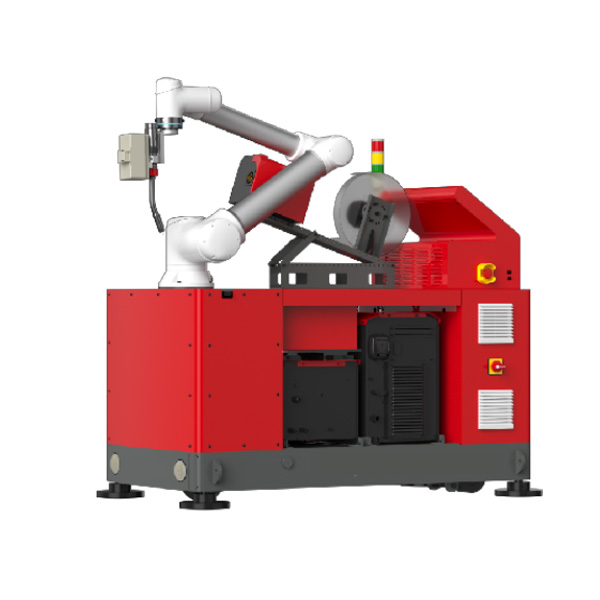
Robots have revolutionized industrial applications of robots in material handling and assembly by transforming these processes. They operate tirelessly, boosting productivity and reducing errors. For example, Amazon employs over 200,000 robots globally to streamline fulfillment. Additionally, robots improve safety by handling hazardous tasks, minimizing workplace injuries, and ensuring precision in manufacturing, which enhances product quality and consistency.
Key Takeaways
- Robots work nonstop, making fewer mistakes and improving efficiency in handling and assembly.
- Safety gets better as robots do dangerous jobs, keeping workers safe and workplaces secure.
- Using robots saves money over time by making more products, lowering worker costs, and checking quality better.
Material Handling Robots in Industrial Applications
Types of Material Handling Robots
Material handling robots play a crucial role in streamlining operations across industries. You can find two main types of these robots in use today:
- Automated Guided Vehicles (AGVs): These robots follow predefined paths to transport materials autonomously. They enhance safety and efficiency in environments like warehouses and factories.
- Autonomous Mobile Robots (AMRs): Unlike AGVs, AMRs navigate freely using advanced sensors and software. They avoid obstacles and adapt to dynamic environments, making them ideal for tasks requiring flexibility.
Both types of robots reduce manual labor and improve productivity, especially in large-scale operations.
Applications in Palletizing and Sorting
Palletizing and sorting are essential tasks in material handling. Robots excel in these areas by offering precision and adaptability. For example, robotic systems equipped with customizable end-of-arm tools (EOAT) securely grip items without causing damage. These robots follow pre-programmed stacking patterns to place products accurately on pallets.
Role/Functionality | Description |
---|---|
Customizable EOAT | Suction cups, clamps, or other tools grip items securely without damage. |
Precision Placement | The arm moves each product to the pallet following a pre-programmed stacking pattern. |
Forming Layers and Slip sheets | Organizes products into layers for stability and balance during shipping and storage. |
Integration with Other Equipment | Connects with conveyors, pallet dispensers, and stretch wrappers for efficient operation. |
Adapting in Real-Time | Monitors operations and adjusts for product variations, conveyor delays, and misalignments. |
These robots also adapt in real-time to handle variations in product size or conveyor speed, ensuring smooth operations.
Handling Hazardous Materials with Robots
Handling hazardous materials poses significant risks to human workers. Robots eliminate these risks by performing dangerous tasks with precision. For instance, mobile handling robots can operate in confined spaces or environments with toxic gases, reducing human exposure.
Key safety protocols ensure the effective use of robots in such scenarios:
- Identify potential hazards in the robot’s work area.
- Evaluate risks associated with these hazards.
- Implement control measures, such as OSHA-compliant guarding and safety devices.
- Monitor the effectiveness of these measures regularly.
By following these steps, you can ensure that industrial robots handle hazardous materials safely and efficiently.
Assembly Robots and Their Industrial Applications
Key Tasks Performed by Assembly Robots
Assembly robots handle repetitive and intricate tasks with unmatched precision. You’ll find them widely used in industries like automotive and electronics. In the automotive sector, these robots perform welding, painting, and moving heavy car parts, ensuring both safety and efficiency. In electronics manufacturing, they assemble tiny components and solder circuit boards with remarkable accuracy.
