
Robotic production lines have revolutionized tunnel rebar manufacturing by introducing unprecedented levels of automation and precision. EVS’s Robotic Tunnel Rebar Intelligent Production Line exemplifies this transformation. This advanced system operates continuously 24/7, enhancing production efficiency while reducing human error. By overcoming traditional bottlenecks, it has set a new standard for intelligent manufacturing in the construction industry.
The adoption of robotic production lines is gaining momentum globally. Many Global Top 500 enterprises have implemented EVS’s solution, showcasing its ability to increase capacity and efficiency. This trend highlights the growing reliance on automation to meet the demands of modern tunnel construction projects.
Key Takeaways
- Robots work nonstop, making more products and reducing mistakes.
- Machines do dangerous jobs, keeping workers safe and focused on easier tasks.
- Accurate robots make rebar with less waste and stronger quality.
- Teaching workers about robots is key to using them well.
- Better robots and AI will make rebar faster and eco-friendly in the future.
Overview of Robotic Production Lines in Tunnel Rebar
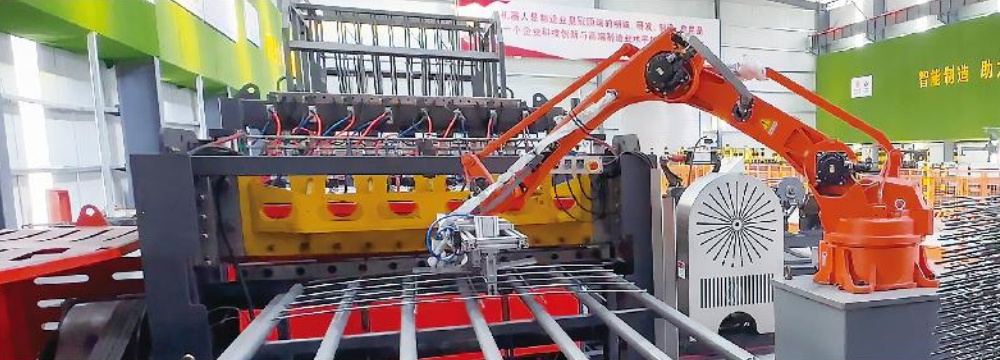
What Are Robotic Production Lines?
Robotic production lines are advanced manufacturing systems that utilize automation and robotics to streamline processes. These systems replace manual labor with high-precision robots, ensuring consistent quality and efficiency. In tunnel rebar manufacturing, robotic production lines handle tasks such as material loading, cutting, welding, and unloading. Intelligent control systems oversee the entire workflow, from raw steel processing to the final assembly of steel arches. This approach not only enhances productivity but also ensures the durability and reliability of the rebar used in tunnel construction.
The process involves multiple steps, each optimized for efficiency and precision. For example:
- Robotic end plate welding ensures strong connections.
- Cold bending machines shape steel into arches for structural integrity.
- Automated unloading systems place finished products onto material racks.
These systems represent a significant leap forward in construction technology, setting new benchmarks for quality and performance.
Importance of Automation in Tunnel Rebar Manufacturing
Automation has transformed tunnel rebar manufacturing by addressing the limitations of traditional methods. Fully automated systems operate continuously, increasing production capacity and reducing downtime. High-precision robots improve the accuracy of welding and cutting, resulting in superior product quality. The chain-type production line conveyance boosts efficiency by over 50%, while intelligent sensors monitor machinery for anomalies, ensuring stable operations.
Automation also eliminates the need for human intervention in hazardous tasks, improving worker safety. The adaptability of these systems to different rebar configurations further enhances productivity. By streamlining workflows and minimizing errors, automation has become indispensable in modern tunnel construction projects.
Key Features of Robotic Systems for Tunnel Segment Production
Robotic systems for tunnel segment production incorporate cutting-edge features to meet the demands of complex construction projects. These include:
- 3D Vision End Plate Assembly Welding System: Ensures stable welding quality with spatial recognition technology.
- Multi-Robot Collaborative Operation: Enhances efficiency and quality through synchronized teamwork.
- Fully Automatic Manufacturing Process: Covers material loading, cutting, welding, and stacking.
- Flexible Production Line Layout: Adapts to various construction site configurations.
