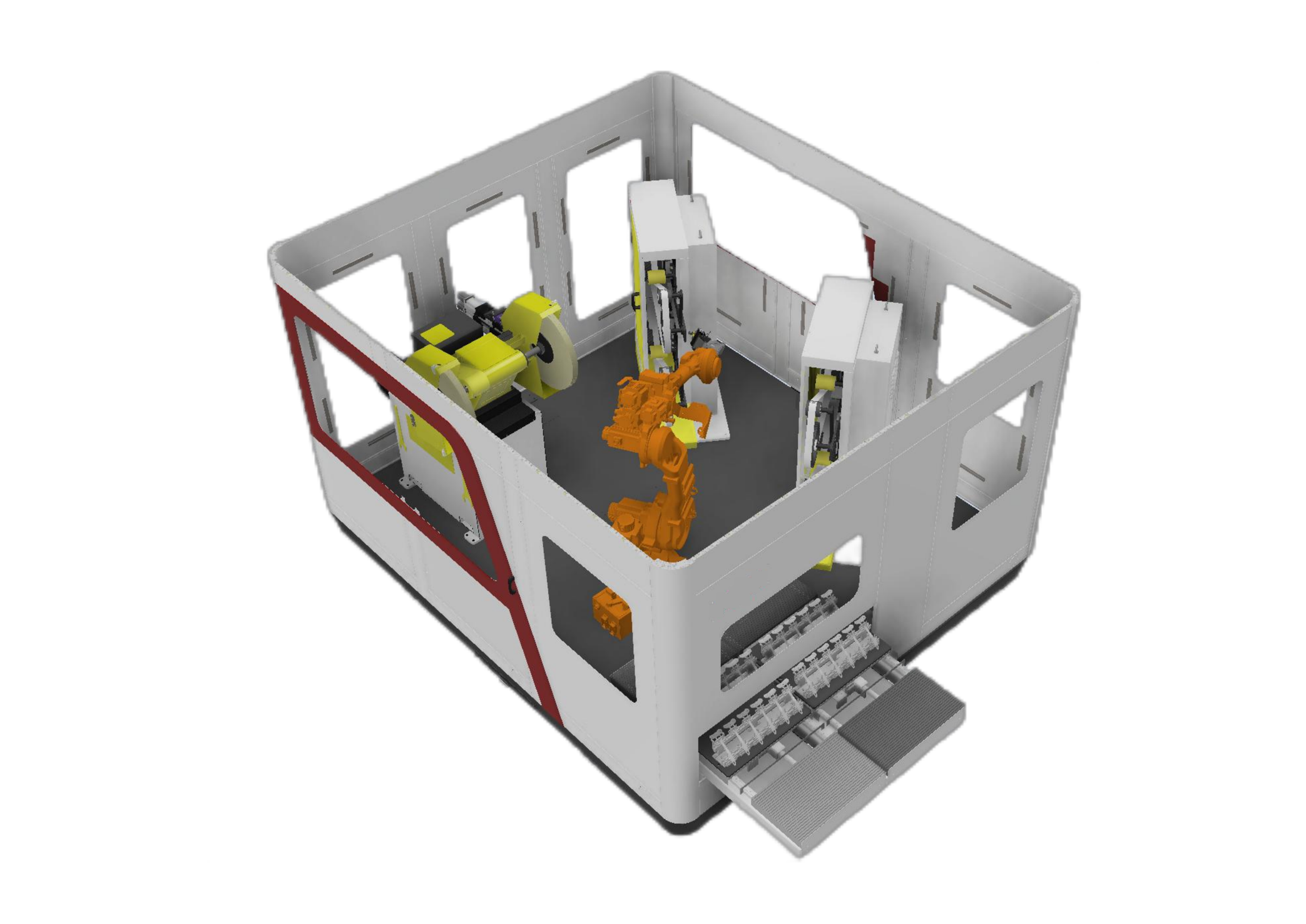
Imagine a world where medical devices are crafted with unparalleled precision, where every surface is polished to perfection, and where human error is a thing of the past. This isn’t science fiction—it’s the reality of high-precision 3D polishing robots in medical device manufacturing.
