
The trackweld station redefines modern welding by offering a groundbreaking solution to tackle intricate tasks. You can rely on its advanced automation to achieve unmatched precision and efficiency. With its seventh external axis, the trackweld station expands the working area, enabling seamless operations even for complex projects. The integration of a handling robot ensures smooth coordination between welding and material handling, boosting productivity. This innovative solution empowers you to overcome challenges like maintaining quality and reducing errors, making it an indispensable tool for industrial applications.
Key Takeaways
- The SevenAxis TrackWeld Station enhances precision in welding with advanced automation, ensuring high-quality welds even in complex geometries.
- By integrating a handling robot, the station streamlines operations, reducing manual intervention and boosting overall productivity.
- Customizable track lengths and high-speed mobility allow the station to adapt to various project requirements, making it versatile for different industrial applications.
- Real-time monitoring and intelligent seam tracking minimize errors and ensure consistent quality across multiple welds, reducing the need for rework.
- The station’s ability to handle diverse welding techniques and materials makes it an essential tool for industries like aerospace, automotive, and construction.
- Comprehensive training and ongoing technical support ensure users can maximize the station’s potential while minimizing disruptions to their workflow.
- Implementing the SevenAxis TrackWeld Station can lead to significant cost savings by reducing waste and improving project completion times.
Common Welding Challenges
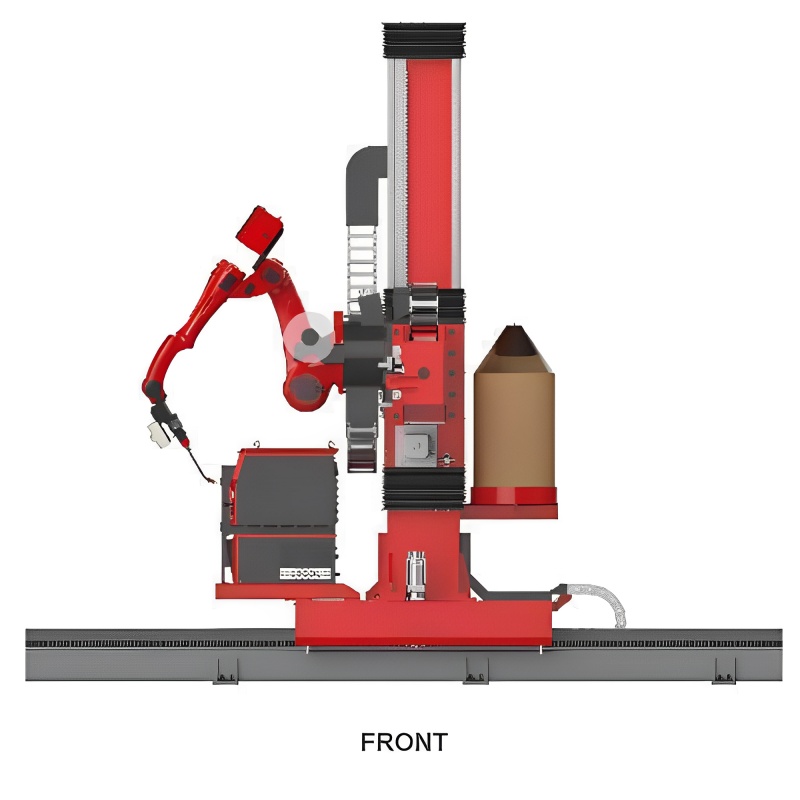
Welding is a critical process in many industries, but it comes with its own set of challenges. These challenges often affect the efficiency, precision, and overall quality of the welding process. Understanding these obstacles can help you appreciate how advanced solutions like the SevenAxis TrackWeld Station address them effectively.
Precision and Accuracy in Welding
Precision plays a vital role in achieving high-quality welds. Even minor deviations in alignment or positioning can lead to weak joints or structural failures. Traditional methods often struggle to maintain consistent accuracy, especially when dealing with complex geometries or varying material thicknesses.
Advanced robotic systems, such as the SevenAxis TrackWeld Station, excel in this area. They ensure precise control of the welding unit and automated seam tracking, even when components change or materials differ. This level of precision minimizes errors and ensures that every weld meets exact specifications.
