Mobile robots will change the way you manufacture. Mobile Intelligent Vision Welding Robots by EVS Robotics are among the most advanced machines available. They bring precision and efficiency unmatched to your production line. They simplify complex tasks, and decrease setup time by leveraging cutting edge technologies like 3D visual recognition. They are ideal for intelligent production line that demands flexibility and consistency.
These robots can help you achieve greater productivity and lower costs. The robots’ ability to run continuously provides seamless automation, without compromising on quality. Their precise execution reduces waste and saves resources, while maintaining superior quality. Mobile welding robots are a cornerstone in modern production because of these features.
Mobile Welding Robots: Benefits and Features
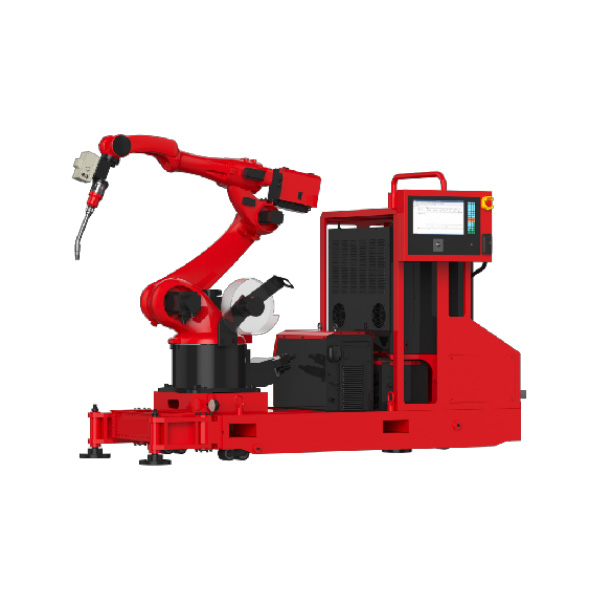
Productivity Increases
Mobile Welding Robots increase productivity by streamlining the welding process. They can perform welding processes faster and with greater consistency, which ensures uninterrupted operations. These robots use advanced features such as 3D visual recognition that reduce setup time through autonomously identifying workpieces and weld seams. This eliminates the need to manually program, allowing for greater efficiency in high-volume production.
- Mobile welding robots have shown measurable benefits for companies.
- Precision in execution reduces waste and rework.
- Increased throughput reduces downtime, and increases the life of consumables.
- Productivity is improved by lowering labor and energy costs.
You can increase your production efficiency and maintain high quality welds by integrating robotic welding into your intelligent production lines.
Cost Savings
Mobile welding robots can save you money by automating the welding process and reducing waste. Precision ensures less errors which reduces rework, and improves the quality of control. The labor cost per part produced is lower with robotic welding than manual welding. Robotic welding cells also optimize the use of resources, including power and wire. This reduces costs.
- Some examples of cost-savings include:
- Increased output and reliable scheduling help to meet orders efficiently.
- Accident-related costs can be reduced by assigning dangerous tasks to cobots.
- The use of gas optimization stations and spatter-removal stations can extend the life expectancy of consumables.
You can reduce your operational costs and still maintain superior welds by using cobot welding systems.
Safety is Improved
Workers are exposed to heat, sparks and hot metal in traditional welding processes. Mobile welding robots reduce these risks by automating welding and incorporating advanced security features. Safety is ensured by collision detection sensors and emergency stops buttons.
- The following are some of the safety benefits of cobot weld:
- Reduced exposure to hazardous environment
- Reduced medical costs and improved worker’s health
- Intelligent monitoring systems can improve workplace safety.
Integrating mobile robots in your production will create a safer work environment for your staff while maintaining high quality results.
Flexible – Enhanced
Mobile welding robots offer unmatched flexibility for your production line. They can adapt to a variety of layouts thanks to their mobility and omnidirectional movements. These robots can be deployed in small spaces and reconfigured quickly to meet changing demands. This flexibility ensures your operations are efficient even in complex layouts and limited floor space.
- Examples of real-world flexibility in action include:
- Robots that are programmed with ” Teach by Demonstration ” excel at low-volume tasks and products that change frequently.
