Imagine a factory floor that is efficient and productive. Precision meets efficiency. Assembly line robots are responsible for this scene, which is not from an animated film. How are these mechanical wonders revolutionizing industry while keeping costs in check and quality at the highest level?
We’ll explore the world of assembly line robots to see how these technological marvels can cut costs without compromising quality. We’ll examine their cost-cutting benefits, discuss implementation challenges and examine how they can improve quality. Discover how robots on assembly lines are changing the manufacturing landscape, one precise movement at atime!
Cost-Cutting Benefits of Assembly Line Robots
A. Reduced labor expenses
Assembly line robots have revolutionized the manufacturing industry by significantly reducing labor expenses. This cost-cutting benefit is one of the primary reasons why companies are increasingly adopting robotic solutions in their production processes. Let’s delve into the various ways in which assembly line robots contribute to reducing labor costs:
-
Elimination of repetitive manual tasks
Assembly line robots excel at performing repetitive tasks with precision and consistency. By automating these routine operations, companies can reallocate human workers to more complex and value-added activities. This shift not only reduces the number of workers required for basic assembly tasks but also improves overall productivity. -
24/7 operation capability
Unlike human workers, robots don’t require breaks, holidays, or sick days. They can operate continuously, 24 hours a day, 7 days a week, without fatigue or loss of efficiency. This round-the-clock operation capability allows manufacturers to maximize production output without incurring additional labor costs for overtime or shift differentials. -
Reduced training and onboarding costs
Implementing assembly line robots can significantly reduce the expenses associated with training and onboarding new employees. Once programmed, robots can perform their designated tasks consistently without the need for ongoing training or skill development. This eliminates the costs associated with recruiting, hiring, and training new workers for repetitive assembly line positions. -
Decreased workplace injuries and associated costs
Assembly line work often involves repetitive motions and heavy lifting, which can lead to workplace injuries and associated costs such as workers’ compensation claims and lost productivity. By assigning these tasks to robots, companies can reduce the risk of workplace injuries, resulting in lower insurance premiums and fewer expenses related to employee health and safety. -
Improved workforce allocation
With robots handling routine tasks, human workers can be reassigned to more complex and strategic roles that require critical thinking, problem-solving, and creativity. This reallocation of human resources allows companies to make better use of their workforce’s skills and expertise, potentially leading to increased innovation and overall business growth.
Let’s take a look at a comparison of labor costs between human workers and assembly line robots:
Factor | Human Workers | Assembly Line Robots |
---|---|---|
Hourly wage | $15 – $30 | Initial investment, then minimal ongoing costs |
Benefits | Health insurance, retirement plans, etc. | None required |
Training | Ongoing costs for skill development | One-time programming, occasional updates |
Productivity | 8-hour shifts, with breaks | 24/7 operation capability |
Error rate | Variable, depends on fatigue and skill level | Consistent, minimal errors |
Scalability | Limited by available workforce | Easily scalable with additional units |
As we can see from this comparison, assembly line robots offer significant advantages in terms of labor cost reduction and operational efficiency.
B. Increased production speed and efficiency
Assembly line robots not only reduce labor expenses but also significantly boost production speed and efficiency. This increase in productivity is a crucial factor in cutting costs and improving overall manufacturing performance. Let’s explore the various ways in which robotic systems enhance production speed and efficiency:
-
Consistent high-speed operation
Assembly line robots can perform tasks at a consistently high speed, far surpassing the capabilities of human workers. This rapid and unwavering pace of operation leads to a substantial increase in production output. For example, a robotic arm can complete hundreds of precise movements per minute, maintaining this speed throughout its operational hours without fatigue or loss of accuracy. -
Parallel processing capabilities
Many robotic systems are designed to perform multiple tasks simultaneously, a feat that is challenging for human workers. This parallel processing capability allows for the completion of complex assembly processes in a fraction of the time it would take using traditional methods. For instance, a single robot might be able to pick, orient, and place multiple components at once, significantly reducing cycle times. -
Optimized workflow and reduced bottlenecks
By strategically implementing robots at key points in the assembly line, manufacturers can optimize their production workflow and minimize bottlenecks. Robots can be programmed to work in perfect synchronization with each other and with human workers, ensuring a smooth and efficient flow of materials and components through the production process. -
Precision and repeatability
Assembly line robots excel at performing tasks with exceptional precision and repeatability. This high level of accuracy reduces the need for quality checks and rework, which in turn increases overall production efficiency. The consistency of robotic operations also allows for better prediction and planning of production schedules, further enhancing efficiency. -
Rapid changeover and reprogramming
Modern assembly line robots are designed with flexibility in mind. They can be quickly reprogrammed or reconfigured to handle different products or variations in the production line. This rapid changeover capability allows manufacturers to adapt to changing market demands or introduce new product lines with minimal downtime, maintaining high efficiency across diverse production runs. -
Integration with IoT and data analytics
Assembly line robots can be integrated with Internet of Things (IoT) sensors and data analytics systems, enabling real-time monitoring and optimization of production processes. This integration allows for continuous improvement in efficiency through data-driven decision-making and predictive maintenance.
