The intelligent production line for tunnel rebars with robot welding represents a breakthrough in tunnel construction. This system integrates intelligent monitoring and automation to deliver unmatched efficiency and precision. Robots with high precision operate continuously to ensure consistent welding quality and minimize human error. This automated process, unlike traditional methods, increases production capacity, reduces labor intensity and creates a safer working environment. The ability to maintain 24-hour operations is a standard in intelligent manufacturing. It transforms construction workflows, and improves project outcomes.
Automating and Precision in the Welding Robot Tunnel Intelligent Production Line
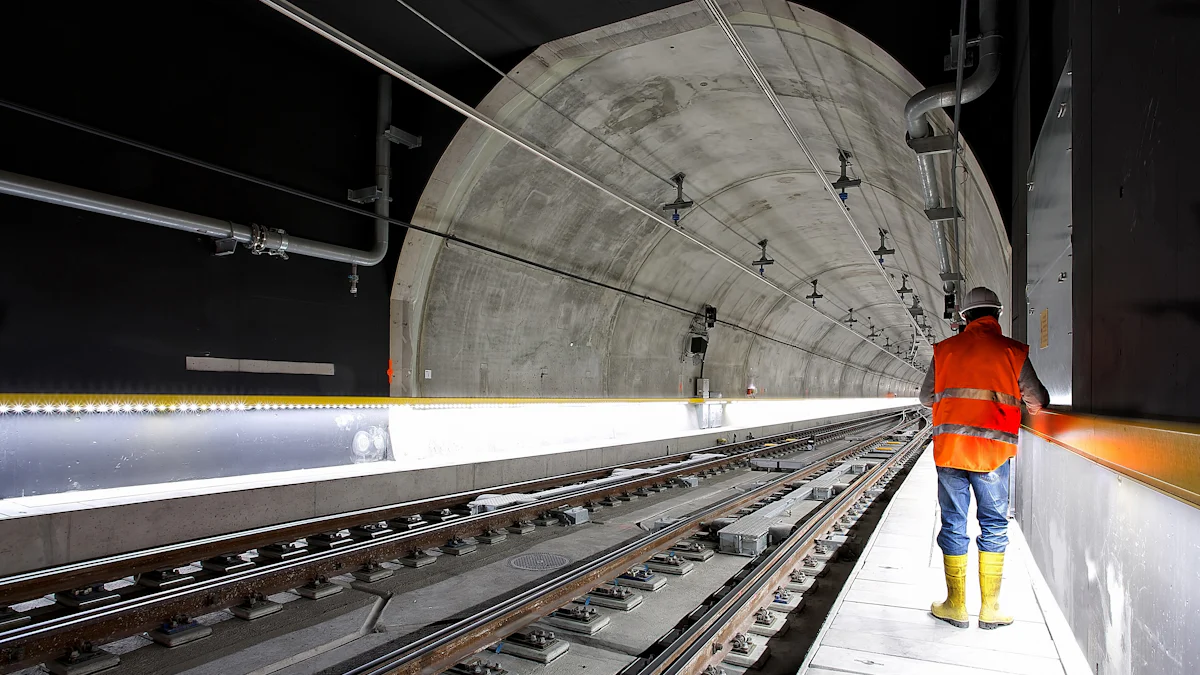
Advanced Robotic Systems
The Robotic Tunnel Rebar Intelligent Production Line, with its cutting-edge robotic systems, redefines automation and precision for construction. These systems use advanced technologies to streamline processes and increase productivity. Robots with high precision perform welding tasks with incredible accuracy. This ensures consistent quality throughout all stages of production. Robots can adapt to different welding scenarios without any manual intervention thanks to the integration of 3D intelligent vision technology.
These robotic systems are characterized by their ability to work continuously and support 24/7 production. This feature increases production capacity and efficiency. EVS’s ‘Navigator welder’ is a flexible machine that combines robotic control with flame cutting systems and 3D vision to provide seamless operation. These advances not only increase welding accuracy, but also reduce human errors. They set a new standard for intelligent manufacturing.
