
Gantry rail dual welding represents a groundbreaking approach to precision welding. This method employs a gantry rail system, often paired with dual robotic configurations, to achieve exceptional accuracy. It has become indispensable in welding bridge girders, where precision directly impacts structural integrity. By minimizing deformation and enhancing weld quality, this technique ensures robust and reliable structures.
For instance, automated gantry systems with dual weld heads have been shown to save up to 15 hours on large-scale projects, significantly boosting productivity. Such advancements highlight the transformative potential of gantry rail dual welding in modern construction.
Key Takeaways
- Gantry rail dual welding enhances efficiency by allowing simultaneous welding on multiple sections, potentially saving up to 15 hours on large projects.
- This method improves structural integrity by providing precise control over heat input, reducing the risk of weak spots and ensuring uniform welds.
- Cost savings are significant, with gantry systems reducing material consumption by up to 80% and energy usage by 40%, making projects more sustainable.
- Proper setup and calibration of the gantry rail system are crucial for achieving high-quality welds and minimizing distortion during the welding process.
- Regular maintenance of the gantry system, including inspections and lubrication, is essential for consistent performance and longevity of the equipment.
- Implementing safety measures, such as proper PPE and training for operators, is vital to prevent accidents and ensure a safe working environment.
- Utilizing advanced technologies like seam tracking can help avoid common welding defects, ensuring precision and quality in challenging applications.
Benefits of Gantry Rail Dual Welding for Bridge Girders
Improved Efficiency and Precision
I have seen how gantry rail dual welding transforms the welding process. This method uses advanced robotic systems to deliver unmatched precision. The dual configuration ensures simultaneous welding on multiple sections, which reduces errors and enhances alignment. Unlike traditional methods, this approach controls heat input effectively. By doing so, it minimizes distortion and ensures consistent weld quality.
For example, gantry systems with dual welding heads can save up to 15 hours on large-scale projects like overhead crane builds. This efficiency directly translates to faster project completion without compromising accuracy.
The system also increases deposition rates, which means more material is applied in less time. This feature is crucial when working on large structures like bridge girders. It ensures that every weld meets the highest standards of quality while maintaining a steady workflow.
Enhanced Structural Integrity
Structural integrity is critical in bridge construction. I have observed how gantry rail dual welding strengthens the overall framework of bridge girders. The precise control over heat input reduces the risk of weak spots or cracks in the welds. This level of precision ensures that the welded joints can withstand heavy loads and environmental stress.
Additionally, the dual robotic setup allows for uniform welds across the entire length of the girder. Uniformity is essential for distributing stress evenly throughout the structure. This method not only enhances the durability of the bridge but also reduces the likelihood of future maintenance issues.
According to industry data, controlling heat input through gantry systems significantly reduces welding deformation. This improvement directly impacts the long-term stability of bridge girders.
Cost and Time Savings
Gantry rail dual welding offers substantial savings in both time and resources. I have noticed that this method consumes fewer materials compared to traditional welding techniques. For instance, advanced gantry systems can reduce welding material consumption by up to 80%. This reduction lowers costs without sacrificing quality.
Power consumption also decreases significantly. Modern gantry systems use up to 40% less energy than conventional methods. These savings make the process more sustainable and cost-effective for large-scale projects.
Projects involving bridge girders benefit immensely from these efficiencies. Faster welding times and reduced resource usage allow teams to allocate their budgets more effectively. This approach ensures that projects stay on schedule and within financial constraints.
Step-by-Step Process for Using Gantry Rail Dual Welding
Preparing the Gantry Rail System
I always start by ensuring the gantry rail system is properly set up. This step involves inspecting the steel rails for alignment and stability. Any misalignment can compromise the precision of the welding process. The rail length and gauge must match the dimensions of the workpiece, especially when working on large structures like bridge girders. For instance, a gantry system with a rail length of up to 30 meters and a gauge of 6 meters provides the flexibility needed for such projects.
Next, I calibrate the system to ensure smooth movement along the X and Y axes. Modern gantry systems, like the GantryRail DualWeld Station, offer movement speeds of at least 20m/min on the X-axis and 12m/min on the Y-axis. These speeds enhance productivity while maintaining accuracy. I also verify that the system operates within the recommended ambient temperature range of 0°C to +45°C. This ensures optimal performance during the welding process.
Setting Up the Welding Equipment
Once the gantry rail system is ready, I focus on the welding equipment. I begin by selecting the appropriate welding method, such as MIG or submerged arc welding (SAW), based on the project requirements. For bridge girders, I prefer dual robotic configurations with twin wire weld heads. These setups allow simultaneous welding on multiple sections, which improves efficiency and ensures uniform welded connections.
I then preset the welding parameters, including voltage, current, and wire feed speed. This step is crucial for achieving consistent weld quality. Advanced systems, like those equipped with Miller® SubArc DC 1000 Digital power sources, allow me to standardize these parameters at the start of the cycle. This eliminates variability and ensures that every weld meets the required standards.
Finally, I load the filler metals into the wire feeders. For large-scale projects, I use high-quality materials like Hobart® filler metals. These materials enhance the durability of welded i beams and other structural components. Proper setup of the welding equipment minimizes downtime and ensures a seamless workflow.