For example, the station’s ability to handle different joining geometries with high precision ensures optimal execution of the seam, regardless of the complexity of the task.
Efficiency and Productivity in Industrial Applications
Industrial applications demand high productivity without compromising on quality. However, traditional welding methods often face bottlenecks due to manual intervention, slow processes, or frequent adjustments. These inefficiencies can lead to delays and increased costs.
Robotic systems like the SevenAxis TrackWeld Station streamline operations by automating repetitive tasks and optimizing workflows. The integration of a handling robot further enhances productivity by coordinating welding and material handling tasks seamlessly. This automation reduces downtime and allows you to complete projects faster while maintaining consistent results.
Quality Control and Error Reduction in Welding Processes
Maintaining consistent quality across multiple welds is a significant challenge. Factors such as welding consumable issues, variations in material properties, and human error can compromise the final product. Resistance welding, for instance, requires precise control of current and pressure to achieve reliable results.
The SevenAxis TrackWeld Station addresses these issues with advanced control systems and real-time adjustments. Its high-speed visual performance ensures accurate monitoring of the welding process, reducing the likelihood of errors. By automating quality checks and minimizing reliance on manual oversight, the station helps you achieve superior welding performance with fewer defects.
With features like automated seam tracking and precise measurement, the station eliminates common issues related to consumables and ensures consistent resistance during the welding process.
Features of the SevenAxis TrackWeld Station

Advanced Robotic Welding System with Seven Degrees of Freedom
The SevenAxis TrackWeld Station introduces a cutting-edge robotic welding system that offers seven degrees of freedom. This advanced design allows you to achieve unparalleled precision and flexibility during welding operations. The system ensures precise control over the welding unit, enabling it to adapt seamlessly to complex geometries and varying material thicknesses.
With its intelligent seam tracking capabilities, the station detects different joining geometries such as butt joints, fillet welds, and T-joints. This feature ensures that every weld meets exact specifications, reducing the risk of weak joints or structural failures. The high-speed visual performance of the system further enhances accuracy by monitoring the welding process in real time. You can rely on this robotic welding system to deliver consistent, high-quality results for even the most intricate tasks.
For example, the system’s ability to measure component positions contactlessly and adjust in real time ensures optimal execution of each weld, regardless of the complexity of the task.
Integration of a Handling Robot for Streamlined Operations
The integration of a handling robot into the SevenAxis TrackWeld Station revolutionizes your workflow. This feature enables seamless coordination between welding and material handling tasks, creating a streamlined workflow that boosts productivity. The handling robot works in tandem with the welding system, ensuring that materials are positioned accurately and efficiently for each weld.
This synchronized operation eliminates the need for manual intervention, reducing downtime and increasing overall efficiency. By automating repetitive tasks, the handling robot allows you to focus on more critical aspects of your projects. Whether you are working on large-scale industrial applications or smaller, intricate tasks, this integration ensures smooth and efficient operations.
The handling robot’s ability to relay operations between welding and material handling tasks makes it an indispensable tool for achieving a streamlined workflow in high-demand environments.
Customizable Track Lengths and High-Speed Mobility
The SevenAxis TrackWeld Station offers customizable track lengths, providing you with the flexibility to adapt the system to your specific needs. Track lengths range from 6 meters to 16 meters, allowing you to choose the configuration that best suits your workspace and project requirements. This adaptability ensures that the station can handle a wide variety of welding tasks, from small-scale projects to large industrial applications.
The station’s high-speed mobility further enhances its efficiency. With a track movement speed of 20 meters per minute or more, the system can quickly adjust to different workpiece situations. This rapid movement minimizes delays and ensures that your projects stay on schedule. The combination of customizable track lengths and high-speed mobility makes the SevenAxis TrackWeld Station a versatile and powerful solution for modern welding challenges.
For instance, the ability to set up working areas on both sides of the track maximizes productivity and ensures efficient use of space in your facility.
High-Precision Visual Performance and Real-Time Adjustments
The SevenAxis TrackWeld Station delivers exceptional visual performance, ensuring precise and efficient welding operations. Its advanced system measures the component position near the welding area without physical contact. This capability allows you to detect the joining position and gap with remarkable accuracy. By using this data, the station adjusts the welding unit in real time, ensuring flawless execution even in challenging scenarios.