Advancement Type | Description |
---|---|
You can also find out more about the Automated Vehicles by clicking here. | The system is able to achieve a fully automatic and intelligent cutting process that increases efficiency. |
The following are some of the most effective ways to increase your effectiveness: | The use of high-precision robots improves the accuracy and quality of welding. |
Flexibility | The EVS “Navigator Welder” features flexible welding technology and intelligent 3D vision. |
Integration of Technologies | Combining control of the robot, flame-cutting system, and 3-D vision allows for seamless operation. |
Continuous Production | The project will support 24/7 production and increase capacity and efficiency. |
High-Precision Sensors
The accuracy of the Robot Tunnel Rebar intelligent production line is largely dependent on high-precision sensors. These sensors allow for precise seam tracking and positioning of the workpiece, which is essential to achieving high quality welds. The production line can be made more efficient by implementing intelligent monitoring systems.
Sensors also help to exceed industry standards for welding accuracy. They can detect environmental changes and adapt accordingly, ensuring stable performance regardless external conditions. This technology advancement improves the welding results, but also reduces labor intensiveness. It creates a safer and efficient working environment.
Tip By integrating high-precision sensors with advanced robotic systems, the Welding Robot Tunnel Rebar Intelligent Production Line is able to deliver unmatched precision and reliability.
The Intelligent Production Line for Tunnel Rebar Welding Robots is Fast and Efficient
Workflow Streamlining
The Intelligent Production Line is a robotized production line that optimizes the entire production process. The fully automated system ensures a smooth workflow, from the raw material handling up to the final assembly. Robots with intelligent monitoring systems perform tasks precisely, reducing the delays caused by errors made by humans.
Integration of industrial network control enhances coordination among multiple machines. This feature allows for coordinated operations and multi-robot cooperation. Robots can perform simultaneous tasks like cutting, welding and stacking. This reduces production time. Modular design allows for quick adjustments and ensures uninterrupted operation even if project requirements change.
Note An efficient workflow is not only a great way to speed up production, but it also helps ensure a consistent level of quality. This is incredibly important for large infrastructure projects.
Increased output
Production output is dramatically increased by the ability of the production line to run continuously, 24 hours a day, 7 days a week. Robotic systems that work at high speeds can complete tasks quicker than the traditional methods. This allows for more units to be produced in a shorter period of time. Modern technologies such as 3D seam recognition ensure that quality is not compromised by speed.
The adaptability of the system to different rebar configurations and sizes further increases productivity. It maximizes efficiency by eliminating the need to make frequent manual adjustments. This technology has led to a 50% increase of production capacity for companies using it, setting new standards in tunnel construction.
Tip This production line is ideal for projects that have tight deadlines or high output requirements.
Welding Robot Tunnel Rebar Intelligent Production Line: Customization and Flexibility
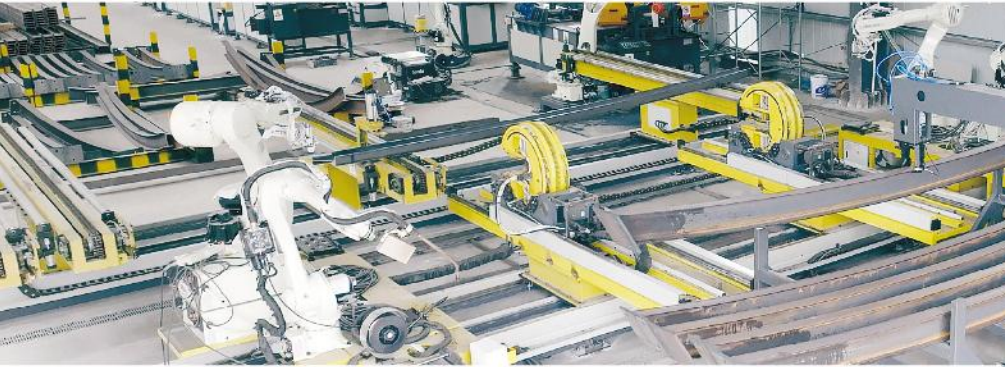
I-Beam Arch Bending Automatic Production Line
Adaptability to Project Requirements
The Intelligent Production Line for Tunnel Rebars and Welding Robots is a flexible solution that can meet a wide range of project needs. The advanced design of the system allows it to perform complex tasks with efficiency and precision. The system integrates many processes seamlessly, from material buffering and aligning to robotic welding and product placement. The production line is flexible enough to meet a variety of construction requirements.
