The 22nd China International Industry Fair officially came to an end last week. As the epidemic lose its momentum in China, various companies boosted their confidence and gathered at CIIF with a brand new look. During the exhibition, QJAR exhibited a number of unmanned and intelligent demonstration lines through multiple application scenarios, pointing out an automatic road in the Post-COVID-19 manufacturing world.
Highlight of QJAR Robot At CIIF 2020, ShangHai
QJAR is one of the leading industrial robot manufacturers in China, now we got 4/6 axis robot with payload from 3kg to 800kg, which can be applied in welding, material handling, machine tool loading/unloading, palletizing, spraying, stamping, machine tending, etc.
Through the construction of the intelligent manufacturing ecosystem, QJAR Robot has become the “main force” to provide “technical output” for the intelligent manufacturing ecosystem. QJAR has formed a complete industrial chain from core components, complete robots, industrial software, system integration, digital and intelligent manufacturing applications, and ASD cloud platform services, and can provide other companies with integrated solutions for intelligent manufacturing, provide competitive and differentiated robots, and integrated application products, and provide high-quality total services for integrators and end-users.
The CEO of QJAR mother company ASD, Chen Helin and EVS CEO Sharon Xiao attended the 6th CEO Roundtable Conference of RS exhibition of CIIF, they shared their view of new opportunities and challenges of China’s robotics industry under global changes, saying that this is a great opportunity for Chinese robot supplier to go aboard to help more countries and companies upgrade their Industrial manufacturing.
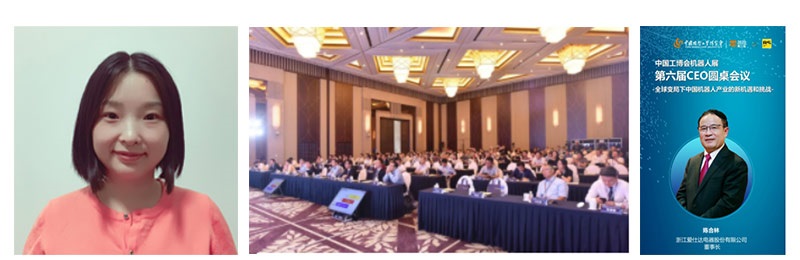
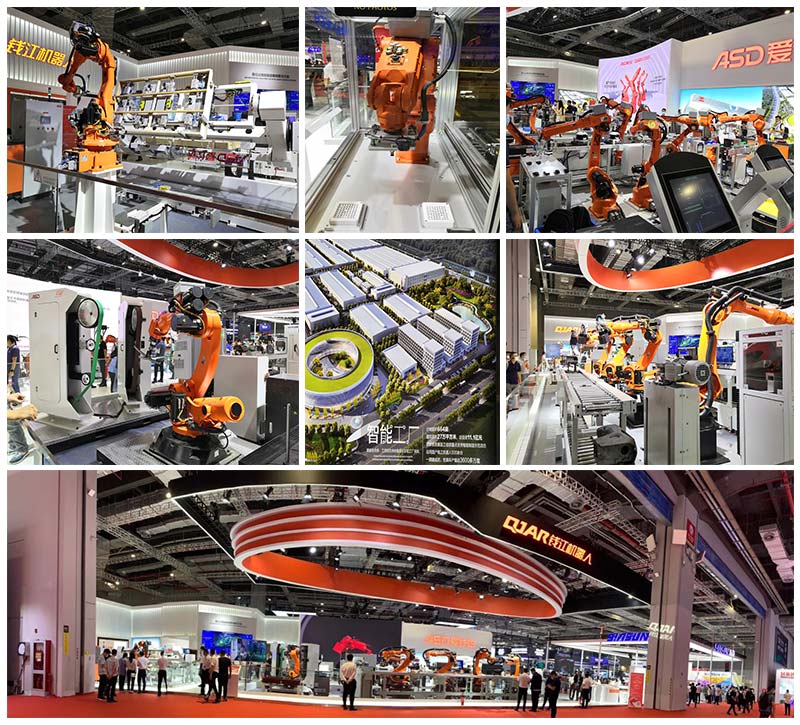
Let’s take a depth review of exhibited applications of QJAR robot:
1. C2M Assembly Line of ASD Rice Cooker
The C2M assembly line of ASD rice cooker is a major innovation and breakthrough in the household appliance industry. The assembly line consists of 11 stations. The first station shows the loading and unloading of the rice cooker by robots. The robots in the second and fifth work stations can accurately assemble parts and inspect whether they are assembled in place under the guidance of the vision system. The third and sixth work stations display robots to automatically feed and screw, and constantly monitor the screw torque data. The fourth station and the tenth station display robot to change the line to transport the rice cooker; the seventh station displays the new application of the robot with a flexible gripper to assemble the inner tank. The eighth and ninth work station uses the visual sensor and laser marking machine to detect and engrave characters on the rice cooker; the eleventh work station displays the robot to cooperate with AGV to store the rice cooker.
