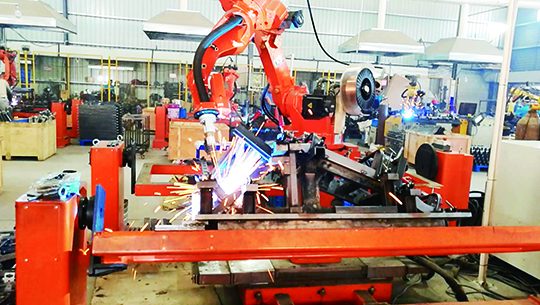
Welding robots have transformed manufacturing by offering precision and efficiency. These robotic welding systems range in cost from $10,000 to over $500,000, depending on their type and features. Factors affecting welding robot prices include end-effectors, safety equipment, and software. The global welding automation market is growing rapidly, with the automotive sector contributing 40% of revenue in 2024. Investing in welding robots reduces waste, improves productivity, and ensures consistent weld quality. The advantages of robotic welding make it a valuable addition to industries like automotive, aerospace, and heavy machinery.
Key Takeaways
- Welding robots cost between $10,000 and over $500,000. The price depends on the type and features. Knowing these costs helps plan for automation.
- Buying welding robots can cut labor costs by 50%. They also boost productivity, making them a smart choice for factories.
- There are different welding robots, like Cartesian and articulated arm robots. Pick the right one based on what your factory needs.
- Safety gear is very important when using welding robots. Spending on safety keeps workers safe and follows rules.
- Most welding robots save enough money to pay for themselves in 1-3 years. They work faster and waste less, making them a good long-term buy.
Types of Welding Robots and Their Pricing
Cartesian Welding Robots
Price Range: $10,000-$50,000 (can exceed $100,000 with advanced end-effectors)
Cartesian welding robots are a cost-effective option for manufacturers looking to automate linear welding tasks. These robots excel in applications like spot, TIG, MIG, and laser welding. Their design makes them suitable for large work areas, offering precision and reliability. If your production line involves repetitive, straight-line welding, Cartesian robots provide an excellent balance between functionality and affordability.
Robot Type | Functionality | Cost Range |
---|---|---|
Cartesian Robots | Suitable for large work areas, excels at spot, TIG, MIG, and laser welding | $10,000 – $50,000 |
Articulated Arm Welding Robots
Price Range: $50,000-$500,000+
Articulated arm welding robots are the most versatile option for complex welding tasks. These robots can bend, twist, and rotate, making them ideal for hard-to-reach areas. Their high precision ensures consistent weld quality, even in challenging angles. You can rely on them for various tasks, including welding, painting, and packing. This flexibility makes them a valuable addition to industries requiring adaptability.
- Flexibility for days: These robots can bend, twist, and rotate in ways that make other robots jealous.
- Nails it every time: They’re accurate, consistent, and won’t mess up just because they stayed up late binge-watching a show.
Robot Type | Functionality | Cost Range |
---|---|---|
Articulated Arm Robots | High precision, can perform any type of welding, excels in difficult angles | $50,000 – $500,000 |
SCARA Welding Robots
Price Range: $10,000-$50,000
SCARA welding robots are compact and efficient, making them perfect for small and medium-sized manufacturing operations. These robots excel in high-speed welding tasks that require precision within a 2D plane. They are particularly effective on assembly lines where time and accuracy are critical. SCARA robots also handle material operations like picking, placing, and transporting items, enhancing their utility in smaller production environments.
Robot Type | Functionality | Cost Range |
---|---|---|
SCARA Robots | Limited to close quarters, perfect for small/medium parts, excels at TIG, MIG, and laser welding | $10,000 – $50,000 |
Collaborative Welding Robots
Features: Work alongside humans, easy to program, and safe for shared spaces.
Collaborative welding robots, also known as cobots, are designed to work safely alongside humans. These robots enhance productivity by allowing you to load and unload parts while the robot performs welding tasks. This seamless collaboration between human workers and automation ensures continuous operation and improved efficiency.
Safety is a key feature of collaborative welding robots. They include advanced mechanisms to protect workers in shared spaces.