This table shows examples of how the system can be used to meet project requirements.
Project Requirement Description |
---|
Material buffering and feeding to the alignment mechanism. |
I-Beam alignment. |
Robotic continuous weld. |
Robotic endplate front welding |
Robotic placement of upper end plates. |
Feeding the C-Type positioning machines. |
Unloading of material by the material feeding mechanism. |
Cutting to size with a saw |
Cold bending machine to arch. |
Flipping and positioning C-Type positioning machines. |
Robotic endplate back welding. |
Unloading C-Type positioning machines by flipping them. |
Unloading automatically by means of the unloading device. |
Place the finished product on the material rack. |
The production line’s adaptability allows it to meet the specific needs of every project. This increases its usefulness in different construction scenarios.
Modular Design
Modular design allows for easy configuration adjustments, allowing the system to adapt to specific production requirements without compromising efficiency. The modular design of the welding Robot Tunnel Rebar Intelligent Production Line allows for simple configuration adjustments. This allows the system to be adapted to specific production needs without compromising on efficiency. Modular design simplifies maintenance, upgrades and ensures long-term reliability.
Below is a table that outlines the various configuration options available.
Configuration Type | Description |
---|---|
Single-line | Simple production requirements can be met with a simple layout. |
Dual-machine parallel lines | Increased production capacity with flexibility. |
Shared lines for multiple machines | This allows for large-scale production, while still being able to adapt to changing demands. |
The modularity of the system allows it to be scaled up or down according to project requirements, resulting in a cost-effective solution for tunnel construction. The system is able to meet the needs of the construction site by offering customized configurations. This further cements its position as the leader in intelligent manufacturing.
Tip Modular design not only increases flexibility, but also minimizes downtime when reconfiguring the system. This ensures uninterrupted operations.
Welding Robot Tunnel Bar Intelligent Production Line Safety Features
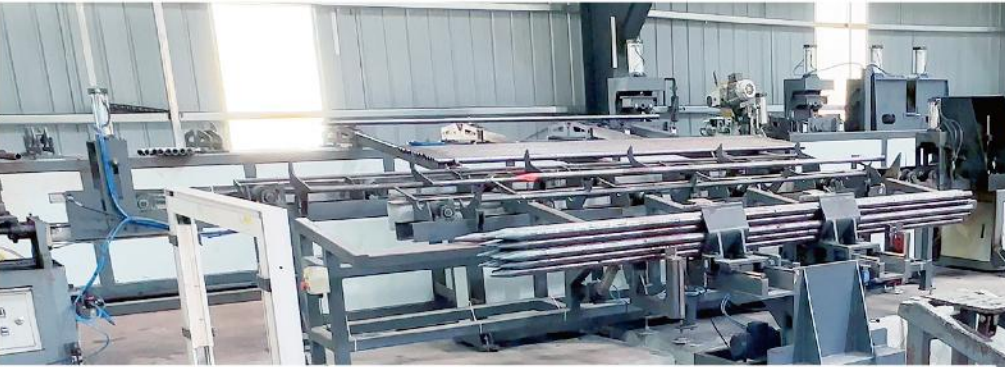
Small Pipe Automatic Production Line
Worker protection mechanisms
The Welding Robot Tunnel Rebar Intelligent Production Line puts worker safety first by integrating technologies that reduce risk. Intelligent monitoring systems and high-precision robots perform complex tasks with a lower risk of human error. Automation reduces the direct involvement of humans in potentially hazardous processes. This creates a safer work environment. The system reduces fatigue and repetitive strain injuries at work by reducing the labor intensity.
