An automated welding robot cell can help manufacturers enhance quality, safety, efficiency, and cost. Before making the investment in such technology, several factors need to be considered.
As well as robotic welding equipment and positioners, additional items like positioners, safety features, fume extraction systems and conveyors may be required to optimize workflow and ensure maximum productivity. A welding robot cell may require a high initial investment that takes time to recoup.
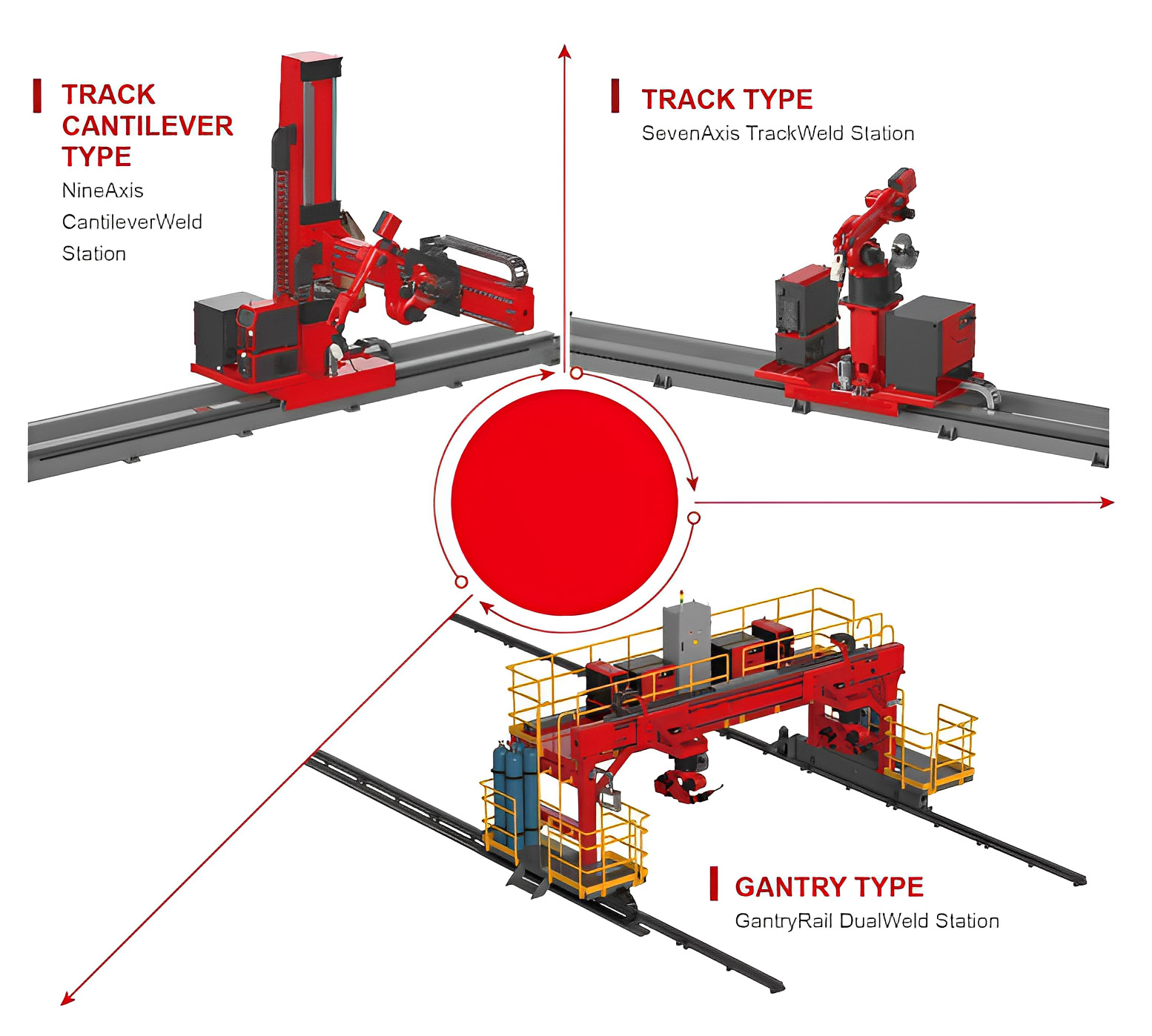
Cost-Effectiveness
Robotic welding cells offer a cost-effective solution for improving productivity, quality and safety in manufacturing. When integrated with other automated systems for seamless production flows, robotic welding cells can help bridge a skilled welder shortage and maintain production levels. Furthermore, data collected via robotic welding cells can also be analyzed and optimized further for analysis purposes.
Robot welding cells may initially cost more than traditional manual weld shops; however, their long-term advantages more than justify their initial investment. Increased productivity, decreased labor expenses and lower waste production all add up to significant cost savings over time. Furthermore, robotic welding cells can often be reconfigured for new applications, further increasing return on investment over time.
As opposed to humans, robotic welders can operate continuously without slowing down or needing breaks, making them far more efficient at saving effort and materials such as fillers and nozzles that would otherwise go to waste. Furthermore, robotic welders are safe enough to work in hazardous environments where humans would otherwise be at risk of injury.