- Modular Design: Simplifies maintenance and reduces downtime.
These systems use advanced materials and intelligent technologies to ensure durability and reliability. Features like precise steel plate cutting and cold bending of I-beams contribute to the structural integrity of tunnel segments. By integrating these capabilities, robotic systems redefine the standards of rebar production in tunnel construction.
Case Studies of Successful Implementations
EVS Robotic Tunnel Rebar Intelligent Production Line
Project Overview
EVS’s Robotic Tunnel Rebar Intelligent Production Line represents a groundbreaking advancement in rebar manufacturing. This system integrates high-precision robotics and intelligent monitoring to automate the entire production process. It has been implemented by several Global Top 500 enterprises to address the growing demand for efficient and reliable tunnel construction solutions. The production line operates continuously, ensuring consistent output and reducing human intervention in hazardous tasks.
Implementation Process
The implementation began with a detailed assessment of the client’s production requirements. EVS customized the production line layout to fit specific site configurations. The system was installed in phases, starting with the automated material loading and cutting modules. Robotic welding units were then integrated, followed by the automated unloading system. Engineers collaborated closely with operators to ensure seamless integration and minimal disruption to existing workflows.
Results Achieved
The production line delivered remarkable results. Clients reported a 50% increase in production efficiency and a significant reduction in labor costs. The automated welding process ensured consistent quality, while the system’s adaptability allowed for the production of various rebar configurations. Worker safety improved as robots handled hazardous tasks, and the intelligent monitoring system minimized downtime by detecting anomalies early.
Automated Rebar Cage Fabrication with Gantry Robots
Project Overview
Gantry robots have revolutionized the fabrication of rebar cages for tunnel construction. These systems automate the entire process, from material handling to welding, ensuring high precision and efficiency. Their ability to adapt to different rebar sizes and models makes them ideal for complex construction projects.
Implementation Process
The implementation involved the installation of gantry robots equipped with spatial 3D seam recognition technology. These robots were programmed to handle multiple rebar configurations, ensuring flexibility. Multi-robot collaborative operations were established to enhance efficiency and quality. The production line layout was tailored to the client’s specific needs, ensuring optimal use of space and resources.
Results Achieved
The gantry robots achieved exceptional results. The fully automatic rebar tying process reduced production time and improved quality. The system’s environmental adaptation ensured consistent operation regardless of weather conditions. Clients also benefited from reduced labor intensity and enhanced safety standards.
Advantage | Description |
---|---|
Automation | Fully automatic manufacturing process, including material loading, cutting, and stacking. |
Flexibility | Multi-variety self-adaptive process with free switching between different sizes and models. |
Enhanced Quality Control | Spatial 3D seam recognition technology ensures stable welding quality. |
Environmental Adaptation | Unaffected by weather, time of day, or seasons, ensuring consistent operation. |
Collaborative Operation | Multi-robot collaborative operation technology for high efficiency and quality. |
Tailored Production Line Layout | Highly adaptable layouts to meet various production scales and needs. |
Planar Rebar-Tying Robot for Tunnel Construction
Project Overview
The planar rebar-tying robot is a specialized solution designed for automatic rebar tying in tunnel construction. This system automates the tying process, ensuring consistent quality and reducing labor requirements. Its compact design makes it suitable for confined construction sites.
Implementation Process
The implementation began with the installation of the rebar-tying robot at the construction site. Engineers programmed the robot to handle various rebar configurations, ensuring adaptability. The system was integrated with existing workflows to minimize disruptions. Operators received training to monitor and maintain the robot effectively.
Results Achieved
The rebar-tying robot delivered outstanding results. The automatic rebar tying process increased productivity and reduced errors. Its compact design allowed for efficient operation in confined spaces. Clients reported improved safety and significant cost savings over time.