In an industry where microns matter and lives are on the line, the demand for flawless medical devices has never been higher. Traditional manufacturing methods are struggling to keep up, leaving medical professionals and patients at risk. But there’s a revolutionary solution on the horizon: advanced robotics that can polish complex 3D surfaces with astounding accuracy.
As we delve into the world of high-precision 3D polishing robots, we’ll explore how these marvels of engineering are transforming medical device manufacturing. From the rise of precision robotics to the intricate workings of 3D polishing technology, we’ll uncover the benefits, applications, and challenges of this groundbreaking technology. Join us on a journey into the future of medical manufacturing, where innovation meets precision to create devices that save lives.
The Rise of Precision Robotics in Medical Manufacturing
Enhancing quality control in medical device production
High-precision 3D polishing robots have revolutionized quality control in medical device manufacturing. These advanced machines ensure consistent surface finishes and dimensional accuracy, critical for medical devices’ safety and effectiveness. By utilizing sophisticated sensors and algorithms, polishing robots can detect and correct minute imperfections that human operators might miss.
Quality Control Aspect | Traditional Methods | Polishing Robots |
---|---|---|
Surface Finish | Variable | Consistent |
Dimensional Accuracy | ±0.1 mm | ±0.01 mm |
Defect Detection | Limited | Comprehensive |
Process Repeatability | Moderate | High |
Improving efficiency and reducing human error
The implementation of polishing robots in medical device manufacturing has led to significant improvements in efficiency and error reduction. These robots can work continuously without fatigue, maintaining high precision throughout extended production runs. Key benefits include:
-
Increased production speed
-
Reduced material waste
-
Minimized rework and scrap rates
-
Enhanced product consistency
Meeting stringent regulatory requirements
Polishing robots play a crucial role in helping medical device manufacturers meet strict regulatory standards. Their precise and documented processes ensure:
-
Traceability of each manufacturing step
-
