Robotic Tunnel Rebar Intelligent Production Line
EVS Welder, with its globally leading industrial auto-mation and intelligent solutions, has successfully designedand manufactured an intelligent production line specificallyfor the production of tunnel rebar. This production lineadheres to automated and intelligent production throughoutthe entire process, from raw material processing to finalwelding.
The entire process is completed by high-precision robots,utilizing advanced industrial robots and intelligent monitor-ing systems. This project has achieved continuous produc-tion 24/7, greatly enhancing production efficiency andcapacity. It also significantly reduces the possibility ofhuman operation errors, effectively reducing the labor inten-sity and safety risks for workers. It has successfully brokenthrough traditional production bottlenecks, achieving trueintelligent manufacturing.
Currently, the Robotic Tunnel Rebar Intelligent ProductionLine has been successfully applied in many Global Top 500enterprises. lt not only helps them maintain competitivenessin the global market but also sets a new benchmark forglobal intelligent manufacturing.
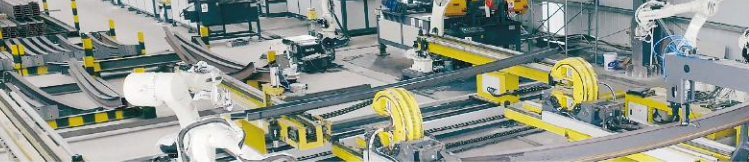
I-Beam Arch Bending Automatic Production Line
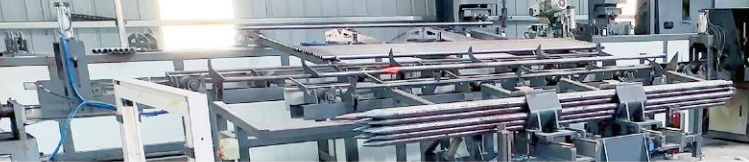
Small Pipe Automatic Production Line
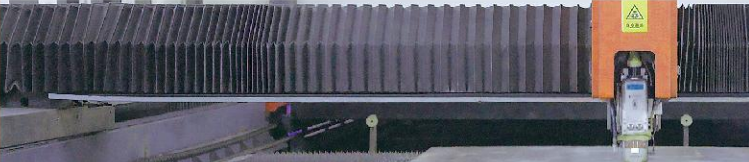
End Plate Cutting Automatic Production Line
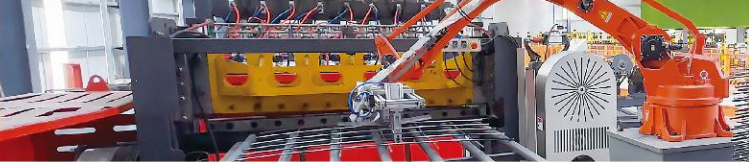
Mesh Panel Automatic Production Line
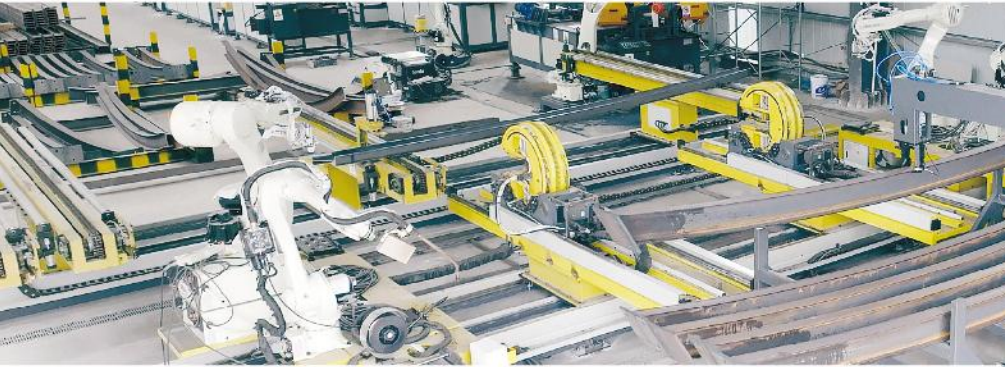
I-Beam Arch Bending Automatic Production Line
Production Process Flowchart
Manual loading of whole bundles onto the material rack.
