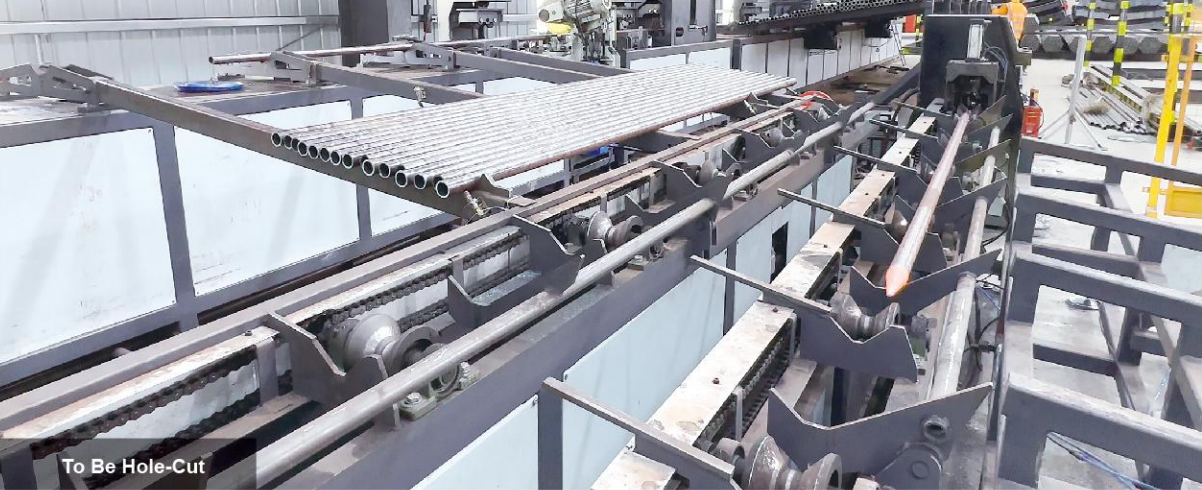
Choosing the right robotic welding system is crucial for the success of your steel structure projects. These systems have transformed the industry by delivering unmatched efficiency, precision, and productivity. For example, robotic welding systems operate continuously without fatigue, enabling faster production cycles and reducing lead times. They also achieve consistent weld quality, minimizing defects and ensuring structural integrity. With the robotic welding market projected to grow at a CAGR of over 10% from 2023 to 2032, adopting advanced steel structure robotic welding solutions has become more important than ever. A strategic selection process ensures you meet your project goals effectively.
Key Takeaways
- Think about what kind of welding you need. Look at the steel types and thicknesses you use. This helps you pick the best welding method.
- Check how big your project is. Big jobs need automated machines. Smaller, custom jobs might work better with flexible robots.
- Decide how precise and high-quality your welds should be. Robotic welders make steady welds that meet industry rules and keep your projects strong.
- Look at the features of robotic welders. Things like smart sensors and easy-to-use software make them more accurate and simple to use.
- Compare the price of new and used machines. New ones have the latest tech, but used ones can save money and still work well.
Identify Your Welding Needs
Material and Welding Process Requirements
Steel types and thickness considerations
Understanding the steel types and thicknesses you work with is essential. Different grades of steel require specific welding techniques to ensure structural integrity. For instance, high-strength steel may need preheating or post-welding treatments to prevent cracking. Thicker materials often demand processes like Stick Welding (SMAW), which is versatile and effective for structural steel construction. On the other hand, thinner materials benefit from MIG Welding (GMAW), known for its efficiency and suitability for long welds. Proper joint design and pre-welding preparation, such as cleaning and edge preparation, also play a critical role in achieving quality welds.
Choosing the right welding process (e.g., MIG, TIG, or spot welding)
Selecting the appropriate welding process depends on your project’s requirements. MIG Welding offers speed and is ideal for high-production environments like construction. TIG Welding (GTAW), while slower, delivers superior weld quality, making it suitable for precision-focused applications such as aerospace or artistic projects. Flux-Cored Arc Welding (FCAW) is another option, preferred for large-scale projects like bridges due to its high deposition rate. Evaluate the balance between efficiency and quality to choose the best system for your application.