The station’s intelligent seam tracking system identifies various joining geometries, such as butt joints, fillet welds, and T-joints. This feature ensures that every weld aligns perfectly with the required specifications. For example, the system can handle zero-gap situations or lap joints with ease, maintaining consistent quality across different tasks. You can rely on this technology to adapt seamlessly to complex geometries and varying material properties.
The WeldMaster 4.0 Track demonstrates similar capabilities by detecting gaps and joining positions with high precision. This ensures optimal control of the welding unit, resulting in superior weld quality.
Real-time data plays a crucial role in enhancing the station’s performance. The system continuously monitors the welding process, making instant adjustments to maintain accuracy. This dynamic approach minimizes errors and ensures consistent results, even in high-speed operations. For instance, the Yaskawa Robotic Welding System uses a laser vision system to track weld joints in real time, achieving precise and optimized welds. The SevenAxis TrackWeld Station incorporates similar cutting-edge technology, allowing you to achieve unparalleled precision.
The high-speed visual performance of the station also improves productivity. With a scanning frame rate of 2000 frames per second and a precision of ≤0.5mm, the system ensures that every detail is captured and addressed. This level of accuracy reduces the need for rework, saving you time and resources. Whether you are working on intricate designs or large-scale projects, the station’s visual capabilities guarantee exceptional results.
For example, the station’s ability to monitor and adjust in real time ensures that even turning parts on a coordinated positioner receive accurate welds. This feature enhances efficiency and reliability in demanding industrial applications.
By combining high-precision visual performance with real-time adjustments, the SevenAxis TrackWeld Station sets a new standard for modern welding systems. You can trust this innovative solution to deliver consistent, high-quality welds while optimizing your workflow.
How the TrackWeld Station Solves Welding Challenges
Enhancing Precision and Accuracy with Root Cause Analysis
Precision is essential in welding, especially when dealing with intricate designs or varying material properties. The SevenAxis TrackWeld Station enhances precision by incorporating root cause analysis into its operations. This approach identifies the underlying factors that could lead to misalignments or weak joints. By addressing these issues at their source, you can achieve consistent first-pass weld quality, reducing the need for rework or scrap parts.
The station’s advanced robotic system ensures precise control over the welding process. It uses weld data monitoring to track every detail in real time. This capability allows you to detect even the smallest deviations and make immediate adjustments. For example, the system can adapt seamlessly to different joining geometries, such as butt joints or fillet welds, ensuring flawless execution every time. Root cause analysis combined with weld data monitoring empowers you to troubleshoot problems effectively and maintain high-quality standards.
With this level of precision, you can minimize errors and eliminate the need for post-weld clean-up, saving both time and resources.
Boosting Efficiency Through Automation and Flexibility
Efficiency is a cornerstone of modern welding automation. The SevenAxis TrackWeld Station excels in this area by automating repetitive tasks and optimizing workflows. Its robotic handling system coordinates welding and material positioning, streamlining operations and reducing downtime. This level of automation allows you to focus on more critical aspects of your projects, boosting overall productivity.
The station’s flexibility further enhances its efficiency. Customizable track lengths and high-speed mobility enable you to adapt the system to various workpiece sizes and configurations. Whether you are working on large-scale industrial applications or smaller, intricate tasks, the station ensures smooth and efficient operations. Production monitoring systems integrated into the station provide real-time insights, helping you make data-driven decisions to optimize performance.
For instance, the station’s ability to handle both resistance welding and other techniques with equal efficiency makes it a versatile solution for diverse industrial needs.
By automating processes and offering unparalleled flexibility, the SevenAxis TrackWeld Station helps you complete projects faster without compromising on quality. This combination of automation and adaptability sets a new standard for welding systems.
Ensuring Consistent Quality with Advanced Control Systems
Maintaining consistent quality across multiple welds is a challenge in any industrial setting. The SevenAxis TrackWeld Station addresses this issue with its advanced control systems. These systems use weld data monitoring to oversee every aspect of the welding process, ensuring that each weld meets exact specifications. This level of oversight minimizes the risk of defects and enhances first-pass weld quality.