Benefits of Robotic Production Lines in Tunnel Rebar
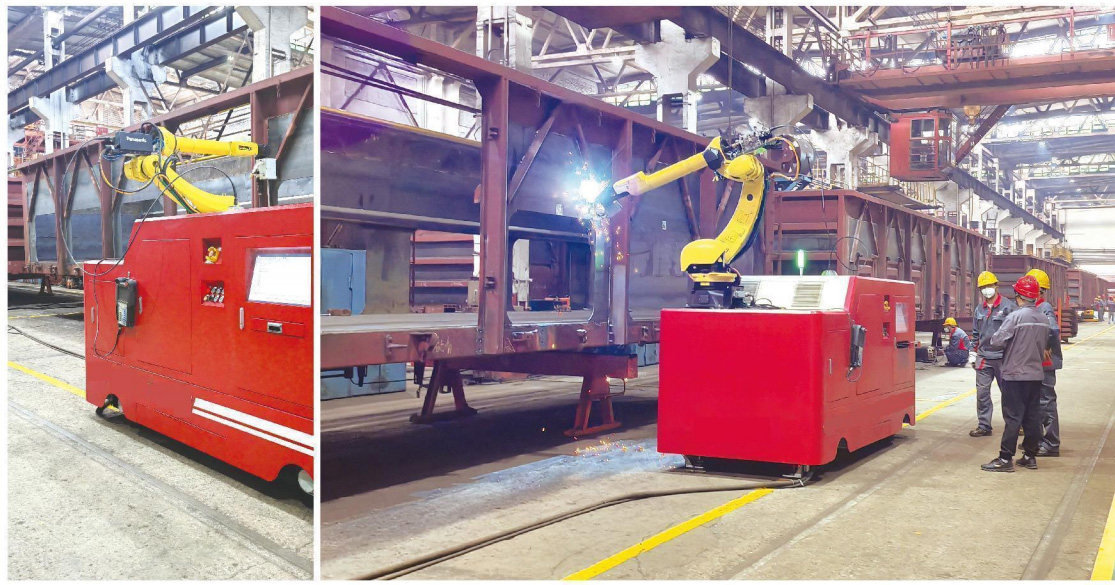
Increased Efficiency and Productivity
Robotic production lines significantly enhance efficiency and productivity in tunnel rebar manufacturing. These systems operate continuously, 24 hours a day, seven days a week, ensuring uninterrupted production. The fully automated and intelligent cutting process eliminates delays caused by manual intervention, streamlining the workflow from raw material handling to final assembly. High-precision robots further optimize efficiency by adapting to various rebar configurations and sizes, reducing the need for manual adjustments.
The integration of advanced sensors for seam tracking and positioning ensures precise welding, which minimizes errors and improves overall output quality. By automating hazardous tasks, these systems also reduce labor intensity, creating a safer work environment. This combination of uninterrupted operation, adaptability, and precision makes robotic production lines indispensable for modern tunnel construction projects.
Enhanced Precision and Quality
Robotic systems redefine precision and quality in tunnel segment production. These systems achieve exact dimensional accuracy in rebar cutting and bending, which reduces material waste and optimizes reinforcement layouts. This level of precision enhances the structural integrity of tunnel segments, ensuring they meet the rigorous demands of tunnel construction.
High-precision robots equipped with advanced seam recognition technology deliver consistent welding quality. This consistency not only shortens project timelines but also increases productivity. By maintaining strict quality standards, robotic production lines provide a reliable reinforcement solution for tunnel construction, setting a new benchmark in the industry.
Cost Savings Over Time
Robotic production lines offer substantial long-term cost savings for tunnel rebar manufacturing. Reduced labor costs and minimized human error contribute to significant financial benefits. The modular design of these systems simplifies maintenance, allowing for quick repairs and reducing downtime. High-quality components resistant to wear further lower maintenance expenses.
Real-time monitoring systems detect issues early, preventing costly disruptions. Additionally, the precision of robotic systems reduces material waste, optimizing reinforcement layouts and enhancing structural integrity. These factors collectively ensure that robotic production lines remain a cost-effective choice for producing tunnel segments efficiently.
Improved Worker Safety
Robotic production lines in tunnel rebar manufacturing have significantly improved worker safety by automating hazardous tasks and reducing human involvement in risky environments. These systems handle complex processes with precision, ensuring safer operations and minimizing the likelihood of accidents.
- Robotic systems automate intricate tasks, such as rebar welding and cutting, which reduces the risk of human error. By eliminating manual intervention in these processes, workers face fewer dangers associated with handling heavy machinery or sharp materials.