Application fields: household appliances, kitchen appliances, toys, medical treatment, electronic products, and other industries.
2. Automatic Grinding Production Line For Sewing Machine Shell
Case overview
A) Basic parameters: Production time: 40s, Material: HT, Working time: 8 hours per shift.
B) Robot model: 4 units QJR210-1 robot was used to polish the tool line.
C) Grinding method: manual clamping, laser displacement sensor to detect the shape of the workpiece, and guides the robot to grind according to the calculation results.
D) Grinding and polishing process: the grinding and polishing unit is composed of four polishing robots, and two parallel circulating conveying lines can realize the continuous polishing of robots.
Advantages:
The innovation analysis of the automatic polishing unit of casting uses a laser displacement sensor to detect the shape of the workpiece and guides the robot to grind according to the scanning results to ensure the consistency of grinding. Motorized spindle with special tools to improve grinding quality. The high-power 20kW flexible adaptive spindle grinding is used to realize the grinding along with the shape. By using two parallel circulating conveying lines, the continuous polishing of the robot can be realized and the production efficiency can be improved. Equipped with tool library to solve the problem of frequent replacement of repair consumables. Cooperate with the MES system to trace and manage product information and control product quality.
Application fields: Metal, automobile, home appliances, motorcycle, hardware, and other industries.
3. Five Star Chair Foot Grinding
Workstation introduction: This unit is mainly composed of robot, gripper, loading table, floating force control belt machine (single station), etc. It is mainly used for rough grinding and fine grinding of five-star chair foot, and can also be used for rough grinding and fine grinding of other metal parts or metal welding parts. This unit is equipped with 2 sets of floating force control belt machines (single station). According to the actual grinding process requirements, different specifications of abrasive belts can be configured to complete the rough and fine grinding of products.
The relevant configuration reference is as follows:
1. Industrial robot: load 210kg
2. Double station loading and unloading slide table and tooling
3. Floating force-controlled abrasive belt machine (rough): power of 5.5kW, speed of 2850rpm; with floating function; floating force can be set in the range of 20-300n as required; equipped with rubber wheel with a hardness of 45 degrees
4. Floating force-controlled abrasive belt machine (fine): power of 5.5kW, speed of 2850rpm; with floating function; floating force can be set in the range of 20-300N as required; equipped with rubber wheel with a hardness of 35 degrees
The process and beat are described as follows: (taking a five-star chair foot product as an example)
Rough grinding: the floating force-controlled abrasive belt machine (rough), equipped with 180 mm abrasive belt, rough grinding the whole part of the workpiece to be polished, the grinding time is about 4min
Fine grinding: the floating force-controlled abrasive belt machine (rough) is used with a 320 mm abrasive belt. The grinding time is about 4min. To sum up: considering the loading, unloading, and jumping time, the overall grinding beat of the five-star chair foot is about 8.5min/piece.
Product advantages: Good product compatibility: switch gripper and tooling can also be used for grinding other metal parts. Strong expansibility: it can be operated independently or in series with similar stations. Application fields: It is mainly used for rough grinding and fine grinding of five-star chair foot, and can also be used for rough grinding and fine grinding of other metal parts or metal welding parts.
4. Intelligent Surfacing Working Station
This “intelligent surfacing working Station” consists of seven parts: QJRB20-1 transport robot, QJR6-1400 arc welding robot, welding system, L-type positioner, fixture, vision system, and welding management system.
The main workflow is as follows:
1. Visually identify the position of incoming material and finished product frame
2. The handling robot grabs the raw materials with electromagnetic chuck and clamps them to the positioner
3. Arc welding robot carries out a surfacing operation on raw materials
4. The handling robot switches the pneumatic gripper to grab the finished product and put it into the finished product frame
5. Transfer the robot back to the electromagnetic chuck and repeat the above actions
The application of the vision system reduces the requirements of feeding and stacking of finished products, reduces manual intervention, and makes the whole working line more automatic. The intelligent welding management system based on MES can effectively collect the parameters in welding production and control the product quality.
5. Palletizing Work Station
Workstation introduction: the workstation displays the whole row of palletizing robot units. The palletizing fixture can complete one, multiple, and one row of palletizing tasks at a time according to the stacking type information, and can realize flexible palletizing tasks. The system consists of JXSS special sponge suction device, high-pressure fan, fan control unit, and pipeline package system.