Consistent quality across batches
-
Compliance with FDA and ISO standards
-
Detailed record-keeping for audits
As regulatory requirements continue to evolve, the adaptability of polishing robots becomes increasingly valuable. Their programmable nature allows for quick adjustments to meet new standards, ensuring that medical device manufacturers stay compliant in a dynamic regulatory landscape.
Understanding 3D Polishing Technology
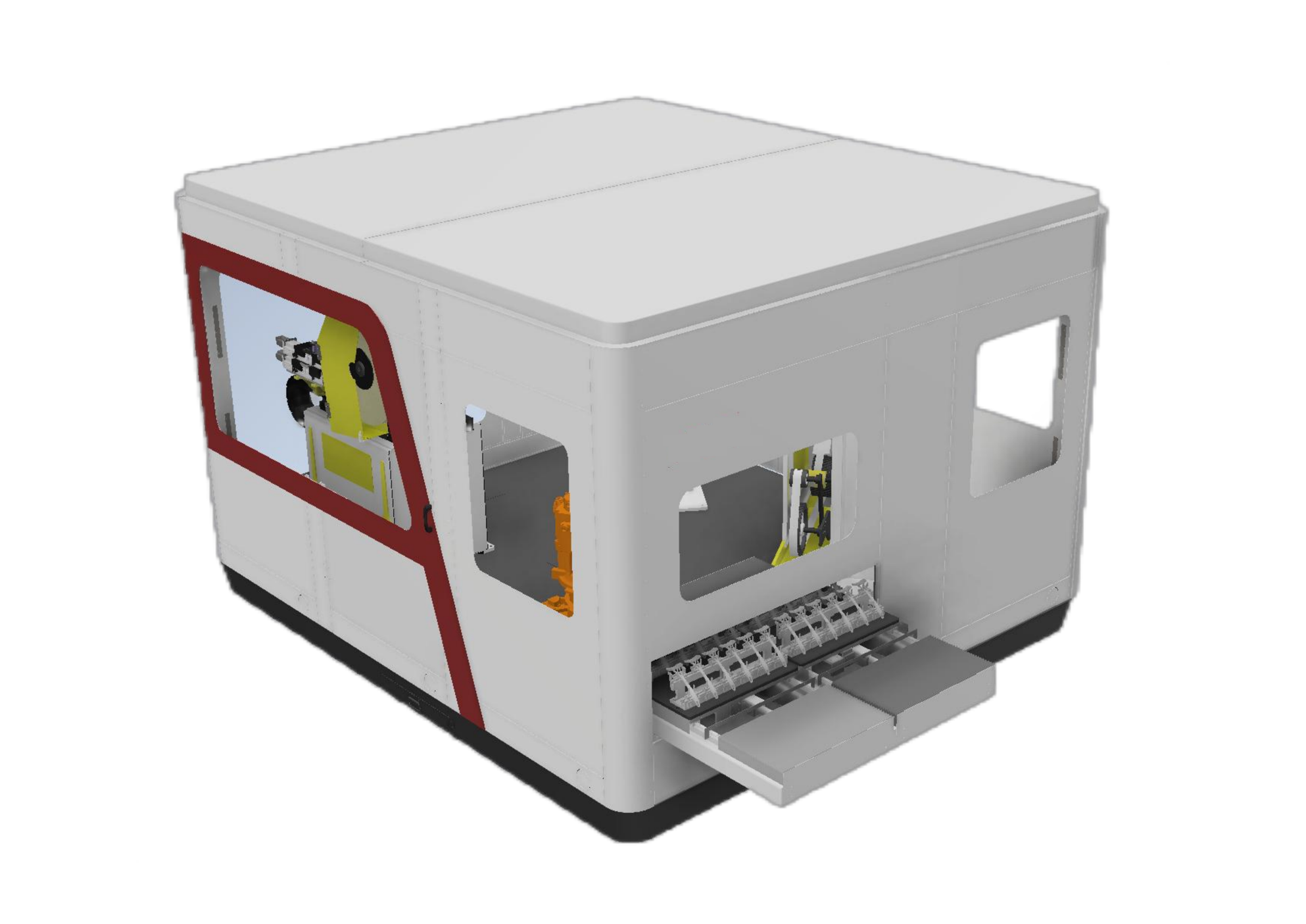
Advanced sensors and imaging systems
High-precision 3D polishing robots rely on cutting-edge sensors and imaging systems to achieve unparalleled accuracy. These advanced technologies enable real-time surface analysis and feedback, ensuring optimal polishing results for medical devices.
-
Optical sensors: Measure surface roughness and detect imperfections
-
Force sensors: Monitor applied pressure during polishing
-
Laser scanners: Create detailed 3D maps of complex geometries
Precision control algorithms
The heart of 3D polishing robots lies in their sophisticated control algorithms. These algorithms process data from sensors and imaging systems to guide the robot’s movements with micron-level precision.
Algorithm Type | Function |
---|---|
Path planning | Optimizes polishing trajectories |
Force control | Regulates applied pressure |
Adaptive feedback | Adjusts parameters in real-time |
Adaptive polishing techniques
Polishing robots employ adaptive techniques to accommodate variations in surface properties and geometries. This flexibility ensures consistent results across different medical devices and materials.
-
Variable speed control
-
Multi-axis motion capabilities
-
Intelligent tool selection based on surface characteristics
Materials compatibility
3D polishing robots are designed to work with a wide range of materials commonly used in medical device manufacturing. This versatility is crucial for maintaining high-quality finishes across diverse product lines.
-
Metals: Stainless steel, titanium, cobalt-chrome alloys
-
Plastics: PEEK, UHMWPE, acrylic
-
Ceramics: Zirconia, alumina
With these advanced features, 3D polishing robots are revolutionizing the medical device manufacturing industry. Next, we’ll explore the numerous benefits these high-precision robots bring to the production process.