If you are considering installing a welding robot cell, it’s best to start out slowly and expand as necessary as your experience increases. Preconfigured systems make setup even simpler for quick start up.
Safety
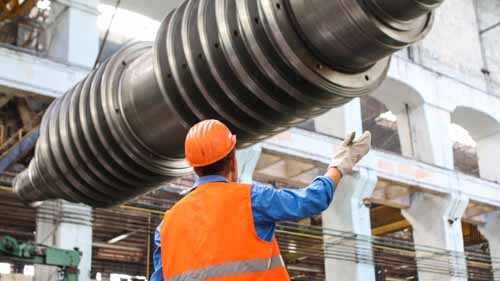
A welding robot cell can be an ideal solution for high-volume production processes that involve repetitive low-skilled work. It improves efficiency, quality and safety while decreasing labor costs and increasing ROI. But before investing in one, businesses should carefully evaluate all aspects of it – including factors like initial investment cost and potential return on investment as well as skilled technicians available to oversee these systems.
Manufacturers of robotic MIG guns typically incorporate design features to increase safety. For instance, certain guns feature front-loading liners to make replacing the liner easier without entering the weld cell and an insulating disc to decrease current usage during maintenance – both features can help prevent accidents and minimize injuries for employees working nearby.
Light curtains, control systems, enclosures to limit fumes and sparks and safety fences are among the many safety features available to robot users. A control system provides information about robot movements as well as any relevant variables; while enclosures help limit noise pollution. A safety fence also serves to shield workers from welding arcs.
Efficiency
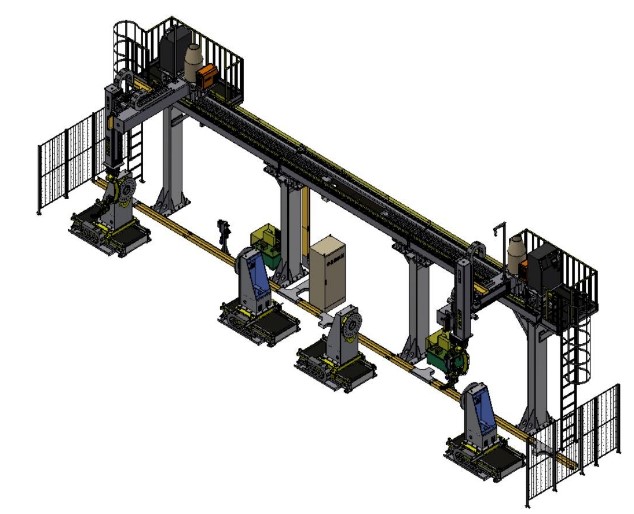
A welding robot cell provides increased efficiency by automating processes and increasing production, as well as improving quality to reduce rework and lower costs. Plus, its versatility enables it to operate in hazardous environments where human welders may be unsafe – making them an attractive solution for companies facing labor shortages.
Robotic welding provides significant uptime benefits. In contrast to manual welding, robotic cells are available 24/7 without interruption for breaks or lunch breaks, leading to significant increases in throughput and productivity daily.
Offline programming also enables robots to make significant incremental improvements quickly without disrupting productivity, which is particularly useful when performing laborious processes such as nozzle cleaning.
Cobot welding cells are an ideal choice for businesses with dynamic production needs, with user-friendly software making reprogramming and redeployment easy. Their safety sensors create a safe work environment if any people or objects come into the path of the robot and it even features stop movement protection if resistance or force increases beyond a preset threshold level. Cobot welding cells also make for an efficient use of limited office space.
Customization
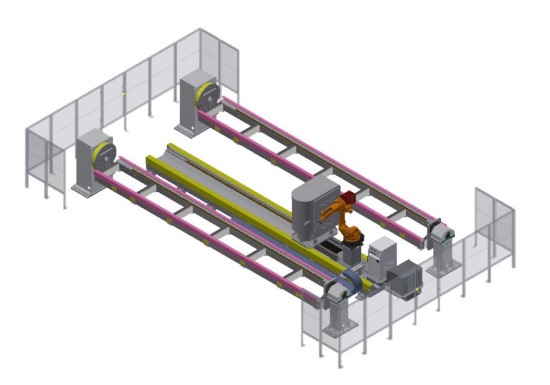
A welding robot cell can be tailored to meet specific manufacturing goals and production needs, enabling manufacturers to maximize efficiency, quality, safety, reliability, and consistency during welding operations.
Dependent upon your application, different kinds of welding robots may be suitable for use in robotic welding cells. SCARA robot arms, in particular, are great choices for high-speed welding applications as they use three perpendicular axes that move in straight lines to provide accuracy during assembly lines; additionally they can also provide flexible motion systems for accessing hard-to-reach areas.
A typical welding robot cell includes a robot arm for welding operations, power supply and wire feeder equipment, control software to monitor movement and weld parameters of the robot arm, as well as positioning equipment like rotary tables or positioners to position parts for welding; additional cell components may include safety features like light curtains or fences as well as fume extraction systems.