The design of the production line ensures that workers are kept at a safe distance away from potentially hazardous operations. Robots with 3D-vision technology and adaptive controls can perform tasks with extreme accuracy, eliminating manual adjustments. This method not only improves the safety, but also overall efficiency. The ability of the system to run continuously without human interaction further reduces worker exposure to risk, setting a standard for worker safety in construction.
Notes: Intelligent monitoring and advanced automation systems are crucial to maintaining high levels of productivity while protecting workers.
Equipment Safety
To minimize operational risk, the Intelligent Production Line for Welding Robot Tunnel Rebar incorporates robust safety features. These features make sure that the machine operates efficiently and reliably under various conditions. Safety measures include:
- Automating processes reduces human error.
- Robots with high precision that improve monitoring capabilities and detect issues early.
- Continuous production capability, which reduces labor intensity and improves operational safety.
Modular design of the system also helps to improve equipment safety, by simplifying maintenance procedures and reducing downtime. Intelligent sensors continuously monitor machinery and alert users to any anomalies. This proactive approach ensures that equipment will not fail and perform consistently. These safety features not only protect workers, but also increase the life expectancy of the components. This makes the production line a good choice for large projects.
Tip Regular maintenance, and intelligent monitoring system ensures that the production line runs safely over time.
Maintenance and Durability for the Welding Robot Tunnel Rebar intelligent Production Line
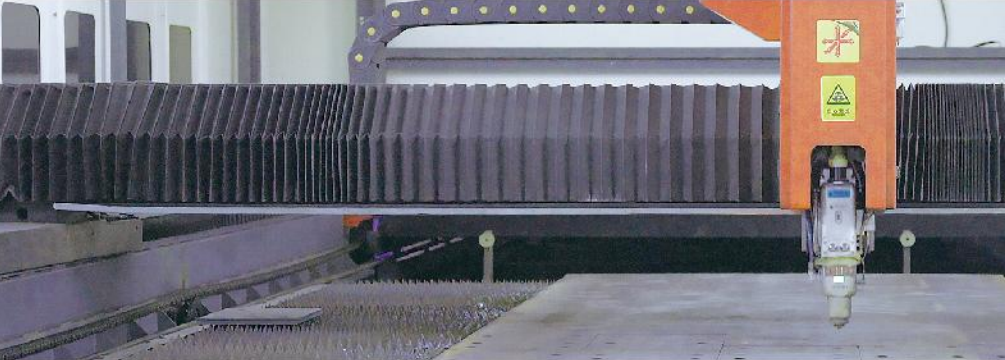
End Plate Cutting Automatic Production Line
Long-Lasting Components
To ensure durability, the welding Robot Tunnel Rebar Intelligent Production Line uses advanced materials and technology. The design incorporates robust components, such as steel sheet cutting systems, I beam cold bending mechanisms and precision-driven robotic welding units. Together, these elements create a production system that can withstand the constant demands of operation.
The system uses intelligent control systems that monitor the entire workflow from the raw steel processing through to the final steel arches. This ensures a consistent product and increases the life of the equipment. It is important that the production line can form strong steel arch supports for tunnel construction. Structural integrity is important. The system’s unmatched durability and reliability is achieved by using high-grade materials, cutting-edge technologies and advanced processes.
- Key Features of Long-Lasting components :
- Steel plate cutting is a precise way to prepare materials.
- Cold bending of I-beams for precise shaping.
- Robot welding to create strong and consistent joints.
- Intelligent control systems for seamless operation.
This feature not only increases the life of the production line, but also reduces the need to replace it frequently. It is a cost-effective option for large-scale projects.
Easy Maintenance
Modular design of the production line simplifies maintenance and ensures minimal downtime. The modules can be accessed individually, which allows technicians to make repairs or replace parts without disrupting the system. This design ensures that there are no operational delays.
Intelligent monitoring systems improve maintenance efficiency. These systems can provide data in real time on the performance of equipment, which allows for early detection. The system generates alerts that allow proactive maintenance and prevent costly breakdowns. High-quality components reduce wear and tear. This in turn reduces the frequency of maintenance.
- Maintenance Advantages :
- Modular design allows for easy and quick maintenance.
- Monitoring in real-time for early detection of issues
- Components of high quality that are resistant to wear.