Different types of robotic systems excel in specific tasks. Cylindrical robots are ideal for welding and painting, while SCARA robots deliver fast and precise movements for assembly and packaging. Delta robots, known for their speed, are perfect for pick-and-place operations on assembly lines. These specialized robots streamline production processes, making them indispensable in modern manufacturing.
Precision in Welding and Fastening
Assembly robots achieve exceptional precision in welding and fastening tasks. Advanced sensors and vision systems guide their operations, allowing them to identify exact locations and orientations. This ensures every weld and fastener is placed correctly. Robots follow pre-programmed instructions, enabling them to perform repetitive actions with high accuracy and zero fatigue.
Recent advancements in robotic welding include models like the QJR6-1400H, which features a 6KG payload and a 1.4-meter reach. These innovations enhance accuracy, reduce lead times, and improve safety in manufacturing. By automating these processes, you can achieve consistent results and minimize errors.
Role in Quality Inspection and Assurance
Robots play a critical role in quality inspection and assurance. Equipped with advanced vision systems and sensors, they meticulously inspect products for defects. This ensures assembly quality and reduces recalls. In sensitive industries like pharmaceuticals, robots check for contaminants and verify proper fill levels, safeguarding product integrity.
Automated inspection systems also enhance speed and accuracy. They reduce human error, improve product quality, and provide traceability in manufacturing. By integrating these robotic systems, you can maintain high standards and build customer trust.
Benefits of Robots in Material Handling and Assembly
Boosting Efficiency and Productivity
Robots significantly enhance efficiency and productivity in material handling and assembly. They operate continuously without breaks, ensuring uninterrupted workflows. This capability allows you to meet tight production deadlines and increase output. Robots also minimize waste by performing tasks with precision, reducing errors that could lead to material loss.
Benefit | Description |
---|---|
Increased productivity | Robots operate continuously, enhancing productivity and minimizing waste through precision tasks. |
Improved quality control | Integrated systems enable robots to detect defects and ensure uniform product quality. |
Reduced costs | Long-term savings from higher output and lower error rates offset initial investment costs. |
Improved workplace safety | Robots handle hazardous tasks, reducing the risk of injury for human workers. |
Increased competitiveness | Robotics provide a competitive edge through speed and cost-efficiency. |
By integrating automation solutions, you can streamline operations and maintain a competitive edge in industrial applications.
Enhancing Workplace Safety
Robots play a vital role in improving workplace safety. They handle hazardous tasks, such as working with toxic chemicals or operating in extreme conditions, which reduces risks for human workers. For example, robots can autonomously detect gas leaks in chemical plants, preventing accidents and protecting lives.
Advanced software continuously monitors robots, identifying potential failures before they occur. Predictive maintenance ensures timely repairs, minimizing risks. Additionally, robotic arms and vehicles eliminate exposure to dangerous machinery, while cobots reduce repetitive strain injuries. By adopting these automation solutions, you create a safer environment for your workforce.
Reducing Costs and Increasing ROI
Although the initial investment in robotics may seem high, the long-term savings justify the expense. Robots operate 24/7, increasing production rates and reducing labor costs. Automation minimizes errors, leading to fewer defective products and lower waste. This efficiency translates into significant cost savings over time.
- Labor Cost Savings: Robots reduce payroll expenses by automating repetitive tasks.
- Reduction in Scrap and Waste: Precision reduces material waste and error correction costs.
- Improved Consistency and Quality: Robots ensure uniformity, enhancing customer satisfaction.
- Enabling Lights-Out Production: Robots work continuously, lowering operational costs.
By leveraging industrial robot applications, you can achieve a quick return on investment, often within a year, while improving overall operational efficiency.
Challenges and Solutions in Robotic Integration
Addressing Safety Concerns
Safety remains a top priority when integrating robots into industrial environments. Without proper measures, accidents and ergonomic issues can arise. You can address these concerns by implementing comprehensive safety protocols and adhering to regulatory standards like OSHA and ISO. Operator training is another critical step. It ensures workers understand how to interact with robots safely, minimizing risks.