Executing the Dual Welding Process
With the system and equipment ready, I proceed to execute the welding process. I program the gantry robot to follow a pre-determined path along the workpiece. This ensures precise and uniform welds across the entire length of the girder. The dual robotic setup allows me to weld both sides simultaneously, which reduces the overall welding time.
During the process, I monitor the heat input closely. Controlling the heat input is essential for minimizing distortion and preventing weak spots in the welded connections. Modern gantry systems excel in this aspect, providing precise control over the welding parameters. This results in high-quality welds that enhance the structural integrity of the bridge.
I also pay attention to the deposition rate. Higher deposition rates mean more material is applied in less time, which is particularly beneficial for large structures like welded i beams. By optimizing the deposition rate, I ensure that the welds are both strong and efficient.
After completing the welding, I conduct a thorough inspection to verify the quality of the welds. This includes checking for uniformity, strength, and any potential defects. A well-executed dual welding process not only improves the durability of the structure but also reduces the need for future maintenance.
Quality Control and Inspection
I always prioritize quality control and inspection to ensure the welding process meets the highest standards. This step is critical for maintaining the structural integrity of bridge girders. I begin by visually inspecting the welds. This allows me to identify surface defects like cracks, porosity, or uneven weld beads. A thorough visual check ensures that no obvious issues compromise the strength of the welded connections.
Next, I use non-destructive testing (NDT) methods to evaluate the internal quality of the welds. Techniques like ultrasonic testing and radiographic testing help me detect hidden flaws. These methods provide detailed insights into the weld’s internal structure without damaging the workpiece. For bridge projects, this level of scrutiny is essential to guarantee long-term durability.
I also measure the weld dimensions to confirm they meet the project specifications. Tools like calipers and weld gauges help me verify the width, height, and penetration of each weld. Accurate measurements ensure that the welding process adheres to the required standards. This step is especially important for large structures like bridge girders, where precision directly impacts performance.
Finally, I document all inspection results. This includes recording any defects, corrective actions taken, and final approvals. Detailed records provide a clear audit trail, which is invaluable for future reference. By following a systematic approach to quality control and inspection, I ensure that every bridge girder meets the demands of modern construction.
For example, using ultrasonic testing on welded bridge girders has proven effective in identifying subsurface defects. This proactive approach minimizes the risk of structural failures.
Best Practices and Common Challenges
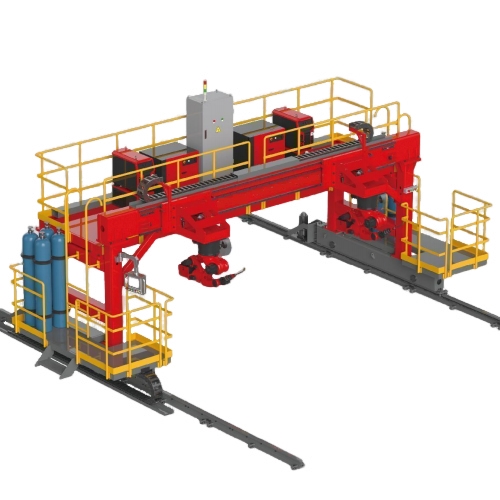
Safety Considerations
Safety remains my top priority when working with gantry rail dual welding systems. I always ensure that all team members wear appropriate personal protective equipment (PPE). This includes welding helmets, gloves, flame-resistant clothing, and safety boots. Proper PPE minimizes the risk of burns, eye injuries, and other hazards.
Before starting any welding operation, I inspect the work area for potential risks. I check for flammable materials, ensure proper ventilation, and confirm that all electrical connections are secure. A clean and organized workspace reduces accidents and improves efficiency.
I also emphasize the importance of training. Operators must understand how to handle the equipment safely. For instance, I train my team on emergency stop procedures and the correct way to operate dual robotic configurations. This preparation ensures that everyone knows how to respond to unexpected situations.
According to industry experts, well-trained operators significantly reduce the likelihood of workplace accidents. Investing in safety training not only protects workers but also enhances productivity.
Avoiding Common Welding Defects
Welding defects can compromise the structural integrity of bridge girders. I focus on preventing these issues by following best practices. One common defect is porosity, which occurs when gas gets trapped in the weld. To avoid this, I ensure that the workpiece is clean and free of contaminants like oil, rust, or moisture.
Another issue I often encounter is incomplete fusion. This happens when the weld metal fails to bond properly with the base material. I address this by setting the correct welding parameters, such as voltage and current. Proper calibration ensures strong and consistent welds.
Seam tracking technology has been a game-changer for me. It allows the gantry system to adjust automatically to the workpiece’s contours. This feature is especially useful for long welds on bridge girders, where precision is critical. For example, a structural steel fabrication company improved their welding deposition rates by upgrading to a gantry system with seam tracking capabilities.
Flexible automation, like seam tracking, proves invaluable in challenging applications. It ensures high-quality welds even when working with varying material thicknesses.