- Reduction in downtime through efficient repair processes
The welding Robot Tunnel Rebar Intelligence Production Line combines advanced monitoring with an easy-to-use design to ensure long-term reliability and ease-of-maintenance.
Welding robot tunnel rebar intelligent production line: Applications and use cases
Tunnel Construction Projects
The Welding Robot Tunnel Rebar Intelligent Production Line revolutionized tunnel construction, addressing critical challenges with rebar production. The advanced robotic systems, intelligent monitoring capabilities and minimal human involvement ensures continuous production. This innovation was successfully implemented by many Global 500 enterprises where it significantly increased production efficiency and decreased labor intensity. The system eliminates human errors by automating tasks like cutting, bending and welding.
The production line is essential in tunnel construction for creating strong steel arch supports that are vital to structural stability. The ability of the production line to run 24/7 allows teams to meet deadlines while maintaining quality. Its ability to adapt to different rebar sizes, shapes and configurations enhances the system’s utility. This technology streamlines the production process and sets new standards for efficiency in tunnel construction.
Broad Infrastructure Applications
The welding Robot Tunnel Rebar Intelligent Production Line is not only used in tunnel construction but also for a variety of infrastructure projects. Its precision and versatility make it an asset for reinforcing structures in concrete and fabricating rebar. Applications include:
- Cutting rebar into specific lengths and bending the required shapes automatically, ensuring consistency in fabrication.
- Pre-made rebar mats and cages are produced for prefabricated construction, which speeds up on-site assembly.
- Automating the placement and coverage of reinforcement within concrete structures.
- To improve durability, reinforce critical infrastructure, such as bridges and dams.
- The high volume of steel rebar needed for high-rise building construction, while ensuring structural integrity and speeding up the construction process.
These applications show the system’s flexibility to meet diverse construction requirements while maintaining accuracy and efficiency. The production line improves infrastructure projects’ safety and durability by automating labor intensive processes.
Tip This system is ideal for projects that require precision and scalability.
The welding Robot Tunnel Rebar Intelligent Production Line has redefined tunnel construction with its advanced automation, precision, and safety features. Robotic systems ensure exact dimensional accuracy in rebar cutting and bending, reducing material waste and optimizing reinforcement layouts. This precision enhances structural integrity while significantly increasing productivity and shortening project timelines. Additionally, robotic welding technology surpasses industry standards, improving welding quality, reducing labor intensity, and lowering operational risks.
The system has measurable benefits, including increased efficiency, improved security, and lower costs. This makes it a vital tool for construction projects of the modern era. Construction professionals can improve project outcomes by adopting this technology. This will set new standards in intelligent manufacturing.
Call for Action: This innovative solution will ensure precision, safety and efficiency on every project.
The FAQ
What is the main purpose of the Intelligent Production Line for Welding Robot Tunnel Rebar?
The system automates the production of rebar for tunnel construction. The system integrates advanced robots with intelligent monitoring in order to improve precision, efficiency and safety. It ensures consistency in quality, and speeds up project timelines by reducing the need for manual intervention.
How does the production line improve worker safety?
The system reduces the need for humans to perform hazardous tasks. Robots with 3D Vision Technology can handle complex operations and reduce risks. Intelligent monitoring systems can detect issues before they become serious, creating a safer working environment.
Can the production line adapt to different project requirements?
The system is modular and has flexible configurations. The system can accommodate a variety of rebar shapes, sizes and production scales. Its adaptability allows it to be used for a variety of construction projects, such as tunnels, high-rises and bridges.
What maintenance features does the system offer?
Modular design allows for independent access to all components, simplifying maintenance. Intelligent monitoring systems provide real-time performance data, enabling proactive issue detection. High-quality materials ensure long-term reliability by reducing wear and tear.
Is the system suitable for large-scale infrastructure projects?
Absolutely! Production line runs 24/7 and increases output significantly. The precision and adaptability of the machine make it perfect for large-scale projects that require high-quality rebars such as tunnels and skyscrapers.
Tip To maximize efficiency, schedule routine maintenance and use the intelligent monitoring features of your system.