It is estimated that as of 2016, only about 40,000 units of warehouse automation solutions were shipped to buyers. However, that figure is forecasted to rise to roughly 620,000 units per year by 2021. Such a sharp increase in uptake can only mean one thing, warehouse automation is delivering positive results for clients.
On the back of this, you may be weighing the idea of automating your warehouse. Nevertheless, like many entrepreneurs, you may also be wondering where to start. Does your facility have to be mega-sized to qualify? How do you go about finding the right warehouse robots?
Read on to find out everything you need to know about warehouse robotics.
What is Warehouse Automation?
Source: geekwire.com
Warehouse automation refers to the use of technological solutions to run operations in a warehouse. You could opt for either full or partial automation.
In a fully automated warehouse, warehouse robots do almost all the work with only a handful of staff involved in operations. An example of this is the Alibaba warehouse in Wixu, Shanghai.
On the other hand, in a partially-automated facility, robots and staff work together. The robots and employees are each assigned the tasks they are lost effective at to reap maximum benefit from their capabilities. Amazon warehouses are an example of warehouses that are run on this principle.
Physical Warehouse Automation
Using forklifts to move packages around a facility takes time and requires a substantial amount of labor. Add to that other tasks like sorting, loading, and unloading packages and it is clear why salaries account for about 65% of warehouse expenses. Physical automation seeks to solve this problem through the use of automated warehouse robots.
Automatic warehouse robots work autonomously with minimal staff input. There are different types and their suitability varies depending on the needs of your warehouse. They include:
Automated Storage and Retrieval Systems (AS/RS)
Source: Pinterest
An AS/RS is a computerized robotic system used to fetch requested packages from storage and deliver them to a common area. It can also be used to store units of inventory in their designated areas.
It is recommended for:
- Large warehouses with high volumes of inventory
- Warehouses that need to capitalize on storage space
- Storage and retrieval inventory tasks that require do not require any additional processes
Automated Guided Vehicles (AGVs)
Source: blog.item24.com
AGVs are driverless vehicles that are used to transport inventory across a warehouse. They follow paths charted using magnetic strips and thus can only stick to predetermined routes. There are, however, models that use a combination of sensors and warehouse maps to find their way.
Further, depending on your inventory payloads, you could opt for automatic guided carts (AGCs). AGCs work on the same principle as AGVs but they are designed to handle smaller payloads.
AGCs or AGVs are ideal for:
- Goods to person applications
- Any size of warehouse provided there is enough room for them to navigate
- Low budget automation plans
Aerial Drones
Source: Pinterest
As drone technology catches on, robotics manufacturers have found ways to harness them for warehouse automation. They are conveniently applicable in any size or type of warehouse.
To suit warehouse applications, they are designed with optical navigation systems and deep learning technologies synced to warehouse management software. This makes it possible for them to be used to:
Scan inventory from aerial positions using RFID technology
Upload data directly to the warehouse management system
Locate and collect light packages within the facility
Autonomous Mobile Robots (AMRs)
Source: 1iigqhoti4p36kwwhmb4218s-wpengine.netdna-ssl.com
AMRs are compact robots that use inbuilt sensors and computerized systems to navigate a warehouse. Unlike AGVs, they can follow flexible routes and can reroute when their path is obstructed. Moreover, they do not require any infrastructural adjustments before they are applied in your facility. They are applicable for :
Transporting packages
Scanning inventory using RFID technology
Locating, sorting, and collecting packages when fitted with a pick and place robotic arm
Articulated Robotic Arm
An articulated robotic arm has flexible joints that enable it to expand and retract somewhat like the human arm. It is usually attached to a firm base for stability. They are suitable for any kind of warehouse and can be used for numerous functions including:
- Picking and placing packages onto racks
- Palletizing
- Loading and unloading inventory
- Sorting packages; if the arm is fitted with sensors
These kinds of robots are recommended for any type of warehouse. Your ideal articulated robot arm will be determined by:
The payloads to be handled
How far you would like the robot arm to reach in relation to storage unit heights
The flexibility or range of motion you hope the robot arm can cover; a 6-axis robot arm is more flexible than a 4-axis robot arm
Digital Automation
Source: Pinterest
Digital warehouse automation refers to the use of Warehouse Management Systems (WMS) for inventory management tasks like stock-taking. WMS software does not work in isolation but rather as part of a larger system of operation. Warehouse robots are often linked to and controlled via such software.
