In an industry where every weld counts, staying ahead of the curve is not just an advantage; it’s a necessity. Spool welding robots are transforming the landscape of metal fabrication, offering solutions to age-old challenges and opening doors to unprecedented possibilities. But are you truly aware of their game-changing potential?
From boosting productivity to enhancing worker safety, these robotic marvels are redefining what’s possible in welding. In this post, we’ll dive into 10 must-know facts about spool welding robots that will not only pique your curiosity but also equip you with the knowledge to make informed decisions for your welding operations. Get ready to explore the cutting-edge world of automated welding, from understanding the basics to glimpsing into the future of this transformative technology.
Understanding Spool Welding Robots
Definition and basic function
Spool welding robots are automated systems designed to perform precise welding operations on cylindrical or tubular components, such as pipes, spools, and pressure vessels. These robots excel in creating consistent, high-quality welds while significantly reducing human intervention in the welding process. The basic function of a spool welding robot is to manipulate a welding torch along a predetermined path, maintaining optimal welding parameters throughout the operation.
Key components
A typical spool welding robot consists of several essential components that work together to ensure efficient and accurate welding:
-
Robotic arm
-
Welding torch
-
Wire feeder
-
Power source
-
Controller
-
Positioning system
-
Safety features
Component | Function |
---|---|
Robotic arm | Moves the welding torch along the weld path |
Welding torch | Delivers the welding arc and filler material |
Wire feeder | Supplies welding wire at a controlled rate |
Power source | Provides electrical power for the welding process |
Controller | Manages robot movements and welding parameters |
Positioning system | Rotates and aligns the workpiece |
Safety features | Ensure operator protection and process integrity |
Types of spool welding robots
Spool welding robots come in various configurations to suit different welding applications:
-
Gantry-style robots
-
Articulated arm robots
-
Column and boom robots
-
Collaborative robots (cobots)
Each type offers unique advantages depending on the specific welding requirements, workspace constraints, and production volume. For instance, gantry-style robots are ideal for large workpieces, while collaborative robots are suitable for smaller operations that require human interaction.
Increased Efficiency in Welding Operations
Speed and precision advantages
Spool welding robots offer significant advantages in terms of speed and precision, revolutionizing welding operations. These automated systems can perform welds at a much faster rate than manual welders, with some models capable of completing welds up to 5 times faster. The precision of spool welding robots is unmatched, consistently producing high-quality welds with minimal errors.
Aspect | Manual Welding | Spool Welding Robot |
---|---|---|
Speed | 1x | Up to 5x faster |
Precision | Variable | Consistent |
Error rate | Higher | Minimal |
Reduced material waste
One of the key benefits of spool welding robots is their ability to significantly reduce material waste. This is achieved through:
-
Precise control of wire feed
-
Optimized welding parameters
-
Minimized overspray and spatter
By reducing waste, spool welding robots not only improve cost-efficiency but also contribute to more sustainable welding practices.
Consistency in weld quality
Spool welding robots excel in maintaining consistent weld quality throughout lengthy production runs. This consistency is crucial for:
-
Meeting stringent quality standards
-
Reducing the need for rework
-
Ensuring structural integrity of welded components
24/7 operation capability
Unlike human welders, spool welding robots can operate continuously, 24 hours a day, 7 days a week. This round-the-clock capability leads to:
-
Increased production output
-
Improved lead times
-
Better utilization of resources
With these efficiency gains, businesses can significantly boost their productivity and competitiveness in the welding industry. Next, we’ll explore the cost-effectiveness of implementing spool welding robots in manufacturing processes.
Cost-Effectiveness of Spool Welding Robots
Initial investment vs. long-term savings
When considering the adoption of spool welding robots, it’s crucial to weigh the initial investment against the long-term savings. While the upfront cost may seem substantial, the return on investment (ROI) often justifies the expense.