Safety Feature | Description |
---|---|
Force-limited joints | Prevents excessive force during operation, reducing the risk of injury to nearby workers. |
Real-time monitoring systems | Continuously checks the environment for human presence, ensuring immediate response to hazards. |
Immediate cessation of operations | Stops the welding process if a human enters a predefined proximity, enhancing safety. |
Programming these robots is straightforward. You can quickly switch between different weld programs and workpieces, store programs for future use, and reduce setup times. This ease of use makes collaborative welding robots an excellent choice for dynamic production environments.
Plasma Welding Robots
Features: Known for precise welds and short cycle times.
Plasma welding robots excel in precision and efficiency. They control the welding torch, arc, and heat application with unmatched accuracy. This results in consistent, high-quality welds that meet the demands of industries requiring precision. The focused plasma arc minimizes spatter and distortion, ensuring clean and reliable welds.
These robots operate at faster speeds than human welders, significantly reducing cycle times. This efficiency increases production throughput, making plasma welding robots a valuable asset for high-volume manufacturing. Whether you need to weld intricate components or achieve flawless seams, plasma welding robots deliver exceptional results.
Resistance Spot Welding Robots
Applications: Common in automotive manufacturing for joining thin metals.
Resistance spot welding robots play a vital role in automotive manufacturing. They are primarily used to join thinner metals, such as sheet metal, which is essential for creating car frames. The process involves applying electric current to heat and bond metal pieces, forming a weld nugget at the spot of application.
- Resistance spot welding is highly economical and widely utilized in automotive assembly lines.
- These robots enhance speed and precision, meeting the industry’s demand for lighter and more precise vehicles.
- Robotic technology has improved efficiency and safety in production, leading to cost savings and increased capacity.
By integrating resistance spot welding robots, you can achieve faster production rates and maintain consistent weld quality, ensuring your manufacturing process stays competitive.
If you want to learn about Mobile Intelligent Vision Welding Robot, please visit: https://www.evsint.com/product-category/mobile-intelligent-vision-welding-cutting-robot/
Additional Costs Influencing Welding Robots Cost
End-Effectors
Costs vary based on application, with specialized tools required for niche industries like aeronautics and defense.
End-effectors play a critical role in determining the functionality and efficiency of welding robots. These tools, attached to the robotic arm, perform specific tasks such as gripping, cutting, or welding. The cost of end-effectors depends on their complexity and the materials they handle. For example, industries like aeronautics and defense often require highly specialized end-effectors to meet stringent quality standards. These advanced tools can significantly increase welding robot pricing. However, investing in the right end-effectors ensures optimal performance and precision, making them a worthwhile addition to your automation setup.
Safety Equipment
Includes enclosures, fume-extraction systems, emergency interlocks, stop buttons, and security fencing.
Safety equipment is essential when integrating welding robots into your production line. It protects workers and ensures compliance with safety regulations. You may need to invest in several components, including:
- Enclosures and fume-extraction systems to remove hazardous particulates.
- Automated emergency interlocks to halt operations during unsafe conditions.
- Emergency stop buttons and protective security fencing to safeguard workers.
These features not only enhance safety but also contribute to the overall cost of welding robots. While the initial investment may seem high, prioritizing safety minimizes risks and ensures smooth operations in the long run.
Software
Tailored software for specialized welding conditions can add to the cost.
Software customization is another factor that influences welding robot pricing. Tailored software adapts robotic welding systems to specific production needs, improving efficiency and reducing waste. However, customization requires additional time and resources, which can increase the upfront cost. Despite this, the benefits often outweigh the expenses. Enhanced operational efficiency leads to higher output and a faster return on investment. By choosing the right software, you can maximize the potential of your welding robots and streamline your automation processes.
Maintenance
Annual maintenance costs vary by provider and robot type.
Maintaining welding robots is essential to ensure their longevity and consistent performance. Annual maintenance costs depend on the type of robot and the service provider. For instance, articulated arm robots may require more frequent servicing due to their complex movements, while simpler models like Cartesian robots might have lower upkeep needs. You should budget for regular inspections, software updates, and replacement of worn-out components. These measures prevent unexpected breakdowns and keep your robotic welding system running efficiently.
Some manufacturers offer maintenance packages that include scheduled servicing and technical support. These packages can save you money in the long run by reducing downtime and extending the lifespan of your equipment. You should also consider training your staff to perform basic maintenance tasks, such as cleaning and lubrication. This proactive approach minimizes wear and tear, ensuring your welding robots operate at peak efficiency.