Automatic loading mechanism loads onto the rollers.
Saw cutting at the end of the material.
Buffering and feeding material to the alignment mechanism.
I-Beam alignment.
Robotic continuous welding.
1.Robotic end plate front welding.
2.Robotic upper end plate placement.
3.Feeding into the C-Type positioning machine.
4.Material unloading by the material feeding and unloading mechanism.
5.Saw cutting to size.
6.Cold bending machine for arching.
7.C-Type positioning machine flipping and positioning.
8.Robotic end plate back welding.
9.C-Type positioning machine flipping for unloading.
10.Automatic unloading by the unloading mechanism.
11.Placing the finished product onto the material rack.
Core Technology Advantages
3D Vision End Plate Assembly Welding System
Robots automatically grasp end plates for efficientassembly and welding.
Spatial 3D seam recognition technology ensuresstable welding quality.
Multi-robot collaborative operation technology.
Multi-variety self-adaptive process, with freeswitching between different sizes and models, andbetween perpendicular and oblique cutting.
Environmental self-adaptation, unaffected byweather, time of day, or seasons.
Intelligent Arch Frame Production Line Technical Features
Fully automatic manufacturing process, includingautomatic material loading, automatic cutting ofheads, automatic jointing,arc control, fixed-lengthcutting, automatic flipping, and automatic stacking.
Industrial network control to achieve multi-machinelinkage and multi-robot collaboration for highefficiency and quality.
Information management with graphical display,making production status clear at a glance andproviding deep insights.
Modular combination with highly reliable design tomeet on-site construction needs.
Five-axis CNC cold bending machine with featuresand advantages such as multi-arc segment formingand one-click type change.
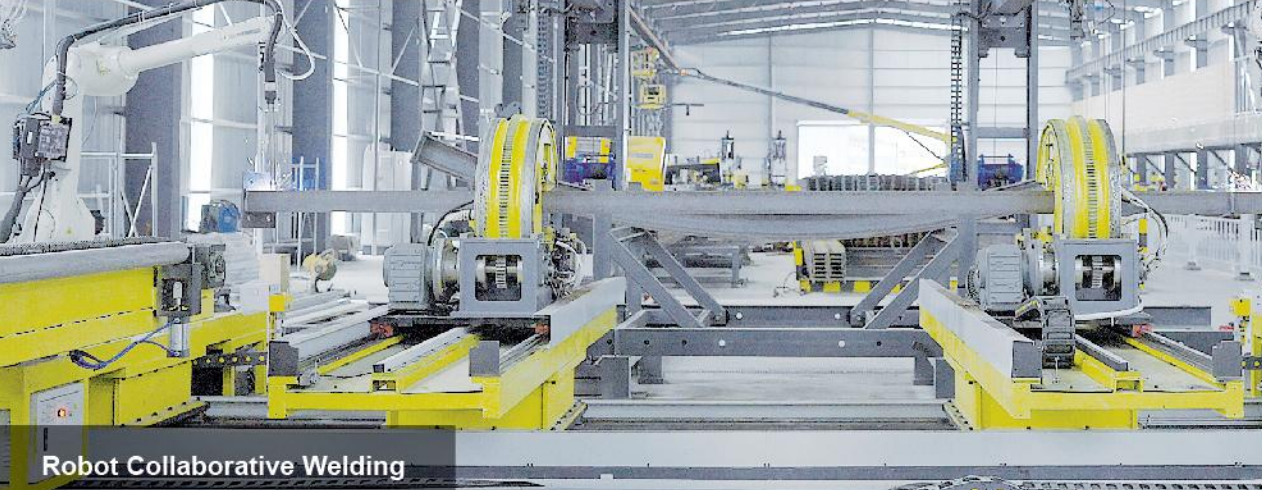
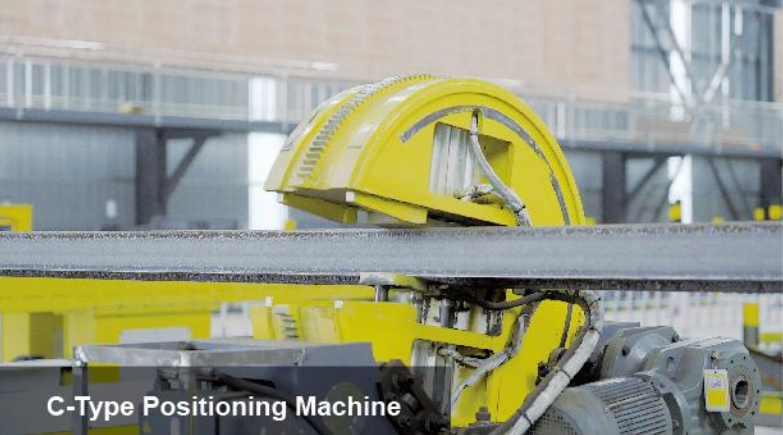
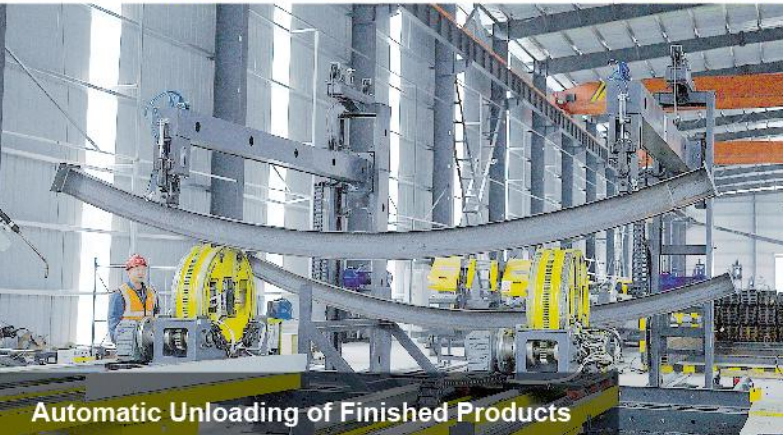
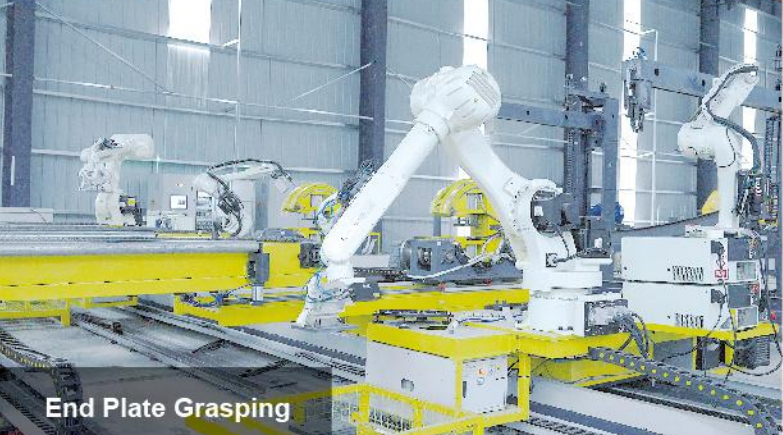
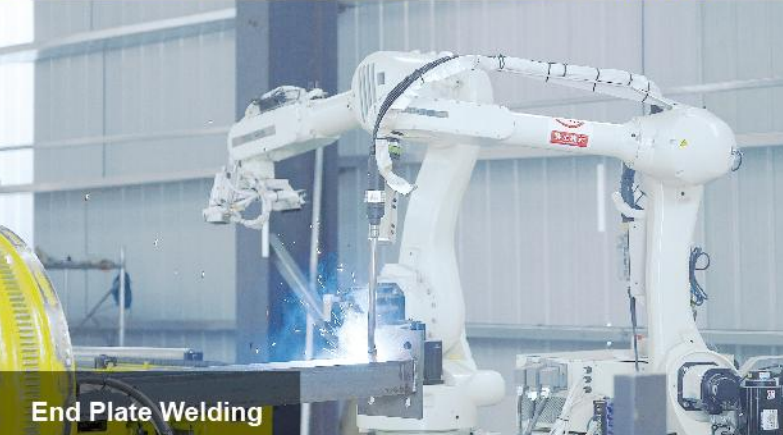
Core Competitiveness
Flexible Production Line Layout Tailored to construction sites, highly adaptable, offering various configurations such as single-line,dual-machine parallel lines, and multi-machine shared lines, to meet a range of production scales and needs.