Maintenance of Equipment
Regular maintenance keeps my gantry rail dual welding system running smoothly. I start by inspecting the steel rails for wear and tear. Misaligned or damaged rails can affect the system’s accuracy. I also check the robotic arms and welding heads for signs of wear. Replacing worn components promptly prevents costly downtime.
Lubrication plays a crucial role in maintaining the system’s mobility. I apply lubricants to the moving parts, such as the X and Y axes, to ensure smooth operation. Keeping the system clean is equally important. Dust and debris can interfere with the equipment’s performance, so I make it a point to clean the system after each use.
I also schedule regular software updates for the gantry system. Updated software improves functionality and ensures compatibility with the latest welding techniques. Routine checks of the power supply and electrical connections further enhance the system’s reliability.
A proactive maintenance approach extends the lifespan of the equipment. It also ensures consistent performance, which is essential for large-scale projects like bridge construction.
Gantry rail dual welding has revolutionized how I approach bridge construction. Its ability to deliver unmatched efficiency, precision, and structural integrity makes it an indispensable tool for welding bridge girders. By following best practices, such as proper equipment maintenance and quality control, I ensure consistent results and long-term durability. Addressing challenges like safety and defect prevention further enhances project outcomes.
I encourage adopting this advanced welding method. It not only saves time and resources but also ensures superior quality. For any bridge project, gantry rail dual welding stands as a reliable and efficient solution.
FAQ
What is gantry rail dual welding, and why is it ideal for bridge projects?
Gantry rail dual welding is a specialized welding method that uses a gantry system equipped with dual robotic configurations. This setup ensures precise and efficient welding, especially for large structures like bridge girders. The dual welding heads allow simultaneous welding on multiple sections, reducing time and improving alignment. I’ve found this method particularly effective in minimizing deformation and enhancing the structural integrity of bridges.
For example, automated gantry systems with submerged arc welding (SAW) have revolutionized productivity. A company using this system reported saving up to 15 hours on large overhead crane builds, showcasing its efficiency for similar bridge applications.
How does gantry rail dual welding improve structural integrity?
This method provides precise control over heat input, which reduces the risk of weak spots or cracks in the welds. The dual robotic setup ensures uniform welds across the entire length of the girder, distributing stress evenly throughout the structure. I’ve seen how this uniformity enhances the durability of bridges, making them more resistant to heavy loads and environmental stress.
According to industry data, controlling heat input through gantry systems significantly reduces welding deformation, directly impacting the long-term stability of bridge girders.
What are the primary design considerations for gantry systems?
When designing a gantry system for bridge projects, I focus on factors like rail length, gauge, and mobility. Custom solutions are available for complex applications, such as Dual Tandem SAW Heavy Duty Gantries. These systems handle large girders with intricate geometries, ensuring flexibility and precision. Proper calibration of the X and Y axes also plays a critical role in achieving accurate welds.
What types of welding methods are compatible with gantry rail systems?
Gantry rail systems support various welding methods, including MIG and submerged arc welding (SAW). For bridge girders, I prefer SAW due to its efficiency and ability to handle large-scale projects. Advanced systems, like those equipped with Miller® SubArc DC 1000 Digital power sources, deliver consistent results. These setups also allow for dual robotic configurations, which enhance productivity and weld quality.
How does gantry rail dual welding save time and resources?
This method reduces welding time by enabling simultaneous welding on multiple sections. It also minimizes material consumption and energy usage. For instance, advanced gantry systems can lower welding material consumption by up to 80% and use 40% less energy than traditional methods. These savings make the process both cost-effective and sustainable for bridge construction.
What safety measures should I follow when using gantry rail dual welding?
Safety is always my top priority. I ensure all team members wear proper personal protective equipment (PPE), such as helmets, gloves, and flame-resistant clothing. Before starting, I inspect the workspace for hazards and confirm that all electrical connections are secure. Training operators on emergency procedures and equipment handling is also essential for maintaining a safe environment.
How can I avoid common welding defects in bridge projects?
To prevent defects like porosity and incomplete fusion, I clean the workpiece thoroughly and set the correct welding parameters. Seam tracking technology has been invaluable for me. It allows the gantry system to adjust automatically to the workpiece’s contours, ensuring precise welds. This feature is especially useful for long welds on bridge girders, where accuracy is critical.
What maintenance does a gantry rail dual welding system require?
Regular maintenance keeps the system running smoothly. I inspect the steel rails for wear, lubricate moving parts, and clean the equipment after each use. Software updates improve functionality and ensure compatibility with the latest welding techniques. Routine checks of the power supply and robotic arms further enhance reliability, which is crucial for large-scale bridge projects.
Can gantry rail dual welding handle complex bridge designs?
Yes, it can. Custom gantry solutions, such as Dual Tandem SAW Heavy Duty Gantries, are designed for complex geometries. These systems provide the flexibility needed to weld intricate designs while maintaining precision. I’ve used such setups to tackle challenging projects, and they consistently deliver excellent results.
Why should I choose gantry rail dual welding for my bridge project?
This method offers unmatched efficiency, precision, and structural integrity. It saves time and resources while ensuring high-quality welds. By adopting gantry rail dual welding, you can achieve superior results and meet the demands of modern bridge construction. I highly recommend this approach for any large-scale project.