The goal of WMS software is to have more control and order in inventory management. It is effective in functions such as:
- Tracking shipments
- Monitoring expiration dates
- Monitoring stock levels for replenishment
There are different types of warehouse management systems that cover different scopes of operations. They include:
Standalone WMS – it is a basic level of software that is applicable in any warehouse and is much more affordable when compared to other types. It focuses solely on warehouse functions and no other parts of the supply chain. They include receiving, packing, shipping, storage, expiry date tracking, barcode scanning, and basic In-house inventory transportation tools.
Supply Chain WMS- this type of software covers a broader scope of operations. In addition to internal warehouse management, it facilitates the management of external processes. They include vendor-related processes, product cycles, distribution processes, risk management among others. Suffice to say, it gives you control of a larger part of your supply chain.
Enterprise Resource Planning – it is more commonly referred to as ERP. It is the all-in-one option of warehouse management systems as it encompasses just about all needs. From human resource management to the incorporation of robotic systems, an ERP system covers all areas of warehouse operations.
Factors to Consider When Choosing Warehouse Software
Source: Pixabay
The needs of your business take center-stage when choosing warehouse software. For instance, a logistics company may have slightly different needs than a product manufacturer. Similarly, a large warehouse may require a more robust system than a smaller one.
Additionally, it is advisable to ensure that your WMS will be compatible with your chosen mode of robotic warehouse automation. In this regard, aim for software that supports internal transportation tools. Other factors that could play a role in your purchase could include:
Budget – comprehensive WMS types cost more as they offer more value but you should also evaluate their potential ROI.
Ease of use – it should be easy for all staff involved to use.
Flexibility – it should be able to adapt in case your warehouse volumes increase and decrease in large amounts.
Security – real-time tracking of inventory and other security measures are essential in maintaining supply chain integrity.
Why Robotic Automation in the Warehouse is Important
Integrating warehouse robots in your facility comes at a cost. You may also have to make other changes like restructuring your staffing as well as structural changes to accommodate robots. Such major changes can seem daunting and cause you to be hesitant about investing in robotic automation.
As with all prudent business decisions, it would be best to weigh your options. What do you stand to gain from robotic automation? Will it be worth the cost, monetary and otherwise, of investment?
Below is a cost-benefit analysis of what you stand to gain by investing in robotic warehouse automation.
Cost
Source: Pixabay
On average, a warehouse employee works a minimum of 40 hours a week earning approximately $15-$20. In a year, that translates to about $40,000 per employee. It is a much larger figure if you extrapolate it to accommodate all workers including those in supervisory and supportive roles.
In contrast, if you invest in warehouse robots, there are no salary costs involved. It is a one-off purchase from which you will reap years of service. Cutting down on salary expenditure alone can make your warehouse way more profitable than it currently is.
A Larger Scale of Operation
Source: Pixabay
The capacity of your warehouse may be limited by its organizational structure. If your staff have to manually retrieve inventory using ladders or levers, the storage racks can only go so high. In such a situation you would likely not be operating at optimum capacity.
Robotic automation such as AS/RS or long-reach robotic arms defies such kinds of constraints. You would be able to stack inventory much higher and retrieve it with just as much ease. Better yet, you would not have to expand your warehouse facility. You would only be maximizing the space you already have. All while earning more from handling larger volumes of stock.
Speed
Consider how much time it takes for your workers to establish the location of a product and walk or drive a forklift to fetch it. Now, compare that to a robotic system where staff would not have to leave their stations. All they would have to do is communicate with the robot over the WMS or wifi and it would fetch whatever was needed.
The latter is a much faster system that allows workers to do much more work in one shift. There would hardly be any need for overtime work. This benefits both your employees and the facility.
Improved Service Delivery
Source: Pixabay
When it comes to the fulfillment of orders, speed is king. Short turn-around times are a major selling point for any business. Your customers will be delighted to have their order handled fast which gives you an edge over your competitors.
