When adding mobile welding robot into your production line, there are various factors to keep in mind – from equipment design and system layout, safety considerations and how it will impact current employees.
These robots can perform and manage welding tasks while keeping workers safe. However, for optimal results they require the appropriate welding fixture that allows parts to be held securely in place for precise results.
The Future of Mobile Welding Robot
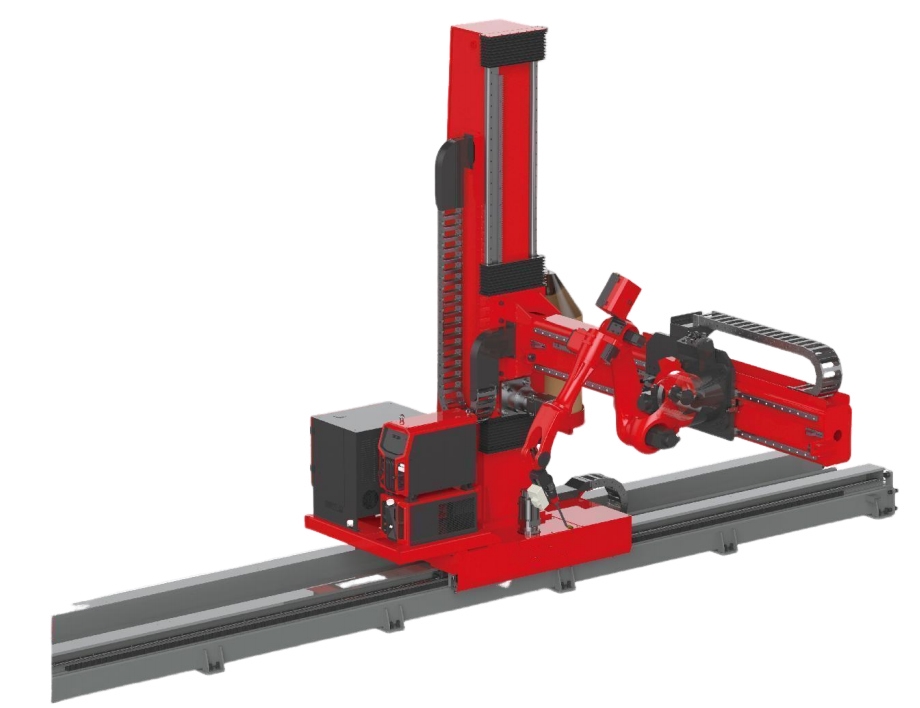
Mobile Welding robotics is revolutionizing manufacturing. They help to increase productivity and quality. While initial investments may seem high, fabricators typically find that the benefits quickly outweigh any associated costs. By cutting wasteful costs such as rework and decreasing overall manufacturing costs, prices per part drop significantly; plus welding cobots allow skilled welders to focus their skillset more specifically than before – an effective combination of human expertise with automated efficiency.
Mobile welding robots are versatile and can be easily moved between projects or sections in a factory. This eliminates expensive safety cages, while allowing workers to move around more freely. Furthermore, this increases worker safety by keeping them away from potentially hazardous work areas with hazardous fumes, heat or electrical hazards.
Mobile welding robots are game changers because of their easy programming process. Many robots employ “teach by demonstration” for learning how to weld, meaning all an operator needs to do is move their arm around to show where to weld – far easier than programming traditional industrial robots which may take days! Mobile welding robots are ideal for low-volume jobs and products that change frequently, as they can be set up in minutes.
Despite their many advantages, welding robots still require people to set them up, program them, operate them and inspect. Welders can remain a part of the industry by working with robots, rather than replacing them. They also have opportunities to upgrade their skills and become familiarized with technology.
