Industrial painting robots offer numerous advantages over their human counterparts: They can perform repetitive tasks without growing weary; eliminate errors and save both time and money due to reduced rework; as well as perform many more complex functions than humans can, saving both both.
These robotic workhorses can be mounted anywhere – from floors and ceilings, rail systems and overhead gantries, even explosion-proof environments!
Most painting robots feature hollow three-roll wrists equipped with rotary atomizers for precise application of coatings, increasing their reach while decreasing wear on connections and cables, as well as mitigating contamination risks.
The following is the application performance of industrial painting robots in various industries:
Automotive
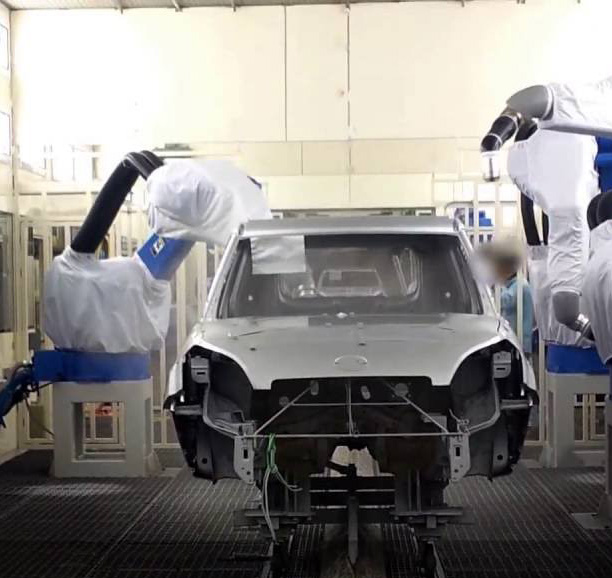
Automakers increasingly depend on painting robots to provide consistent, high-quality paint jobs on their cars. Robots have proven adept at handling an accelerated production cycle without compromising quality or performance; helping manufacturers meet consumer demand without compromising either.
Paint robots employ special industrial coatings designed to provide added protection against factors like corrosion, abrasion and chemical exposure – thus prolonging their components and materials’ lifespan.
To maximize robot performance, look for systems equipped with force torque sensors. These sensors provide real-time feedback about forces and torques being experienced by the end-effector, enabling adjustments to be made dynamically to improve application precision and adaptability.
Select a robot model that supports offline programming to minimize programming time and eliminate rework. With this approach, trajectories for your robot can be created and tested virtually before being sent into production – saving both time and reducing rework costs. Also look for models that allow easy floor, wall or ceiling mounting options for optimal flexibility.
Aerospace
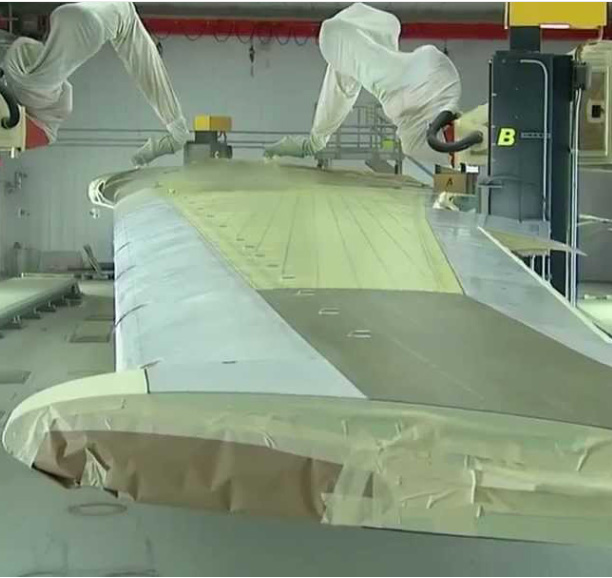
Boeing relies on painting robots as an integral component of lean manufacturing efforts in order to maintain aircraft with fresh appearances, which contribute to higher production rates and reduce production waste.
Aircraft manufacturers have discovered that using robot painters increases production while saving money and decreasing exposure to hazardous chemicals.
Aerospace painting robots can be programmed to paint complex structures with different textures, or even different colors on one surface, while also being capable of adjusting how much paint they apply – helping eliminate waste while providing optimal thickness levels.