- Compact and mobile, they are ideal for small spaces. This maximizes the production area.
- Businesses can adjust their operations based on the market demand and maintain competitiveness.
Their versatility is further enhanced by their ability to perform complex cutting and welding tasks. These robots can identify weld seams, and adjust parameters in real-time using advanced AI features. It ensures that the robot can perform precisely, even under difficult conditions. EVS Robotics’ Mobile Intelligent Vision Welding Robot, for example, uses 3D visual recognition technology to scan workpieces autonomously and extract information about the weld seam. It eliminates manual programming and saves time.
Features | Description |
---|---|
Easy Programming | The mobile welding robots use a ‘teach-by-demonstration’ method to simplify the programming process. |
Efficiency | Precision allows for significant reductions in weld times, waste material, and energy consumption. |
Scalability | The small footprint of the mobile units and their mobility make it easy to set up in different production environments. |
Versatility | Nine Axis Cantilever Welding has a wide range of accessories to improve handling and quality. |
Integrating a mobile robot for welding into your production gives you the flexibility to adapt to changing needs and tackle different tasks. This will ensure that your production remains efficient, precise and ready to face future challenges.
How to Integrate Mobile Welding Robots Effectively
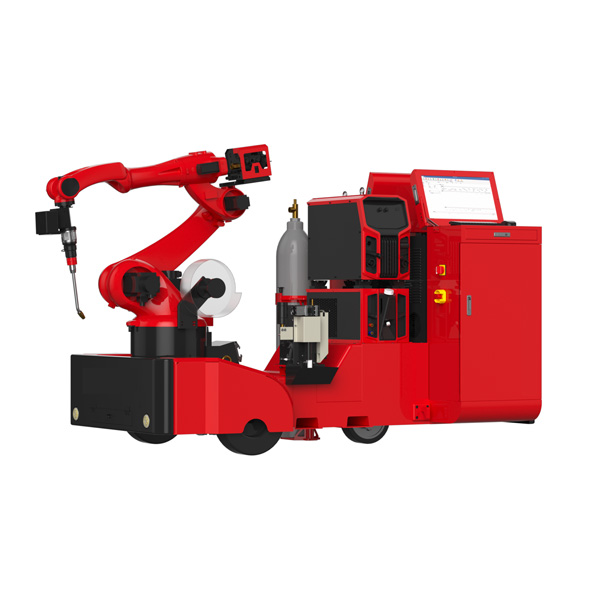
Assessment of Production Needs
You must first evaluate your requirements before integrating a mobile robot welding into your production line. Start by identifying the challenges you face in your welding processes. Find out if issues such as inconsistent welds, high labor costs or production bottlenecks affect your operation. This will allow you to decide where robot automation can be most beneficial.
When assessing your needs, consider the following:
- Know your welding requirements including the materials you use and the production volume.
- Calculate the initial costs of your investment, including software installation and updates.
- Check the safety features of your system and its user-friendliness.
- In tight spaces, mobile robots must have flexibility and mobility.
- To maintain safety mechanisms, plan regular inspections and functional testing.
You can improve productivity and efficiency by analyzing all these factors.
The Right Mobile Welding robot
It is important to choose the right mobile robot for high efficiency and precision. Pay attention to factors such as payload capacity, accuracy, and compatibility. The RX Series Weld Process Library is a feature that can handle complex tasks and makes it ideal for intelligent production line.
Key Features | Description |
---|---|
Safety Features | Included are collision detection sensors and emergency stops buttons to reduce operator risks. |
Easy of Programming | Many robots use “teach-by-demonstration”, simplifying the set-up process. |
Flexibility | Mobile robots are easily movable to accommodate different production requirements. |
Total cost of ownership | When evaluating your options, consider the initial investment as well as installation and maintenance costs. |
These features will ensure seamless integration of your robot into your production line, and maximize the benefits from welding automation.
Ensure compatibility with the production line
Integrate the robot welding with your existing software and machinery systems to ensure compatibility. This minimizes interruptions and maximizes the efficiency of your workflow. Start by verifying that the robot tool centers align with your production needs. Check and clean the fixturing regularly to ensure performance.
