pro
Key Features
The OmniWeld Pro is a flexible mobile welding robot made for tough industrial jobs. Its multi-axis robotic arm works with great accuracy, even on tricky shapes. The robot uses AI-powered material recognition to change settings for different materials automatically. Its compact design helps it move easily in small spaces. The OmniWeld Pro also has real-time thermal monitoring to stop overheating and keep welds steady.
Feature | Description |
---|---|
Multi-Axis Arm | Handles detailed welding tasks with high precision. |
AI Material Recognition | Adjusts welding settings for different materials automatically. |
Compact Design | Fits and moves well in tight areas. |
Thermal Monitoring | Stops overheating to ensure steady weld quality. |
Pros and Cons
Pros:
- Very precise for detailed welding work.
- Adjusts to different materials without manual changes.
- Small size makes it easy to use in tight spots.
- Thermal monitoring keeps welds consistent.
Cons:
- Needs skilled workers to use it well.
- Costs more than simpler welding robots.
Unique Innovations
The OmniWeld Pro has dynamic weld path optimization, which finds the best welding route instantly. This saves materials and improves work speed. It also has remote operation capability, letting you control it from anywhere using a secure cloud system. These features make the OmniWeld Pro a great pick for industries needing accuracy and efficiency.
Pro Tip: Want a robot that’s smart, precise, and advanced? The OmniWeld Pro is a great choice.
8. ArcMover 5000
Key Features
The ArcMover 5000 is a powerful mobile welding robot made for tough industrial jobs. Its dual-arm system lets it weld on two surfaces at once, making work faster. The robot uses AI-powered path optimization to find the best welding routes quickly. Its all-terrain mobility system helps it move easily on bumpy or rough ground, perfect for construction and shipyard tasks. It also has real-time thermal sensors that check heat levels to stop material damage.
Feature | Description |
---|---|
Dual-Arm System | Welds two surfaces at the same time to save time. |
AI Path Optimization | Finds the best welding routes instantly. |
All-Terrain Mobility | Moves smoothly on rough or uneven ground. |
Thermal Sensors | Checks heat to keep materials safe. |
Pros and Cons
Pros:
- Dual arms make work faster and more efficient.
- Works great on uneven or rough surfaces.
- Stops overheating with smart thermal sensors.
- AI path planning saves materials and time.
Cons:
- Needs skilled workers to set up and maintain.
- Costs more than simpler welding robots.
Unique Innovations
The ArcMover 5000 can weld on many surfaces at once, making it great for tricky projects. Its self-learning AI system adjusts to different materials and conditions for better results. The robot’s modular design allows easy part replacement or upgrades without stopping work.
Did you know? The ArcMover 5000 cuts welding time by 35%, making it perfect for big industrial jobs.
9. MobileFusion X
Key Features
The MobileFusion X is a modern mobile welding robot built for efficiency and comfort. It has a climate-controlled cab that keeps operators safe and comfortable. This helps them focus better and work faster. The robot also has a self-contained mobile fusion compressor with special cooling technology. This feature makes it weld up to 150% more than older machines.
Feature | Description | Performance Impact |
---|---|---|
Climate-controlled cab | Keeps operators safe and comfortable while working. | Improves focus and boosts productivity. |
Self-contained mobile fusion compressor | Uses cooling technology to speed up welding tasks. | Increases daily production by up to 150%. |
Pros and Cons
Pros:
- Works faster with advanced cooling features.
- Comfortable cab design helps operators stay focused.
- Built strong for long-term use in industries.
Cons:
- Costs more upfront than simpler robots.
- Needs regular care to keep working well.
Unique Innovations
The MobileFusion X uses adaptive fusion technology to change settings based on materials. This keeps welds smooth and consistent. Its modular design lets you swap parts or upgrade without stopping work. These features make it great for industries needing flexible and efficient tools.
Did you know? The MobileFusion X cuts downtime by 40%, making it perfect for big projects.
10. WeldTech Rover
Key Features
The WeldTech Rover is a flexible mobile welding robot made for tough jobs. Its 360-degree rotational arm helps it weld in tight spots. The robot uses autonomous navigation with LiDAR and GPS to move easily in tricky areas. Its multi-material compatibility lets it weld different metals like steel and aluminum. The smart cooling system stops it from overheating, so it works well for long hours.