- Intelligent monitoring systems oversee operations with high accuracy, detecting potential issues early. This proactive approach minimizes the need for manual adjustments, further safeguarding workers from exposure to unsafe conditions.
- Continuous operation of robots ensures that production runs smoothly without requiring workers to perform repetitive or physically demanding tasks. This reduces labor intensity and prevents fatigue-related injuries.
The integration of advanced robotics has transformed the safety landscape in rebar manufacturing. These systems not only enhance operational efficiency but also prioritize the well-being of workers by addressing safety concerns at every stage of production.
- Automation of processes significantly reduces the chances of human error, which often leads to workplace accidents.
- High-precision robots equipped with intelligent sensors enhance monitoring capabilities, ensuring that anomalies are detected and resolved promptly.
- Continuous production capability lowers the need for manual labor in hazardous environments, contributing to a safer workplace.
By automating the handling, cutting, and welding of rebar, robotic production lines create a safer working environment. Workers no longer need to engage directly with dangerous machinery or materials, which drastically reduces the risk of injuries. These advancements demonstrate how technology can enhance both productivity and safety in tunnel rebar manufacturing.
Challenges in Implementing Robotic Production Lines
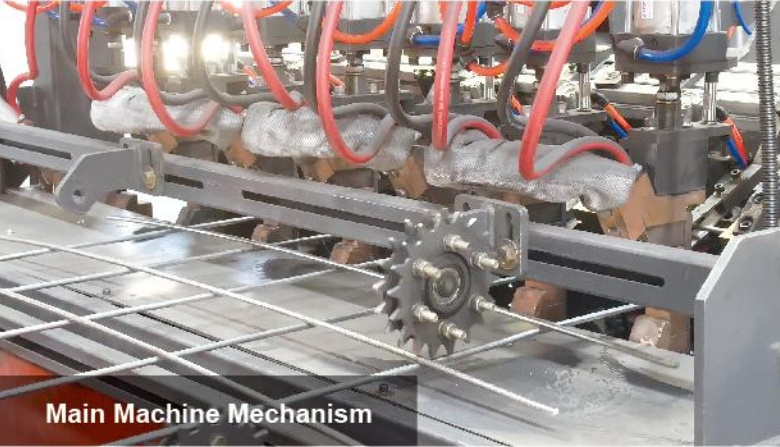
High Initial Investment Costs
Implementing robotic production lines in rebar manufacturing requires significant upfront investment. Companies must allocate resources for purchasing advanced robotic systems, integrating them into existing workflows, and customizing layouts to meet specific production needs. These costs can be a barrier, especially for small and medium-sized enterprises. However, the long-term benefits, such as increased efficiency and reduced labor costs, often outweigh the initial expenses.
The cost of high-precision robots, intelligent monitoring systems, and advanced software adds to the financial burden. Additionally, companies must invest in infrastructure upgrades to accommodate these systems. Despite these challenges, many organizations recognize the value of automation in improving productivity and maintaining competitiveness in tunneling projects.
Integration with Existing Systems
Integrating robotic production lines with existing systems presents technical and logistical challenges. Companies must ensure compatibility between new robotic systems and current machinery, software, and workflows. A structured approach can simplify this process:
- Assess automation needs by analyzing current processes to identify areas where robotics can have the most impact.
- Design custom solutions in collaboration with experts to address specific production requirements.
- Integrate robotic systems with existing machinery and software to ensure seamless operation.
- Train employees to operate and maintain the new systems effectively.
This step-by-step strategy minimizes disruptions and ensures a smooth transition to automated production. Successful integration enhances the efficiency of tunnel systems and supports the demands of modern construction projects.
Training and Workforce Adaptation
Adopting robotic production lines requires a skilled workforce capable of managing advanced systems. Training programs play a crucial role in equipping employees with the necessary skills. For example, a regional food processing company successfully trained workers to program and maintain automated packaging lines. Similarly, an electronics manufacturer enhanced operational efficiency by teaching employees to oversee robots and analyze production data.
Effective training programs focus on critical skills such as problem-solving, adaptability, and collaboration. Initiatives like the Workforce Innovation and Opportunity Act (WIOA) connect job seekers with training opportunities in tech-driven industries. These programs prepare workers to adapt quickly to new tools and systems, ensuring productivity in tunneling projects.