Tip: Regular maintenance not only reduces long-term costs but also enhances the reliability of your robotic welding system.
Factory Space
Adequate space is needed for robots, safety features, and increased production capacity.
When integrating welding robots into your production line, you must allocate sufficient factory space. A robotic welding system requires a larger footprint compared to semi-automatic welding setups. You need room for the robot, welding power source, and additional equipment like safety enclosures and fume extraction systems. Proper spacing ensures smooth material flow into the welding cell, which boosts productivity.
Crowded workspaces can hinder efficiency and pose safety risks. To avoid these issues, plan your layout carefully. Ensure there is enough clearance around the robot for maintenance and operation. If your facility has limited space, consider compact models like SCARA robots, which are designed for smaller environments. By optimizing your factory layout, you can maximize the benefits of welding robots while maintaining a safe and efficient workspace.
Note: Investing in adequate space upfront can prevent costly adjustments later and improve overall workflow.
Total Cost of Welding Automation and Return on Investment (ROI)
Initial Investment
Significant upfront costs ranging from $10,000 to $500,000+ depending on the robot type and features.
When you consider welding robots, the initial investment can seem substantial. The purchase price alone ranges from $50,000 to over $150,000, depending on the model and features. Installation costs typically add another $10,000 to $25,000. You’ll also need to account for programming, which can cost between $3,000 and $10,000, especially if your welding automation setup requires customization.
Additional expenses include safety equipment like enclosures and ventilation systems, which ensure compliance with workplace safety standards. Monthly operational costs for consumables, such as welding wire and shielding gas, can range from $1,000 to $3,000. Annual maintenance costs, estimated at $2,000 to $5,000, keep your robotic welding system running smoothly. While these costs add up, they lay the foundation for long-term savings and efficiency.
Long-Term Savings
Reduced labor costs, waste, and downtime contribute to cost savings.
Robotic welding systems offer significant savings over time. Unlike human welders, robots work continuously without breaks, reducing labor costs by up to 50%. This uninterrupted operation boosts productivity and minimizes downtime. Additionally, the precision of welding robots ensures fewer defects, which means less material waste and reduced rework. For example, a robotic welder that cuts welding time in half can lower annual labor costs to $50,000 while maintaining quality. These savings allow the system to pay for itself within a few years, making it a cost-effective investment.
Productivity and Efficiency
Robots achieve up to 85% efficiency compared to 20% for skilled human welders.
Welding robots excel in efficiency and consistency. They maintain up to 95% arc-on time, compared to less than 50% for human welders. This means robots spend more time actively welding, leading to higher output per hour. Their precision programming ensures consistent weld quality, reducing defects and improving overall productivity. With efficiency rates of up to 85%, robotic welding systems outperform skilled human welders, who typically achieve only 20%. By integrating welding automation, you can significantly enhance your production capabilities while maintaining high-quality standards.
ROI Timeline
Most welding robots pay for themselves within 1-3 years through increased output and reduced costs.
Investing in welding robots may seem like a significant expense upfront, but the return on investment (ROI) often comes faster than you might expect. Many businesses report that their robotic welding systems pay for themselves in less than three years. In some cases, companies have seen these systems recover their costs in under two years. This rapid ROI is a result of increased efficiency, reduced waste, and lower labor expenses.
The timeline for ROI can vary depending on your industry and production needs. For example:
- A robotic welder that cuts welding time in half could pay for itself in about 2.5 years.
- Some manufacturers achieve ROI in just two years, thanks to significant savings and improved productivity.
- On average, a good robotic welding system should pay for itself within a few years.
The financial benefits extend beyond the initial payback period. Once the system has recovered its cost, you continue to save money through reduced labor requirements and minimized material waste. Robots work faster and more consistently than human welders, which means you can produce more in less time. This efficiency not only boosts your output but also enhances your bottom line.
By choosing the right welding robots for your operation, you can maximize these benefits. Whether you’re in automotive manufacturing or aerospace, the long-term savings and productivity gains make robotic welding a smart investment. With a typical ROI timeline of 1-3 years, these systems quickly transition from an expense to a profit-generating asset.
