Mobile Intelligent Vision Welding&Cutting Robot will redefine industrial automation by 2025. This advanced robot delivers unmatched precision and efficiency by combining 3D visual recognition with AI-driven adaptiveness and dual operating modes. With its intelligent automation capabilities, you can easily overcome IT automation challenges such as labor shortages and inefficiencies.
The Mobile Intelligent Vision Welding&Cutting Robot has a unique mobile that allows it to be deployed in multiple locations and maximize resource utilization. Intelligent vision systems ensure precise alignment and high-quality welds, which reduces errors and rework. Businesses have seen productivity increase of up to 20 after adopting this cutting edge solution. This demonstrates its impact on digitalization.
The Mobile Intelligent Vision Welding&Cutting Robot, with its seamless design and energy-efficient implementation, addresses workforce concerns as well as integration issues. It also lowers operational costs. It allows you to overcome challenges in automation and achieve superior results for welding and cutting operations.
The Key Takeaways
- Mobile Smart Vision Robot is a robot that improves factory operations using AI and 3D vision. It makes the work faster and more accurate.
- Robots can do boring jobs, thereby solving the worker shortage. The workers can then focus on more important tasks, improving the overall quality of work.
- Data checks can instantly identify problems with work steps. These problems can be quickly fixed, which helps to optimize resources and production.
- Robots that move keep the work moving, ensuring quality and reducing interruptions. It saves money, and produces more products.
- modular design in robots allows them to be easily adapted and expanded. This allows businesses to respond quickly to new requirements.
Automating the Workforce: A Solution to Shortages of Labor
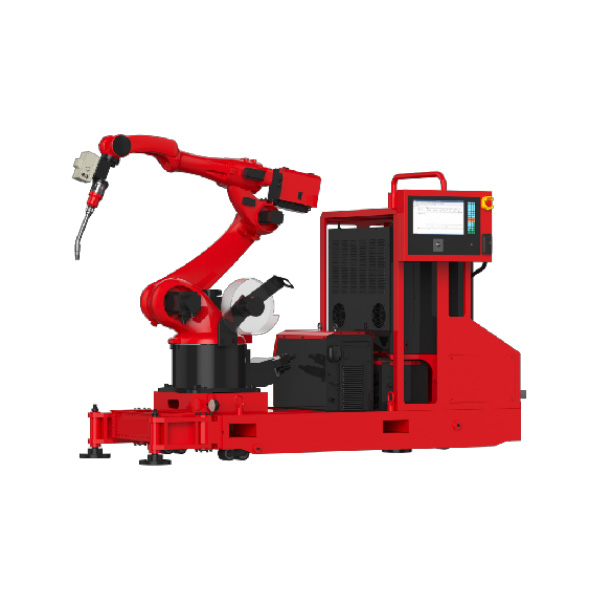
Automating repetitive and complex tasks
Automating repetitive and complex tasks is a key way to combat labor shortages. For example, robots in auto assembly plants can insert steering wheel millions of times with no errors. Robots in small-scale production use advanced algorithms for path planning to perform repetitive tasks without human intervention. This allows you to concentrate on more valuable activities, while automating processes requiring precision and consistency.
Robots in warehouses perform labor-intensive jobs, allowing workers to focus on more impactful tasks. Robots such as PuduBot can handle the delivery of food and goods, relieving staff. Automating these tasks can increase efficiency and relieve the burden on your staff. In 2021 American manufacturers ordered nearly 29,000 robots, a 37% rise from 2020. This trend shows the increasing reliance on intelligent automated solutions to solve workforce challenges.
AI Enhances Workforce Productivity
AI-powered intelligent automation increases productivity of the workforce by allowing workers to concentrate on strategic tasks. Mobile Intelligent Vision Robots use AI to automatically adjust parameters and identify seams. It reduces the risk of human error, and produces high-quality results. Automation removes physically-demanding tasks and allows workers to focus on areas such as quality control and safety.