Robotic warehouse automation also greatly reduces errors in operations. Robots do not slip up due to fatigue and they operate on accurate computerized systems. As a result, your inventory handling and dispatch processes will likely begin to run at an unprecedented efficiency.
Improved Inventory Management
Source: Pinterest
It is such a convenient delight when you can easily check your stock levels daily and trace each stock unit. It makes running the warehouse significantly easier but there are other benefits to it too.
Some industries, like the pharmaceutical sector, are governed by strict accountability regulations. You need to be able to track and trace each inventory unit for the entire duration that it is under your domain. This is a challenge that suitable warehouse robots and a good WMS can help you overcome. A quick robot scan using RFID technology will give you a real-time stock update whenever necessary.
Pilferage would also become a thing of the past. You could allocate staff passwords to access the WMS which would give you a trail of who handled what inventory and when. Moreover, RFID chips are fully traceable.
When to Bring Robotic Systems Into Your Warehouse
Source: Pixabay
When you should introduce a robotic system into your warehouse is both a question of timing and purpose. If you time it just right, you will reap better gains and have an easier time transitioning into automatic systems. As for purpose, understanding the challenges you hope to solve will help you choose the right robotic systems for your facility.
Let us examine some scenarios that are ideal for the introduction of a robotic warehouse system.
Scaling Up
Source: Pixabay
As your warehouse business expands, it may outgrow your current operating systems. Some indicators of this are:
- Constantly having to hire more staff to meet the demands of the business
- Backed up orders
- Insufficient storage space
It could also be that you are looking to expand the business of your own volition. Either way, scaling up requires an operating system that can handle the pressures of a larger operation.
Therein lies the importance of robotic automation. It will enable you to expand without needing to hire more staff and to utilize your current space more efficiently. You will also be able to maximize profits by earning more while operating at low costs.
Staffing Challenges
Source: Pexel
Given the long hours involved in warehouse jobs and sometimes strenuous tasks, warehouse employees have a high-turnover. The downside of this is having to hire and train new staff often. It slows down operations and can also be costly. This is equally a challenge if you have high and low cycles that require you to adjust your staffing accordingly.
Robots are forever employees unless they malfunction and even then they are often fixable. Additionally, whether during low or high seasons, you can deploy them as needed at no extra cost. They offer you staffing flexibility you would be hard-pressed to achieve with employees.
In the recent past, another spanner has been thrown into the warehouse works; the Coronavirus. Warehouses are enclosed spaces and given the nature of operations, it would be difficult to implement recommended safety protocols. Workers are also wary of exposing themselves to the disease at work.
Some companies have found great success in having fewer employees work alongside robots. It allows for proper social distancing without compromising operations. It is also an easier time to make the transition into robotic systems as most business activities are in a lull. You could recoup your investment when normalcy returns and the world economy picks up.
Inefficiencies
Source: Pixabay
When errors are common in the operations of a warehouse, most facilities resort to hiring more staff. The idea behind this is that if there is more supervision there will be fewer errors and improved efficiency. Unfortunately, this solution does not always work. On the contrary, sometimes the more workers in an operation chain, the higher the chances of errors.
Robots are designed to be precise in their operations. As opposed to inflating your staffing, you would be better off investing in robotic systems. You are guaranteed results and it is a long-term solution.
Branding
Source: Pixabay
The world has gone digital. Running an efficient high-tech warehouse operation system paints your brand in the right light. Customers are drawn to warehouses where they are certain their products or shipments will be in good hands. More so now that supply chain integrity is under scrutiny due to a burgeoning black market system.
How to Access a Warehouse Robotics System
The robotics industry has been on a growth spurt in the last few years. As you seek to automate your warehouse, you will need to sift through a substantial pile of options. Here are some pointers that could help you better navigate your purchasing process.
Assess Your Needs
Source: Pexel
What problem are you hoping to solve in your warehouse and what type of robot would be best? The answer to this question will help you narrow down your list of warehouse robotics companies.
If, for example, you need to automate your receiving and putaway procedures, consider a palletizing robot arm or a pick and place alternative. Your search would also focus on robotic arm manufacturers.