Investing in workforce development not only addresses the challenges of adaptation but also fosters a collaborative environment where human workers and robots work together seamlessly. This approach enhances the overall efficiency of rebar production and supports the evolving needs of construction projects.
Maintenance and Technical Support
Effective maintenance and technical support are critical for ensuring the long-term performance of robotic production lines in tunnel rebar manufacturing. These systems rely on advanced technologies, making regular upkeep essential to prevent disruptions and maintain operational efficiency.
Robotic production lines require routine maintenance to ensure safe and reliable operation. Tasks such as cleaning, lubrication, and inspection of robotic components help prevent wear and tear. Intelligent monitoring systems play a vital role by providing real-time data on equipment performance. These systems detect anomalies early, allowing technicians to address potential issues before they escalate into costly breakdowns.
The modular design of many robotic systems simplifies maintenance procedures. Individual modules can be accessed and repaired without halting the entire production line. This feature minimizes downtime and ensures that operations remain uninterrupted. The table below highlights common maintenance challenges and their solutions:
Challenge Type | Description |
---|---|
Regular Maintenance | Regular maintenance is essential to ensure the production line operates safely over time. |
Intelligent Monitoring Systems | These systems provide real-time data on equipment performance, allowing for early issue detection. |
Modular Design | A modular design simplifies maintenance, allowing individual modules to be accessed for repairs without disrupting the entire system. |
Technical support also plays a crucial role in the success of robotic production lines. Manufacturers often provide comprehensive training programs to equip operators with the skills needed to manage and maintain these systems. Access to skilled technicians ensures that any technical issues are resolved promptly, reducing the risk of prolonged downtime.
By prioritizing maintenance and leveraging intelligent monitoring systems, companies can maximize the lifespan and efficiency of their robotic production lines. A proactive approach to technical support further enhances reliability, ensuring that these advanced systems continue to meet the demands of modern tunnel construction projects.
Lessons Learned from Case Studies
Importance of Planning and Customization
Effective planning and customization play a pivotal role in the successful implementation of robotic production lines for rebar manufacturing. Each construction project presents unique challenges, requiring tailored solutions to meet specific production demands. Companies that prioritize detailed assessments of their operational needs can design systems that align with their goals. For instance, customizing production line layouts ensures optimal use of space and resources, enhancing efficiency.
Planning also involves anticipating potential obstacles and developing strategies to address them. This proactive approach minimizes disruptions during implementation and ensures a smooth transition to automated processes. By focusing on customization, organizations can adapt robotic systems to handle various rebar configurations, improving productivity and maintaining high-quality standards.
Collaboration Between Engineers and Operators
Collaboration between engineers and operators is essential for the seamless integration of robotic systems. Engineers bring technical expertise, while operators provide practical insights into daily workflows. This partnership fosters a comprehensive understanding of the production process, enabling the development of user-friendly systems.
During implementation, engineers work closely with operators to ensure the new technology aligns with existing practices. Training programs further strengthen this collaboration by equipping operators with the skills needed to manage and maintain robotic systems. This cooperative approach not only enhances operational efficiency but also builds trust among the workforce, encouraging acceptance of automation.
Continuous Monitoring and Optimization
Continuous monitoring and optimization are critical for maintaining the performance of robotic production lines. Standard operating procedures (SOPs) ensure consistent task execution, reducing variability and enhancing efficiency. These procedures also outline maintenance schedules, minimizing unexpected breakdowns and downtime.
Advanced monitoring systems collect real-time data on machine performance through IoT sensors. This data undergoes analysis to identify patterns that indicate potential failures. Based on these insights, machine settings are adjusted in real-time to optimize production flow. Communication between system components ensures smooth coordination, while AI models refine predictions using historical data.
By implementing these strategies, companies can achieve long-term reliability and efficiency in rebar production. Continuous learning and adaptation ensure that robotic systems remain effective in meeting the evolving demands of modern engineering projects.
Addressing Workforce Concerns Early
Early engagement with the workforce is critical when implementing robotic production lines in tunnel rebar manufacturing. Employees often feel uncertain about how automation might impact their roles. Addressing these concerns proactively fosters trust and ensures a smoother transition to advanced systems.
