It is not uncommon for welding H-beams to be a difficult process. This can cause your operation to slow down and affect the quality. Common obstacles include misaligned beams and inconsistent welds. SevenAxis TrackWeld automates and improves precision in this process. The seventh external axis allows for precise torch positioning and stabilizes the placement. It also eliminates interference from surrounding equipment. This innovation improves not only weld quality, but also efficiency. The SevenAxis TrackWeld’s ability to handle large workpieces while saving floorspace allows you to achieve high-quality results consistently.
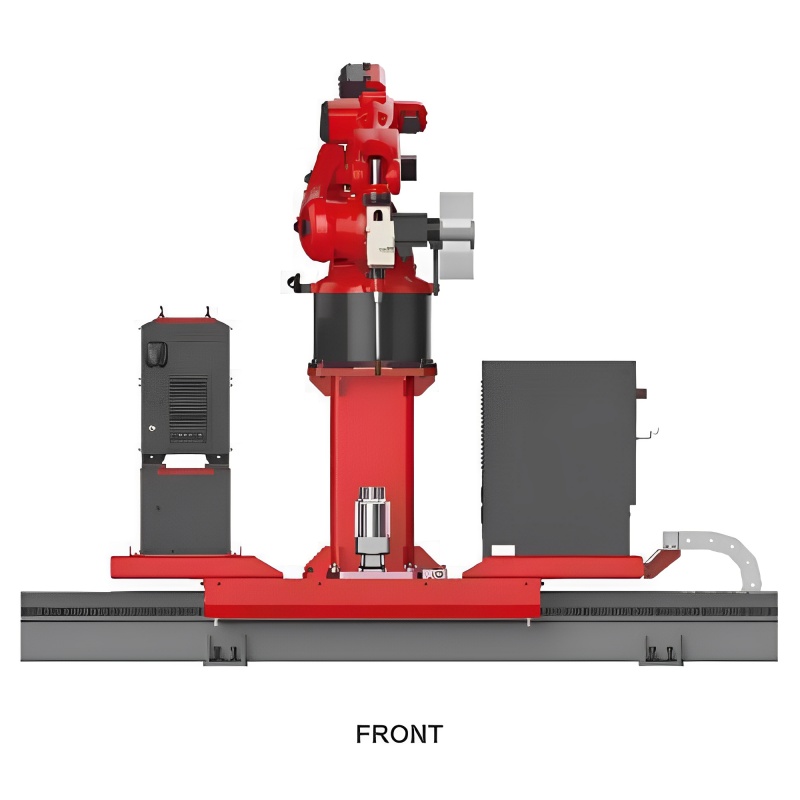
The Key Takeaways
- SevenAxis TrackWeld is designed to address common welding challenges such as misalignment, inconsistent welds and inconsistency. It ensures high precision and accuracy.
- The system’s advanced automated reduces inefficiency and allows for faster project completion, as well as lower labor costs.
- The SevenAxis trackWeld is easy to use and requires minimal training.
- Flexible and mobile, the system is suitable for a wide range of industrial applications from heavy machinery manufacture to construction.
- SevenAxis TrackWeld users have reported significant improvements. These include a reduction of 30% in production time, and an increase of 25% in weld strength.
- This technology allows businesses to achieve high-quality, consistent results. It gives them an edge in the industry.
H-Beams: Common welding challenges
The welding of H-beams presents its own challenges. These obstacles can affect your productivity and the quality of your work. Understanding these problems is the first step to overcoming them.
Alignment Problems
It is difficult to achieve the correct alignment when welding H-beams. Unaligned beams may lead to structural weakness and uneven welding. Manual adjustments are often required with traditional methods, increasing the risk of error. It can be difficult to maintain a consistent position, especially when you are working with large workpieces. Misalignment can affect the quality of the weld and also require additional time to correct.
Uneven Welding Quality
Another common problem is maintaining consistent weld-quality. Weak or uneven welds can be caused by variations in torch placement, heat application, or speed. These irregularities compromise the structural integrity. You may struggle to get the precise welds you need without advanced tools. The challenge is magnified when you are dealing with thicker or intricate materials.