Factor | Initial Investment | Long-term Savings |
---|---|---|
Cost | High upfront expense | Significant savings over time |
Time | Training and setup required | Increased productivity and efficiency |
Quality | Learning curve for optimal results | Consistent high-quality welds |
Maintenance | Regular upkeep needed | Reduced human error and rework |
Reduced labor costs
Spool welding robots significantly reduce labor costs in several ways:
-
Fewer workers required for the same output
-
Elimination of overtime pay for rush jobs
-
Reduced training expenses for specialized welding techniques
-
Lower insurance and benefits costs associated with human workers
Lower error rates and rework expenses
The precision of spool welding robots leads to a substantial reduction in error rates and rework expenses:
-
Consistent weld quality eliminates the need for frequent inspections
-
Automated processes reduce material waste
-
Fewer defects mean less time and resources spent on rework
-
Improved first-pass yield rates increase overall productivity
With these benefits in mind, it’s clear that while spool welding robots require a significant initial investment, they offer substantial cost savings in the long run through reduced labor costs, improved efficiency, and lower error rates. Next, we’ll explore how these robots enhance safety for welding professionals.
Enhanced Safety for Welding Professionals
Minimizing exposure to hazardous environments
Spool welding robots significantly reduce the risks associated with welding by minimizing human exposure to hazardous environments. These robots can operate in confined spaces, high-temperature zones, and areas with toxic fumes, keeping welders safe from potential dangers.
Hazard | How Spool Welding Robots Mitigate Risk |
---|---|
Fumes | Robots operate in enclosed areas, reducing human exposure |
Heat | Robots withstand high temperatures, protecting workers |
Radiation | Automated welding minimizes direct exposure to arc radiation |
Confined Spaces | Robots access tight spaces, eliminating need for human entry |
Reduction in repetitive strain injuries
Welding professionals often suffer from repetitive strain injuries due to the nature of their work. Spool welding robots alleviate this problem by:
-
Performing repetitive tasks consistently without fatigue
-
Handling heavy equipment and materials
-
Maintaining precise movements for extended periods
This automation allows human workers to focus on supervision and quality control tasks, significantly reducing the physical strain on their bodies.
Improved workplace ergonomics
The introduction of spool welding robots leads to improved workplace ergonomics for welding professionals. By taking over physically demanding tasks, these robots enable a more ergonomic work environment:
-
Operators can control robots from comfortable, ergonomic workstations
-
Reduced need for awkward positioning or prolonged standing
-
Decreased lifting and carrying of heavy welding equipment
These improvements in workplace ergonomics contribute to better long-term health outcomes for welding professionals, reducing the risk of musculoskeletal disorders and enhancing overall job satisfaction.
Versatility in Welding Applications
Adaptability to various pipe sizes
Spool welding robots showcase remarkable versatility when it comes to handling different pipe sizes. These advanced machines can seamlessly adjust to accommodate a wide range of diameters, from small-bore pipes to large-diameter spools. This adaptability is crucial in industries where diverse piping systems are common.
Pipe Size Range | Applications |
---|---|
Small (1″ – 4″) | HVAC, Plumbing |
Medium (6″ – 12″) | Process piping, Oil & Gas |
Large (14″ and above) | Power plants, Offshore platforms |
Compatibility with different welding processes
One of the key advantages of spool welding robots is their ability to perform various welding techniques. This flexibility allows manufacturers to use a single system for multiple applications, increasing efficiency and reducing equipment costs.
Common welding processes supported by spool welding robots include:
-
Gas Metal Arc Welding (GMAW)
-
Flux-Cored Arc Welding (FCAW)
-
Gas Tungsten Arc Welding (GTAW)
-
Submerged Arc Welding (SAW)
Customizable programming for specific projects
Spool welding robots offer unparalleled customization options, allowing operators to tailor welding parameters for each unique project. This level of control ensures optimal results across diverse applications and materials.