Project Scale and Production Volume
High-volume production vs. custom fabrication
Your project scale significantly influences the type of robotic welding equipment you need. High-volume production benefits from automated systems designed for repetitive tasks, ensuring consistent weld quality and faster output. Custom fabrication, however, may require more flexible solutions like collaborative robots (cobots) that adapt to varying designs and smaller production runs.
Automation needs for repetitive tasks
Repetitive tasks in welding automation demand precision and efficiency. Robotic welding systems excel in maintaining consistent welds across identical components. For example, steel structure robotic welding solutions equipped with advanced sensors can handle complex geometries and heavy-duty applications. This reduces human error and increases productivity, especially in industries like automotive and construction.
Desired Outcomes and Quality Standards
Precision and quality expectations
Robotic welding systems are renowned for their precision. They follow programmed paths with exceptional accuracy, ensuring consistent welds that meet industry standards. Features like adaptive fill technology and optical part recognition further enhance quality by managing varying weld gaps and eliminating the need for manual adjustments. These capabilities make robotic welding equipment indispensable for projects requiring high-quality results.
Speed and efficiency goals
Achieving speed without compromising quality is crucial in welding processes. MIG Welding, for instance, offers fast production rates, making it ideal for large-scale projects. Robotic systems equipped with real-time monitoring ensure welding parameters stay within specified ranges, reducing defects and downtime. By automating repetitive tasks, you can meet tight deadlines while maintaining efficiency.
Evaluate Features of Robotic Welding Equipment
Precision and Accuracy
Importance of repeatability in welding
Repeatability is a cornerstone of robotic welding processes. It ensures that every weld meets the same quality standards, regardless of production volume. This consistency reduces defects and enhances the structural integrity of your steel projects. For example, seam-tracking sensors with an accuracy of +/- 0.1mm allow welding robots to adapt to variations in workpieces. This adaptability ensures precise weld placement and minimizes errors, even in complex geometries.
Advanced sensors and vision systems (e.g., EVS Robotics’ Mobile Intelligent Vision Robot)
Advanced sensors and vision systems elevate the performance of robotic welding equipment. These technologies monitor parameters like temperature, position, and alignment in real time. Automated sensing technologies also enable welding robots to adjust operations based on workpiece dimensions. For instance, EVS Robotics’ Mobile Intelligent Vision Robot uses 3D visual recognition to scan and extract weld seam information autonomously. This feature eliminates the need for complex programming, saving time and improving accuracy. Machine vision systems further enhance precision by providing visual feedback, ensuring each weld aligns perfectly with the design.
Workcell Design and Flexibility
Modular vs. fixed workcell setups
The choice between modular and fixed workcell setups depends on your production needs. Modular workcells offer flexibility, allowing you to reconfigure them for different tasks. They are ideal for facilities handling diverse projects. Fixed workcells, on the other hand, provide stability and are better suited for high-volume production. For example, the ArcWorld C-52 is a compact workcell designed for low- to medium-volume fabrication, while the ArcWorld 1200 features a dual-robot configuration for increased productivity.
Space considerations in your facility
Space constraints play a critical role in selecting the right workcell. Compact workcells like the ArcWorld C-52 require minimal floorspace, making them suitable for smaller workshops. Larger setups, such as the ArcWorld 1200, demand more room but deliver higher productivity. Evaluate your facility’s layout to ensure the chosen workcell integrates seamlessly without disrupting other operations.
Software and Programming
User-friendly interfaces and ease of programming
User-friendly software simplifies the operation of robotic welding systems. Intuitive interfaces guide you through the programming process, making it accessible even for operators without prior robotics experience. Many systems allow operators to learn and transition between tasks in under an hour. This ease of use reduces training time and minimizes disruptions to your workflow.
Integration with existing systems
Modern robotic welding equipment integrates seamlessly with existing production systems. Features like real-time data acquisition validate joint strength and weld penetration during operations. This integration ensures welding robots work efficiently alongside upstream and downstream processes, enhancing overall productivity. For instance, EVS Robotics’ Mobile Intelligent Vision Robot adapts to various tasks, making it a versatile addition to your production line.