Factor in other needs as well like whether a supplier can offer end-effectors or custom solutions if you have unique requirements. It is equally helpful if the firm is diligent about after-sale service; you may need some troubleshooting guidance as you adjust to the system. Price and their scope of delivery will also inevitably sway your decision.
Where Should You Look?
When you know what you need and have your budget set aside all that’s left is looking for a supplier. You could explore avenues such as:
An online search
Source: Pexel
At first glance, an online search seems like a very unconventional way to locate warehouse robotics suppliers. However, it might actually be the best place to start. Most robot manufacturer websites have detailed product information and you could also read reviews from other customers for some insight. You will conveniently be able to compare as many options as you like at the touch of a button.
Further, an online search does not limit you to manufacturers that you can physically visit. You can engage robotics suppliers from across the world. Their prices may be much lower or they may even have more advanced technology than firms in your locality.
Once you have a list of viable options, you can also ask for price quotes for what you hope to purchase online. It will help you decide if you would like to engage them further.
Trade Fairs
If you like to physically see and understand what you are investing in, trade fairs would be a great option for you. A cross-section of robotics stakeholders attend such events and display their warehouse robots among other latest inventions. You would have a chance to not just compare brands but also engage their representatives.
Additionally, some trade fairs host seminars that may be of great benefit to you. New trends are discussed during such sessions and product details are unpacked in depth. There is always a lot to learn which could go a long way to inform your purchase decision.
Installation and Adjusting to Warehouse Robotics
Source: Pexels
The installation process and level of disruption that your facility may experience will depend on the robots you choose. Some, like the automatic storage and retrieval system, require more intricate procedures whereas introducing a robotic arm is an easy fix. The goal here is to understand the process so that you can schedule the interruption of services.
Other key issues you may face entail:
Safety – during the installation process, it is best to have operations in that wing of the warehouse shut down. Any inventory in the vicinity should also be moved to prevent the possibility of damage and subsequent losses. Most importantly, endeavor to engage robotics professionals during installation and even thereafter as you transition.
Staff training – the concept of warehouse robotics is generally similar but the application in each warehouse is unique. As such, the success of your warehouse automation project will depend heavily on staff training. Make an effort to facilitate as many training sessions with as much educational material as necessary.
Staff safety – even with training and safety features installed in robots, accidents can happen. Liaise with your warehouse robot supplier in how you can best improve safety for staff while working alongside robots. Amazon, for example, opted to have their staff wear special jackets with additional sensors to notify robots of their presence in a workspace.
Re-assigning employees – some employees’ responsibilities will be taken over by the robotic system thereby necessitating their re-assignment. Staff cuts tend to have negative effects on overall morale, therefore, it is advisable to retain as many workers as you can. They can take on other tasks within the facility such as dispatch or positions further down in the supply chain.
Conclusion
In the history of businesses, automation has always heralded a new dawn. It opens new frontiers that older ways of running things could not have delivered. There is a whole new world of brilliant warehousing possibilities that await you on the other side of automation. Time to find a warehouse robot manufacturer and get started, wouldn’t you say?
Also Read:
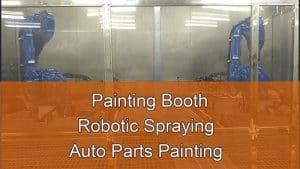
Painting Booth | Robotic Spraying | Auto Parts Painting
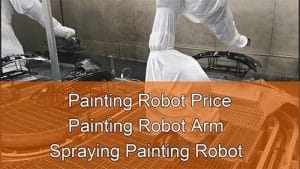
Painting Robot Price|Painting Robot Arm|Spraying Painting Robot
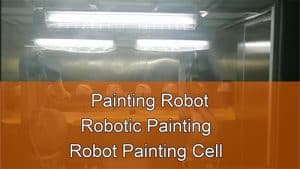
Painting Robot | Robotic Painting | Robot Painting Cell
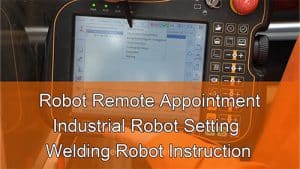