Key customizable features:
-
Weld speed and travel angle
-
Heat input and penetration depth
-
Oscillation patterns and width
-
Multi-pass welding sequences
With this versatility, spool welding robots can tackle a wide array of welding tasks, from simple straight pipe welds to complex multi-pass joints on exotic materials. Next, we’ll explore how these robots integrate with Industry 4.0 technologies to further enhance their capabilities and efficiency.
Integration with Industry 4.0 Technologies
IoT connectivity features
Spool welding robots are at the forefront of Industry 4.0 integration, with advanced IoT connectivity features that revolutionize welding operations. These robots can seamlessly connect to other machines, sensors, and systems within a smart factory ecosystem. This interconnectivity allows for real-time data exchange, enabling more efficient production processes and predictive maintenance.
Key IoT features of spool welding robots include:
-
Wireless communication protocols (Wi-Fi, Bluetooth, 5G)
-
Cloud connectivity for data storage and processing
-
API integration for third-party software compatibility
-
Real-time status updates and alerts
IoT Feature | Benefit |
---|---|
Wireless communication | Enables flexible deployment and easy reconfiguration |
Cloud connectivity | Facilitates remote access and data backup |
API integration | Allows for customized automation workflows |
Real-time updates | Improves response time to production issues |
Data collection and analysis capabilities
Modern spool welding robots are equipped with advanced sensors and data collection systems that gather crucial information about welding processes. This data is then analyzed to optimize performance, improve quality, and reduce downtime.
Key data collection and analysis capabilities include:
-
Weld quality monitoring
-
Energy consumption tracking
-
Production rate analysis
-
Predictive maintenance forecasting
These capabilities enable manufacturers to make data-driven decisions, leading to increased efficiency and cost savings.
Remote monitoring and control options
The integration of remote monitoring and control features in spool welding robots allows operators to manage welding processes from anywhere, at any time. This flexibility enhances productivity and reduces the need for on-site supervision.
Remote capabilities typically include:
-
Real-time video feeds of welding operations
-
Remote adjustment of welding parameters
-
Performance monitoring dashboards
-
Automated alerts and notifications
These features not only improve operational efficiency but also contribute to enhanced safety by reducing the need for physical presence in potentially hazardous welding environments. As we explore the next section, we’ll see how these technological advancements contribute to the environmental benefits of robotic welding.
Environmental Benefits of Robotic Welding
Reduced energy consumption
Spool welding robots significantly reduce energy consumption compared to traditional welding methods. These automated systems operate with precision, minimizing idle time and optimizing energy use. A typical spool welding robot can achieve up to 30% energy savings over manual welding processes.
Energy Consumption Factor | Manual Welding | Spool Welding Robot |
---|---|---|
Idle Time | High | Low |
Precision | Variable | Consistent |
Overall Efficiency | Moderate | High |
Decreased emissions
The adoption of spool welding robots leads to a substantial reduction in emissions. By automating the welding process, these robots minimize fume generation and decrease the release of harmful particulates into the environment. This not only improves air quality in the workplace but also reduces the overall carbon footprint of welding operations.
-
Lower fume generation
-
Reduced particulate release
-
Improved air quality
-
Decreased carbon footprint
Optimized material usage
Spool welding robots excel in optimizing material usage, significantly reducing waste in welding operations. These precision-driven machines ensure:
-
Accurate material deposition
-
Minimal overspray
-
Consistent weld quality
By minimizing errors and maximizing efficiency, spool welding robots contribute to sustainable manufacturing practices. This optimization not only reduces material waste but also lowers the environmental impact associated with raw material production and transportation.
With these environmental benefits, spool welding robots are becoming increasingly attractive to industries seeking to improve their sustainability practices. As we move forward, let’s explore the challenges that companies may face when implementing these advanced welding systems.