Feature | Description |
---|---|
360-Degree Rotational Arm | Reaches tight spaces for accurate welding. |
Autonomous Navigation | Moves smoothly using LiDAR and GPS systems. |
Multi-Material Capability | Welds different metals without needing changes. |
Smart Cooling System | Keeps the robot cool for nonstop work. |
Pros and Cons
Pros:
- Rotational arm makes welding in small spaces easy.
- Moves well in hard-to-reach places.
- Works on many materials, saving time.
- Cooling system keeps it running for long hours.
Cons:
- Costs more than simpler robots.
- Needs skilled workers to operate it well.
Unique Innovations
The WeldTech Rover has real-time weld quality monitoring. This uses AI to fix mistakes as they happen, saving materials. Its modular design lets you change parts or upgrade without stopping work. Another great feature is its energy-efficient power system, which uses 30% less energy, making it eco-friendly.
Pro Tip: Want a robot that’s precise, adaptable, and saves energy? The WeldTech Rover is a smart choice.
AI Integration in Mobile Welding Robots
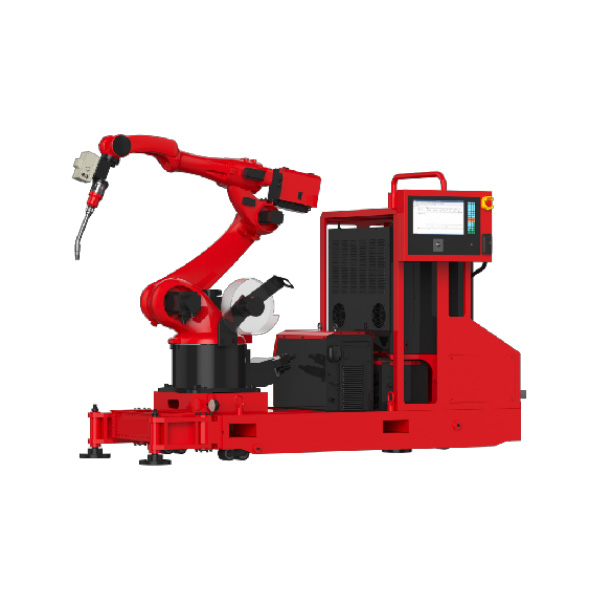
Improving accuracy and flexibility in welding tasks
AI has changed how mobile welding robots work, making them more accurate and flexible. Smart systems and advanced programs now help these robots perform better in tough industrial jobs.
- Better Welding Settings: AI tools like the Taguchi method find the best welding settings. These tools keep welds consistent and reduce mistakes during work.
- Improved Predictions: AI models like neural networks and genetic algorithms predict welding results better. This reduces errors and makes the process more efficient.
- Live Monitoring: Special cameras track the welding process in real time. They catch problems early, lowering the chance of defects.
AI also helps robots handle tricky tasks like uneven weld lines or hard-to-control settings. For example:
- Smart Edge Detection: Image tools help robots find welding edges accurately for clean starts.
- Flexible Path Planning: Adaptive algorithms adjust settings to handle complex welding paths.
- Smooth Movements: AI systems improve robot movements, making them faster and smoother.
These improvements are already helping industries, like in Finland, where AI boosts welding control. As AI grows, mobile welding robots will become even more precise and efficient in the future.
Real-Time Monitoring for Welding Quality
Using data to boost accuracy and efficiency
Real-time monitoring has changed how welding quality is checked. It gives quick feedback and useful tips to improve work. This helps keep welds consistent and lowers mistakes and delays. Tools like WeldEye Quality Control, used by Aker Solutions, track welding details automatically. This removes the need for manual checks and meets industry rules.
- Quick Alerts: These tools warn you right away if something goes wrong. You can fix issues fast to keep welds accurate and avoid problems.
- Saving Money: Automating quality checks cuts costs and helps companies stay competitive.
- Better Records: Digital systems make it easier to keep and review project files.
Aker Solutions says their digital system gives them almost full control over welding. This has made their work faster and reduced errors a lot.