The station’s real-time monitoring capabilities play a crucial role in ensuring consistent results. By continuously tracking the welding process, the system can identify and correct issues as they arise. For example, it can detect variations in material properties or changes in component positioning and adjust the welding parameters accordingly. This proactive approach eliminates the need for extensive troubleshooting and reduces the likelihood of errors.
With features like automated seam tracking and precise measurement, the station ensures that every weld aligns perfectly with the required standards.
The integration of production monitoring systems further enhances quality control. These systems provide detailed reports on welding performance, allowing you to identify trends and make informed adjustments. By leveraging this data, you can improve efficiency and maintain high-quality standards across all your projects.
The station’s ability to minimize spatter and eliminate the need for anti-spatter compounds further underscores its commitment to delivering superior weld quality.
By combining advanced control systems with real-time monitoring and data-driven insights, the SevenAxis TrackWeld Station ensures that you achieve consistent, high-quality results in every application.
Real-World Applications: Aerospace, Automotive, and Construction
The SevenAxis TrackWeld Station demonstrates its versatility across industries that demand precision and efficiency. Its advanced features make it an essential tool for tackling complex welding tasks in aerospace, automotive, and construction sectors.
Aerospace Industry
In aerospace, precision is non-negotiable. Every weld must meet stringent quality standards to ensure the safety and reliability of aircraft components. The SevenAxis TrackWeld Station excels in this environment by delivering consistent, high-quality welds. Its ability to handle intricate geometries and varying material thicknesses ensures that even the most complex parts are welded with accuracy.
For example, the station’s real-time monitoring and automated seam tracking eliminate errors, reducing the need for rework or scrap parts. This capability is crucial in aerospace, where material waste and production delays can be costly.
The station’s high-speed mobility and customizable track lengths also enhance productivity. You can efficiently weld large components, such as fuselage sections or wing assemblies, without compromising on quality. By automating repetitive tasks, the station allows you to focus on innovation and design, driving advancements in aerospace technology.
Automotive Industry
Mass production in the automotive industry relies heavily on precision and speed. The SevenAxis TrackWeld Station meets these demands by streamlining welding processes and ensuring consistent results. Its robotic system excels at repetitive tasks, making it ideal for assembling car frames, exhaust systems, and other critical components.
The station’s ability to minimize or eliminate spatter reduces the need for post-weld clean-up, saving time and resources. This feature enhances efficiency, allowing you to meet tight production schedules without sacrificing quality.
The integration of a handling robot further boosts productivity. By coordinating welding and material handling tasks, the station reduces downtime and optimizes workflows. Whether you are producing electric vehicles or traditional models, this advanced system ensures that every weld meets exact specifications, enhancing the durability and safety of your products.
Construction Industry
In construction, welding plays a vital role in creating strong and reliable structures. The SevenAxis TrackWeld Station adapts seamlessly to the diverse needs of this industry. Its ability to handle large workpieces, such as steel beams and girders, makes it an invaluable asset for building bridges, skyscrapers, and other infrastructure projects.
The station’s high-precision visual performance ensures flawless execution, even in challenging conditions. By detecting gaps and joining positions with remarkable accuracy, it guarantees that every weld contributes to the structural integrity of your projects.
The station’s flexibility also shines in construction applications. Customizable track lengths and high-speed mobility allow you to adapt the system to various project requirements. Whether you are working in a controlled environment or on-site, the station delivers consistent, high-quality results that meet industry standards.
By addressing the unique challenges of aerospace, automotive, and construction industries, the SevenAxis TrackWeld Station proves its value as a versatile and powerful solution. Its advanced technology empowers you to achieve superior results while optimizing efficiency and reducing costs.
Benefits for Users of the TrackWeld Station
Cost Savings Through Reduced Waste and Rework
The SevenAxis TrackWeld Station helps you achieve significant cost savings by minimizing waste and rework. Its advanced robotic system ensures precise control over every weld, reducing the likelihood of errors that lead to material waste. By addressing the root causes of welding challenges, such as misalignments or inconsistent seam quality, the station eliminates the need for costly corrections.