Challenges in Implementing Spool Welding Robots
Initial setup complexity
Implementing spool welding robots presents several challenges, with initial setup complexity being a significant hurdle. The process requires careful planning and expertise to ensure optimal performance. Here’s a breakdown of the key factors contributing to setup complexity:
-
Space requirements
-
Power and utilities
-
Integration with existing systems
-
Programming and calibration
Factor | Complexity Level | Key Considerations |
---|---|---|
Space requirements | High | Dedicated area, safety zones |
Power and utilities | Medium | Voltage, compressed air, cooling systems |
Integration | High | Communication protocols, software compatibility |
Programming | Very High | Custom weld paths, parameter optimization |
Operator training requirements
Transitioning from manual welding to robotic systems demands comprehensive training for operators. The learning curve can be steep, encompassing:
-
Robot programming basics
-
Weld parameter adjustment
-
Troubleshooting and maintenance
-
Safety protocols
Operators must develop new skills to effectively manage spool welding robots, which can take several weeks or months of intensive training.
Maintenance considerations
Regular maintenance is crucial for the longevity and performance of spool welding robots. Key maintenance aspects include:
-
Daily inspections of welding components
-
Periodic calibration of robot axes
-
Cleaning and lubrication of moving parts
-
Software updates and backups
Implementing a robust maintenance schedule is essential to minimize downtime and ensure consistent weld quality. As we move forward, it’s important to consider how these challenges impact the selection process for the right spool welding robot.
Future Trends in Spool Welding Robotics
Advancements in AI and machine learning
As the field of spool welding robotics continues to evolve, artificial intelligence (AI) and machine learning are set to revolutionize the industry. These technologies will enable spool welding robots to become more intelligent, adaptive, and efficient. AI algorithms will allow robots to optimize welding parameters in real-time, adjusting for variations in material properties and environmental conditions. Machine learning models will analyze vast amounts of welding data to predict potential defects and improve overall weld quality.
AI/ML Feature | Benefit |
---|---|
Real-time optimization | Improved weld quality |
Predictive maintenance | Reduced downtime |
Adaptive learning | Enhanced versatility |
Data-driven insights | Increased productivity |
Improved sensor technologies
The future of spool welding robots lies in advanced sensor technologies that will significantly enhance their capabilities. These innovations include:
-
High-resolution vision systems for precise seam tracking
-
Thermal imaging sensors for temperature monitoring
-
Force-feedback sensors for improved control and safety
-
Acoustic sensors for real-time weld quality assessment
These sensors will work in harmony to provide spool welding robots with unprecedented levels of awareness and control, resulting in superior weld quality and consistency.
Enhanced collaboration with human welders
While automation continues to advance, the future of spool welding robotics will also focus on improving collaboration between robots and human welders. This symbiotic relationship will leverage the strengths of both:
-
Robots handling repetitive, high-precision tasks
-
Humans overseeing complex decision-making and quality control
-
Collaborative robots (cobots) working alongside welders in shared spaces
-
Augmented reality interfaces for intuitive robot programming and control
This enhanced collaboration will lead to increased productivity, improved safety, and a more skilled workforce capable of managing advanced welding operations. As we look towards these exciting developments, it’s clear that the integration of spool welding robots will continue to transform the welding industry.
Selecting the Right Spool Welding Robot
Assessing project requirements
Before investing in a spool welding robot, it’s crucial to thoroughly assess your project requirements. Consider the following factors:
-
Material types and thicknesses
-
Welding processes needed
-
Production volume
-
Workspace constraints
Requirement | Importance | Considerations |
---|---|---|
Material | High | Compatibility with various metals |
Process | High | MIG, TIG, or other specialized methods |
Volume | Medium | Throughput capacity of the robot |
Workspace | Medium | Robot size and reach requirements |
Evaluating robot specifications
Once you’ve determined your project needs, evaluate spool welding robot specifications:
-
Payload capacity
-
Reach and working envelope
-
Repeatability and accuracy
-
Control system features
-
Integration capabilities
Considering manufacturer support and warranties
Choosing a reliable manufacturer is as important as selecting the right spool welding robot. Look for:
-
Comprehensive training programs
-
Responsive technical support
-
Robust warranty coverage
-
Availability of spare parts
ROI calculation tips
To justify the investment in a spool welding robot, calculate the potential return on investment:
-
Estimate current welding costs (labor, materials, overhead)
-
Project productivity increases with robotic welding
-
Factor in reduced material waste and improved quality
-
Consider long-term savings on labor and training
Remember, while the initial cost may be high, spool welding robots often provide significant long-term savings and productivity gains.
