1. Product Overview
The programming-free remote control teaching painting system is a new generation of teaching technology developed by our company for spraying small batches, multiple varieties, and complex special-shaped parts. The emergence of this technology allows ordinary workers to spray once with the teaching handle, and the robot can record and reproduce the spraying trajectory 1:1. Since there is no inertia and resistance, the robot can fully reproduce the workers’ spraying skills and techniques, ensuring that every product produced is made by a master.
Different from the traditional teaching pendant programming method, the programming-free remote teaching technology does not require code editing. The teaching process is no different from the workers’ normal spraying process. Ordinary workers can easily get started after simple training, which greatly reduces the threshold of teaching. At the same time, the teaching process and the manual spraying process are combined into one, and the programming efficiency is nearly 100 times higher, which significantly reduces the time and cost of integrators programming and debugging at the customer site.
Different from drag-and-drop teaching, the biggest advantage of programming-free remote control teaching technology is that there is no inertia and resistance. The teaching process is no different from the workers’ usual spraying process. The workers can freely play with the teaching handle and fully integrate their spraying experience and skills.
The robot’s reproduction trajectory is integrated into the robot’s reproduction trajectory to ensure that every product produced is made by a master; secondly, the programming-free remote control teaching technology adopts a human-machine separation operation mode, and there is no physical contact between the operator and the robot, so safety is fully guaranteed; in addition, the programming-free remote control teaching technology adopts a common industrial robot body, and uses harmonic reducers and RV reducer transmissions. There are no gears, chains, cylinders and other transmission mechanisms, so that each reproduction trajectory remains highly consistent, and the reproduction accuracy is guaranteed to ensure the consistency of product quality.
Table 1 Comparison of various teaching methods
Serial number | Teaching pendant programming | Drag and drop teaching | Programming-free remote control teaching |
Principle | Point-to-point code editing track | Manually dragging the robot end to demonstrate the trajectory | Holding the teaching handle to demonstrate the trajectory |
Difficulty of operation | Requires multiple professional technicians to operate | Ordinary workers can operate | |
Programming efficiency | Low | High | |
Advantage | Traditional, stable | Low operating threshold; fast trajectory generation and short component replacement time | |
1. Flexible, no inertia and resistance, suitable for complex and special-shaped parts; 2. Human-machine separation, inherently safe; 3. High trajectory reproduction accuracy and strong consistency ; | |||
Disadvantages | The development cycle is long and not suitable for small batch and multi-variety scenarios | 1. There is inertia and resistance, it is not flexible, and it is difficult to handle special-shaped parts; 2. Human and machine are mixed, and there are safety hazards; 3. The trajectory reproduction accuracy is low and the consistency is poor; |
2. Technical Parameters
2.1 Teaching range
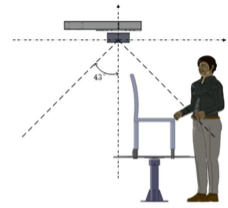
The programming-free remote control teaching system measures and automatically records the operator’s teaching trajectory through the cooperation of the teaching box and the teaching handle. The teaching range is mainly determined by the teaching box. The teaching box can be installed in two ways: upside down installation and horizontal installation. Figure 1 shows a schematic diagram of the teaching range when the teaching box is installed upside down.
It should be noted that the effective teaching range of the teaching box only represents the area that the teaching system can accurately detect. The trajectory taught within the effective teaching range of the teaching box does not necessarily mean that it can be reproduced on the robot body, because the robot body is restricted by various physical factors such as arm length, joint angle, angular velocity, angular acceleration, etc., and may not meet the requirements for teaching trajectory reproduction. Therefore, in order to give full play to the performance of this system, it is necessary for the operator to have a certain degree of understanding and mastery of the characteristics and indicators of the robot body.
2.2 Teaching accuracy
The teaching accuracy is related to factors such as the processing and assembly accuracy of parts. At the same time, the teaching accuracy near the vertical axis of the teaching box is relatively high. After actual measurement, when the teaching handle is located in the core area of the teaching range, the displacement accuracy in the teaching trajectory is about 2~5m; when the handle is located at the edge of the teaching range, the displacement accuracy is about 10m. The speed during teaching will also affect the teaching accuracy. The accuracy is higher in static or low speed, and the accuracy will be reduced to a certain extent in the dynamic process due to the existence of following errors.