To illustrate the impact of assembly line robots on production speed and efficiency, let’s consider a hypothetical case study:
Metric | Before Robot Implementation | After Robot Implementation | Improvement |
---|---|---|---|
Units produced per hour | 100 | 250 | 150% increase |
Production uptime | 80% | 95% | 15% increase |
Defect rate | 5% | 1% | 80% reduction |
Cycle time per unit | 3 minutes | 1.2 minutes | 60% reduction |
Product changeover time | 2 hours | 30 minutes | 75% reduction |
This case study demonstrates the significant improvements in production speed and efficiency that can be achieved through the implementation of assembly line robots.
C. Minimized downtime and maintenance costs
One of the key advantages of assembly line robots is their ability to minimize downtime and reduce maintenance costs. This aspect of robotic systems contributes significantly to overall cost reduction in manufacturing processes. Let’s explore how assembly line robots help in minimizing downtime and maintenance expenses:
-
Predictive maintenance capabilities
Modern assembly line robots are equipped with advanced sensors and diagnostic systems that enable predictive maintenance. These systems continuously monitor the robot’s performance, component wear, and other critical parameters. By analyzing this data, manufacturers can predict when maintenance is needed before a breakdown occurs, significantly reducing unplanned downtime. -
Longer operational lifespan
Compared to traditional machinery, assembly line robots typically have a longer operational lifespan. They are designed to withstand continuous operation in industrial environments and are built with durable components. This extended lifespan means fewer replacements and upgrades, leading to reduced long-term maintenance costs. -
Reduced wear and tear
Robots perform tasks with consistent precision, which leads to reduced wear and tear on both the robotic components and the tools they use. This consistency results in less frequent need for repairs or replacements, further minimizing maintenance costs and potential downtime. -
Remote monitoring and diagnostics
Many modern robotic systems allow for remote monitoring and diagnostics. This capability enables technicians to identify and often resolve issues without physically being present on the factory floor. Remote troubleshooting can significantly reduce response times and minimize downtime during maintenance or repair operations. -
Modular design for easy repairs
Assembly line robots are often designed with modularity in mind. This means that individual components or modules can be quickly replaced if they fail, rather than requiring a complete system overhaul. This modular approach reduces the time and cost associated with repairs and maintenance. -
Consistent performance under harsh conditions
Unlike human workers, robots can operate consistently in harsh or hazardous environments without fatigue or health risks. This capability reduces the need for frequent breaks or shift changes, minimizing production interruptions and associated costs. -
Automated self-maintenance routines
Some advanced robotic systems are capable of performing basic self-maintenance routines, such as self-cleaning or automatic tool changes. These features help to maintain optimal performance and reduce the frequency of manual maintenance interventions.
To better understand the impact of assembly line robots on downtime and maintenance costs, let’s examine a comparative analysis:
Factor | Traditional Assembly Line | Robotic Assembly Line |
---|---|---|
Average downtime per month | 48 hours | 12 hours |
Maintenance frequency | Weekly | Monthly |
Annual maintenance cost | $100,000 | $40,000 |
Unexpected breakdowns per year | 15 | 3 |
Average repair time | 4 hours | 1 hour |
Lifespan of equipment | 5-7 years | 10-15 years |
Preventive maintenance efficiency | Manual inspections | Continuous monitoring with predictive analytics |
This comparison clearly illustrates the advantages of robotic assembly lines in terms of reduced downtime and maintenance costs.
