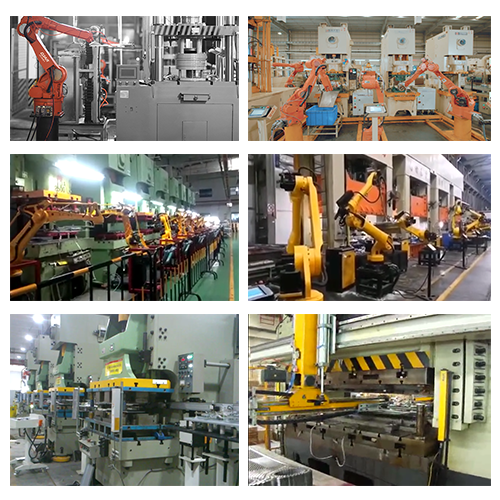
Are production errors, wasteful materials and inefficient processes becoming an ongoing source of frustration for you? Electronic Vision Systems (EVS) have proven invaluable at solving such problems by augmenting machine tending robots with visual intelligence for precision placement that once seemed unimaginable. But exactly how does this technology work and what effect can it have on my business?
In this post, we’ll take an in-depth look at vision-equipped machine tending robots and discover their transformative effects on various industries and implementation challenges. Get ready to be amazed as this cutting-edge technology could be your solution to production line woes!
Enhancing Machine Tending Robots with Vision
Improved accuracy in object detection
Machine tending robots equipped with advanced vision systems can significantly enhance their accuracy in object detection. These systems utilize high-resolution cameras and sophisticated algorithms to precisely identify and locate parts, even in complex environments. By incorporating machine learning techniques, these robots can adapt to variations in part shapes, sizes, and orientations, ensuring consistent performance.
Feature | Benefit |
---|---|
High-resolution cameras | Detailed part recognition |
Advanced algorithms | Precise localization |
Machine learning | Adaptation to part variations |
Real-time adjustments for optimal placement
Vision-enabled machine tending robots excel in making real-time adjustments for optimal part placement. They can:
-
Continuously monitor the work environment
-
Detect changes in part positions or orientations
-
Adjust grip and placement strategies on-the-fly
-
Compensate for minor misalignments or vibrations
This dynamic capability ensures that parts are always placed with the highest precision, regardless of environmental factors or slight inconsistencies in part presentation.
Reduced errors and waste in production
By integrating vision systems, machine tending robots significantly reduce errors and waste in production processes. The enhanced accuracy and real-time adjustment capabilities lead to:
-
Fewer misplaced or dropped parts
-
Decreased damage to delicate components
-
Minimized need for rework or quality checks
-
Optimized material usage and reduced scrap
Increased flexibility for handling diverse parts
Vision-enabled machine tending robots offer unprecedented flexibility in handling diverse parts. They can quickly adapt to different:
-
Part geometries and sizes
-
Surface finishes and textures
-
Material properties
This versatility allows manufacturers to use a single robot for multiple product lines or easily switch between different parts without extensive reprogramming. As production needs evolve, these robots can be quickly reconfigured to handle new parts, making them a valuable asset in dynamic manufacturing environments.
Precision Placement Capabilities
Sub-millimeter accuracy in object positioning
Machine tending robots equipped with advanced vision systems can achieve remarkable precision in object placement, often reaching sub-millimeter accuracy. This level of precision is crucial for industries where even the slightest misalignment can lead to significant quality issues or production errors.
Accuracy Level | Typical Applications |
---|---|
0.1 mm | Microelectronics assembly |
0.5 mm | Automotive component fitting |
1.0 mm | General manufacturing |
Adaptive gripping techniques
Vision-integrated machine tending robots employ sophisticated gripping mechanisms that can adapt to various object shapes, sizes, and materials. These adaptive techniques include:
-
Force-feedback grippers
-
Vacuum suction cups
-
Magnetic end effectors
-
Multi-finger robotic hands
By combining these gripping methods with real-time visual data, robots can handle delicate components without damage and securely manipulate irregularly shaped objects.