Benefits of High-Precision 3D Polishing Robots
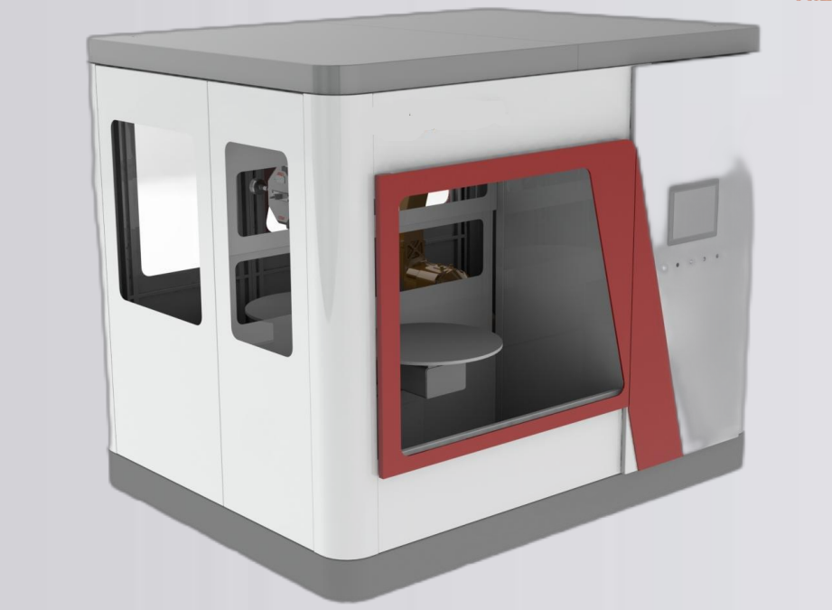
Achieving consistent surface finishes
High-precision 3D polishing robots excel at delivering uniform surface finishes across medical devices. Unlike manual polishing, which can be prone to human error and fatigue, these robots maintain consistent pressure and movement throughout the polishing process. This results in:
-
Improved product quality
-
Reduced rejection rates
-
Enhanced aesthetic appeal
Manual Polishing | Robotic Polishing |
---|---|
Inconsistent results | Uniform finishes |
Prone to human error | Precise, repeatable outcomes |
Variable pressure | Controlled, consistent pressure |
Handling complex geometries
One of the most significant advantages of 3D polishing robots is their ability to navigate intricate shapes and hard-to-reach areas. This capability is crucial for medical devices with:
-
Curved surfaces
-
Internal cavities
-
Micro-features
Polishing robots can be programmed to follow complex paths, ensuring every surface receives the required treatment.
Increasing production speed
Automation through polishing robots significantly boosts production efficiency:
-
24/7 operation capability
-
Faster processing times
-
Reduced setup and changeover periods
Reducing material waste
Precision control in robotic polishing minimizes material removal, leading to:
-
Optimized use of raw materials
-
Decreased scrap rates
-
Lower production costs
Enhancing product longevity
The superior finish achieved by high-precision polishing robots contributes to extended product life:
-
Improved corrosion resistance
-
Enhanced wear resistance
-
Better performance in implantable devices
These benefits collectively result in higher-quality medical devices that meet stringent industry standards and improve patient outcomes. As we explore further, we’ll see how these advantages translate into specific applications within medical device manufacturing.
Applications in Medical Device Manufacturing
Orthopedic implants
High-precision 3D polishing robots have revolutionized the manufacturing of orthopedic implants. These advanced machines ensure smooth, precise finishes on hip replacements, knee joints, and spinal implants. The robots can navigate complex geometries, maintaining consistent pressure and speed to achieve uniform surface finishes.
Implant Type | Benefits of Robotic Polishing |
---|---|
Hip replacements | Enhanced wear resistance, improved longevity |
Knee joints | Reduced friction, increased patient comfort |
Spinal implants | Optimized surface for bone integration |
Cardiovascular devices
In the realm of cardiovascular devices, polishing robots play a crucial role in producing stents, heart valves, and pacemaker components. The precision offered by these robots is paramount in creating devices that interact seamlessly with delicate cardiovascular tissues.
-
Stents: Ultra-smooth surfaces to prevent blood clot formation
-
Heart valves: Perfectly polished leaflets for optimal blood flow
-
Pacemaker components: Flawless finishes to enhance biocompatibility
Dental prosthetics
The dental industry has embraced polishing robots for creating high-quality dental implants, crowns, and bridges. These robots can achieve mirror-like finishes on various materials, including titanium and ceramics, ensuring both aesthetic appeal and functional excellence.