1. Open Communication Channels
Management teams should establish clear communication channels to share the benefits of automation. Workers need to understand how robotic systems enhance productivity, improve safety, and create opportunities for skill development. Regular meetings and informational sessions can help clarify misconceptions and reduce resistance.
Tip: Use real-world examples to demonstrate how automation complements human roles rather than replacing them.
2. Comprehensive Training Programs
Providing robust training programs equips employees with the skills needed to operate and maintain robotic systems. Hands-on workshops and interactive sessions build confidence and competence. Training should focus on practical skills, such as troubleshooting and monitoring, while also emphasizing the long-term career benefits of learning advanced technologies.
3. Involving Employees in the Process
Involving workers in the planning and implementation stages creates a sense of ownership. Employees who contribute their insights feel valued and are more likely to embrace the changes. Collaborative efforts between engineers and operators ensure that the new systems align with existing workflows.
4. Addressing Job Security Concerns
Automation often raises fears about job displacement. Companies can alleviate these concerns by highlighting the creation of new roles, such as robot operators and maintenance technicians. Offering career development opportunities reassures employees about their future within the organization.
By addressing workforce concerns early, companies can build a collaborative environment where employees and robotic systems work together seamlessly. This approach not only enhances operational efficiency but also strengthens workforce morale and adaptability.
Future Implications and Trends

Advancements in Robotic Technology
Robotic technology continues to evolve, offering transformative possibilities for tunnel rebar manufacturing. Automation now enhances production efficiency by streamlining processes and reducing delays. Robots equipped with advanced precision tools minimize material waste during rebar cutting and bending. Intelligent monitoring systems further improve safety and ensure consistent quality throughout production.
Emerging innovations include seamless integration of material buffering and aligning systems. These advancements optimize workflows, reducing idle time and enhancing productivity. Robotic welding systems now deliver higher output while lowering labor intensity. Additionally, modern robots exhibit flexibility, adapting to diverse construction requirements with ease. These technological strides promise to redefine automation in tunnel construction, setting new benchmarks for efficiency and adaptability.
Potential for Wider Adoption in Tunnel Segment Production
The growing demand for efficient and reliable construction solutions positions robotic production lines as a cornerstone of tunnel segment production. Their ability to operate continuously and adapt to various configurations makes them ideal for large-scale projects. Companies increasingly recognize the value of automation in meeting tight deadlines and maintaining high-quality standards.
As robotic systems become more accessible, their adoption is likely to expand across the construction industry. Modular designs simplify integration, enabling companies to customize layouts for specific needs. Training programs equip workers with the skills to manage these systems, fostering a collaborative environment. These factors collectively support the wider implementation of robotic production lines, transforming how tunnel segments are manufactured.
Sustainability and Environmental Impact
Robotic production lines contribute significantly to sustainable construction practices. Advanced robotics optimize energy consumption by executing precise movements and minimizing idle time. Continuous operation reduces overall energy usage compared to traditional manual methods. High precision and repeatability ensure minimal material waste, scrap, and rework, conserving resources and reducing environmental impact.
By integrating automation, companies can achieve sustainability goals while maintaining efficiency. Robots enhance resource optimization, aligning with the industry’s shift toward environmentally conscious practices. These systems not only improve productivity but also support the broader objective of sustainable construction, paving the way for a greener future in tunnel manufacturing.
Role of AI and Machine Learning in Automation
Artificial intelligence (AI) and machine learning (ML) have become pivotal in advancing automation within tunnel rebar manufacturing. These technologies enable robotic systems to perform complex tasks with unparalleled precision and efficiency, transforming traditional production processes into highly optimized operations.
AI enhances automation by ensuring precise dimensional accuracy during rebar cutting and bending. This precision minimizes material waste and optimizes reinforcement layouts, which improves the structural integrity of tunnel segments. Machine learning algorithms analyze production data to identify patterns and predict potential issues, allowing systems to adjust operations in real-time. This adaptability not only boosts productivity but also shortens project timelines by reducing delays caused by manual interventions.
