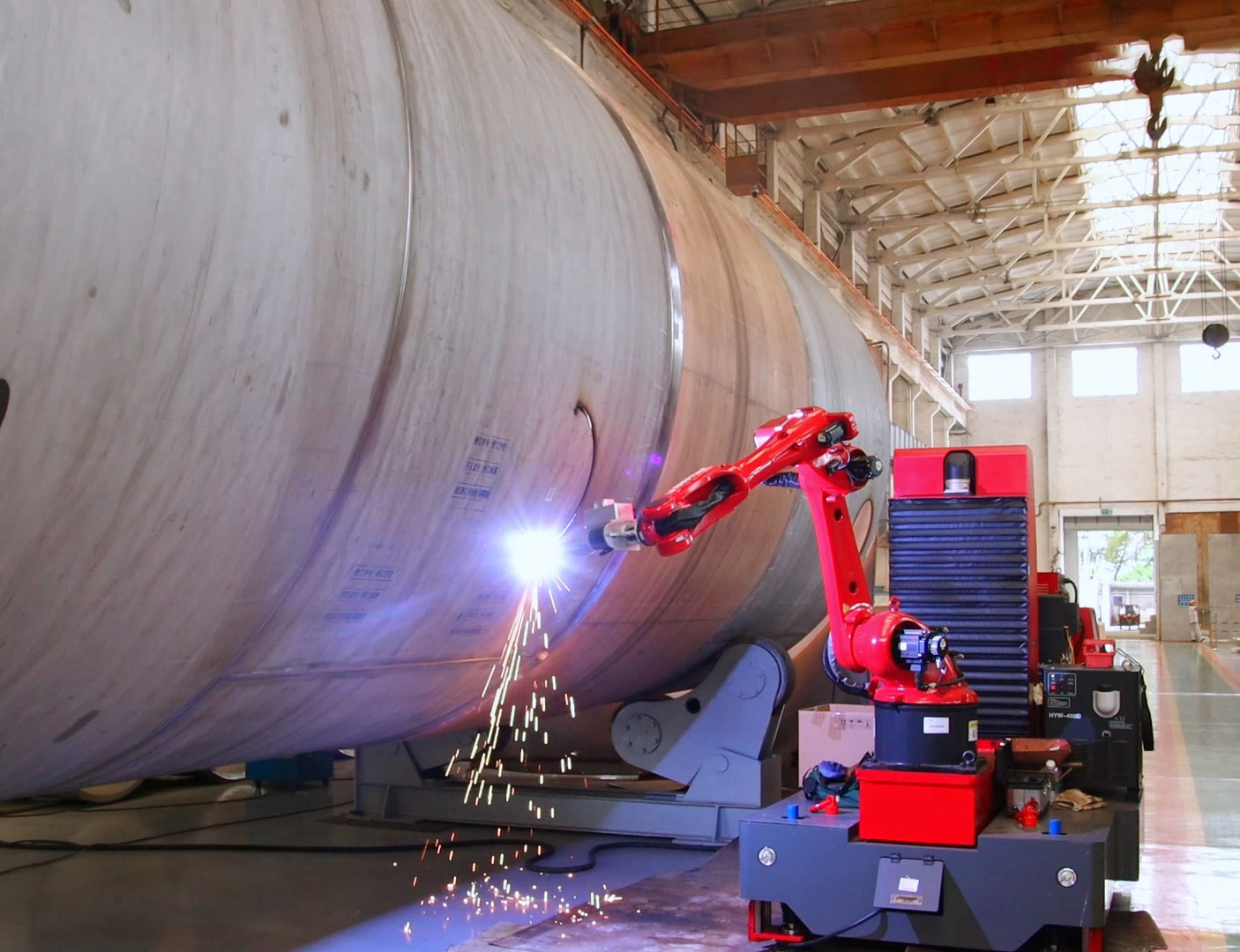
The use of robots with autonomous plasma cutting technology is transforming factories. Plasma cutting robots help industries operate faster, better, and smarter. These robots are highly accurate when cutting and handling materials. They can work nonstop, which saves money and boosts production. With smart sensors, they make clean, precise cuts every time.