Aerospace painting robots can be safely deployed in hazardous Class 1 Division 1 environments, providing a cost-effective alternative to human workers. When selecting an aerospace paint or coating robot, the following factors should be taken into consideration: payload capacity matching the weight of materials being handled and enough reach arm to access hard-to-reach spots; intuitive programming software is also something worth keeping an eye out for.
Consumer Electronics
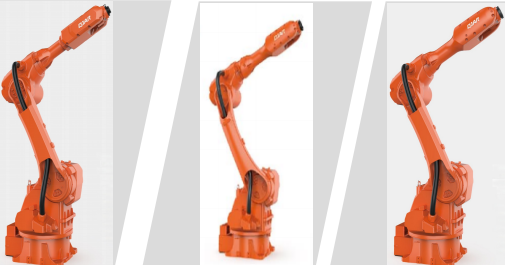
Painting robots have become an indispensable component of consumer electronics production, used to apply specialty coatings with precise accuracy to electronic components. Their use requires high levels of consistency and accuracy – which explains their increasing popularity within this sector.
Robots provide flexible industrial solutions, from applying clear coat to protect delicate components to electrostatic paint that provides structural integrity – these industrial robots can do it all! Additionally, multiple coats can be easily applied at once for increased durability and aesthetics.
When selecting the ideal robot for your application, look for one with a high payload capacity and reach. Furthermore, look for an intuitive programming system so you can adjust its trajectories instantly on-demand.
Choose a robot capable of using either water-based spray paint or powder paint and make sure that your facility can accommodate this by considering whether a dedicated area or spray booth is needed for its operation. Furthermore, ensure the robot meets ATEX regulations to avoid deflagration.
Home Appliances
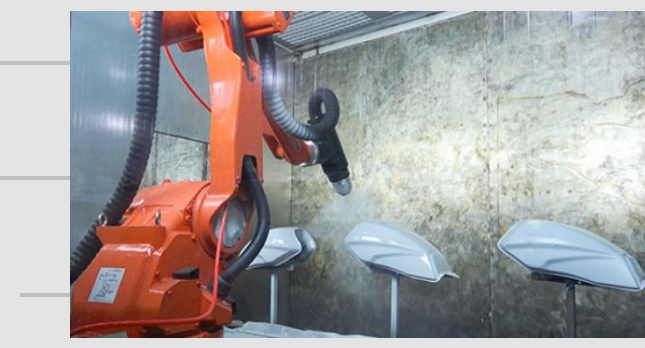
Painting robots use advanced algorithms, software and in-built cameras to deliver industrial paint evenly with unmatched accuracy. Furthermore, these bots can identify spots needing painting in real-time without masking or other manual processes – saving companies both labor costs and production time.
Robotic spray paint systems can work continuously without tiring, leading to increased productivity and quality improvements. They are also more adept at handling harsh solvents and chemicals, helping companies reduce material waste as well as potential OH&S risks.
Though these systems require some human supervision, they reduce complexity by eliminating complex programming needs and increasing accuracy compared to manual operations. Painting robots also help eliminate costly rework rates and production delays while speeding up production times significantly. Furthermore, some painting robots are tailored specifically to modern manufacturers – including being able to handle different paints and materials efficiently – for instance the MYRO indoor paint robot takes simple commands from an iPad to quickly optimize production space with its floor plan work order function – perfect for companies that need quick solutions that quickly optimize production space as quickly as possible!
Furniture Manufacturing
Furniture industry production lines rely heavily on robotic paint robots for high-quality, consistent results. Painting robots provide precise, even coats of paint on wooden cabinet doors, metal stairways and other furniture components – with large workspaces accommodating even the most hectic production lines.
Furniture manufacturing companies can integrate painting robots into their wood finishing operations to decrease waste, speed up production and enhance finish quality. These robots work round-the-clock and deliver steady output to meet market demands; freeing up floor space while shifting workers to more beneficial roles.
When selecting furniture manufacturing painting robots, look for models that can easily integrate into existing lines and apply coatings that suit the type of coating needed. Also ensure there is enough payload capacity for materials and paint applicator weight; program interface must be user-friendly and adapt to various applications easily.
Heavy Equipment and Machinery
Industrial painting robots offer manufacturers an effective tool to boost quality, productivity and profitability by spraying continuously without fatigue and consistently, thus reducing waste material and rework costs while at the same time minimising their environmental footprint by limiting VOC emission rates and other pollutants.