Follow these best practices to ensure smooth integration
- Implement an preventive maintenance program on the robot and peripherals.
- Verify that the robots are operated by trained personnel.
- Create a layout to optimize the placement of robots.
Fixturing components in the right position is essential for repeatable, precise welds. The correct fixturing of components is also important. You can maximize the potential of robotic welders by designing workflows with accuracy and efficiency in mind.
Training and Skill development
Provide comprehensive training for operators and maintenance staff
Your team will be able to operate and maintain mobile welding robots effectively with the right training. To maximize the performance of the robot, operators and maintenance personnel must be familiar with its features and capabilities. Comprehensive training programs can help to build confidence and reduce mistakes during operation.
Prioritize training that emphasizes safety, programming and troubleshooting. Many leading manufacturers offer courses that are tailored to particular applications. These courses teach essential skills such as using teach pendants to program and understanding the navigation system of the robot. Teach pendants make it easy for operators to program welding tasks.
Here is a brief overview of the most effective training methods.
Evidence | Description |
---|---|
Welding robots should only be operated by trained technicians | To ensure safety and efficiency, only qualified individuals should be involved in programming. |
Use of teach pendants | As recommended by OEMs, this is essential for programming welding robots. |
Resource from OEMs | The best brands offer courses all year round and training for specific applications. |
These training programs will ensure that your staff can use the advanced features of the robot with ease.
Building internal expertise for troubleshooting, optimization and optimization
Your team will be able to optimize workflows and troubleshoot problems independently if you develop internal expertise. It reduces the need for external support, and downtime is reduced. Encourage your employees to get hands-on training with the mobile robot welding during training sessions. The robot’s behavior can be better understood by exposing them to real-world situations.
You can create a culture of knowledge sharing within your company. The exchange of tips and best practices between operators and technicians will improve overall efficiency. Keep your team up to date with regular workshops and refresher classes.
Your team will be able to adapt to changing production requirements if you build internal expertise. You can maximize the potential of your mobile robot by hiring skilled operators and technicians.
Integration: Challenges and Solutions
High Initial Investment
At first, investing in mobile welding robotics such as those that are used to weld robot tunnel rebar can appear expensive. You can make better decisions by exploring your financing options and performing a return-on-investment (ROI) calculation. Financing options like leasing or Robotics-as-a-Service (RaaS) allow you to spread costs over time, making robotic automation more accessible. As an example:
Financing Option | Description |
---|---|
Lease | Spread payments over 3-7 years for easier cash flow management. Upgrade technology option. |
Robotics-as-a-Service (RaaS) | Subscription model with predictable costs is ideal for SMEs that want to grow without high costs. |
Understanding the financial benefits of ROI is easier with an ROI analysis. You can, for example:
- Investment for a robot welder: $120,00
- First-year total cost: $125,000
- Savings potential in the first year: $50,000
- Annual savings of $95,000
- Payback period: approx. 2.5 years
To maximize efficiency and productivity, prioritize areas with high impact. Robotic welding cells are best suited for tasks that require precision and repetitive actions.
Training and Learning Curve
It can be difficult to adapt to mobile robots, particularly for jobs like welding robot tunnel bar. Manufacturer-supported training programs simplify this process. These programs show operators how to use “teach-by-demonstration” features, which make programming intuitive and reduce setup time. The operator can improve their skills by working with robots. This combines human expertise and robotic technology.
Partnering with experts will ensure seamless knowledge transfer. Experts can help your team with programming, safety protocols and maintenance. This collaboration will minimize inefficiencies, and give your team confidence to operate robotic welding cells.
Maintenance and Downtime
To keep your robots working smoothly, preventive maintenance is vital. Create a schedule for maintenance that includes cleaning fixtures, checking connections and inspecting consumables. Cleaning stations and spatter-removal systems can help reduce downtime, and prolong the life of MIG torches.
As an example:
- Cleaning stations increase productivity by reducing the accumulation of debris.