Examples show how real-time monitoring helps. For example, machine learning in laser welding reached 71% to 99% accuracy in spotting different welding events. It can tell stable from unstable conditions, stopping problems like pores. With results in just 2 milliseconds, these tools work instantly in factories.
Using real-time data gives you more control over welding. It makes work faster, ensures better results, and saves money, making your projects more dependable.
Pro Tip: Use real-time monitoring tools to improve quality and avoid expensive fixes.
Enhanced Mobility for Complex Environments
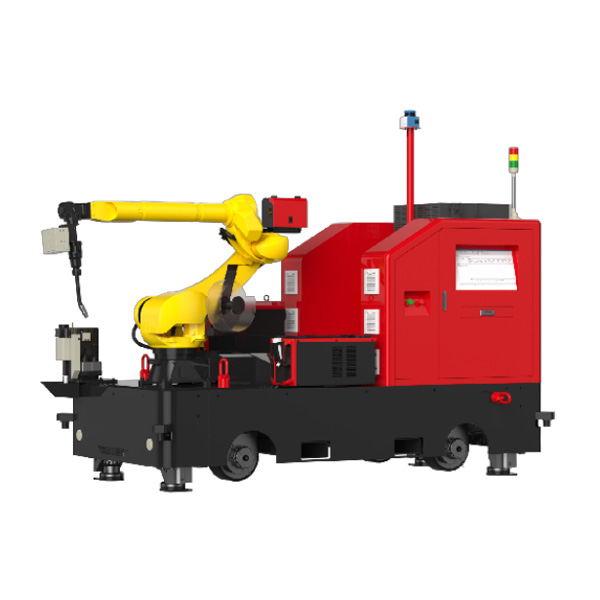
New technologies help robots work in tough spaces
In 2025, mobile welding robots come with advanced mobility tools. These tools help them move easily in tricky industrial areas. Robots can now handle tight spots, uneven ground, and busy work zones with great accuracy and speed.
Here are some key mobility improvements:
- Advanced Inertial Sensors
Robots now use special sensors like MEMS and FOG IMUs. These sensors give accurate movement data, even when GPS signals are weak. They are very stable, with errors as low as 0.001°/hr. - AI-Driven Navigation Systems
AI-powered systems combine data from many sensors to plan paths. These systems are better than older methods and adjust quickly to changes in the environment. - Acoustic Positioning Solutions
Robots use USBL systems with AI to work underwater or in noisy places. These systems provide exact location and direction details. - Cloud Ground Control
A cloud-based platform helps manage multiple robots at once. It gives real-time updates, making it easier to control robots during big projects.
Innovation Type | Key Features | Performance Metrics |
---|---|---|
Advanced Inertial Sensors | MEMS and FOG IMUs, temperature-stable, fast data output | Errors as low as 0.001°/hr |
AI-Driven Navigation Systems | Uses AI and sensors for better path planning | Beats older navigation methods |
Acoustic Positioning Solutions | USBL systems with AI for underwater and noisy areas | Accurate location and direction info |
Cloud Ground Control | Cloud platform for managing robot fleets | Real-time updates for smooth operations |
These upgrades make robots more dependable in hard-to-reach places. From narrow pipes to rough construction sites, they work with precision and save time.
Pro Tip: Pick robots with smart mobility tools for better results in tough spaces.
In 2025, mobile welding robots have transformed how industries work. These robots help finish jobs quicker and with steady quality. They make work safer by handling dangerous tasks and avoiding crashes with sensors. Using tools like 3D vision, they save time during setup and work better. Using these advanced robots keeps you competitive in the industry.
FAQ
Which industries gain the most from mobile welding robots?
Industries like construction, shipbuilding, automotive, and aerospace benefit greatly. These robots boost productivity, lower mistakes, and handle tough welding jobs well.
How do mobile welding robots keep workers safe?
They have safety tools like collision sensors and emergency stops. Real-time monitoring also helps reduce dangers in risky workplaces.
Are mobile welding robots a good choice for small businesses?
Yes, they cut material waste, save time, and reduce labor costs. Though they cost more at first, they save money over time for small businesses.
Pro Tip: Think about your needs and budget before buying a mobile welding robot to get the most out of it.