IoT enabled smart factories boost productivity. Sensors and machines are used to collect data in real time, which allows a smaller team to manage large operations. 42 % of manufacturers are increasing automation. This approach can help overcome IT automation challenges and improve overall efficiency.
Supporting 24/7 operations through Mobility
Mobile robots, such as the Mobile Intelligent Vision Robot ensure continuous operations and round-the-clock production. These robots are able to operate continuously without becoming fatigued, ensuring quality and reducing the amount of downtime. This reduces labor costs while increasing production rates. During the COVID-19 epidemic, robots proved their worth by enabling staggered work shifts and maintaining safety protocol.
This omnidirectional mobility allows the robot to easily navigate in complex environments. The robot’s flexibility allows it to operate in difficult environments without interruption. By investing in IT staff training and upgrading their skills, you can reap the benefits of intelligent automaton and maintain your competitive edge.
Tackling Process Inefficiencies
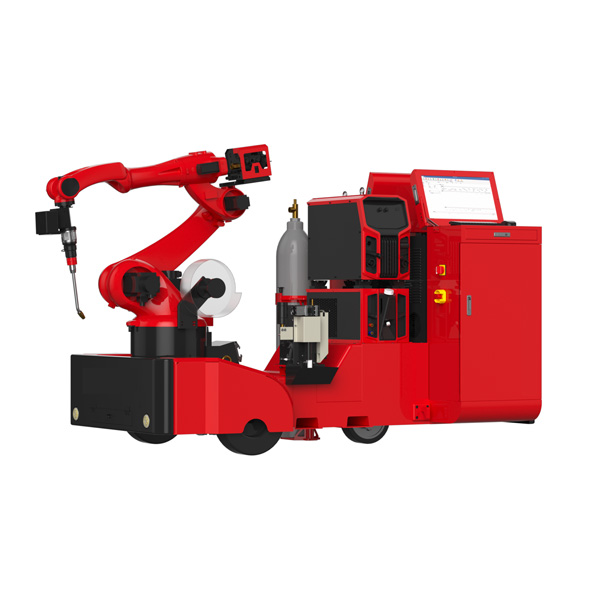
Real-time Data Analysis for Workflow Optimisation
Real time data analysis transforms the way you manage workflows, by identifying inefficiencies and solving them as they happen. You can gain a complete view of your operation by collecting data from machines, sensors, and production logs. This data is analyzed by machine learning models to identify potential bottlenecks. You can then address the issue before it disrupts production. Setting threshold values allows for continuous monitoring and optimization. Alerts inform you when workflows are disrupted, so that you can take swift action to maintain your productivity.
This approach improves not only operational efficiency, but also decision-making. You can reduce delays by optimizing your production processes. This will also improve the allocation of resources. By regularly refining your prediction models, you can ensure that your system adapts and runs smoothly.
Machine Vision: A Streamlining Tool for Complex Workflows
Machine Vision Technology simplifies complex workflows through automation of repetitive tasks, and by ensuring precision. In industrial settings, its ability to improve product quality and operational efficiency is indispensable. Machine vision systems, for example, inspect products with unmatched accuracy, reducing mistakes and ensuring compliance to regulatory standards. Automation speeds up production cycles, reducing the need for human intervention.
Contribution Type | Description |
---|---|
Enhance Product Quality | Machine vision systems offer unmatched accuracy and consistency for quality control processes. |
Improved operational efficiency | Automating repetitive tasks can streamline workflows and speed up production cycles. |
Cost Reduction | Reduces the amount of human labor required for repetitive tasks. This can lead to cost savings. |
Regulatory Compliance | Quality control measures ensure compliance with regulatory requirements. |
You can save a lot of money by integrating machine vision in your processes.
Reduce downtime and errors in operations
Automation can reduce downtime and operational mistakes by connecting the equipment via SCADA and PLCs and RTUs to improve monitoring. Predictive Maintenance, powered by IoT sensor and data analytics monitors equipment in real-time. This proactive approach allows you to identify potential failures and perform timely maintenance, thus avoiding unplanned downtime. This process is further enhanced by machine learning, which alerts you when maintenance needs to be performed.