- Spatter removal systems improve throughput and reduce replacement frequency.
Access spare parts and technical assistance to resolve issues quickly. Maintenance during production pauses will minimize disruptions, and keep your intelligent production line running efficiently.
Integration Complexity
Collaboration with System Integrators to Ensure Smooth Implementation
System integrators can help you integrate mobile welding robots seamlessly into your production line. These professionals have the expertise to design and install robot systems that are tailored to your needs. A structured approach will help you get the best results.
- Planning and Assessment – Start by evaluating the current processes. Identify the areas that automation will add value. Together with your integrator, create a plan outlining your goals and requirements.
- Design & Build : Work with your integrator to create a robotic system tailored to your needs. Customization allows the robot to be aligned with your workflow, ensuring optimal performance.
- Installation & Testing: Install robotic system, and test thoroughly. The robot must be tested to ensure it meets your performance requirements and that it operates correctly.
- Support and Training: Teach your team how to maintain and operate the system. The integrator’s ongoing support helps to address any problems and ensures success over the long term.
Tip : Select an integrator who has experience in your field. Their expertise can streamline processes and reduce challenges.
Follow these steps to integrate mobile welding robots seamlessly and reap their benefits.
Test and iterate Workflows before Full-Scale Implementation
Test workflows prior to full-scale deployment. This will minimize disruptions and increase efficiency. Start by running the robot under controlled conditions. You can identify any potential problems and make necessary adjustments without impacting production.
Simulation tools can be used to fine-tune the robot’s program. These tools allow you to visualize the robot and its movements, and optimize performance. Implement the robot on a small part of your production line after initial testing. Monitor the robot’s performance and get feedback from your operators. This feedback can be used to improve workflows and eliminate inefficiencies.
Note : Iterative testing is a way to ensure that the robot will adapt to your production needs. This reduces the chance of error during full-scale deployment.
You can make sure that the robot is operating at its maximum efficiency by testing and iterating your workflows.
Practical Tips to Optimize Automated Welding Efficiency
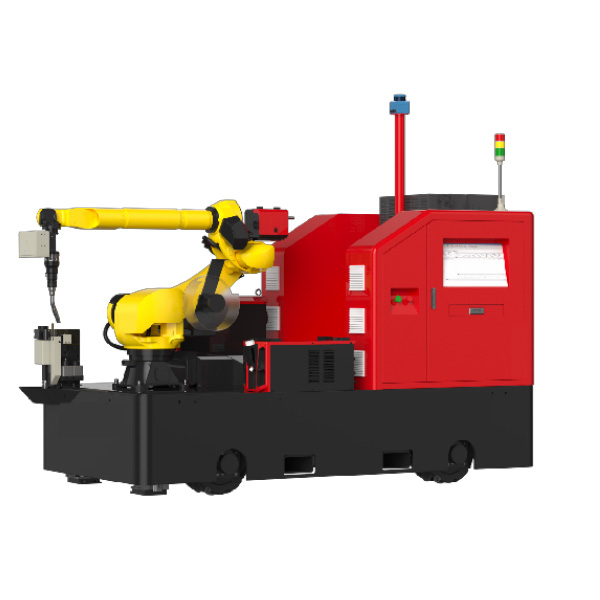
Best Practices in Programming
Simulation tools can be used to improve welding and cutting programs
Simulators are essential for optimizing robotic weld cells . You can refine your welding and cutting programmes before implementing them. This reduces costs because it avoids unnecessary expenses and downtime. Programming can be done before installation, which can reduce production time. Simulation software also enhances the design capabilities of robotic systems, making them safe and functional before they are used in real life.
- The following are some of the benefits of using simulation tools:
- Reduce costs by better planning and fewer mistakes.
- Reduced production time by enabling immediate processing following installation.
- Improved design capabilities to ensure safer and more efficient operations.
You can increase the accuracy and efficiency of automated welding processes by using simulation tools.
Standardizing programming protocols for consistency and efficiency
Standardizing your programming protocols will ensure consistency in your intelligent production line. By using uniform methods you can reduce errors and increase the reliability of robotic weld cells. This also simplifies maintenance and troubleshooting. For example, the use of a teach pendant to program cobot welding systems will ensure accurate and repeatable outcomes. Standardization allows you to maintain high productivity and precision in your operations.