Compensation for part variations and misalignments
One of the most significant advantages of integrating vision systems into machine tending robots is their ability to compensate for part variations and misalignments. This capability ensures consistent performance even when dealing with:
-
Non-uniform part sizes
-
Slight deformations in components
-
Misaligned workpieces on conveyors
-
Variations in part orientation
The vision system continuously analyzes the workspace, allowing the robot to make real-time adjustments to its movements and gripping strategy. This adaptive behavior significantly reduces errors and improves overall production efficiency.
Applications in Various Industries
A. Electronics manufacturing
In the electronics industry, machine tending robots equipped with vision systems excel at precise component placement and PCB assembly. These robots can:
-
Identify and pick tiny components with utmost accuracy
-
Place surface-mount devices (SMDs) on circuit boards
-
Inspect solder joints and component alignment
Task | Precision | Speed |
---|---|---|
SMD placement | ±0.02 mm | Up to 120,000 CPH |
PCB inspection | 10 µm resolution | 100 cm²/second |
B. Automotive assembly
Vision-guided machine tending robots revolutionize automotive assembly lines by:
-
Aligning and inserting engine components
-
Handling and positioning body panels
-
Performing quality control checks on assembled parts
C. Pharmaceutical packaging
In pharmaceutical manufacturing, these robots ensure:
-
Precise dosage filling in medication containers
-
Sterile handling of sensitive medical products
-
Inspection of packaging integrity and labeling accuracy
D. Aerospace component handling
The aerospace industry benefits from vision-integrated robots for:
-
Precise positioning of aircraft structural components
-
Inspection of complex geometries in engine parts
-
Handling of delicate composite materials
E. Food and beverage processing
In food and beverage processing, machine tending robots with vision capabilities offer:
-
Hygienic handling of food products
-
Accurate sorting and packaging of items
-
Quality control checks for consistency and defects
These diverse applications demonstrate the versatility of vision-enhanced machine tending robots across industries, significantly improving precision, efficiency, and quality control in manufacturing processes.
Overcoming Implementation Challenges
Integration with existing robotic systems
Integrating vision systems into existing machine tending robots can be a complex process, but it offers significant benefits in precision and flexibility. Here are some key considerations:
-
Compatibility: Ensure the vision system is compatible with the robot’s control system
-
Communication protocols: Implement proper protocols for seamless data exchange
-
Software updates: Upgrade robot software to support vision-guided operations
-
Hardware modifications: Adapt robot end-effectors or add cameras as needed
Integration Step | Purpose | Challenges |
---|---|---|
Compatibility check | Ensure system harmony | Legacy systems may require upgrades |
Protocol implementation | Enable data exchange | Different protocols may need translation |
Software upgrade | Support vision functions | Downtime during installation |
Hardware modification | Adapt for vision capabilities | May require custom solutions |
Calibration and maintenance requirements
Proper calibration and regular maintenance are crucial for the optimal performance of vision-enabled machine tending robots:
-
Initial calibration:
-
Camera alignment
-
Lens focus adjustment
-
Color and contrast settings
-
-
Periodic recalibration:
-
After system updates
-
Following significant environmental changes
-
When accuracy drifts
-
-
Routine maintenance:
-
Lens cleaning
-
Cable inspection
-
Software updates
-
Training operators for vision-enabled systems
Effective training is essential for operators to maximize the potential of vision-enabled machine tending robots:
-
Vision system basics:
-
Camera technology
-
Image processing principles
-
Lighting techniques
-
-
Software interface training:
-
Vision program creation
-
Parameter adjustment
-
Troubleshooting common issues
-
-
Hands-on practice:
-
Simulated scenarios
-
Real-world application exercises
-
By overcoming these challenges, manufacturers will be able to successfully integrate vision systems in their machine-tending robots and improve precision and efficiency for various industrial applications.
Robots that can be programmed to operate machines with vision are revolutionizing the precision placement of products in many industries. These robots are able to identify, locate and handle objects accurately with unmatched precision by integrating advanced vision system. This technology transforms manufacturing processes and improves quality control in industries ranging from electronics to automotive.
Integration of vision systems in machine-tending robots is becoming increasingly important as businesses embrace automation. By overcoming implementation challenges and realizing the full potential of these technologies, businesses can increase productivity, reduce mistakes, and remain competitive in an industry that is rapidly changing. This innovative approach to machine-tending is a must for anyone who wants to succeed in the future of manufacturing.