Increased Efficiency
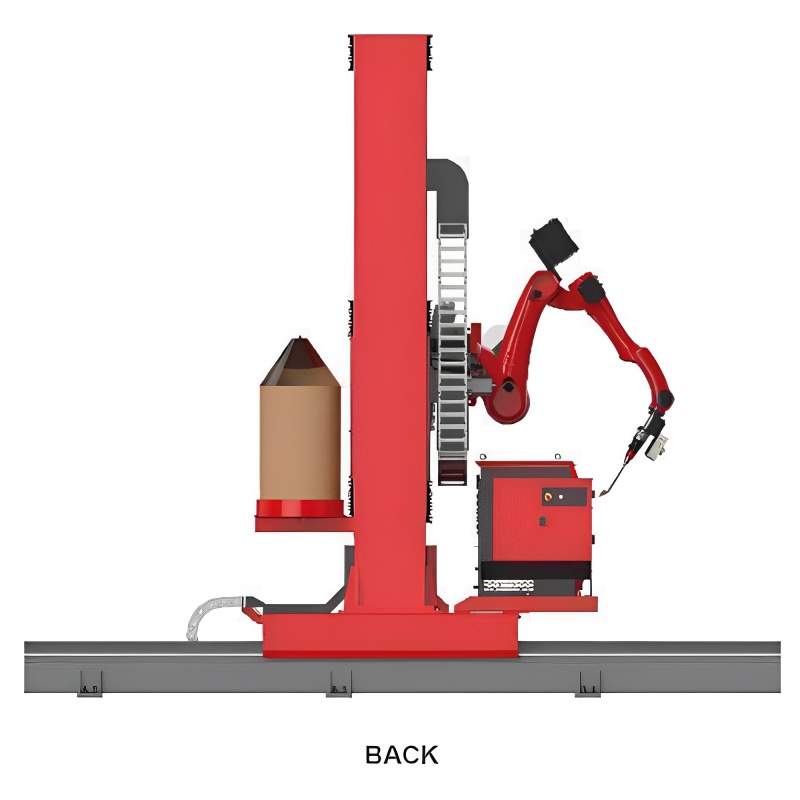
Robot welding is far more efficient than its manual equivalent, cutting weld time, material waste and energy consumption through precision execution which reduces rework and material wastage. They are also characterized by a high level of consistency, making them ideal for low-volume, high-mix productions.
Mobile welding robots are a great way to save money on labor costs, energy costs and materials while increasing productivity and quality of the welds. It also reduces downtime because it reduces the frequency of machine startup, which consumes resources.
It is important to identify which welding tasks need automation before investing in a mobile robot. This will allow you to determine the potential ROI of your investment and whether it makes sense for your company.
It is important to optimize your welding robot’s operation over time. Aspects of its operation such as power and wire usage, robot position/tracking capability and gas consumption should all be optimized as this can significantly decrease maintenance and repair expenses over time.
No matter the size or configuration of your shop, robotic automation can fit seamlessly into current workflows without disrupting current processes or requiring additional equipment. This is especially applicable to smaller shops, where space and cost may not be a concern. Additionally, mobile welding robots can enable smaller shops to accept work they would otherwise have declined – creating additional revenue streams.
Cleaning stations and peripherals can be added to robotic welding cells for mobile welding robots. This will increase their productivity. A spatter removal station, for instance, can help decrease downtime and extend consumable lifespan by clearing away excess debris from front end of guns before reuse; this helps increase throughput while simultaneously decreasing MIG gun swap out frequency saving time and money in exchange for higher throughput productivity and throughput rates.
Scalability
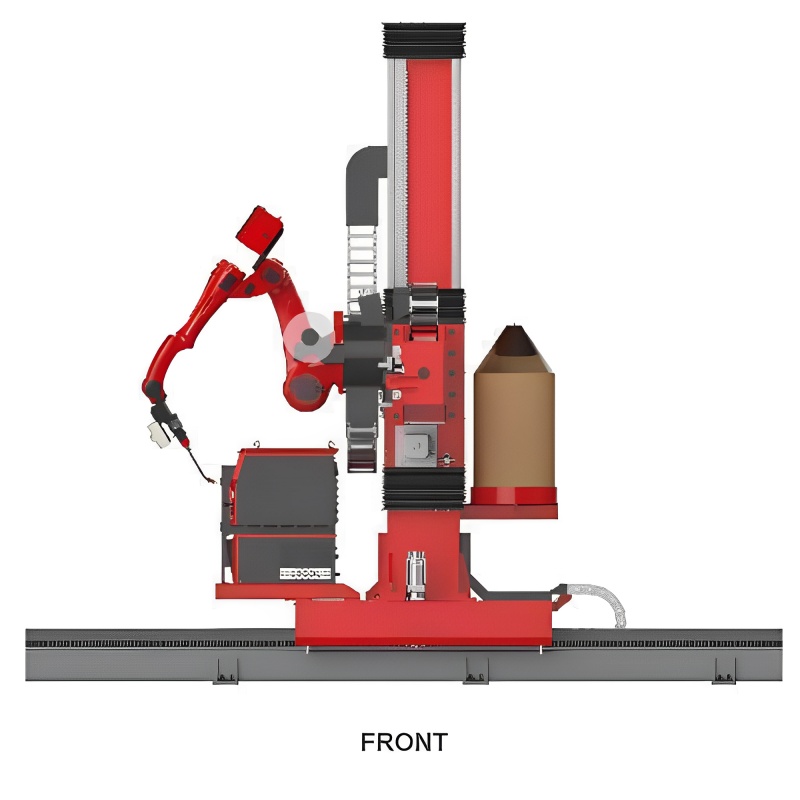
Mobile robots are an ideal solution for dynamic environments. They can be quickly redeployed, programmed to perform new welding tasks and reduce costs by eliminating the need for manual labor.