Economic and Social Benefits: Highly autornated and informational design significantly enhances construction managementstandards, ensures stable quality, and delivers clear comprehensive benefits.
Advanced Technology Application and Competitive Advantage: Deep industry process cultivation, independently developed 3Dvision technology, robot control technology, and unmanned production models, with iterative improvements to maintainindustry-leading status
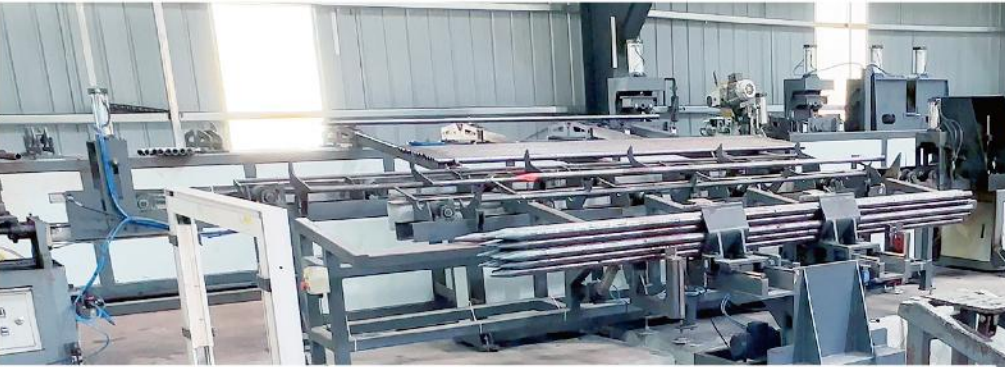
Small Pipe Automatic Production Line
Production Process Flowchart
Manual Material Loading
Automatic Material Separating Mechanism for Separating Materials
Single Piece Enters the Passive Conveyor Line
Feeding by the 1st Clamping and Conveying Mechanism
Alignment and Grouping of Front and Rear Steel Pipes
1.Lifting Cylinder on the Passive Conveyor Line for Material Flipping
2.Feeding by the 3rd Clamping and Conveying Mechanism
3.Fixed-Size Cutting by the Pipe Cutting Machine
4.Flipping from the 1st Bidirectional Line into the 2nd Bidirectional Line
5.Continuous Welding
6.Steel Pipe Enters the 1st Bidirectional Line
7.Enters the Taper Machine for High-Frequency Heating and Taper Shaping
8.Retums to the 1st Bidirectional Line
9.Flipping from the 1st Bidirectional Line into the 2nd Bidirectional Line
10.Enters the Hole Cutting Machine for Hole Cutting
11.Packaging Machine Moves into Position for Packaging
12.Shaping and Clamping Mechanism Moves to the Buffer Mechanism for Receiving and Clamping for Shaping
13.Flipping from the 2nd Bidirectional Line into the Buffer Mechanism with 19 Pieces
14.Returns to the 2nd Bidirectional Line
15.Labeling Machine Applies Labels
16.Shaping and Clamping Mechanism Moves for Material Release
17.Manual Lifting for Unloading Materials
Advantages of the Small Pipe Automated Production Line
- Intelligent: Fully digital control technology eliminates the need for manual intervention, significantly improving efficiency.