D. Lower material waste
Assembly line robots play a crucial role in reducing material waste, which is another significant factor in cutting costs for manufacturing operations. By minimizing waste, companies can not only save on raw material expenses but also reduce their environmental impact. Let’s explore how assembly line robots contribute to lower material waste:
-
Precision in material handling
Robots excel at handling materials with extreme precision. They can measure, cut, and dispense materials with accuracy that far surpasses human capabilities. This precision ensures that only the exact amount of material needed is used for each product, significantly reducing overuse and waste. -
Consistent application of adhesives and sealants
In many manufacturing processes, adhesives and sealants are crucial components. Assembly line robots can apply these materials with consistent pressure and in precise amounts, eliminating excess application and reducing waste. This consistency not only saves material but also improves product quality and reduces the need for rework. -
Optimized cutting and shaping
Robotic systems can be programmed to optimize cutting patterns for materials like sheet metal, fabric, or plastics. By nesting parts efficiently and minimizing scrap, robots can significantly reduce material waste compared to manual cutting processes. -
Real-time quality control
Many assembly line robots are equipped with vision systems and sensors that can perform real-time quality control checks. By detecting defects early in the production process, these systems prevent the waste of additional materials and components that would otherwise be used to complete a defective product. -
Reduced human error
Human errors in assembly processes can lead to significant material waste. Robots, on the other hand, perform tasks with consistent accuracy, dramatically reducing errors that result in scrapped materials or products. -
Efficient handling of hazardous materials
For processes involving hazardous or difficult-to-handle materials, robots can be used to ensure precise and safe handling. This reduces the risk of spills or mishandling that could result in material waste and potential environmental hazards. -
Data-driven material usage optimization
Robotic systems integrated with data analytics can provide valuable insights into material usage patterns. This data can be used to further optimize production processes, refine material requirements, and identify areas where waste can be reduced. -
Improved inventory management
By providing accurate data on material usage, robotic systems enable more precise inventory management. This helps prevent overordering of raw materials and reduces the risk of materials expiring or becoming obsolete before use.
To illustrate the impact of assembly line robots on material waste reduction, let’s examine a comparative analysis:
Waste Reduction Factor | Traditional Assembly | Robotic Assembly |
---|---|---|
Material utilization rate | 85% | 97% |
Scrap rate | 8% | 2% |
Adhesive/sealant waste | 15% | 3% |
Defective products | 5% | 1% |
Raw material inventory accuracy | 90% | 99% |
Hazardous material spills per year | 10 | 1 |
This comparison clearly demonstrates the significant improvements in material waste reduction that can be achieved through the implementation of assembly line robots.
Now that we’ve explored the various cost-cutting benefits of assembly line robots, including reduced labor expenses, increased production speed and efficiency, minimized downtime and maintenance costs, and lower material waste, it’s clear that these technological advancements offer substantial advantages for manufacturers. However, it’s important to note that while robots can significantly reduce costs, their implementation must be carefully planned to ensure that quality is maintained or even improved. In the next section, we’ll delve into how manufacturers can maintain and enhance product quality while leveraging the cost-saving benefits of robotic assembly systems.
Maintaining Quality with Robotic Assembly
Precision and consistency in tasks
Assembly line robots have revolutionized manufacturing by offering unparalleled precision and consistency in tasks. Unlike human workers who may experience fatigue or distractions, robots can perform repetitive tasks with unwavering accuracy for extended periods. This level of consistency is crucial for maintaining high-quality standards in production.
One of the key advantages of assembly line robots is their ability to execute tasks with micrometer-level precision. This is particularly important in industries such as electronics, automotive, and aerospace, where even the slightest deviation can lead to significant quality issues. For example, in the production of smartphones, robots can place components with an accuracy of up to 0.02mm, ensuring that each device meets stringent quality requirements.
Moreover, the consistency provided by robots translates into reduced variability in the final product. This uniformity not only enhances the overall quality but also simplifies quality control processes, as there is less need for extensive sampling and testing.
Advanced quality control systems
The integration of advanced quality control systems with assembly line robots has further enhanced their ability to maintain high-quality standards. These systems use a combination of sensors, cameras, and artificial intelligence to detect defects and anomalies in real-time, ensuring that only products meeting specified criteria move forward in the production process.