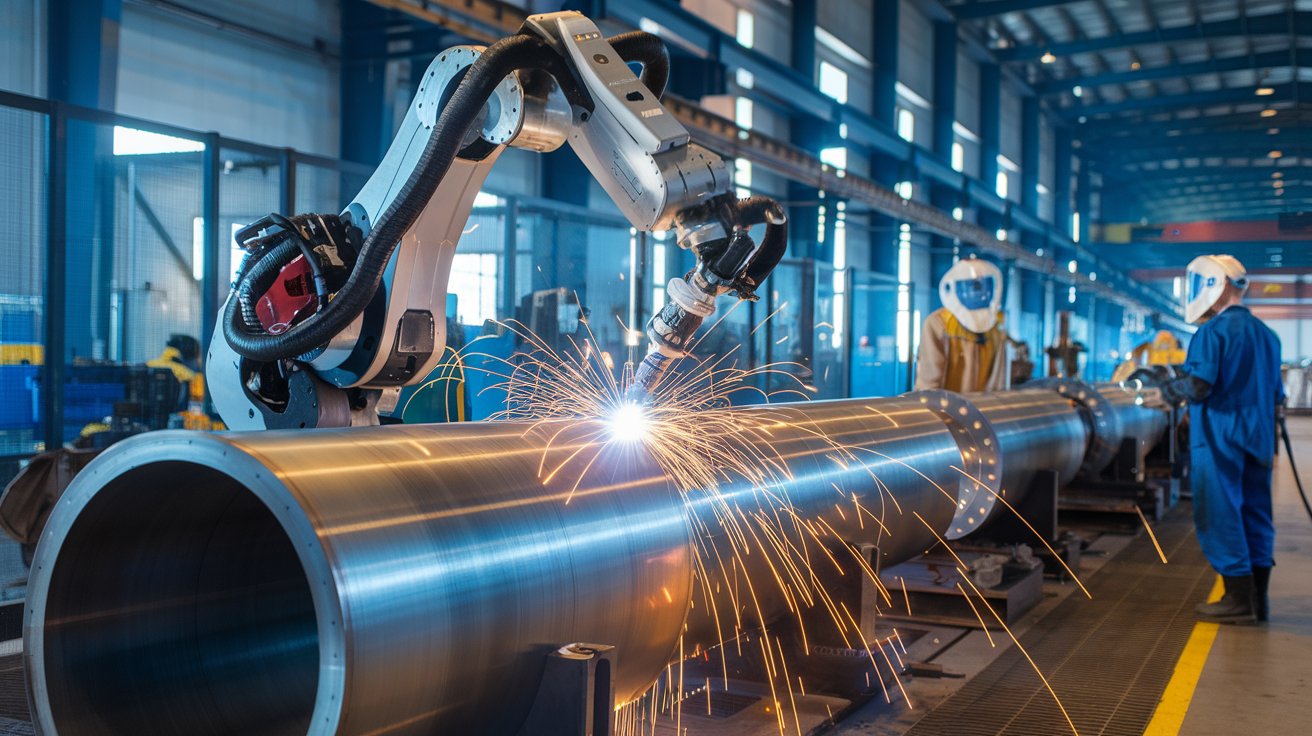
As the welding industry continues to evolve, investing in the right spool welding robot becomes crucial for businesses looking to stay competitive. By carefully considering your specific needs and thoroughly researching available options, you can harness the power of these cutting-edge machines to optimize your welding operations and drive your business forward in this rapidly changing technological landscape.