The Nine Axis Cantilever Weld Station is designed to work in any environment. It seamlessly collaborates with manual welders, while offering productivity gains and a greater ROI from robotic automation. Unlike traditional industrial robotics that require weeks of training for your manual welders and full CAD programming, Nine Axis Cantilever Weld Station is fully programmed using an easy-to use interface. It’s the perfect solution for shipyards or offshore platforms, renewable power farms, mining, or any industrial setting requiring fast automation while accommodating valuable welding workforces.
Before choosing a mobile welding robot, it is essential that you understand exactly what your requirements are. Determine what materials will be being welded as well as your production volume and current setup so the robot will fit seamlessly into your workflow. Consider your initial investment costs such as installation, software updates and reprogramming requirements in response to changing production demands; additionally examine safety features and user friendliness of systems available so as to meet company standards and needs.
Mobile welding robots are easier to set up due to their small footprint. Plus, their mobility means they can fit in tight spaces where fixed robots may not. Cobots can be mounted on carts and wheeled to any part in your facility. This allows for maximum flexibility.
Nine Axis Cantilever Welding stands out from its competition by being not only mobile but also boasting a comprehensive collection of accessories to increase its versatility in handling welding jobs. Fixtures and positioners enable precise positioning to reduce cycle times while improving arc-on times while improving weld quality.
Integrating a mobile robot into your production line allows you to increase your capacity when needed and reduce it in periods of low demand. This keeps your business competitive on any market. This unparalleled scalability, when combined with the other benefits of robotic automation creates an unparalleled flexibility which is revolutionizing manufacturing.
Safety
A welding robot can reduce the amount of heat workers are exposed to, reducing medical costs and helping them stay healthy. Its implementation into production processes brings new safety concerns. Accidents can occur if the welding robot system is not properly managed or if its operator does not follow proper protocols while interacting with it. Errors like programming errors or hardware malfunctions can cause unexpected movements which result in dangerous, sudden arm swings that cause injuries or damage in an unintended manner.
Industrial robots should be operated in caged environments that are clearly separated from workers. Collaborative robots, on the other hand, are designed to share workspaces with humans. They have safety features built in to minimize the risk of harming humans. These include collision detection sensors, which help adjust or stop movements to avoid colliding, hand-guiding systems, which allow operators to manually maneuver the cobot to reduce accidental collisions, and emergency stop buttons around its exterior to enable rapid emergency shutdown.
It is essential that the mobile welding robot deployment process does not include any tools or debris which could be a danger during operations. Therefore, regular visual inspections should be conducted in order to identify potential hazards and take remedial actions where needed. In addition, performing functional tests on your robotic system regularly to make sure all safety mechanisms are functioning as intended is also highly recommended.
A risk assessment must include measures to mitigate identified hazards, measure their frequency and severity. This is especially important for robotic welding robots with high voltage power systems that require lockout/tagout devices and procedures. This can help prevent fire or shock hazards caused by these devices. By identifying risks associated with welding robots manufacturers can better prioritize necessary maintenance and safety measures for these systems; for example identifying high voltage electric risks with such machines could enable manufacturers to prioritize maintenance and safety measures more easily – for instance requiring high voltage power may pose electrical hazards if maintained improperly by an electrician who fails to implement lockout/tagout procedures; failure may cause shock or fire risks as a result.