Product advantages: flexible palletizing, strong adaptability; highly integrated seriation; can adapt to the palletizing tasks of different application scenarios according to customer requirements; the fan system adopted has low gas consumption and energy saving.
Application fields: food, beverage, tobacco, wine, sugar, tea, and other FMCG industries; medicine, e-commerce, logistics, supermarket and other carton container palletizing applications.
6. Steel Structure Welding Working Station
This set of “steel structure welding working station” consists of five parts: Qianjiang QJR6-1400 arc welding robot, welding system, head and tail positioner, fixture, and laser recognition system.
The main workflow is as follows:
1. The laser recognition system identifies the workpiece offset
2. Arc welding robot starts welding work
The laser recognition system can effectively solve the defects such as inaccurate clamping and positioning and deformation of parts caused by the weight and structure characteristics of steel structure workpiece, which is not conducive to welding automation.
Workstation introduction: It is equipped with an intelligent arc welding system. In order to deal with the relevant errors such as loading and unloading of medium and heavy plates and welding deformation, it is equipped with laser seam positioning and tracking function, which is used for real-time and accurate tracking of welding seam in the welding process. With the addition of an external turnover mechanism, the steel structure workpiece and the robot welding gun can be in the best processing position. Under the premise of ensuring the welding quality, welding processing is fast and effective. Extended slide rail application to meet the one-stop welding requirements of long steel structures. Equipped with digital communication arc welding power supply, and processing with collaborative operation function, so that the overall workstation work more smoothly, improve the welding quality and efficiency.
Product advantages: It is suitable for steel structure medium and heavy plate welding processing. The assembly error and welding deformation error can be solved by laser positioning and tracking function. The application of positioner and slide rail can be expanded to meet the one-stop-all position welding processing of steel structure. The high-power digital power supply is equipped with a water-cooling system to meet the continuous welding requirements of thick plates.
Application fields: It can be used in shipbuilding, construction machinery, coal machinery, steel structure, and pressure vessel manufacturing, and other medium and heavy plate processing industries.
7. Upholstered Furniture Nailing Automation
This work station consists of 6 axis robot, K type positioner, an automatic nailing gun, fixture, etc.
Confifuration:
Robot: QJR50-1 6 axis robot, 50kg payload, 2012mm arm span, ±0.07mm accuracy.
K type positioner: main axis rotation speed≤5R/min, second axis rotation speed≤8 R/min
Nailing gun: MEITE
Fixture: electromagnetic valve controller, air cylinder
Gripper: aluminum profile
Safety fence: aluminum profile
Advantages: Automatic orthopaedic, high stability, high compatibility.
Application fields: upholstered furniture, and other industry which needs nailing.
8. Ultra Precise Robot Detection Work Station with Linear Motor
Workstation introduction: This workstation adopts the latest product of Qianjiang robot, the small six-axis robot, with the marble platform of a linear motor and ARHawkVision intelligent vision platform, which is fully developed independently, to realize the organic combination of the six-axis robot, linear motor, and 2D vision, and become an intelligent ultra-precision linear motor robot detection workstation with high efficiency, flexibility, and precision. Extremely high positioning accuracy, speed, and mature control system can effectively and stably shorten the detection period and improve the production efficiency by stabilizing quality and quantity. To provide customers with more flexible robot vision detection solutions.
Product advantages: The robot: Stable performance: fully imported configuration, the rich and reliable experience of integrated projects application. High-cost performance: the best combination of quality and cost. Strong compatibility: support IO/bus and other external communication protocol requirements.
Linear motor marble platform:
Direct drive: linear motor drive, no screw/belt/chain, and another traditional transmission mechanism, compact and simple structure.
Control scheme: it provides a full closed-loop integrated solution from control to drive to transmission. The excellent synchronous drive of two shafts of the gantry is more stable to ensure the production quality.
Communication protocol: The unique and stable bus protocol can effectively avoid the interference of the interference source to the precision of the pulse control mode.
High speed and precision: acceleration up to 3G, speed up to 4M/S, repeatable positioning accuracy up to ±0.005mm.
Application Field:
1. Optical/acoustic and other high-precision detection/assembly equipment.
2. COG/FOG/COF high precision detection/binding equipment
3. Laser welding/cutting equipment with high differential compensation performance in the lithium battery industry
4. Photovoltaic module industry typesetting and transplanting equipment
5. Wafer cutting equipment
6. Semiconductor chip packaging equipment;
Last Words: If you are interested to cooperate or if you have an automation project please feel free to discuss more.