Robotic welding technology, powered by AI, further elevates automation standards. Intelligent systems equipped with spatial recognition ensure consistent welding quality, which enhances the durability of rebar structures. These systems also reduce labor intensity by automating repetitive and hazardous tasks, creating a safer work environment. By mitigating operational risks, AI-driven welding solutions contribute to the reliability and efficiency of tunnel construction projects.
Machine learning plays a critical role in predictive maintenance. Advanced monitoring systems collect real-time data from sensors embedded in robotic components. Algorithms process this data to detect anomalies and predict equipment failures before they occur. This proactive approach minimizes downtime and extends the lifespan of machinery, ensuring uninterrupted production.
The integration of AI and ML also supports multi-robot collaboration. These technologies enable robots to communicate and coordinate tasks seamlessly, enhancing overall efficiency. For example, AI-driven systems can allocate resources dynamically, ensuring that each robot operates at optimal capacity. This level of coordination allows production lines to adapt to varying demands without compromising quality.
AI and ML have redefined automation in tunnel rebar manufacturing. By combining precision, adaptability, and predictive capabilities, these technologies set new benchmarks for efficiency and reliability in modern construction projects.
The case studies demonstrate the transformative impact of robotic production lines in tunnel rebar manufacturing. These systems ensure exact dimensional accuracy, enhance structural integrity, and operate continuously to meet project deadlines. High-precision robots streamline processes, reduce material waste, and improve worker safety by automating hazardous tasks.
Key Benefits of Robotic Production Lines
Benefit | Description |
---|---|
Consistent Quality | Robots execute tasks with high precision, eliminating quality variations and human error. |
Increased Productivity | Robots can work tirelessly, significantly increasing production output compared to manual labor. |
Improved Worker Safety | Robots handle hazardous tasks, reducing the risk of workplace injuries for human workers. |
Cost Savings | Long-term savings from increased productivity and reduced labor costs offset initial investments. |
Flexibility | Robots can be reprogrammed for different tasks, enhancing manufacturing flexibility. |
Addressing challenges such as high initial costs and workforce adaptation is essential for maximizing success. Companies must invest in training programs and proactive maintenance strategies to ensure seamless integration and long-term efficiency.
Looking ahead, advancements in robotics, AI, and machine learning will redefine automation in construction. Technologies like robotic bricklayers and autonomous systems will enhance precision, reduce project timelines, and improve safety. As the industry embraces automation, these innovations will pave the way for sustainable and efficient construction practices.
The future of tunnel rebar manufacturing lies in intelligent automation. By adopting robotic production lines, companies can achieve unparalleled efficiency, quality, and safety, setting new benchmarks for the construction industry.
FAQ
What are the primary benefits of robotic production lines in tunnel rebar manufacturing?
Robotic production lines improve efficiency, precision, and safety. They operate continuously, reducing downtime and increasing output. High-precision robots ensure consistent quality, while automation minimizes human error. These systems also enhance worker safety by handling hazardous tasks, making them indispensable for modern tunnel construction projects.
How do robotic systems adapt to different rebar configurations?
Robotic systems use advanced technologies like multi-robot collaboration and 3D vision systems. These features allow them to adjust seamlessly to various rebar sizes and shapes. Flexible production line layouts further enhance adaptability, ensuring compatibility with diverse construction requirements.
Are robotic production lines cost-effective in the long run?
Yes, robotic production lines offer significant long-term savings. They reduce labor costs, minimize material waste, and lower maintenance expenses through modular designs. Real-time monitoring systems prevent costly disruptions, ensuring uninterrupted production. These factors make them a cost-effective solution for tunnel rebar manufacturing.
What role does AI play in robotic production lines?
AI enhances automation by enabling precise cutting, bending, and welding. Machine learning algorithms analyze production data to predict issues and optimize operations. AI-driven systems also improve multi-robot collaboration, ensuring seamless task coordination and boosting overall efficiency in tunnel rebar manufacturing.
How do robotic production lines improve worker safety?
Robotic systems automate hazardous tasks like welding and cutting, reducing the risk of workplace injuries. Intelligent monitoring systems detect potential issues early, minimizing manual intervention. By handling repetitive and dangerous processes, these systems create a safer work environment for workers.
Tip: Companies can further enhance safety by providing training programs for employees to manage and maintain robotic systems effectively.