Preventative Maintenance also plays an important role. Lubrication and cleaning tasks extend the life of machinery and reduce errors. Digitizing maintenance plans ensures that tasks are completed on time, minimising disruptions. These strategies result in a significant increase in the reliability of equipment and operational efficiency.
Intelligent automation can help you to reduce production downtime and improve the performance of your systems.
Addressing Automation Implementation Challenges
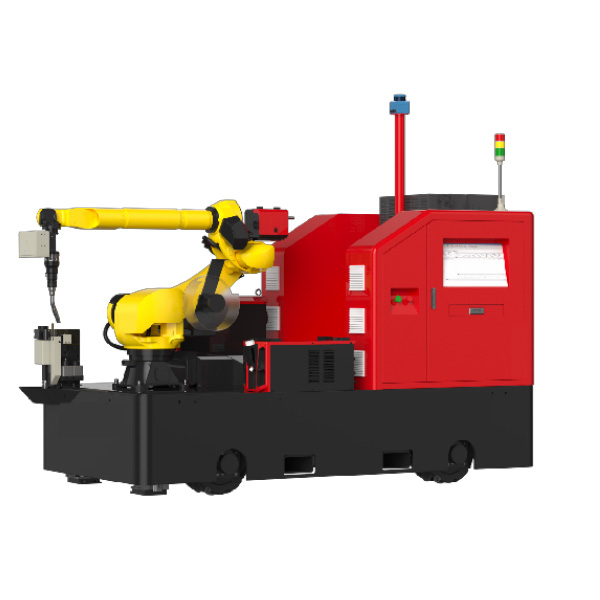
Integrate seamlessly with legacy systems
Integration of modern automation technology into legacy systems can present common challenges. You may face complexity in integration due to older systems being designed as stand-alone solutions. It can be difficult to integrate them into modern architectures. In addition, outdated security mechanisms within legacy systems may introduce vulnerabilities that put your operation at risk. Custom connectors are often resource-intensive and require specialized skills.
You can overcome these obstacles by adopting strategies such as modular automation solutions. These solutions let you integrate new technologies in small steps, reducing operational disruptions. By training your employees on the new systems, you can address issues such as resistance to change and skills gaps. Focusing on these strategies will help you ensure a smoother changeover and minimize any impact to your business.
AI-Driven Adaptability in Diverse Applications
AI-powered intelligent automation offers unparalleled adaptability for diverse applications . Mobile Intelligent Vision Robots, for instance, use AI to automatically adjust parameters and identify weld seams. It can be used in a variety of industries from metalworking to automotive without extensive reprogramming.
AI-driven systems are also capable of handling complex tasks such as real-time data analytics and predictive maintenance. These features allow you to optimize workflows while reducing downtime. Intelligent automation can help you overcome automation implementation issues while improving productivity and efficiency. This adaptability will ensure that your automation solution remains relevant as your business changes.
Minimizing Disruption During Deployment
If you don’t manage automation technology deployments carefully, they can cause disruptions to your business. Adopting strategies such as rolling implementation can help minimize disruptions. This method allows you to roll out updates to a smaller group of users. You can then monitor the performance and fix any issues before you do a large-scale rollout. Another effective strategy is blue-green deployment. This involves maintaining two identical environments to ensure seamless transitions, and minimal downtime when updating.
Canary deployments are also worth consideration. You can identify potential problems early by introducing updates to controlled groups of users. These strategies will help you to avoid challenges with automation after deployment and ensure that the implementation process is smooth. Planning carefully and implementing these best practices will help you achieve end-toend automation with minimum disruption.