The integration of weld data monitoring further enhances cost efficiency. This system gathers valuable data at the source, creating a virtual paper trail for each weld. You can use this information to identify and resolve quality issues before they escalate, saving both time and resources. For example, the station’s ability to detect joining positions and gaps with high precision ensures that every weld meets exact specifications, reducing the need for post-weld clean-up or adjustments.
By automating processes and maintaining consistent quality, the station provides a cost-effective solution for industries seeking to optimize their welding operations.
Improved Productivity with Faster Project Completion
The SevenAxis TrackWeld Station revolutionizes your workflow by boosting productivity and enabling faster project completion. Its robotic handling system automates repetitive tasks, allowing you to focus on more critical aspects of your projects. This level of automation reduces downtime and ensures that operations run smoothly from start to finish.
Customizable track lengths and high-speed mobility further enhance the station’s efficiency. With track movement speeds of 20 meters per minute or more, the system adapts quickly to different workpiece situations. Whether you are working on large-scale industrial applications or intricate designs, the station ensures that your projects stay on schedule.
For instance, the station’s ability to handle resistance welding with equal efficiency across various techniques allows you to complete tasks faster without compromising on quality.
Production monitoring systems integrated into the station provide real-time insights into performance. These systems help you make data-driven decisions to optimize workflows and improve overall efficiency. By combining automation with intelligent monitoring, the station sets a new standard for productivity in modern welding systems.
Enhanced Reliability and Reduced Error Rates
Reliability is a cornerstone of the SevenAxis TrackWeld Station. Its advanced robotic technology ensures consistent performance, reducing error rates and enhancing the dependability of your operations. The station’s intelligent seam tracking system detects different joining geometries, such as butt joints, fillet welds, and T-joints, ensuring flawless execution every time.
Real-time monitoring plays a crucial role in maintaining reliability. The station continuously tracks the welding process, making instant adjustments to address any deviations. This proactive approach minimizes errors and ensures that every weld aligns perfectly with the required standards. For example, the system’s ability to detect gaps and joining positions with remarkable accuracy guarantees consistent results, even in high-speed operations.
The station’s commitment to precision and quality makes it an indispensable tool for industries requiring reliable and efficient welding solutions.
By reducing error rates and enhancing reliability, the SevenAxis TrackWeld Station empowers you to achieve superior results while maintaining high-quality standards. Its innovative features and user-centric design make it a valuable asset for tackling complex welding tasks with confidence.
Versatility Across Various Welding Techniques and Materials
The SevenAxis TrackWeld Station stands out for its ability to adapt to a wide range of welding techniques and materials. This versatility makes it an essential tool for industries that require precision and efficiency in diverse applications. Whether you are working with intricate designs or large-scale projects, this station ensures consistent, high-quality results.
Adapting to Various Welding Techniques
The station’s advanced robotic system supports multiple welding techniques, including resistance welding, arc welding, and laser welding. Each technique benefits from the station’s intelligent seam tracking and real-time adjustments. For example, the system detects joining geometries like butt joints, fillet welds, and T-joints with remarkable accuracy. This capability ensures that every weld aligns perfectly with the required specifications.
The WeldMaster 4.0 Track demonstrates similar precision by detecting gaps and joining positions contactlessly. This feature guarantees optimal control of the welding unit, resulting in superior weld quality.
The station’s flexibility extends to handling zero-gap situations and lap joints. Its ability to adapt seamlessly to different welding methods allows you to tackle complex tasks with confidence. By automating these processes, the station reduces the need for manual intervention, saving you time and resources.
Handling Diverse Materials with Ease
Modern industries often require welding across various materials, such as steel, aluminum, and titanium. The SevenAxis TrackWeld Station excels in this area by offering precise control over the welding process, regardless of the material type. Its robotic system adjusts parameters in real time to accommodate differences in material properties, ensuring consistent results.
For instance, the station’s weld data monitoring system gathers valuable information at the source. This data helps you identify and resolve quality issues specific to each material. By leveraging this information, you can achieve reliable welds across a wide range of applications.
Weld data monitoring simplifies operations by creating a virtual paper trail for each weld. This feature helps you maintain high-quality standards while controlling costs.