Some of the key features of advanced quality control systems in robotic assembly lines include:
-
Machine vision systems
-
Non-destructive testing methods
-
In-line measurement and inspection
-
Automated error correction
Let’s explore these features in more detail:
Feature | Description | Benefits |
---|---|---|
Machine vision systems | High-resolution cameras and AI algorithms that inspect products for visual defects | Identifies issues invisible to the human eye, reduces manual inspection time |
Non-destructive testing | Methods like ultrasound or X-ray inspection that check internal components without damaging the product | Ensures structural integrity without sacrificing finished products |
In-line measurement | Automated systems that measure critical dimensions during assembly | Catches dimensional errors early in the process, reducing waste |
Automated error correction | Robots that can adjust their actions based on quality control feedback | Minimizes human intervention, speeds up error resolution |
These advanced quality control systems work in tandem with assembly line robots to create a robust quality assurance process. By detecting and addressing issues in real-time, manufacturers can significantly reduce the number of defective products that reach the end of the production line, ultimately saving costs and improving customer satisfaction.
Adaptability to different product specifications
One of the most significant advantages of assembly line robots is their adaptability to different product specifications. This flexibility allows manufacturers to maintain high-quality standards across a diverse range of products without the need for extensive retooling or retraining.
Modern assembly line robots can be quickly reprogrammed to handle various product specifications, enabling manufacturers to:
-
Rapidly switch between different product models
-
Accommodate customization requests
-
Implement design changes without significant downtime
-
Produce small batches of specialized products efficiently
This adaptability is particularly valuable in industries with frequent product updates or high levels of customization, such as the automotive sector. For instance, a single robotic assembly line can be programmed to assemble different car models with varying specifications, ensuring consistent quality across the entire product range.
The key to this adaptability lies in the robots’ modular design and sophisticated software. Manufacturers can easily update robot programs, swap out end-effectors (the “hands” of the robot), and adjust settings to meet new product requirements. This level of flexibility not only maintains quality across different product specifications but also contributes to cost savings by reducing the need for dedicated production lines for each product variant.
Real-time data analysis for continuous improvement
Assembly line robots equipped with sensors and connected to data analytics platforms provide a wealth of information that can be used for continuous quality improvement. This real-time data analysis capability allows manufacturers to:
-
Identify trends and patterns in production quality
-
Predict potential quality issues before they occur
-
Optimize production processes for better efficiency and quality
-
Make data-driven decisions for process improvements
The integration of real-time data analysis with robotic assembly lines creates a feedback loop that constantly refines and enhances the production process. For example, if data analysis reveals that a particular step in the assembly process is contributing to a higher rate of defects, manufacturers can quickly adjust the robot’s programming or the process parameters to address the issue.
Some key metrics that can be analyzed in real-time include:
-
Cycle times
-
Defect rates
-
Machine performance
-
Environmental conditions (temperature, humidity, etc.)
-
Material usage and waste
By continuously monitoring and analyzing these metrics, manufacturers can maintain and even improve quality over time. This data-driven approach to quality management ensures that assembly line robots not only maintain consistent quality but also contribute to ongoing process improvements.
Now that we have explored how assembly line robots maintain quality through precision, advanced quality control systems, adaptability, and real-time data analysis, let’s consider the practical aspects of implementing these robotic solutions in manufacturing environments.
Implementing Robotic Solutions
Assessing current assembly processes
Before implementing robotic solutions in your assembly line, it’s crucial to conduct a thorough assessment of your current processes. This evaluation will help you identify areas where robots can make the most significant impact, both in terms of cost reduction and quality improvement.
To begin, consider the following steps:
-
Map out your existing workflow
-
Identify bottlenecks and inefficiencies
-
Analyze production data
-
Evaluate quality control measures
-
Assess worker safety and ergonomics
Let’s dive deeper into each of these steps:
-
Mapping out your existing workflow: Create a detailed flowchart of your current assembly process, including all stages from raw material input to final product output. This visual representation will help you pinpoint areas where robots could potentially streamline operations.
-
Identifying bottlenecks and inefficiencies: Look for stages in your assembly line where production slows down or where errors are more likely to occur. These are prime candidates for robotic intervention.