Automating Scalability
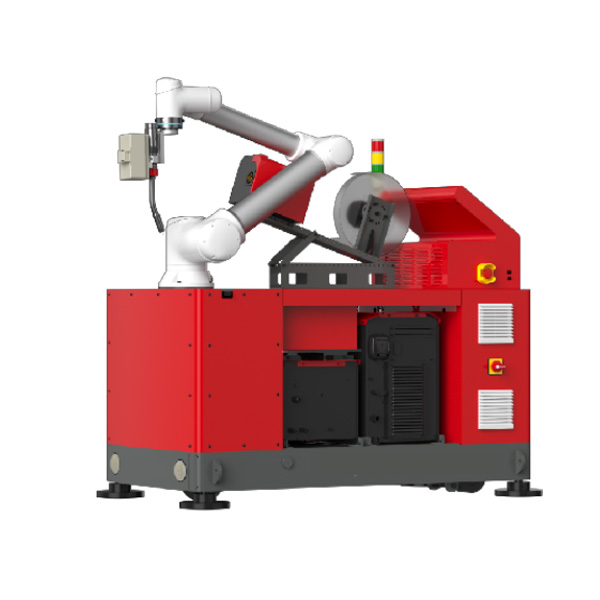
Modular Design for Flexible Installation
Modular Design simplifies management of automation at scale through the division of systems into smaller and independent modules. Each module is individually tested to ensure reliability and performance. This allows for rapid scaling of production and easy replication of processes. Modular systems encourage innovation because they allow upgrades and adaptions to new technologies, without having to overhaul the entire system.
Benefit | Description |
---|---|
Enhance Product Quality | Independent testing of each module improves performance and reliability. |
Scalability | Easy replication and rapid scaling up of products. |
Encouraging Innovation | Modular upgrades and rapid adaptation to new technology are encouraged. |
Modular design allows you to meet the increasing demand for automation while maintaining quality and efficiency. This strategy will ensure that your automation systems are future-ready and adaptable.
Mobile Support for Expanding Production Lines
The importance of mobility in scaling automation systems cannot be overstated. Mobile robots like the Mobile Intelligent Vision Robot adapt easily to changing production requirements. They can navigate in complex environments, and they can support expanding production lines. Flexibility allows you to meet changing demands without compromising your productivity.
Mobile robots reduce the need for fixed infrastructure and make it easier to reconfigure production layouts. This adaptability can be crucial for industries that face cost and efficiency issues. Mobility allows you to scale your operations and maintain a consistent output even in periods of rapid expansion.
Scaling solutions for growing businesses that are cost-effective
Automation scaling doesn’t need to be expensive. Automation of repetitive tasks can reduce labor costs and operational expenses . This creates cost efficiency. Employees are able to focus on more valuable tasks, which increases output and profitability. Automation reduces errors and ensures reliable processes, as well as faster service delivery.
- Automation of repetitive tasks reduces labor costs and increases profitability.
- Productivity Increased: Employees concentrate on strategic roles to boost productivity.
- Better Customer Service: Delivering services faster and more consistently meets customer expectations.
- Automated processes are more reliable and reduce errors.
Automating invoicing and reporting, as well as client interactions, streamlines business operations. These solutions can help you scale your business while reducing costs and improving efficiency. You can grow your business and stay competitive by investing in automation.
Ensure Data Automation Security and Overcome the Challenges
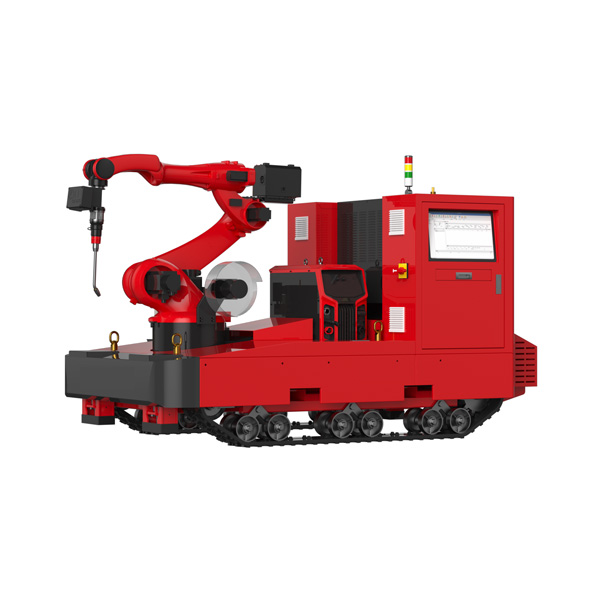
Cybersecurity features for safe operations
Cybersecurity is essential to protect industrial control systems against potential threats. Cyberattacks can cause expensive disruptions and safety hazards. Cybersecurity solutions are available to safeguard critical infrastructure. They include firewalls and intrusion detection systems as well as AI-driven tools for monitoring threats.
