Explore Robotic Laser Welding With a 30-year Expert
In this video, we share the important points you need to know about robotic laser welding projects. After extensive efforts, we’ve made an exclusive visit with an expert who has over 30 years of experience in the laser welding industry.
In this video, we’ll share the insights and professional perspectives of this seasoned specialist. Stay tuned till the end – you don’t want to miss this. The demand for robotic laser welding is on the rise in the global market. Today, we delve into the heart of this technology: Is robotic laser welding a mature and reliable option now? When it comes to choosing a welding solution, How should customers choose among robotic laser welding, TIG welding, or MIG/MAG welding? As we know, the key to any robotic project is reliability and minimizing risk. We’ll explore the difference on welding methods and which equipment is optimal and what critical factors to consider during selection on equipment of robotic laser welding.
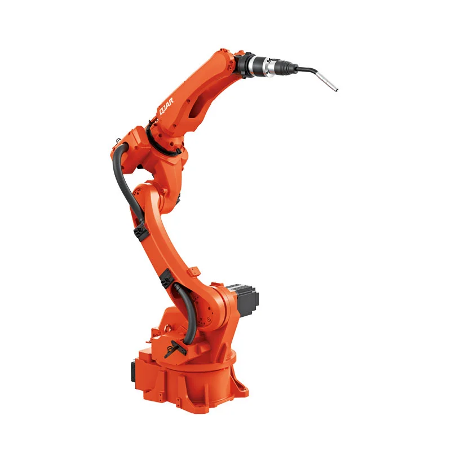
Critical Factors to Consider for Laser Welding Robot:
- We’ve emphasized that aligning the working process standard with customer needs is crucial, and the selection of laser power must be based on the material, thickness, and quality requirements of the welding task.
- The choice of robot involves considering load capacity, precision, and rigidity, and ideally, should come with a dedicated laser welding software package, which many robot companies currently lack.
- We’ve also stressed the importance of conducting sample welding tests before confirming a project plan.
- Robotic laser welding can be applied in numerous metalworking industries. In China it’s particularly applied in thin sheet welding for new energy vehicles and home appliances, though it remains an expensive option. However, its costs have significantly reduced in recent years. As laser welding becomes more cost-effective, it’s likely to replace a substantial market share of traditional TIG welding, and it’s a trend we’re already observing.
- The advantages of laser welding are: higher efficiency, better welding seam formation, minimal spatter, smaller weld pool, and aesthetically pleasing welds that could eliminate the need for grinding. And the disadvantage is its higher cost.