-
Analyzing production data: Review historical data on production rates, cycle times, and output quality. This information will provide a baseline for comparison when evaluating the potential impact of robotic solutions.
-
Evaluating quality control measures: Assess your current quality control processes and identify areas where automation could enhance accuracy and consistency.
-
Assessing worker safety and ergonomics: Identify tasks that pose safety risks or require repetitive motions that could lead to worker fatigue or injury. These tasks are often ideal for robotic replacement.
By thoroughly assessing your current assembly processes, you’ll be better equipped to make informed decisions about where and how to implement robotic solutions.
Choosing the right robotic system
Once you’ve assessed your current processes, the next step is selecting the appropriate robotic system for your assembly line. This decision is critical, as the right choice can significantly impact your cost-cutting efforts and quality maintenance.
When choosing a robotic system, consider the following factors:
-
Task requirements
-
Payload capacity
-
Speed and precision
-
Flexibility and adaptability
-
Integration capabilities
-
Cost and return on investment (ROI)
Let’s examine these factors in more detail:
Task requirements
Different assembly tasks require different types of robots. For example:
Task Type | Recommended Robot Type |
---|---|
Pick and place | SCARA or Delta robots |
Welding | Articulated arm robots |
Painting | Cartesian robots |
Assembly | Collaborative robots (cobots) |
Choose a robot that specializes in the specific tasks you need to automate.
Payload capacity
Ensure the robot you select can handle the weight of the components it will be working with. Overloading a robot can lead to reduced accuracy and increased wear and tear.
Speed and precision
Consider the speed at which the robot needs to operate to meet your production goals. Additionally, evaluate the level of precision required for your assembly tasks. Some robots offer high speed but lower precision, while others prioritize accuracy over speed.
Flexibility and adaptability
If your production line handles multiple product variants or frequently changes, look for robots that can be easily reprogrammed or reconfigured. Collaborative robots (cobots) are often a good choice for flexible production environments.
Integration capabilities
Ensure the robotic system you choose can integrate seamlessly with your existing equipment and software systems. This integration is crucial for maintaining a smooth workflow and maximizing efficiency.
Cost and ROI
While the initial investment in robotic systems can be significant, it’s essential to consider the long-term return on investment. Calculate the potential cost savings from increased productivity, reduced errors, and lower labor costs to determine the most cost-effective solution for your assembly line.
Integration with existing infrastructure
Integrating robotic solutions into your existing assembly line infrastructure is a critical step in successfully implementing automation. This process requires careful planning and execution to ensure a smooth transition and minimal disruption to ongoing operations.
Consider the following aspects when integrating robots into your assembly line:
-
Physical layout: Assess your current factory layout and determine how robots will fit into the existing space. You may need to redesign parts of your assembly line to accommodate the new equipment.
-
Power and utilities: Ensure your facility has the necessary power supply and utilities to support the robotic systems. This may include upgrading electrical systems or installing compressed air lines.
-
Safety measures: Implement appropriate safety measures, such as safety fences, light curtains, or collaborative robot features, to protect human workers and comply with safety regulations.
-
Control systems: Integrate the robot’s control system with your existing production control systems. This may involve updating your manufacturing execution system (MES) or enterprise resource planning (ERP) software to communicate with the robotic controllers.
-
Data collection and analysis: Set up systems to collect and analyze data from the robotic systems. This information can be valuable for monitoring performance, identifying issues, and continuously improving your processes.
-
Material handling: Consider how materials will be fed to and from the robotic workstations. You may need to implement automated material handling systems, such as conveyors or automated guided vehicles (AGVs), to support the robots.
-
Quality control: Integrate automated inspection systems or vision systems to maintain quality control in your robotic assembly processes.
To ensure a successful integration, consider the following best practices:
-
Start with a pilot project: Begin by implementing robots in a small section of your assembly line to test their effectiveness and iron out any issues before scaling up.
-
Involve key stakeholders: Engage with operators, maintenance staff, and engineers throughout the integration process to gather valuable insights and address concerns.
-
Plan for downtime: Schedule the integration during planned downtime or slower production periods to minimize disruption to your operations.
-
Partner with experts: Work with experienced system integrators or robotics experts to ensure a smooth implementation and maximize the benefits of your robotic solutions.