Safety Concern | Description |
---|---|
Comprehensive Safety Protocols | Essential for ensuring safe operation of robots in industrial settings. |
Adherence to Regulatory Standards | Compliance with OSHA, ANSI, and ISO standards is crucial for safety in robotic operations. |
Operator Training | Proper training for operators is necessary to minimize risks associated with robotic integration. |
Ergonomic Issues | Addressing ergonomic concerns to prevent long-term health issues for workers. |
Potential for Accidents | Risks of accidents if safety measures are not properly implemented. |
Advanced software for monitoring and predictive maintenance also enhances safety. It identifies potential failures before they occur, reducing the risk of accidents. By prioritizing safety, you create a secure environment where humans and robots can work together effectively.
Managing High Initial Costs
The high upfront cost of robotic systems often deters businesses. However, you can manage these expenses by collaborating with experts to identify your specific operational needs. Choosing cost-effective robotic systems tailored to your requirements can also reduce initial costs.
Investing in robots may seem expensive at first, but the long-term benefits justify the expense. Robots optimize manufacturing operations, leading to significant savings. They increase productivity, reduce labor costs, and improve quality control. These advantages often result in a positive return on investment within a year.
Overcoming Integration Challenges
Integrating robots into existing workflows can be complex. You may face challenges like programming difficulties, workflow disruptions, and safety concerns. Careful planning and collaboration with experienced professionals can help you overcome these obstacles.
- Assess your current workflows and identify areas where robots can add value.
- Develop a detailed integration plan to minimize disruptions.
- Train your team to handle programming and maintenance tasks.
- Implement safety measures to ensure a secure work environment.
By addressing these challenges proactively, you can streamline the integration process and maximize the benefits of industrial robot applications.
Future Trends in Industrial Robotics
AI Integration in Material Handling and Assembly
Artificial intelligence is transforming material handling and assembly processes. AI-powered robots now make intelligent decisions and adapt to real-time changes in their environment. For instance, the Routing Agent processes material data to plan efficient movement paths. It dynamically adjusts for obstacles, ensuring smooth operations. Similarly, the Maintenance Agent uses predictive algorithms to monitor system health. This approach schedules maintenance before failures occur, reducing downtime and optimizing performance.
Machine learning further enhances these capabilities. Robots equipped with AI can analyze data, predict outcomes, and adjust their actions. This adaptability improves efficiency and ensures consistent results. By integrating AI into your operations, you can achieve smarter automation and better system performance.
Human-Robot Collaboration in Manufacturing
Collaborative robots, or cobots, are reshaping manufacturing by working alongside humans. These robots handle repetitive tasks, freeing you to focus on creative and complex work. This collaboration boosts productivity and job satisfaction. Cobots also improve workplace safety by taking on hazardous tasks, reducing the risk of injuries.
Their precision enhances product quality and minimizes errors. For example, cobots perform quality checks to ensure products meet high standards. This reduces defects and builds customer trust. By integrating cobots into your processes, you can achieve a safer, more efficient, and cost-effective manufacturing environment.
Advancements in Autonomous Robotic Systems
Autonomous robotic systems are evolving rapidly, offering exciting possibilities for industrial applications. Advanced sensing technologies, such as LiDAR and 3D vision, improve spatial awareness and precision. AI and machine learning enable robots to learn from data and adapt to tasks, enhancing performance over time.
Integration with the Internet of Things (IoT) allows robots to communicate in real-time. This connectivity optimizes operations and enables predictive maintenance. Additionally, 3D printing supports the rapid prototyping of robotic components, accelerating innovation. These advancements make autonomous systems more versatile and efficient, paving the way for smarter industrial automation.
The industrial applications of robots in material handling and assembly have transformed manufacturing. They enhance efficiency, precision, and safety while reducing costs. Adopting robotic solutions ensures higher productivity and quality. Emerging trends like AI and IoT integration promise smarter, more adaptable systems, paving the way for a future of seamless industrial automation.
FAQ
What industries benefit the most from robotic material handling and assembly?
Industries like automotive, electronics, pharmaceuticals, and e-commerce benefit greatly. Robots improve efficiency, precision, and safety, making them essential for high-volume and high-precision operations.
How do robots improve workplace safety?
Robots handle hazardous tasks, reducing human exposure to risks. For example, they work with toxic chemicals, operate in extreme conditions, and prevent repetitive strain injuries.
Tip: Regularly monitor and maintain robots to ensure optimal safety and performance.
Are robots cost-effective for small businesses?
Yes, robots can be cost-effective. Collaborative robots (cobots) offer affordable solutions for small businesses. They require minimal programming and deliver quick returns on investment through increased productivity.
Note: Start with scalable robotic systems to match your business growth.