Time Inefficiencies
Inefficient welding of H-beams is a common problem. Manual processes and repeated adjustment slow down your workflow. It may take you extra time to correct errors or fix poorly welded sections. Not only does this delay project timelines, but it also increases labor cost. Traditional methods are often inefficient and unable to handle projects with tight deadlines.
SevenAxis TrackWeld Solves These Challenges
Precision and Accuracy
Precision is essential for structural integrity. SevenAxis TrackWeld uses advanced alignment technology that helps you achieve the perfect position every time. The seven degrees of freedom in the SevenAxis TrackWeld allows you to position your workpieces accurately, even on large or complex pieces. This level of control reduces the chance of error during the welding process.
A high scan frame rate of 2000 frames/second ensures that each weld can be monitored in real time. You can rely on the SevenAxis TrackWeld for consistent welds with a precision =0.5mm. This accuracy increases the strength of the welds and reduces the need for rework.
Expert insight: “Seven axis robots have an additional axis and are therefore considered high-DOF robots (degree of flexibility) as they are configured in this way. Track system is the seventh axis and is best used for applications that require large work envelopes. ” – Welding expert
Efficiency and Speed
The time factor is crucial in any welding operation. SevenAxis TrackWeld optimizes workflow by coordinating the control between the robot track and the robot. This seamless integration enables faster welding cycles and allows you to finish projects quicker without compromising quality. Its ability to handle large workpieces enhances the system’s efficiency and makes it ideal for environments with high demand.
A handling robot can take efficiency to a new level. This robot streamlines your workflow by facilitating relay operations between welding tasks and handling tasks. SevenAxis TrackWeld automates these processes to reduce downtime and keep your operation running smoothly. Focus on meeting deadlines and improving your productivity.
Features that are User-Friendly
The SevenAxis TrackWeld is known for its ease of use. The intuitive controls allow even operators with little training to use it. Automation capabilities allow you to get professional results in a short time. The user-friendly interface allows you to maximize the system’s potential with minimal learning.
Flexible track lengths and mobility of the system make it ideal for industrial applications. SevenAxis TrackWeld can adapt to your specific needs, whether you are working on heavy machinery manufacturing or infrastructure development. The system’s mobility enables you to place it wherever is needed. This provides unparalleled convenience and flexibility.
Benefits and Applications in the Real World
SevenAxis TrackWeld Benefits Industries
SevenAxis TrackWeld is revolutionizing welding processes in several industries. Its advanced features are a great asset to sectors that require precision, efficiency and adaptability.
- Construction : This system is ideal for welding complex steel structures and bridges. It can also be used to weld high-rise building. The ability to weld large workpieces is a great asset for construction projects.
- Infrastructure The system excels at infrastructure projects such as railways, pipes, and power plants. It produces consistent welds, which are crucial for reliability and safety over the long term.
- Heavy Machinery Manufacturing In this industry, you will often be dealing with complex designs or heavy-duty materials. SevenAxis TrackWeld solves these problems by providing precise torch positioning and eliminating the requirement for additional positioners.
Did you know? Seven-axis robots can eliminate the need for torch positioners and stabilizers, while saving floor space. They are ideal for industries that require high-quality welding and efficient workflows.
Measurable improvements
SevenAxis TrackWeld delivers measurable results in your operations.
Case studies showing increased productivity and reduced costs
The system has been a major boost in productivity for companies. Automating welding and handling can help you complete projects quicker and save labor costs. One manufacturer, for example, reduced production time by 30 percent after integrating SevenAxis TrackWeld in their workflow. This efficiency directly translates into cost savings and allows you to allocate your resources more efficiently.
Weld Quality Improvements and Structural Integrity Examples
Precision of the system ensures consistent quality welds, even with intricate designs or heavy material. Welds can be produced with precision of =0.5mm to improve the structural integrity. One construction company noted a 25% increase in the strength of their welds, which reduced the risk for structural failure. These results show that the SevenAxis TrackWeld meets and exceeds industry standards.
Expert insight: “Seven axis robots allow for better torch placement, and they avoid interference from peripherals. This results in improved welds and the ability to work with larger pieces. ” – Robotics specialist
Adopting the SevenAxis TrackWeld will give you a competitive advantage in your field. The SevenAxis TrackWeld is an essential tool for modern applications due to its ability to deliver tangible advantages.