By 2025, many industries will rapidly adopt this autonomous plasma cutting technology. Fields like aerospace and construction are already utilizing these robots for impressive results. Developing countries are also investing significantly in robots to enhance their factories. Understanding this technology now will position you for success in future manufacturing.
Key Takeaways
- Plasma cutting robots make work safer by doing risky jobs. This lowers injuries and keeps workers away from harmful fumes.
- These robots cut very precisely, making better parts and wasting less material. This helps save money.
- Using plasma cutting robots makes work faster. Factories can run all the time and finish jobs quicker than people can.
- Adding plasma cutting robots needs good planning. You must check what is needed, pick the right systems, and keep the workspace safe.
- In the future, plasma cutting will use smarter AI, save more energy, and have helpful robots working with people. This will make factories greener.
Benefits of Plasma Cutting Robots
Improved safety and fewer workplace dangers
Plasma cutting robots make workplaces much safer. They handle hot plasma arcs and sharp materials, keeping workers safe from injuries. Automating risky jobs creates a safer place for your team. These robots also reduce exposure to harmful fumes and sparks during cutting. With fewer accidents, your workplace runs better and follows safety rules.
Robots with predictive maintenance systems stop equipment from breaking dangerously. Using these technologies protects workers and keeps operations smooth.
Better cutting accuracy and quality
Plasma cutting robots are great at making precise cuts. Their smart sensors and CNC systems ensure accurate cuts, even on tricky designs. This accuracy improves part quality and reduces the need for fixes. These robots deliver consistent results on thin or thick metals.
Robotics with plasma cutting also uses materials more efficiently. By planning cutting paths well, waste is reduced, and cuts are cleaner. This improves quality and lowers costs from wasted materials. Plasma cutting robots help meet high standards while staying efficient.
Higher efficiency and lower costs
Plasma cutting robots make work faster and easier. They work nonstop without breaks, finishing tasks quicker than people. Companies using them see better efficiency and profits. For example:
- Automated cutting lowers scrap by 30%, saving material costs.
- CNC programming speeds up jobs and copies designs accurately.
- Smart cutting paths use materials better and reduce waste.
Robots also cut costs in many ways:
- Fewer workers needed, lowering labor costs.
- Less downtime with predictive maintenance and quick repairs.
- Longer equipment life with regular automated care.
- Lower costs for parts due to advanced systems.
Using plasma cutting robots pays off quickly. While setup costs may seem high, long-term savings from better productivity and lower expenses make it worth it.
Easier workflows with automation
Automation has changed how factories work. Adding plasma cutting robots removes delays and keeps tasks running smoothly. These robots never stop, finishing jobs on time with great accuracy. This steady performance improves both speed and product quality.
A big benefit of automation is less manual work. Plasma cutting robots handle repeated tasks easily, letting workers focus on harder jobs. For example, instead of measuring and cutting by hand, robots follow programmed steps perfectly. This lowers mistakes and ensures every cut is correct.
Automation also helps use resources better. With plasma cutting robots, tasks are planned well, making machines work their best. For instance:
- Robots work all day and night, increasing productivity.
- Automated systems handle urgent jobs without slowing others.
- Smart sensors check robot health, preventing breakdowns.
Another advantage is flexibility. Plasma cutting robots can cut many materials and designs. Whether it’s thin metal or thick steel, they deliver exact results. This lets you take on different projects without losing quality.
Automation also makes it easy to add new tools. As robotics and plasma cutting improve, you can upgrade systems to stay competitive. This keeps your factory modern and efficient as technology changes.
Using plasma cutting robots not only simplifies tasks but also sparks new ideas. By automating simple jobs, you can try new methods and improve old ones. This helps your business lead in precision manufacturing.
Tip: Start small with automation. Focus on one task, like plasma cutting, and expand as you see success. This step-by-step method avoids problems and makes the change easier.
With automation, factories run better. Plasma cutting robots bring accuracy, quality, and speed that manual work can’t match.
Types of Robotics and Plasma Cutting Systems
Overview of plasma cutting robots and their capabilities
Plasma cutting robots have changed how metalwork is done. These robots cut metals quickly and precisely, making them great for industries needing top results. They use fast, heated gas to cut materials cleanly. Whether it’s thin sheets or thick plates, these robots adjust to your tasks.