Consider Cost and Maintenance of Robotic Welding Systems
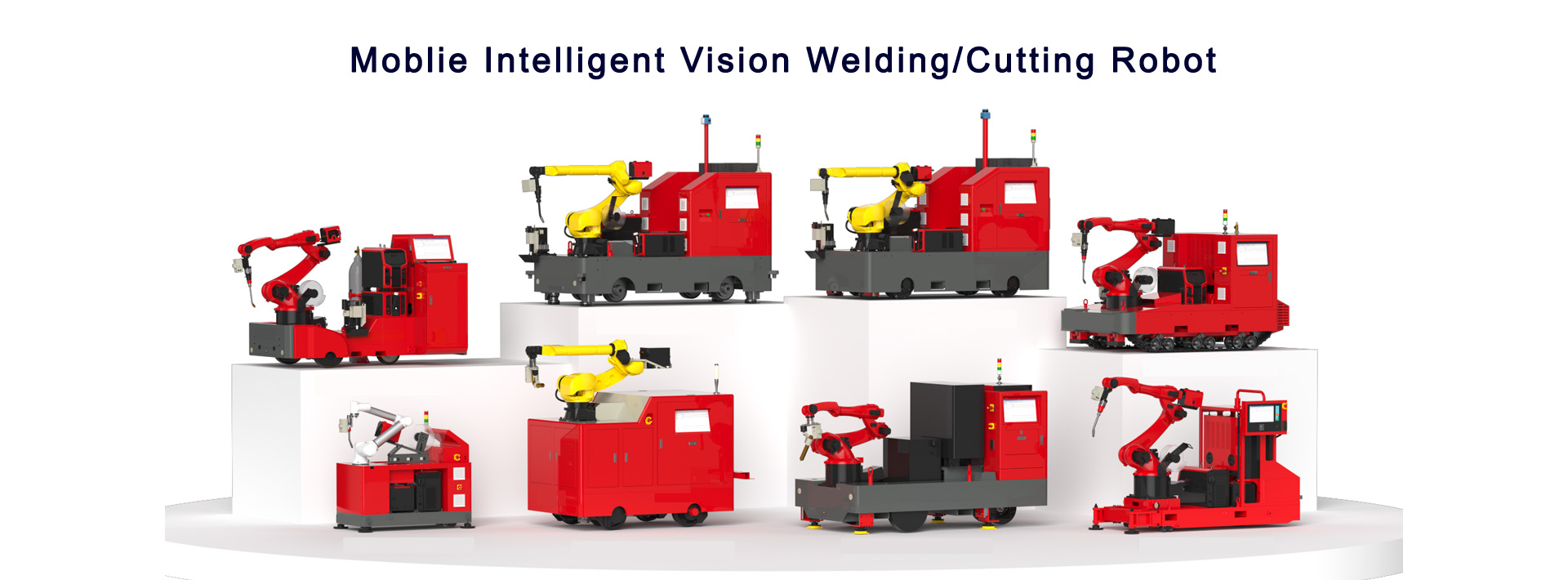
Upfront Costs
Equipment purchase price
When investing in robotic welding systems, you need to account for the initial purchase price. Basic models start at approximately $50,000, while advanced systems with enhanced features can exceed $150,000. This cost typically includes the robot, welding gun, control systems, and initial software. These prices reflect the level of automation and precision offered by the equipment.
Installation and setup expenses
Installation and setup costs are another important consideration. These expenses range from $10,000 to $25,000, depending on the complexity of the system and your facility’s requirements. Proper installation ensures the robotic welding equipment operates efficiently and integrates seamlessly into your production line.
Operational and Long-Term Costs
Consumables and energy usage
Operational costs include consumables like welding wire, gas, and electrodes. These materials can cost between $1,000 and $3,000 monthly, depending on production volume. Robotic welding systems use consumables more efficiently than manual processes, reducing waste caused by human error. Energy usage also adds to monthly expenses, with electricity costs typically amounting to a few hundred dollars.