Enhancing Efficiency Through Automation
The station’s robotic capabilities streamline operations by automating repetitive tasks. This automation not only boosts productivity but also ensures that every weld meets exact specifications. The integration of high-speed visual performance further enhances efficiency. With a scanning frame rate of 2000 frames per second, the system captures every detail, reducing the likelihood of errors.
Customizable track lengths and high-speed mobility add another layer of adaptability. These features allow you to configure the station to suit your specific needs, whether you are working on small components or large structures. By combining automation with flexibility, the station sets a new standard for modern welding systems.
Meeting Industry Demands with Versatility
The SevenAxis TrackWeld Station’s ability to handle various welding techniques and materials makes it a valuable asset across industries. Its advanced robotic technology empowers you to achieve superior results while optimizing efficiency. Whether you are in aerospace, automotive, or construction, this station adapts to your unique requirements, delivering consistent, high-quality welds every time.
By addressing the root causes of welding challenges, such as precision and quality control, the station ensures that you meet industry demands with confidence.
Implementation and Ease of Use
Seamless Integration into Existing Workflows
The SevenAxis TrackWeld Station is designed to fit effortlessly into your existing workflow. Its advanced technology ensures compatibility with a wide range of industrial setups, allowing you to maintain operational continuity. Whether you are upgrading from traditional welding systems or incorporating the station into a fully automated production line, the transition is smooth and efficient.
The station’s modular design simplifies the process of recommending and implementing the solution. You can customize its features to align with your specific needs, ensuring that it complements your current processes. For example, its customizable track lengths and high-speed mobility allow you to adapt the system to your workspace without disrupting ongoing operations. This adaptability minimizes the need for extensive reconfiguration, saving you time and resources.
A professional welder once shared how seamlessly the Track-Weld system integrated into their railroad project, enabling them to weld tracks efficiently without compromising the workflow. The result was a sturdy track capable of carrying heavy cargo trains.
By integrating the SevenAxis TrackWeld Station into your workflow, you can enhance productivity while maintaining consistency in your operations. Its ability to streamline tasks ensures that your team can focus on achieving superior results without unnecessary interruptions.
Comprehensive Training and Ongoing Technical Support
To ensure you get the most out of the SevenAxis TrackWeld Station, comprehensive training programs are available. These programs are tailored to your team’s skill level, providing hands-on experience with the station’s features and capabilities. From basic operations to advanced troubleshooting, the training equips your team with the knowledge needed to operate the system confidently.
Ongoing technical support further enhances your experience. A dedicated support team is always ready to assist you with maintenance, upgrades, or any challenges you may encounter. This proactive approach ensures that your station remains in optimal condition, reducing the likelihood of unexpected issues. For instance, if you need assistance with maintenance or optimizing the station for a specific task, the support team provides timely and effective solutions.
Track-Weld experts have demonstrated how their specialized knowledge and support extend the lifetime of critical components, such as railroad gauge corners, by rebuilding them to their original profile. This expertise ensures long-term reliability and cost savings.
With access to training and technical support, you can maximize the station’s potential while minimizing disruptions to your workflow. This combination of education and assistance empowers you to achieve consistent, high-quality results.
Minimal Downtime During Installation and Setup
The installation process for the SevenAxis TrackWeld Station is designed to minimize downtime. Its modular components and user-friendly design enable quick assembly, allowing you to resume operations as soon as possible. The station’s compatibility with various industrial environments further streamlines the setup process, ensuring that it integrates seamlessly into your facility.
During installation, a team of experts works closely with you to ensure that the station is configured correctly. This collaborative approach reduces the risk of errors and ensures that the system operates at peak efficiency from day one. For example, the station’s ability to handle diverse welding tasks without extensive adjustments allows you to start using it immediately after setup.
In collaboration with rail OEM manufacturers, Track-Weld has proven that efficient installation and maintenance practices can significantly reduce total cost of ownership while extending the lifetime of critical components.
By minimizing downtime during installation, the SevenAxis TrackWeld Station helps you maintain productivity and meet project deadlines. Its efficient setup process ensures that you can start benefiting from its advanced features without unnecessary delays.