- Automated: From material loading to finished product bundling, fully automatic operation with no human participation,
ensuring stable product quality. - Digitalized: Industrial network control with real-time status display for comprehensive monitoring.
- Easy to Operate: Foolproof design with one-touch start, fully automated operation throughout the process.
- Efficiency Improvement: Chain-type production line conveyance is highly efficient and fast, increasing efficiency by over 50%.
- Versatile Adaptability: Quick product model switching to accommodate various steel pipe diameters.
- Plasma Hole Cutting: Utilizes digital plasma power sources in conjunction with CNC clamps for precise hole piercing.
- Automatic Bundling:Automatic counting and bundling without the need for human participation.
- Continuous Innovation: Applied in multiple projects with ongoing improvements and refinements to maintain industry
leadership.
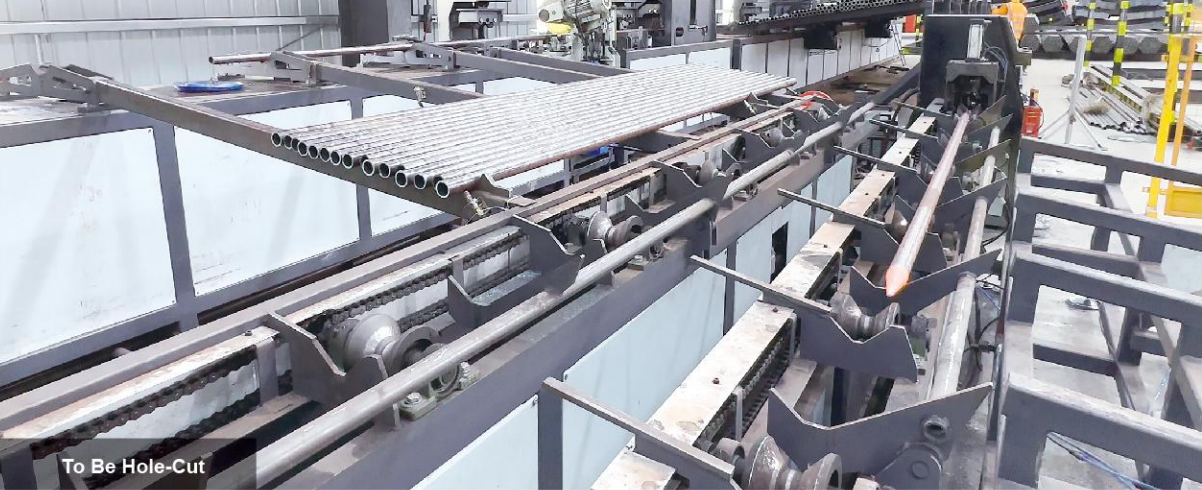
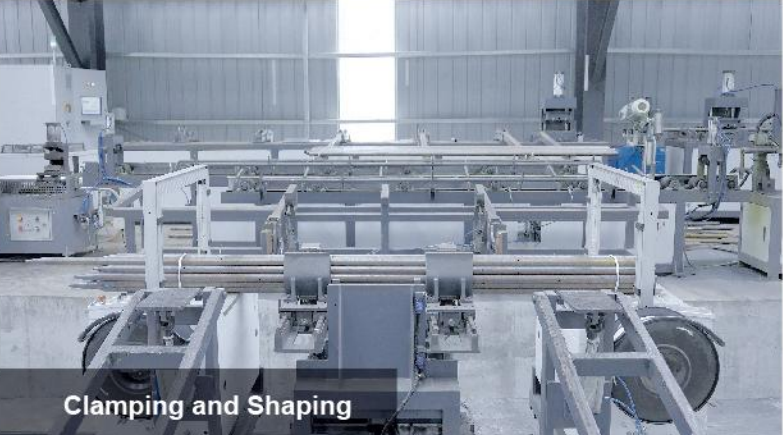
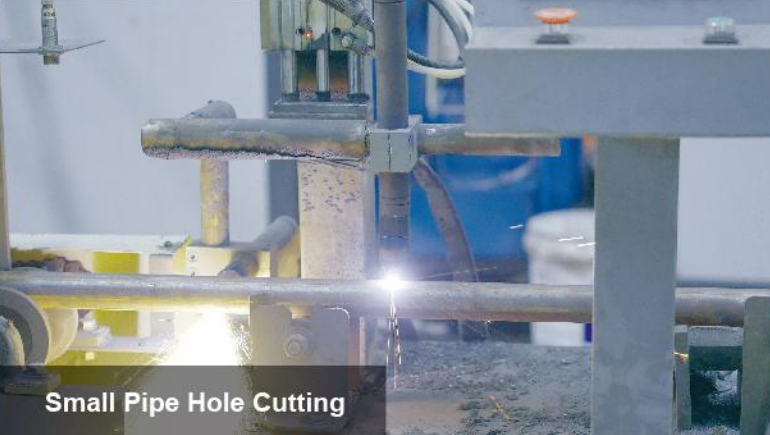
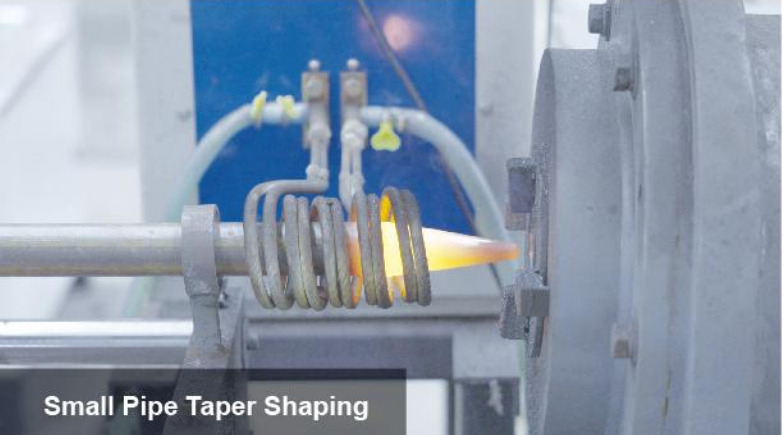
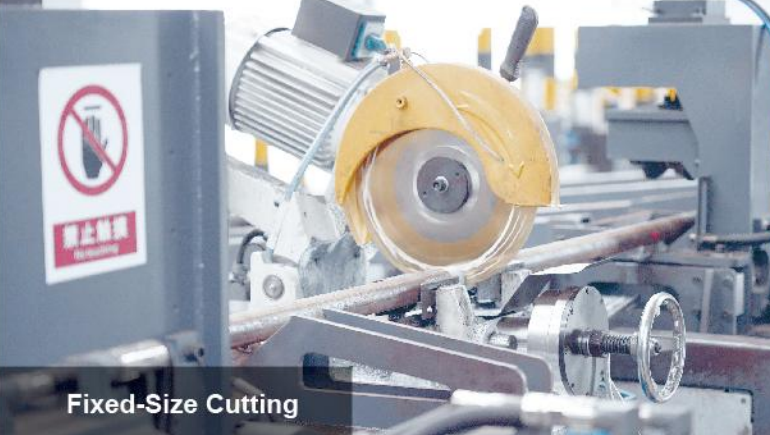
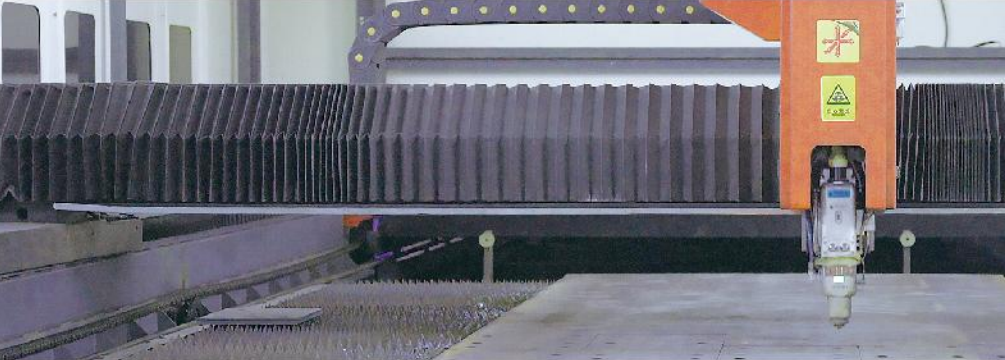
End Plate Cutting Automatic Production Line
Production Process Flowchart
Manual Material Loading
Automatic Material Separating Mechanism for Separating Materials
Single Piece Enters the Passive Conveyor Line
Feeding by the 1st Clamping and Conveying Mechanism
1.Lifting Cylinder on the Passive Conveyor Line for Material Flipping
2.Feeding by the 3rd Clamping and Conveying Mechanism
3.Fixed-Size Cutting by the Pipe Cutting Machine
4.Flipping from the 1st Bidirectional Line into the 2nd Bidirectional Line