For materials less than 2.75 inches thick, plasma cutting is better than older methods like oxy-fuel cutting. It works best on metals thinner than 1 inch, giving smooth edges and less extra work. While oxy-fuel can cut thicker materials with many torches, plasma cutting robots are best for accuracy and speed.
Note: Plasma cutting robots are great for making tricky shapes, like curves or angles, that are hard to do by hand.
Key features of autonomous plasma cutting technology
Autonomous plasma cutting systems have smart tools that make work easier. These systems mix robotics with advanced tech to give steady results. They cut both thin and thick metals, making them useful for many jobs. They also create detailed designs with smoother finishes, unlike manual cutting.
But, like all machines, they need proper setup to avoid problems like rough edges or bad cuts. Sometimes, extra surface work is needed to meet strict rules. Even with these challenges, their fast speed and flexibility make them a big improvement for factories.
Compatibility and integration considerations
When adding plasma cutting robots to your work, check if they fit with your current tools. They work best with CNC programming, which helps guide their cutting paths. You’ll also need a safe workspace with good airflow to handle cutting fumes.
Think about the materials you use. Plasma cutting robots are great for metals of different thicknesses but work best on materials under 2.75 inches. For thicker plates, you might need other tools, like oxy-fuel cutting. By matching these robots to your needs, you can get the most out of them and improve your workflow.
How to Integrate a Plasma Cutting Robot
Assessing manufacturing needs and objectives
Before adding a plasma cutting robot, think about your goals. Decide what tasks you need the robot to do. Do you want better cutting accuracy, less waste, or faster production? Knowing your goals helps match the robot to your needs.
Look at how your work is done now. Find slow spots or problems a robot can fix. For example, if cutting tricky shapes is hard, a robot can help. Also, think about the materials you use most. Plasma cutting robots are great for metals under 2.75 inches thick. This makes them perfect for industries like cars and construction.
Tip: Car makers using aluminum machines save 40% on chassis costs. This shows how robots can save money in factories.
— Riccardo Ferrario, General Manager, IDRA Group
Check your budget and timeline too. The starting cost might seem high, but robots save money over time. They cut labor, material, and repair costs. Knowing your limits and goals will help you make smart choices.
Choosing the right robotic and plasma cutting systems
Pick a robot that fits your needs. Focus on how well it works, how flexible it is, and if it matches your tools. If you often change part shapes, choose a robot that programs quickly. This saves time and effort.
Challenges | Solutions |
---|---|
Parts get stuck in the trim press | Small tool changes let robots trim any part |
Hard to switch between part shapes | Robots quickly program for new shapes and designs |
Tight rules cause scrap parts | Robots keep a safe distance to avoid crashes |
Choose features that save time and reduce mistakes. For example:
- Quick part changes mean less waiting.
- More space between tools and parts makes programming easier.
- Smart tools with data stop operator errors.
Note: Robots are great for cutting detailed shapes that are hard by hand.
Make sure the robot works with your current CNC tools and software. This makes programming easier and keeps things running smoothly. Also, pick a robot that can upgrade later. A flexible robot keeps your factory ready for new tech.
Preparing the workspace for seamless integration
A safe workspace is key for using a plasma cutting robot. First, make sure the area is safe. Plasma cutting makes noise, fumes, and sparks that can be dangerous. Add good ventilation to handle fumes. Give workers safety gear like goggles and gloves to protect them.
Safety Concern | Description |
---|---|
Noise | Loud sounds can hurt hearing; keep levels below 85 dB. |
Fumes and gases | Dangerous to breathe; use vents to clear the air. |
Light and sparks | Bright light and sparks can harm eyes and skin; wear safety gear. |
Next, set up the space for the robot’s size and movement. Remove anything that could block its path. Mark areas for the robot and workers to avoid accidents. Make sure the floor can hold the robot’s weight and vibrations.
Lastly, prepare for power and data needs. Robots need steady power and good connections to CNC systems. Test these before starting to avoid problems. A clean and safe workspace helps the robot work well.
Installation, programming, and calibration
Setting up a plasma cutting robot needs careful planning. First, read the manufacturer’s instructions for proper setup. Place the robot in a safe and suitable workspace. Secure its base so it doesn’t move while working. Connect it to power and the CNC system, making sure cables are correct. This helps the robot work smoothly with your software.