Training and upskilling human workers
As you implement robotic solutions in your assembly line, it’s crucial to address the impact on your human workforce. While robots can take over many repetitive and physically demanding tasks, human workers remain essential for oversight, maintenance, and complex decision-making. Training and upskilling your workforce is key to ensuring a successful transition to a robot-assisted assembly line.
Consider the following strategies for training and upskilling your workers:
-
Assess skill gaps: Identify the new skills required to work alongside and manage robotic systems. This may include:
-
Robot programming and operation
-
Maintenance and troubleshooting
-
Data analysis and interpretation
-
Quality control in automated systems
-
-
Develop comprehensive training programs: Create training programs that cover both technical and soft skills. These programs should include:
-
Hands-on training with the specific robotic systems being implemented
-
Safety protocols for working around automated equipment
-
Problem-solving and critical thinking skills
-
Teamwork and communication in a robot-assisted environment
-
-
Offer continuous learning opportunities: Provide ongoing training and development opportunities to keep your workforce up-to-date with the latest advancements in robotics and automation.
-
Create new roles and career paths: As you automate certain tasks, create new roles that leverage human skills and expertise. For example:
-
Robot operators and programmers
-
Automation technicians
-
Process improvement specialists
-
Data analysts
-
-
Foster a culture of innovation: Encourage employees to contribute ideas for improving processes and leveraging robotic technology more effectively.
-
Address concerns and resistance: Be transparent about the changes and address any fears or concerns your workforce may have about job security or their changing roles.
To support these strategies, consider implementing the following:
-
Mentorship programs: Pair experienced employees with those new to working with robots to facilitate knowledge transfer and skill development.
-
Cross-training initiatives: Encourage employees to learn multiple skills to increase their versatility and value in the evolving work environment.
-
Partnerships with educational institutions: Collaborate with local colleges or technical schools to develop relevant training programs and create a pipeline of skilled workers.
By investing in training and upskilling your workforce, you can ensure a smooth transition to a robot-assisted assembly line while maintaining a skilled and engaged human workforce. This approach not only helps in successfully implementing robotic solutions but also positions your company for long-term success in an increasingly automated manufacturing landscape.
As we move forward, it’s important to recognize that the implementation of robotic solutions is an ongoing process. Continuous improvement and adaptation will be necessary to fully realize the benefits of automation while maintaining a competitive edge in the rapidly evolving manufacturing sector.
Future Trends in Assembly Line Robotics
AI and machine learning integration
As assembly line robots continue to evolve, the integration of artificial intelligence (AI) and machine learning (ML) is set to revolutionize the manufacturing industry. These advanced technologies are enhancing the capabilities of robots, making them more adaptive, efficient, and intelligent than ever before.
AI-powered robots can now make real-time decisions based on complex data analysis, allowing them to optimize their performance and adapt to changing production requirements. This level of autonomy reduces the need for constant human supervision and intervention, further cutting costs while maintaining high-quality standards.
Machine learning algorithms enable robots to:
-
Identify patterns and anomalies in production processes
-
Predict maintenance needs before breakdowns occur
-
Optimize production schedules based on historical data
-
Improve quality control through advanced visual inspection techniques
One of the most significant advantages of AI and ML integration is the ability for robots to learn and improve over time. As they gather more data and experience, these intelligent machines can refine their processes, leading to continuous improvements in efficiency and quality.
AI/ML Capability | Benefit to Assembly Line |
---|---|
Predictive maintenance | Reduced downtime and maintenance costs |
Adaptive process optimization | Increased productivity and efficiency |
Advanced quality control | Improved product quality and consistency |
Real-time decision making | Enhanced flexibility and responsiveness |
The integration of AI and ML in assembly line robots is not just a futuristic concept; it’s already being implemented in various industries. For example, automotive manufacturers are using AI-powered robots to perform complex welding tasks with greater precision and speed than ever before. These robots can adjust their welding parameters in real-time based on the specific characteristics of each component, ensuring consistent quality across the production line.
Collaborative robots (cobots)
Next, we’ll explore the rise of collaborative robots, or cobots, which are transforming the way humans and machines interact on the assembly line. Unlike traditional industrial robots that operate in isolated areas, cobots are designed to work alongside human workers safely and efficiently.