Maintenance and repair requirements
Routine maintenance is essential to keep your system running smoothly. Regular inspections, part replacements, and software updates help prevent downtime. While robotic systems are reliable, you should budget for occasional repairs and energy consumption. These measures ensure long-term efficiency and reduce unexpected costs.
Return on Investment (ROI)
Productivity gains and cost savings
Robotic welding systems significantly reduce labor costs. For example, manual welding operations costing $100,000 annually can drop to $50,000 with automation. This $50,000 annual savings highlights the productivity gains and cost efficiency of robotic solutions.
Payback period analysis
The payback period for robotic welding equipment is relatively short. A system costing $120,000, with $5,000 in yearly maintenance, can achieve first-year savings of $50,000. With ongoing yearly savings of $95,000, the ROI payback period is approximately 2.5 years. This rapid return makes steel structure robotic welding solutions a smart investment for long-term profitability.
Compare Steel Structure Robotic Welding Solutions
Traditional Industrial Robots
High-speed, high-precision capabilities
Traditional industrial robots excel in large-scale steel structure projects due to their unmatched speed and precision. These welding robots operate continuously, ensuring consistent weld quality and reducing production time. Their ability to handle complex geometries and varying weld gaps makes them indispensable for demanding applications like bridges or highway structures.
Tip: Automating dangerous tasks with these robots enhances workplace safety by minimizing human involvement in hazardous environments.
Best suited for large-scale production
For large-scale production, traditional robots offer several advantages:
- Enhanced Safety: They reduce the risk of accidents by automating dangerous tasks.
- Increased Efficiency: Continuous operation improves productivity and shortens project timelines.
- Cost Savings: Long-term savings from reduced labor costs outweigh the initial investment.
- Precision and Quality: These systems maintain consistent quality throughout the fabrication process.
Collaborative Robots (Cobots)
Safety features for working alongside humans
Cobots are designed with advanced safety features, making them ideal for shared workspaces. These features include:
Safety Feature | Description |
---|---|
Monitored standstill | Detects human presence and stops the robot if it gets too close. |
Hand-guided controls | Allows operators to manually guide the robot for safe teaching of paths. |
Speed and separation monitoring | Slows or stops the robot when humans approach, ensuring safety in shared spaces. |
Power and force limiting technology | Limits force and torque to prevent injuries during accidental contact. |
Flexibility for smaller-scale or custom projects
Cobots are perfect for smaller-scale or custom steel structure projects. Their compact size allows them to fit into tight workspaces without extensive safety measures. You can rely on cobots to complete tasks faster than human workers, improving productivity. Equipped with specialized tools, they deliver precise results, ensuring consistent quality. Cobots also reduce fatigue-related injuries by taking on repetitive tasks.
Hybrid Solutions
Combining traditional and collaborative features
Hybrid robotic welding solutions combine the strengths of traditional robots and cobots. For example, systems like KUKA’s laser hybrid welding merge laser and arc welding technologies. This combination results in faster welding speeds, improved seam quality, and reduced thermal distortion.
Use cases for hybrid systems
Hybrid systems shine in applications requiring both precision and adaptability. The UR10e robotic welding application uses hybrid planning to streamline multi-step processes. It scans weld seams with a laser scanner and executes welding motions based on accurate waypoints. These systems are ideal for industries needing flexible yet high-quality robotic welding solutions.