You can also adopt new technologies, such as remote monitoring and Industrial Internet of Things IIoT (IIoT), without having to expose your systems to unnecessary risk. Implementing these measures will ensure that your automation systems are resilient and future-ready. Adhering to cybersecurity standards, such as ISA/IEC 62443, helps you meet safety and security requirements.
Safe Data Handling and Storing Mechanisms
To prevent breaches and unauthorised access, it is important to take a proactive approach when handling sensitive industrial data. Implementing several key practices can help you improve data security.
- Train your employees to recognize and avoid data security threats.
- Data loss prevention solutions (DLP) can be used to monitor and stop unauthorized data transfers.
- Restriction of access to sensitive data through role-based user access controls.
- Data can be encrypted both in transit and at rest to render it unreadable by anyone without the correct decryption keys.
These mechanisms safeguard your data against internal and external threats. They also ensure the integrity of automation processes. You can maintain your trust in operations by prioritizing data security.
Standards and Regulations of Industry
Complying with industry standards will ensure that your automation system operates safely and efficiently. Regulatory bodies like OSHA, ISO IEC and ANSI established guidelines addressing electrical hazards, mechanical risks, operational risks and environmental impacts. These standards will protect your workers, and reduce the risk of fines.
Automation technologies, for example, must adhere to specific safety standards in order to avoid accidents and maintain smooth operations. You can demonstrate your commitment to safety and reliability by aligning all of your systems with the regulations. Compliance with these regulations not only safeguards your employees, but also enhances your industry reputation.
To address common IT automation issues, it is important to focus on compliance and security. You can effectively overcome these challenges by adopting advanced cybersecurity, secure data handling, and adhering industry standards.
The Mobile Intelligent Vision Welding and Cutting Robot transforms how you approach automation. Its flexibility and precision improve welding processes, while mobility ensures deployment across multiple locations. You can reduce errors, rework, and operational costs with its intelligent vision system and energy-efficient design. This robot empowers you to overcome automation challenges and achieve consistent, high-quality results. By adopting this technology, you position your business for success in 2025 and beyond. Stay competitive by embracing this innovative solution to revolutionize your industrial operations.
The FAQ
What industries can benefit most from the Mobile Intelligent Vision Welding and Cutting Robots?
This robot can be used in industries such as automotive and metalworking. The advanced features of this robot make it ideal for tasks that require precision and adaptability. It improves automation across multiple applications to ensure efficiency and scalability.
How can the robot increase accuracy in welding and cutting?
The robot automatically adjusts parameters using 3D Visual Recognition. It ensures high-quality and precise results. The machine vision system reduces errors and is a reliable automation solution in industrial settings.
Can the robot handle complex situations?
The robot’s omnidirectional movement allows it to adapt to different environments and navigate obstacles. It can be deployed in difficult environments without compromising its performance. The flexibility of the system allows for seamless automation in multiple locations.
Does the robot easily integrate with existing systems and equipment?
Modular design of the robot simplifies integration into legacy systems. It can be implemented incrementally to reduce disruptions. The AI-driven adaptability of the system ensures compatibility across diverse applications. This makes it a great choice for modernizing automated processes.