Tip: To accelerate your ROI, focus on optimizing your production processes and selecting robots tailored to your specific needs.
Advanced Features and Evolving Technology in Welding Robots
Autonomous Robotic Welding
Innovations like machine vision and algorithms eliminate the need for programming.
Autonomous robotic welding has revolutionized how you approach welding tasks. Modern systems now adapt to different welding conditions in real-time, eliminating the need for manual programming. This innovation allows you to save time and focus on other critical aspects of production.
Key advancements include:
- AI-powered vision systems that analyze the weld pool and automatically adjust parameters for optimal results.
- Automated sensing technologies that adapt operations based on workpiece dimensions, ensuring consistent weld quality.
- Real-time data acquisition and analysis to detect faults and correct welding operations instantly.
These features not only improve efficiency but also enhance the precision of your automated welding systems. For instance, robots can now generate their own paths without programming, making them more accessible and user-friendly. This level of automation ensures seamless operation, even in complex welding scenarios.
Adaptability
Robots can handle deviations and high-mix production environments, making them suitable for various industries.
Welding robots have become increasingly adaptable, making them indispensable in high-mix production environments. They can recognize joint configurations and adjust their welding strategies to reduce defects. This adaptability ensures consistent quality, even when material properties vary.
Here’s how they excel:
- Real-time adjustments during welding allow robots to correct deviations instantly.
- They transition seamlessly between different products, eliminating the need for reprogramming.
- Robots handle deformations in large structures, such as bridge beams, adapting to variations during the welding process.
For example, some robotic cells can weld up to 50 different products monthly without requiring programming for each switch. This flexibility makes robotic welding a valuable asset for industries like construction, automotive, and aerospace.
Future Trends
Advancements in automation are making welding robots more accessible to small and medium-sized businesses.
Emerging trends in welding robot technology are breaking down barriers for small and medium-sized businesses. Collaborative robots, or cobots, are a prime example. These robots work alongside human operators, enhancing productivity without requiring extensive safety measures.
Other trends include:
- AI and machine vision advancements that improve weld quality and reduce defects.
- Cost reduction strategies, such as economies of scale and innovative production methods, that lower the financial barrier.
- Adoption of advanced manufacturing technologies like 3D printing to streamline production.
These developments make welding robots more affordable and practical for smaller operations. As automation continues to evolve, you can expect even greater accessibility and efficiency in the near future.
Welding robots represent a significant investment, but their long-term benefits make them a smart choice for businesses. These systems deliver unmatched accuracy, ensuring consistent, high-quality output. They work tirelessly, boosting productivity and reducing reliance on skilled labor. By automating repetitive tasks, welding robots lower production costs and minimize waste. Their ability to operate in hazardous environments also enhances workplace safety.
Understanding the types of welding robots and their associated costs helps you evaluate your specific needs and budget. This knowledge allows you to assess potential returns and choose the right system for your industry. As technology advances, welding robots are becoming more adaptable and accessible, opening opportunities for businesses of all sizes to improve efficiency and remain competitive.
FAQ
What is the average cost of a welding robot?
The cost of a welding robot typically ranges from $10,000 to over $500,000. The price depends on the type, features, and additional components like end-effectors or software. For example, SCARA robots are more affordable, while articulated arm robots with advanced capabilities cost significantly more.
How much space do you need for a welding robot?
You need enough space for the robot, safety equipment, and smooth material flow. Compact models like SCARA robots fit smaller areas, while larger systems require more room. Proper planning ensures efficient operation and minimizes safety risks.
How long does it take for a welding robot to pay for itself?
Most welding robots achieve ROI within 1-3 years. This depends on factors like production volume, labor cost savings, and reduced waste. High-efficiency robots often recover costs faster due to increased productivity.
Do welding robots require frequent maintenance?
Welding robots need regular maintenance to ensure optimal performance. Annual costs vary by robot type and provider, ranging from $2,000 to $5,000. Routine tasks like cleaning and lubrication help extend the robot’s lifespan and prevent unexpected breakdowns.
Can small businesses afford welding robots?
Yes, advancements in technology have made welding robots more accessible. Compact and collaborative robots offer affordable options for small businesses. These systems provide flexibility and efficiency, making them a worthwhile investment for growing operations.
Tip: Start with a cost-effective model and scale up as your production needs grow.