In this article we’d like to introduce the robotic machine tending(loading and unloading, pick and place, parts handling, etc). Robots can tend injection molding machine,cnc lathe, punching/stamping machine, die casting, cylindrical grinding machine, hot forging machine, etc.
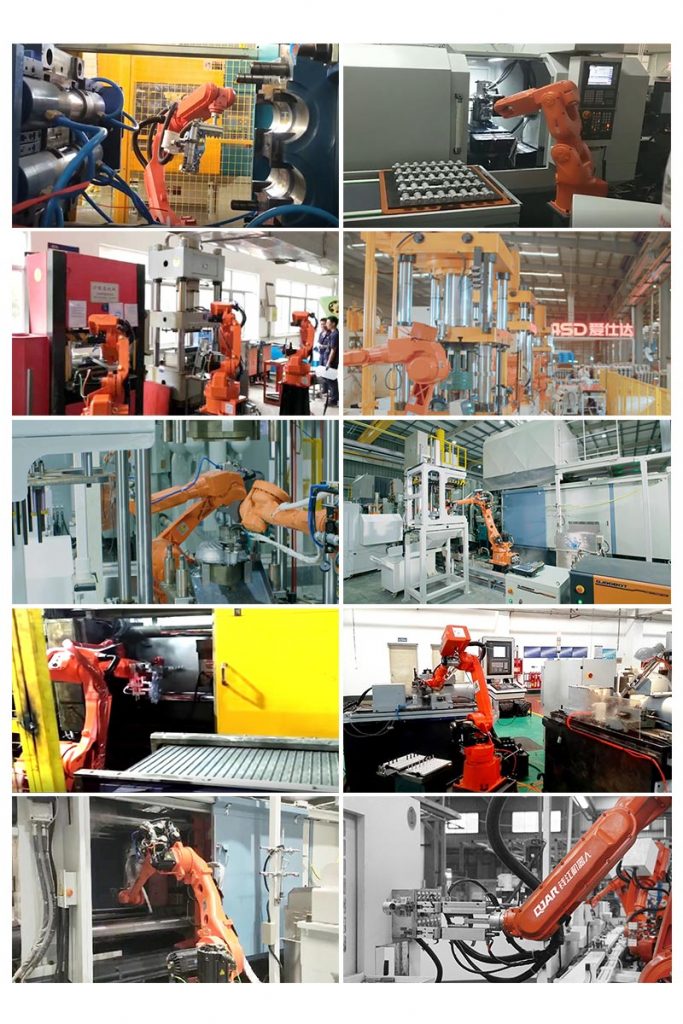
So what is machine tending and why would we use industrial robots to tend the various machines?
According to IFR(international federation of robotics), machine tending is defined as overseeing a machine while it performs a job, as well as the process of feeding parts in and out. The traditional tending processes were mostly done by human. The tasks are always tedious, dangerous, and require a high level of repetitive consistency, also the factory is often lack of qualified workers. So robots are more competent to do these kinds of job because the robots have advantages as below:
1. increased productivity
2. decreased manufacturing labor
3. decreased overall costs
4. improved quality
5. enhanced safety
6. operational flexibility
7. inventory optimization
This is a machine world today, we use different kinds of machines for manufacturing. Where there is machine, there is machine tending. According to IFR, the machine tending robots installed in 2017 already reached 178,000 units and it is going to grow at a very fast speed.
In summary, robotic machine tending often comes with injection molding machine, CNC lathe, punching/stamping machine, die casting machine, cylindrical grinding machine, hot forging machine, etc. Let’s take a look at some examples:
1. Injection Molding Machine Tending
Production line introduction: There are 8 units of QJR10-1 in this manufacturing line, they can help with working piece feeding, picking the finished working piece from the injection molding machine and cutting the sprue gate, etc. Robot used: QJR10-1, 6 axis, 10kg payload, repeat positioning accuracy ± 0.05mm, 1671mm arm span
Project highlight: This manufacturing line realized the flexible production of different products, meaning the QJAR robots can deal with multiple model’s downspouts in a single production line. QJAR robots replaced the labor force and realized the fully automatic production of the whole production line. QJAR robots massively improved the working efficiency, only one person is on duty, the robots and injection molding machine can working a long period of time without interruption.
2. Machine Tool Loading and Unloading
Production line introduction: this project uses 14 sets of QJR6S-1 industrial robots and 2 sets of QJR6-1 industrial robots in 2 production lines, realizes the automatic loading and unloading for piston from the CNC machine tool.
Technical progressiveness of projects: Flexible production, robot can realize automatic loading and unloading for various types of piston from the CNC machine tool without changing fixture. With high repeat accuracy (±0.03mm) and fast speed, QJAR robots completely replaces the manually repetitive work, reduces the labor by at least 20 people and improves the productivity by at least 15%.
3. High-end Cookware Casting Intelligient Line
Production line introduction: QJR50-1A die-casting robot and QJRB20-1 robot are uesd in this production line. It realizes the automatic production of hot casting, deburring, stamping and shaping of cookware. Project technical difficulties and advanced nature: SCADA and MES systems are deployed in the production line, which realize real-time monitoring of aluminum temperature, consumption, remote monitoring of robot and equipment’s movement rate, speed, maintenance, remote update and other functions. The die casting machine is equipped with a smoke and dust removal system to ensure low dust and smoke, and the production environment is safe and environmentally friendly. Cost saving, benefit increasing, robot replacing labor, which not only solves the labor cost pressure brought by the rising labor cost to the enterprise, but also the robot can run continuously for long hours, improving the production efficiency.
4. Sheet Stamping, Cutting, Loading and Unloading
Project features: Qianjiang QJR6-1 universal robot, load 6kg, repetitive positioning accuracy ± 0.03mm, arm span 1441mm. It can be used in welding, spraying, loading and unloading, handling, sorting, cutting and other applications. This project adopts three QJR6-1 six axis robots of Qianjiang to realize the grabbing of sheet metal, loading and unloading of stamping machine, loading and unloading of cutting machine, without manual work in the whole process, saving 3 workers and greatly saving labor cost. According to the set trajectory, the robot can run continuously for 24 hours without fatigue, which is more efficient than manual operation.
5. Inner Pot Stretching Line
Through 9 sets of QJR10-1, 3 sets of digitization hydraulic machines and 5 sets of full-automatic punching machines. This line realised automated plate feeding, greasing, turning and trimming. The robot can realize the process switch of multi-seed program, fast transformation and less manual operation. The robot adopts bus control mode to monitor the operation and fault situation in real time
6. Die Casting Release Agent Spraying and Parts Picking
Robot used: QJR20-2: 6 axis, load 20kg, arm span 1668mm, repeat positioning accuracy ± 0.05mm, protection grade IP67, ExdpxIIBT4Gb.
Project introduction:Qianjiang die-casting robot can realize the rapid picking up of die-casting metal products and spraying of release agent. By matching with the detection sensor, it can carry out on-line slag ladle detection and product integrity detection. The robot can still run stably for a long time in the harsh environment of high temperature and humidity.
Last words: If you are interested to know more or if you are inspired and want to automate your factory, please don’t hesitate to reach out.
Michael from EVS Robotics