Table 2 Technical parameters of programming-free remote control teaching system
Serial number | Content | Parameter | Remark | |
1 | Number of supported axes | 1. Tandem axes: The system supports up to 7 tandem axes as standard ; 2. Additional axes such as turntables and guide rails support up to 12 axes; | If you need to support more axes, please contact our sales personnel | |
2 | Displacement | Static accuracy | About 2~5mm | |
Dynamic accuracy | Related to the specific situation | |||
Teaching range | Manual operation range | |||
3 | attitude | Accuracy | Within 1° | For higher requirements, please use customized version |
Range | ±60° | |||
4 | Communication Interface | Use EtherCAT to communicate with the servo drive; RJ45 port; | ||
Communication with PLC and other host computers supports TCP/IP; RJ45 port; | For other communication protocols, please contact our sales personnel | |||
5 | Supported Hardware | Support EtherCAT type servo drive | Recommended servo drive model | |
6 | size | Teaching box | L250mm*W200mm*H120mm | |
Teaching handle | L220mm*W60mm*H200mm | |||
Industrial Computer | L155mm*W58mm*H240mm | |||
IO Module | L200mm*W90mm*H45mm | |||
7 | weight | Teaching box | 8.5kg | |
Teaching handle | 300g (without spray gun and fixture) | |||
8 | powered by | DC24V | ||
9 | Operating temperature | -10℃~+75℃ | It is recommended to teach in an environment of +10℃~+55℃ |
*Please note: Due to product differences, there may be some errors in parameter measurement!
The programming-free remote control teaching system currently has two versions: stand-alone version and assembly line version. The stand-alone version is mainly used in situations where there is no line body, and can be used in conjunction with a rotating turntable to complete the spraying action; the assembly line version is mainly used in assembly line spraying scenes, and can be used in conjunction with hanging lines, ground rails and other moving lines to achieve the spraying process.
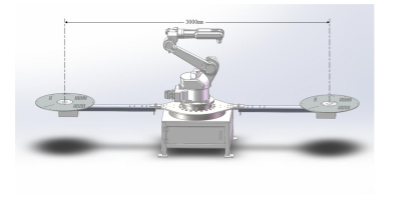
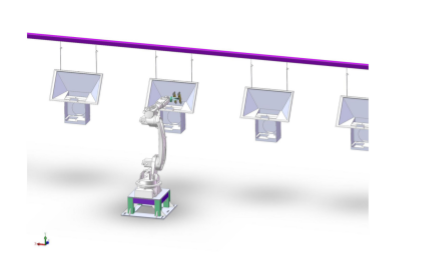
3. Product List
The core components of the programming-free remote control teaching system provided by our company include industrial computers, teaching boxes, teaching handles, and I0 modules.
As shown below.
Figure 4 Core components of the programming-free remote control teaching system
Table 3 Parameters of standard core components
Serial number | Content | Parameter | Quantity | Remark |
1 | Industrial Computer | i3 processor; 8G DDR4 memory; 128G solid state drive; built-in robot control system software; | 1 piece | |
2 | Teaching handle | Size: L220mm*W60mm*H200mm | 1 piece | No spray gun fixture included |
3 | Teaching box | Size: L250mm*W200mm*H120mm | 1 piece | |
4 | IO Module | Guide rail installation, EtherCAT bus interface; NPN type, 16DI+16D0; | 2 pieces |
Serial number | Project | Parameter | Quantity | Remark |
1 | Encoder | Photoelectric encoder, 5V power supply, differential output; line number: recommended 1000p/r | 1 piece | Pipeline version use |
2 | Encoder mounting bracket | Install with encoder | 1 set | |
3 | Photoelectric sensor switch | 24V power supply, through-beam type, NPN output | 1 piece | |
4 | Turntable | custom made | Standalone version | |
5 | Electronic handwheel | Pulse generator, used to detect whether the teaching trajectory interferes | 1 piece | |
6 | Spray gun fixture | Matches with the teach handle and clamps the spray gun at the same time | 1 piece | Need to be customized according to the spray gun |