Assess Manufacturer and Support Services
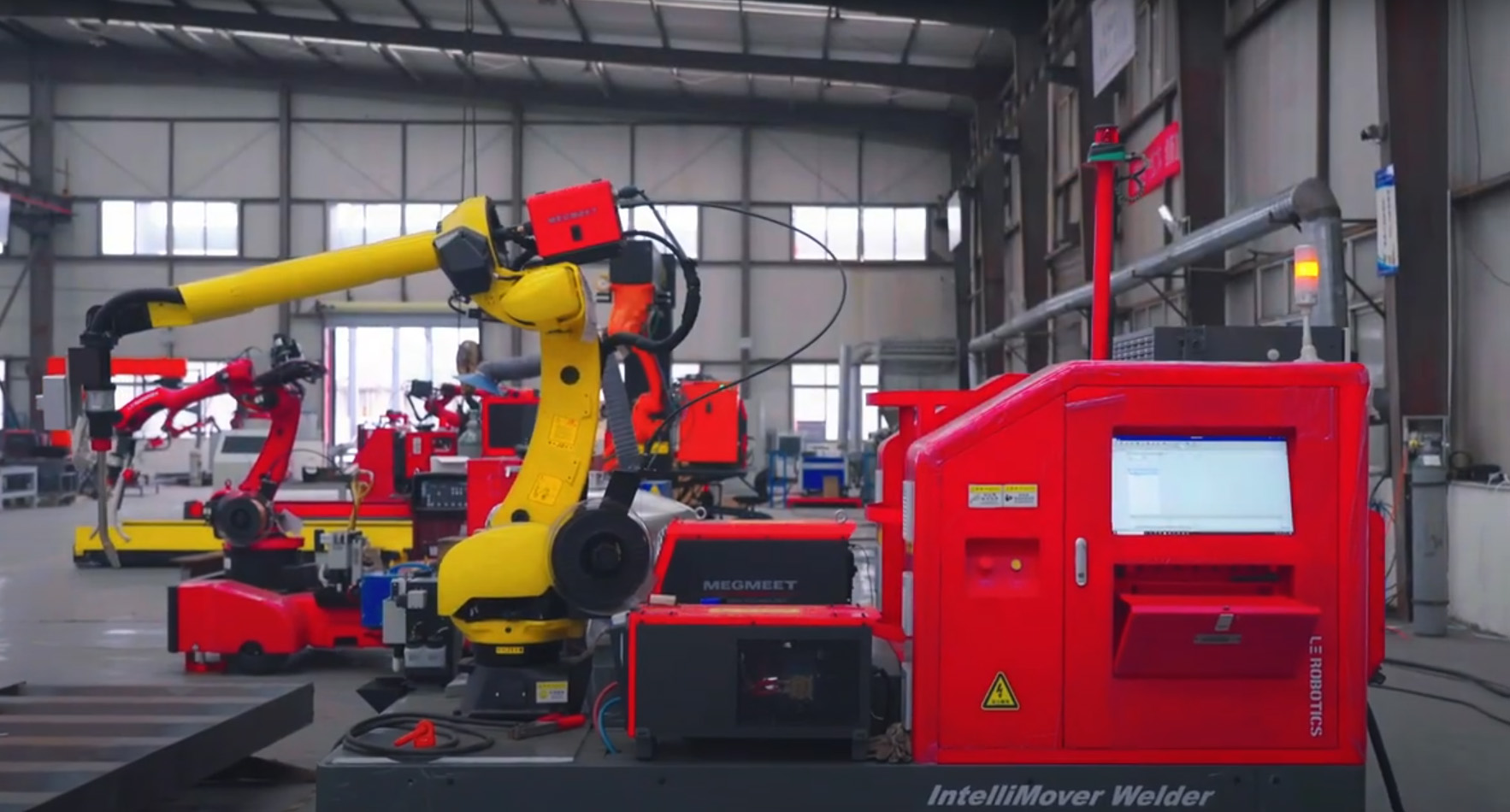
Reputation and Reliability
Researching top manufacturers in the industry
Selecting a reliable manufacturer ensures you receive high-quality robotic welding equipment. Look for manufacturers with a proven track record in the industry. Key factors to consider include:
- Welding software capabilities: Ensure the system integrates seamlessly with your existing setup and offers easy programming.
- Safety compliance: Choose manufacturers that prioritize safety features like emergency stop systems and sensors. These features protect workers and ensure smooth operations.
A manufacturer’s reputation often reflects their commitment to innovation and customer satisfaction. Researching industry leaders and their product offerings can help you make an informed decision.
Customer reviews and case studies
Customer reviews and case studies provide valuable insights into a manufacturer’s reliability. Reviews highlight real-world experiences, while case studies showcase successful implementations. Look for examples of projects similar to yours. This helps you gauge how well the equipment performs under comparable conditions.