Cobots offer several advantages over traditional assembly line robots:
-
Enhanced safety features allow for close human-robot collaboration
-
Easier programming and setup, reducing implementation costs
-
Greater flexibility to adapt to different tasks and production needs
-
Improved ergonomics for human workers, reducing physical strain
These collaborative robots are particularly valuable for small and medium-sized enterprises (SMEs) that may not have the resources or space for large-scale robotic installations. Cobots can be easily integrated into existing production lines, providing a cost-effective solution for automating specific tasks without overhauling the entire assembly process.
One of the most exciting developments in cobot technology is the integration of advanced sensors and AI, enabling them to learn from their human counterparts. This allows for a more natural and intuitive collaboration between humans and robots, with each leveraging their unique strengths to optimize production processes.
Cobot Feature | Benefit |
---|---|
Force-sensing technology | Safe interaction with humans and delicate objects |
Easy programming interfaces | Reduced training time and costs |
Portable design | Flexibility to move between different workstations |
Vision systems | Enhanced accuracy in pick-and-place operations |
As cobot technology continues to advance, we can expect to see even greater integration of these collaborative machines in various industries. From electronics assembly to food packaging, cobots are proving to be versatile tools that can significantly enhance productivity without sacrificing the valuable skills and judgment of human workers.
IoT and smart factory concepts
The Internet of Things (IoT) is another game-changing technology that’s shaping the future of assembly line robotics. By connecting robots, sensors, and other devices to a centralized network, manufacturers can create “smart factories” that are more efficient, responsive, and data-driven than ever before.
In a smart factory, assembly line robots are no longer isolated machines but part of an interconnected ecosystem. This connectivity allows for:
-
Real-time monitoring of production processes
-
Seamless communication between different machines and systems
-
Centralized control and optimization of the entire production line
-
Data-driven decision making at all levels of the manufacturing process
The implementation of IoT in assembly line robotics enables manufacturers to achieve unprecedented levels of efficiency and flexibility. For instance, if a sudden change in customer demand requires a shift in production priorities, the entire assembly line can be reconfigured almost instantly through centralized controls.
Moreover, the vast amount of data collected through IoT devices can be analyzed to identify bottlenecks, optimize processes, and predict potential issues before they occur. This proactive approach to manufacturing can lead to significant cost savings and quality improvements.
IoT Application | Impact on Assembly Line |
---|---|
Real-time monitoring | Immediate detection and resolution of issues |
Predictive maintenance | Reduced downtime and maintenance costs |
Supply chain integration | Improved inventory management and logistics |
Energy consumption tracking | Enhanced sustainability and cost reduction |
As the concept of smart factories continues to evolve, we can expect to see even greater integration between assembly line robots and other smart devices. This could include everything from automated guided vehicles (AGVs) that deliver components to the assembly line, to smart packaging systems that adapt to different product specifications in real-time.
Sustainable and energy-efficient robotic solutions
With growing concerns about environmental impact and rising energy costs, the future of assembly line robotics is increasingly focused on sustainability and energy efficiency. Manufacturers are looking for ways to reduce their carbon footprint while maintaining productivity, and advanced robotic solutions are playing a crucial role in achieving these goals.
Several key trends are emerging in sustainable assembly line robotics:
-
Energy-efficient motors and actuators
-
Lightweight materials and designs to reduce power consumption
-
Regenerative braking systems that capture and reuse energy
-
Smart power management systems that optimize energy use across the production line
These energy-efficient robots not only help reduce operating costs but also contribute to a company’s sustainability goals, which are becoming increasingly important to consumers and stakeholders.
Sustainable Feature | Benefit |
---|---|
Energy-efficient motors | Reduced power consumption and operating costs |
Lightweight materials | Lower energy requirements for movement |
Regenerative braking | Energy recovery and reuse |
Smart power management | Optimized energy consumption across the assembly line |
In addition to energy efficiency, future assembly line robots are likely to incorporate more sustainable materials and manufacturing processes. This could include the use of recycled or biodegradable components, as well as the development of robots designed for easy disassembly and recycling at the end of their lifecycle.