Surgical instruments
Polishing robots have significantly improved the manufacturing of surgical instruments. From scalpels to endoscopes, these robots ensure that each instrument meets the highest standards of precision and cleanliness.
Now that we’ve explored the diverse applications of polishing robots in medical device manufacturing, let’s examine the challenges that come with implementing this technology in healthcare settings.
Overcoming Challenges in Implementation
Initial investment costs
While high-precision 3D polishing robots offer significant benefits, the initial investment can be substantial. Here’s a breakdown of the costs involved:
Cost Component | Description |
---|---|
Robot Hardware | The core polishing robot system |
End Effectors | Specialized tools for various polishing tasks |
Software | Control and programming systems |
Integration | Installation and setup in existing facilities |
Training | Initial staff education and certification |
To mitigate these costs, consider:
-
Phased implementation
-
Leasing options
-
Government grants or tax incentives for advanced manufacturing
Integration with existing manufacturing processes
Seamlessly integrating polishing robots into current production lines requires careful planning. Key steps include:
-
Process mapping to identify integration points
-
Workflow redesign to optimize robot placement
-
Updating quality control procedures
-
Establishing communication protocols between systems
Staff training and adaptation
Adopting new technology often faces resistance. To ensure smooth implementation:
-
Provide comprehensive training programs
-
Encourage hands-on experience with the robots
-
Highlight career development opportunities
-
Create a support system for ongoing learning
Customization for specific medical devices
Polishing robots must be tailored to handle diverse medical devices. This involves:
-
Developing device-specific polishing programs
-
Creating custom end effectors for unique geometries
-
Fine-tuning force control for delicate components
-
Implementing vision systems for complex shapes
By addressing these challenges systematically, manufacturers can successfully integrate high-precision 3D polishing robots into their medical device production processes. This leads to improved quality, efficiency, and consistency in the final products.
Future Trends and Innovations
AI-driven polishing optimization
AI-driven polishing optimization is revolutionizing the field of high-precision 3D polishing robots for medical device manufacturing. By leveraging machine learning algorithms, these systems can:
-
Analyze surface characteristics in real-time
-
Adapt polishing parameters dynamically
-
Predict optimal polishing paths
This results in:
Benefit | Description |
---|---|
Improved quality | Consistently achieving higher surface finishes |
Reduced cycle time | Optimizing polishing sequences for efficiency |
Minimized material waste | Precise material removal based on part geometry |
Collaborative robot systems
The integration of collaborative robots (cobots) with polishing robots is enhancing flexibility and safety in medical device manufacturing. These systems offer:
-
Human-robot interaction for complex polishing tasks
-
Easy programming and repurposing for different products
-
Compact designs suitable for cleanroom environments
Integration with 3D printing technologies
As 3D printing becomes more prevalent in medical device production, polishing robots are evolving to seamlessly integrate with these additive manufacturing processes. This synergy allows for:
-
Direct post-processing of 3D printed components
-
Customized polishing strategies for complex geometries
-
Reduced lead times from design to finished product
Expanded material capabilities
Future polishing robots will be equipped to handle an ever-widening range of materials used in medical devices, including:
-
Advanced ceramics
-
Biocompatible alloys
-
Composite materials
This expansion will enable the production of more sophisticated and effective medical devices, pushing the boundaries of what’s possible in patient care and treatment.
High-precision 3D polishing robots are revolutionizing the medical device manufacturing industry. These advanced machines offer unparalleled accuracy, consistency, and efficiency in producing intricate medical components. By combining cutting-edge robotics with sophisticated polishing techniques, manufacturers can achieve superior surface finishes and meet stringent quality standards.
As the medical device sector continues to evolve, embracing high-precision 3D polishing robots will be crucial for staying competitive. Companies that invest in this technology can expect improved product quality, reduced production costs, and enhanced capabilities to meet complex design requirements. The future of medical device manufacturing lies in the seamless integration of precision robotics, paving the way for innovative, life-saving devices that push the boundaries of what’s possible in healthcare.