Regular Maintenance and Inspections
Routine checks are essential to ensuring optimal robot performance
Regular inspections will ensure that your robot tunnel rebar system is performing at its best. Regular inspections can help identify problems like errors in programming, mechanical issues, and power supply issues. By addressing these issues proactively, you avoid unexpected downtime or costly repairs. Verifying code and debugging are two ways to resolve programming issues, while lubrication, part replacements and lubricants can address mechanical wear.
Preventing downtime by proactively addressing wear and tear
Maintaining your robotic welding cell is easy with proactive maintenance. Create a maintenance plan that is tailored to your needs. Include tasks such as inspecting connections and cleaning fixtures. Replace worn components. Consider contracting maintenance for daily and proactive support. Quality spare parts will ensure compatibility and performance of your cobot welder.
Data and Analytics: Leveraging Data and Analytics
IoT and Sensor Technologies: Monitoring Robot Performance
IoT technologies and sensor technology provide real-time insight into the performance your welding robots. The moneo Real-Time Monitoring System, for example, tracks motor performance and detects overload situations. It can also predict issues such as wire feed problems. These insights enable you to prevent failures from occurring and ensure your robotic welding cell operates efficiently.
Data insights can be used to reduce costs and improve operational efficiency.
Data analytics can transform automated welding processes. Data analytics can be used to improve weld quality and prevent failures by using predictive maintenance. You can also identify inefficiencies by analyzing weld data and optimize resource usage. Documenting welding processes continuously improves safety, and records are kept. You can increase productivity and precision of your intelligent production line by leveraging data.
Continuous Improvement
Feedback from the operators and production team for improvements
By actively obtaining feedback from your operators and production team, you can unlock the potential of mobile welding robots. They can give valuable insight into the performance of robots as they interact with them daily. They can often identify areas of improvement that were not immediately evident during the initial deployment.
Create a feedback system that is structured. To collect feedback, use surveys, suggestion boxes or regular team meetings. Encourage operators to share what they know, such as the challenges they face or features that they find most useful. Production teams can also identify inefficiencies or suggest improvements to robot integration.
Tip : Reward and recognize valuable feedback. This will encourage your team to actively participate in the improvement process.
Analyze feedback to identify themes or issues that are recurring. Consider additional training or updates to software if, for example, multiple operators have reported difficulty with a particular programming feature. This information can be used to improve workflows, increase robot performance and smooth operations.
Update robot software to meet changing needs
Updating your mobile welding robots ensures that they will remain effective even as your production requirements change. Software updates are a great way to improve functionality, eliminate bugs and add new features. These updates can improve the robot’s capability to perform complex tasks or adapt new materials and designs.
Plan periodic software reviews for your robot. Check for any updates from the manufacturer such as firmware upgrades, new programming tools or other updates. Install these updates as soon as possible to ensure peak performance.
Note : Before updating programs or settings, always make a backup to prevent data loss.
Upgrade hardware components as necessary. Addition of advanced sensors and AI modules, for example, can increase precision and adaptability. Staying proactive will ensure that your robots deliver quality results and can meet the needs of modern production lines.
Mobile welding robots, like the Mobile Intelligent Vision Welding Robot by EVS Robotics, redefine how you approach production. These advanced systems enhance productivity by streamlining workflows and reducing errors. Their precision minimizes material waste, while their flexibility allows seamless adaptation to diverse production line layouts. By automating tasks like welding robot tunnel rebar, you can achieve consistent quality and improved efficiency.
Planning and training are essential for the successful integration of robotic welders. Long-term success is achieved by addressing challenges like initial investment and maintenance. These robots offer unmatched precision and scalability with features such as cobot welding, intelligent production line adaptation and cobot. Automation allows your business to remain competitive in an industry that is rapidly changing.
Tip Investing mobile welding robots will not only reduce labor costs, but also increase production speed. This ensures that your operations are efficient and future-ready.