Programming the robot means creating cutting paths for your tasks. Use CNC software to design these paths with exact sizes and angles. Test the program on a small piece to check accuracy. Change settings to improve speed and precision. For tricky designs, split the job into smaller parts to avoid mistakes.
Calibration keeps the robot cutting accurately. Start by lining up the plasma torch with the cutting table. Use tools to measure the space between the torch and material. Adjust settings for clean, even cuts. Regular calibration stops wear from hurting performance. Check the robot often to keep it working well.
Tip: Keep the workspace clear when setting up the robot. This avoids accidents and lets the robot move easily.
Testing, quality assurance, and operator training
Testing makes sure the plasma cutting robot works correctly. Begin by doing test cuts on different materials. Check the cuts for smooth edges, accuracy, and consistency. If there are problems, fix the program or recalibrate the robot. Write down test results to track progress.
Quality checks are important for good results. Look at finished pieces for rough edges or missed cuts. Use tools to confirm the size matches the design. Make a checklist to make inspections faster. Fix any problems quickly to keep quality high.
Training operators is key to using the robot well. Teach your team how to program, calibrate, and fix issues. Let them practice with the robot to learn its features. Share safety tips for handling plasma arcs and fumes. Encourage them to report problems early to avoid delays.
Note: A trained team spots issues fast, saving time and boosting efficiency.
Industry Applications of Plasma Cutting Robots
Automotive: Accurate cutting for car parts
Plasma cutting robots are changing how cars are made. They cut car parts with great accuracy, making sure everything fits well. This reduces mistakes during assembly and improves car quality. These robots can also create detailed shapes needed for modern vehicles.
The car industry is using plasma cutting robots more than ever. This is because factories want faster and more precise ways to make parts. New technologies like AI have made these robots even better, making them essential for car production.
Metric | Value |
---|---|
Current Market Revenue | USD 2.1 Billion (2024) |
Projected Market Revenue | USD 4.5 Billion (2033) |
CAGR (2026-2033) | 9.5% |
Fastest Growing Application | Automotive |
Did you know? Plasma cutting robots can save 30% of materials, helping the environment and cutting costs.
Aerospace: Precise cuts for special materials
In aerospace, every part must be perfect. Plasma cutting robots make clean cuts without damaging materials like titanium or aluminum. These materials are often used in planes. The robots can switch tasks quickly, which helps factories work faster.
Metric | Description |
---|---|
Precision | Makes clean cuts with little heat damage. |
Efficiency | Quickly switches between tasks to save time. |
Versatility | Handles cutting and welding in one cycle. |
These robots can cut many materials with speed and accuracy. This makes them a top choice for aerospace companies that need high-quality parts while saving time.
Construction: Fast and accurate metal cutting
Construction projects use plasma cutting robots to cut large metal pieces. These robots make exact cuts for building frames, meeting strict safety rules. They work nonstop, speeding up projects and lowering labor costs.
Performance Metric | Rating |
---|---|
Cutting Precision | ★★★☆☆ |
Versatility | ★★★★☆ |
Cutting Speed | ★★★★★ |
Plasma cutting robots are flexible for construction needs. They can cut thick steel beams or detailed designs. Adding these robots to construction saves time and allows for creative designs.
Tip: Using plasma cutting robots can lower costs and keep quality high.
Other industries: Custom and creative uses
Plasma cutting robots are changing industries with their flexibility and accuracy. Outside of automotive, aerospace, and construction, these robots are used in unique and creative ways.
1. Shipbuilding and Marine Industry
In shipbuilding, plasma cutting robots cut large metal sheets for ships. They make precise cuts for hulls and decks, ensuring safety and strength. These robots also speed up repairs by quickly making replacement parts.
2. Art and Sculpture
Artists use plasma cutting robots to create detailed metal designs. These robots help make complex patterns with great precision. From big public sculptures to small art pieces, they allow artists to explore new ideas.
3. Renewable Energy Sector
The renewable energy industry uses plasma cutting robots for wind turbines and solar panels. These robots ensure parts fit perfectly, improving energy use. Automating production helps meet the rising demand for green energy.