Furthermore, the integration of renewable energy sources, such as solar or wind power, into robotic assembly lines is becoming more common. Some manufacturers are even exploring the possibility of energy-positive factories, where the production line generates more energy than it consumes.
As we look to the future, the trend towards sustainable and energy-efficient robotic solutions is likely to accelerate. This shift will not only benefit the environment but also help manufacturers reduce costs and improve their competitive edge in an increasingly sustainability-conscious market.
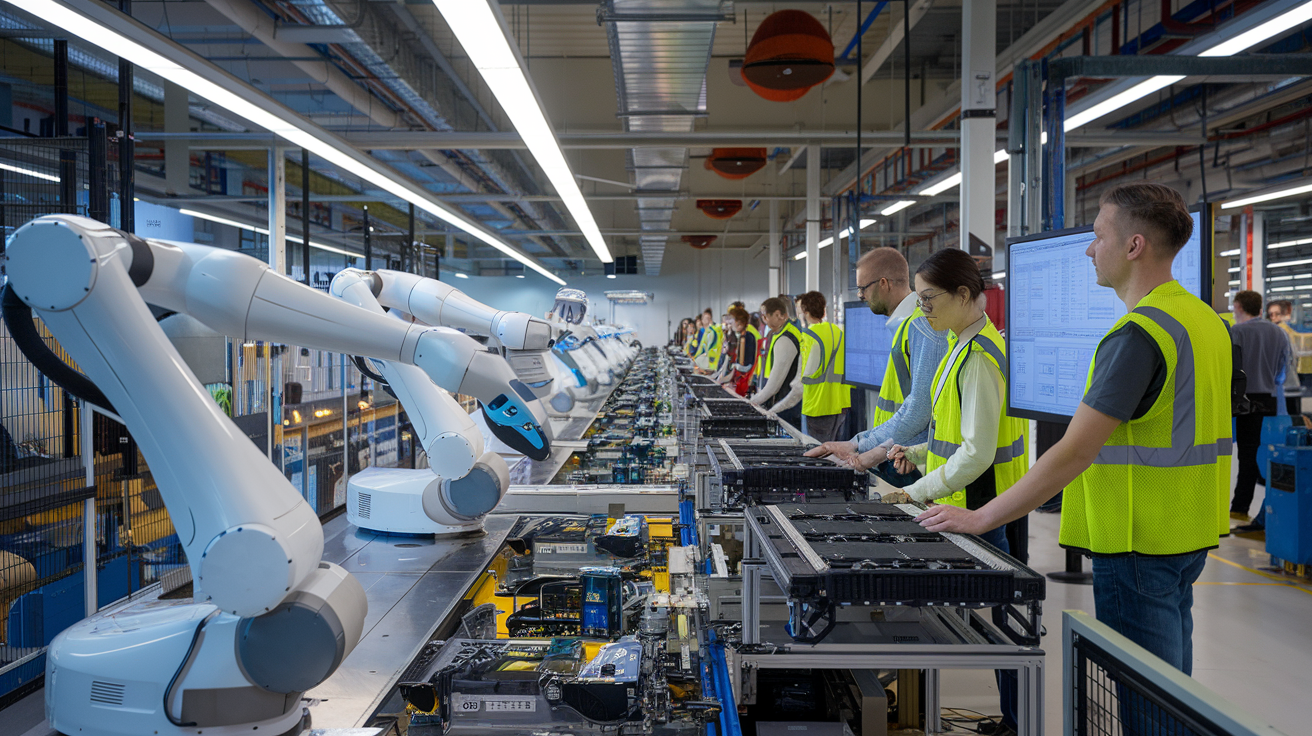
Robots on assembly lines have revolutionized the manufacturing industry, offering cost-saving benefits and maintaining high standards of quality. These automated systems are able to reduce labor costs and increase productivity while minimizing errors. This results in significant savings for companies. Robotic solutions allow companies to streamline assembly processes, improve consistency and respond quickly to changing demands.
The future of robotic assembly lines looks bright as technology advances. Robots will be more adaptable and efficient with the integration of machine learning and artificial intelligence. Businesses that adopt these innovations are well-positioned to remain competitive on the global market. They can balance cost-effectiveness and superior product quality. For companies to remain on the cutting edge of manufacturing, they should invest in robotic assembly solutions. They should also stay informed about the latest trends.