Training and Integration Support
Onboarding and operator training programs
Comprehensive training programs ensure your team can operate the system efficiently. Manufacturers often provide:
Type of Support | Description |
---|---|
Onsite Installation and Training | Hands-on training ensures staff can operate and maintain the system, minimizing downtime. |
Physical Assembly and SAT | The team handles assembly and site acceptance testing at the customer’s location. |
Continuous Support and Maintenance | Ongoing support ensures the welding automation system remains efficient and reliable long-term. |
These programs reduce the learning curve and help your team adapt quickly to the new system.
Assistance with system integration
Proper integration ensures the robotic welding equipment works seamlessly with your production line. Manufacturers often offer:
- Custom systems tailored to your specific needs.
- Real-time data acquisition for continuous monitoring and optimization.
- Application-specific design to enhance system performance.
These services ensure smooth operations and maximize productivity.
After-Sales Support
Availability of spare parts and repairs
Reliable after-sales support minimizes downtime. Choose manufacturers that provide easy access to spare parts and repair services. This ensures your system remains operational even during unexpected breakdowns.
Ongoing technical support and updates
Technical support and software updates keep your system running efficiently. Manufacturers offering regular updates ensure your equipment stays compatible with evolving technologies. Continuous support helps you maintain peak performance over time.
Decide Between New or Used Robotic Welding Systems
Benefits of New Systems
Latest technology and features
New robotic welding systems offer cutting-edge technology and advanced features. These systems include the latest innovations in welding automation, such as enhanced sensors, AI-driven processes, and intuitive software interfaces. By investing in new equipment, you gain access to tools that improve efficiency and precision. New systems also allow you to select models tailored to your exact specifications, ensuring they meet your production needs. This customization enhances safety and productivity, reducing overhead costs and increasing profitability.
Warranty and manufacturer support
Purchasing new automated welding equipment comes with the added benefit of manufacturer warranties. These warranties guarantee that the system will perform within specifications for a set period. You also receive comprehensive support, including training, integration assistance, and access to spare parts. This level of service minimizes downtime and ensures your system operates at peak performance.
Advantages of Used Systems
Lower upfront costs
Used robotic welding systems provide a cost-effective alternative for automating welding processes. These systems typically cost around 50% less than new ones, making them an attractive option for businesses with limited budgets. This significant reduction in startup costs allows you to implement welding automation more affordably. Lower initial expenses also lead to quicker returns on investment, enabling you to allocate resources to other areas of your operation.
Availability of refurbished options
Refurbished systems offer a middle ground between new and used equipment. These systems undergo thorough inspections and repairs to ensure they meet performance standards. Refurbished options provide reliable performance at a fraction of the cost of new systems. They also come with limited warranties, giving you added peace of mind.
Key Considerations for Both Options
Evaluating system condition and lifespan
When choosing between new and used systems, you must evaluate the condition and expected lifespan of the equipment. New systems have no history of misuse or poor maintenance, ensuring optimal performance. For used systems, inspect the machine’s housing, components, and maintenance records. A well-maintained used system can still deliver reliable results, but thorough evaluation is essential to avoid unexpected issues.
Compatibility with your project needs
Your project requirements should guide your decision. New systems offer the flexibility to handle complex tasks and integrate seamlessly into modern machine shop automation setups. Used systems may lack some advanced features but can still meet the needs of smaller-scale or less demanding projects. Assess your production goals and choose the option that aligns with your operational demands.
Selecting the right robotic welding system ensures your projects meet quality and efficiency goals. You must align the system with your specific needs by considering factors like proper welding fixtures, integration with other processes, and whether a custom or pre-engineered solution fits best. Inappropriate fixtures alone can cause up to 40% of rejected parts, emphasizing the need for precision.
Evaluating features, costs, and manufacturer support helps you make informed decisions. Innovative solutions like EVS Robotics’ Mobile Intelligent Vision Robot offer unmatched flexibility, precision, and AI-driven optimization. Consult experts, schedule demos, and explore these advancements to maximize your ROI.