4. Metal Fabrication Industry
Plasma cutting robots are very useful in metal fabrication. They handle custom jobs like cutting special shapes for buildings or small batches of parts. Their ability to adapt makes them essential for staying competitive.
Tip: Think about how plasma cutting robots can solve your industry’s problems. Their flexibility offers endless opportunities.
Plasma cutting robots go beyond regular manufacturing. Their ability to meet different needs makes them valuable in many industries.
Future Trends in Autonomous Plasma Cutting Technology
AI-driven advancements in robotics and plasma cutting
Artificial intelligence (AI) is changing how robots and plasma cutters work. AI helps robots make smarter choices while cutting. This leads to better accuracy and fewer mistakes. For example, AI plans cutting paths to save materials and energy. Robots can also adjust to different materials automatically, making work faster and easier.
AI also helps prevent breakdowns. It watches over plasma cutters and warns about problems early. This avoids delays and lowers repair costs. As AI improves, robots will handle harder tasks with less help from people.
Emerging materials and cutting techniques
New materials are pushing plasma cutting to new levels. Modern systems now cut strong alloys and advanced composites. This makes them useful for industries like aerospace and cars. Cleaner energy sources are also being used, which helps the environment.
New methods, like IoT-enabled systems, are improving factories. These systems track machines in real time and predict maintenance needs. Plasma cutters now waste less material and use less power per cut. These eco-friendly changes support the need for greener manufacturing.
- Plasma cutters use cleaner energy, helping the environment.
- IoT systems track machines and predict repairs.
- Better materials make plasma cutters more flexible for different jobs.
Adoption of collaborative robots (cobots) in manufacturing
Collaborative robots, or cobots, are changing factories. Cobots work with people to make jobs safer and faster. They are easier to program and cost less than regular robots, making them great for small businesses.
Cobots are growing fast, with a 22.8% yearly growth expected over 20 years. In car factories, cobots are great for welding and putting parts together. They save time and money, making them a smart choice for modern factories.
- Cobots are simple to program and cost less than regular robots.
- They help with jobs like welding and assembly.
- Cobots are expected to grow quickly in the next two decades.
Sustainability and energy-efficient plasma cutting solutions
Sustainability is now very important in manufacturing. Plasma cutting robots help by saving energy and reducing waste. Adding robots to your work makes operations cleaner and saves resources.
Energy-saving plasma cutters use smart technology to lower power use. They change energy levels based on material thickness. For example, thin metals need less power, and the system adjusts. This cuts electricity costs and reduces your carbon footprint.
Robots with smart sensors make cutting more accurate. They follow paths carefully and waste less material. This precision helps use every piece of metal well. These robots can also cut recycled metals, making production eco-friendly.
Another benefit is fewer harmful fumes. Old cutting methods release toxic gases. New plasma cutters have vents that trap and clean these fumes. This keeps workers safe and meets environmental rules.
Sustainability also means longer-lasting tools. Robots with maintenance features find problems early. Fixing issues quickly avoids big repairs and tool replacements. This saves money and lowers the need for new equipment.
Using energy-saving plasma cutters helps the planet. These tools let you work efficiently while caring for the environment. Your business stays strong and supports global green goals.
Using robots with plasma cutting technology makes manufacturing safer and faster. These systems, guided by CNC tech, cut materials accurately every time. They help factories work better, waste less, and meet high-quality goals.
To use this technology well, follow a clear plan. First, figure out what your factory needs. Then, choose the right tools and set up your workspace. This step-by-step process makes adding robots easier and more effective.
By 2025, factories will change a lot. New trends like saving energy, using eco-friendly methods, and more automation will lead the way. Robotic plasma cutters will be key, helping factories save money, work faster, and stay safe.
- Main benefits of using robotic plasma cutting technology:
- Robots make exact cuts with smart control systems.
- They boost production to meet growing factory needs.
Trend Type | Details |
---|---|
Tech Improvements | Using energy-saving tools and smarter ways to make things. |
Green Practices | Focus on recycling and using materials that break down safely. |
More Automation | Factories in places like North America and Asia need more robots. |
Better Efficiency and Safety | Robots cut costs, improve safety, and make work faster. |
Getting ready for these changes now will help your factory succeed. Adding robots and plasma cutting tools will keep your business strong as manufacturing evolves.