When selecting a paint robot for your facility, look for advanced features like force torque sensors and collision detection. These technologies allow the robot to accurately assess its environment, applying paint evenly across surfaces of different geometry and surfaces – this ensures consistency, reduces rework/waste costs and prevents potential damages to itself or equipment it is painting.
Consideration should also be given to how your robot fits into existing production processes, and its integration. Depending on your industry, modifications to production lines or installing compatible hardware and software interfaces may be required in order for the robot to function smoothly. Also important: selecting a manufacturer with comprehensive onboarding and continuous support services so your team can ramp up quickly without encountering downtime.
Shipbuilding
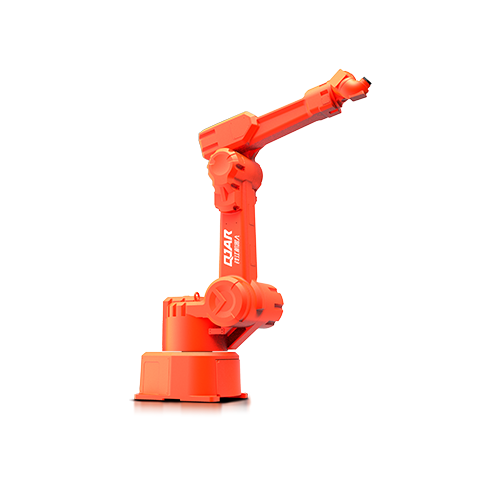
Large sea vessels require protective paint coatings to safeguard them against corrosion, abrasion and other environmental conditions. Painting robots are capable of applying these coatings faster and more accurately than human painters – increasing quality while shortening docking time.
Painting robots that excel are self-contained systems that can complete multiple functions simultaneously in one stage, thus reducing the number of changes needed between functions. Furthermore, these painting robots can operate in environments with high ambient temperatures, salt fog and wind; integrated systems designed by Generic Systems for SRG Global provide user friendly graphical user interfaces along with process tracking features and memory backup for optimal operation.
When choosing a paint robot, payload capacity should be taken into account to ensure it can support the weight of materials and applicator. Make sure it has sufficient degrees of freedom to reach all areas of the workpiece and look for an atomizer (the business end of paint tool) which dispenses coating directly onto it. Also ensure it fits seamlessly with existing systems in your facility or consider investing in an explosion proof model capable of operating safely within Class 1 Division 1.
Construction Materials
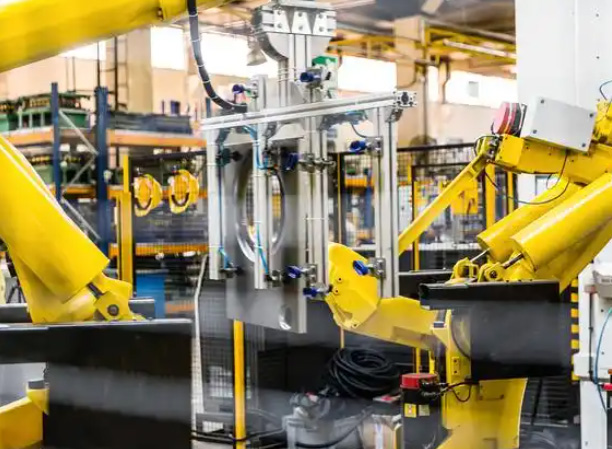
Painting robots are unmatched workhorses, applying coatings 30 times faster than human labor. Their consistent application ensures uniform results while minimising waste and rework while improving quality control and improving safety. Furthermore, these robotic painters can handle corrosion-resistant or fire retardant paints for applications.
When selecting a painting robot, take into account the size and complexity of items to be painted as well as types of paint or coatings you intend to use and production volumes. If incorporating it into an existing production line, look for one which allows for seamless integration by matching its path with conveyor speeds and trajectory.
When handling flammable liquids, selecting a robot with closed loop paint process control is crucial for success. This feature monitors fluid flow to eliminate problems like over or under film build-up as well as reduce waste. For added safety reasons, consider choosing one with hollow wrist so cables and paint tubes can run inside rather than through its arm; also take into consideration whether your environment requires dusty environments or can accommodate dust particles in its workspace.