Automated Material Offloading
- Utilizing robots with fiber laser power sources toachieve automatic offloading of various end plates;
- 3D vision guidance allows for the absence of precisepositioning and placement of the sheet metal, withthe robot automatically completing workpiececalibration;
- Fully automatic nesting design, mixing and arranginglarge and small plates to maximize the utilization rateof the sheet metal;
- Capable of processing the maximum thickness ofend plates up to 40mm.
Automated Plate Picking
- 3D vision guidance enables the handling robot toautomatically pick up end plates and sort them;
- Adhesion detection between end plates,automatically picking up the next end plate;
- Collaborative operation, with a full box command forAGV to automatically transfer and switch to an emptybox.
Material Management &AGV Distribution
- The system is equipped with a temporary storage forend plates, connected to theERP system for unifiedsupervision of product specifications and models;
- Equipped with fully automatic material transfervehicles (AGVs), which automatically deliver endplates to the designated line and return empty boxesto the warehouse.
Information Management
- Implementing a networked management system, witha graphical interface to intuitively display data andprocesses, ensuring that all key information ispresented in real-time in a clear and intuitive manner,making decisions faster and more accurate, andimproving work efficiency.
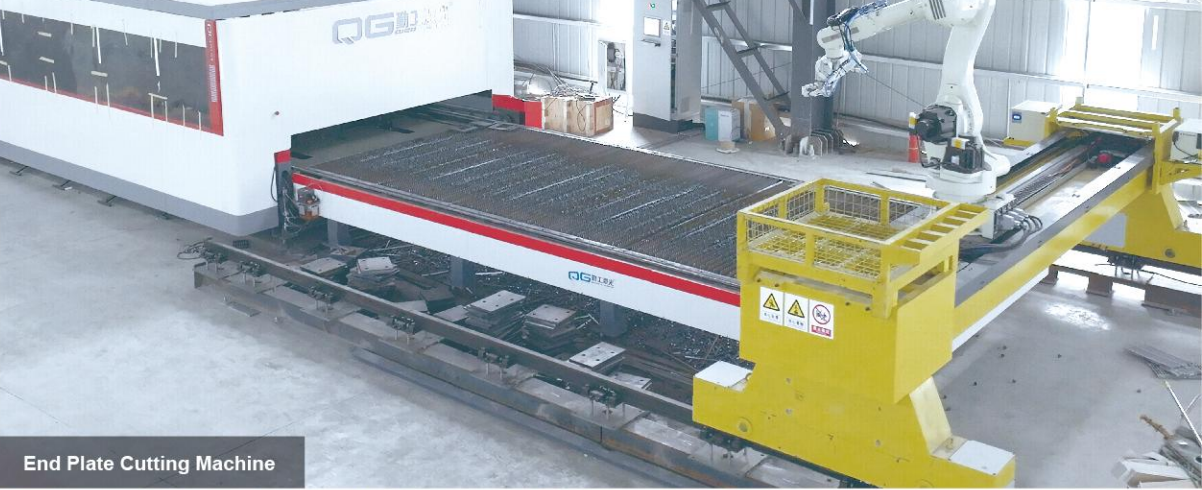

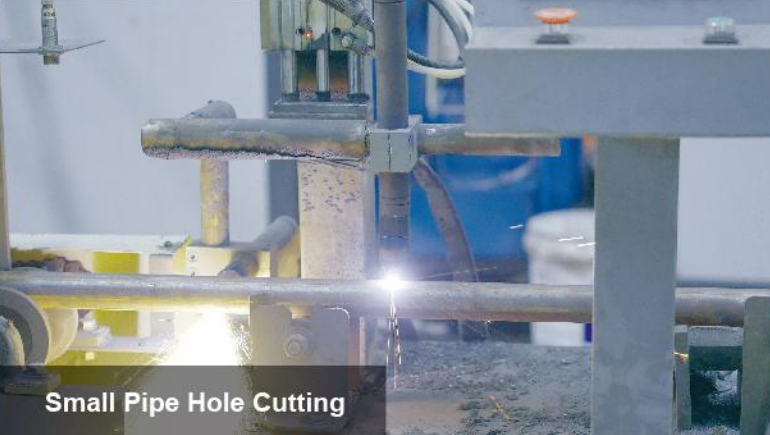
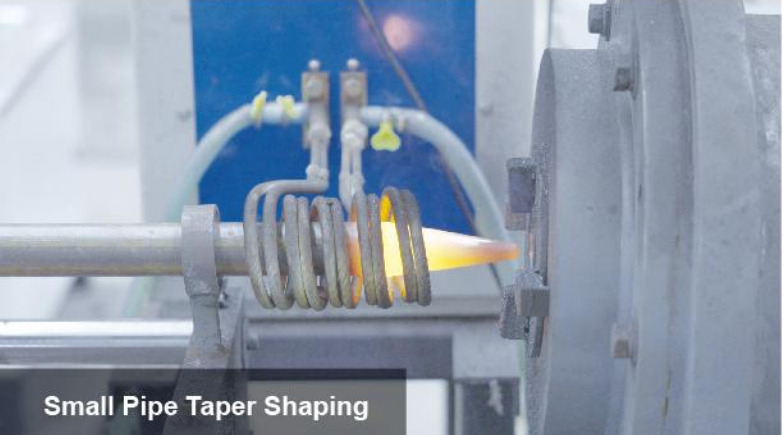
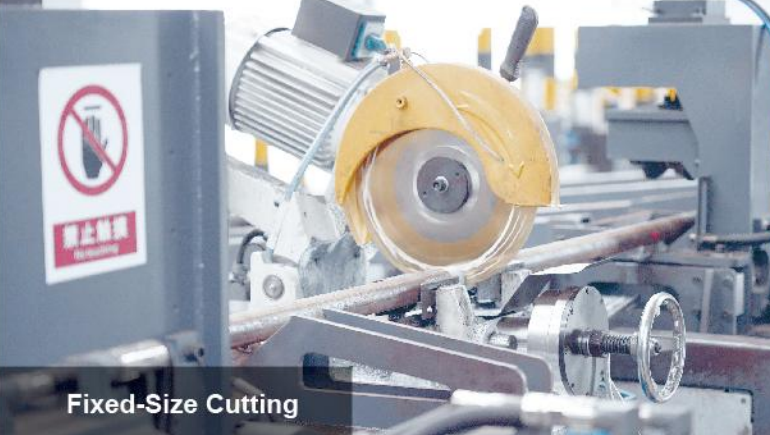
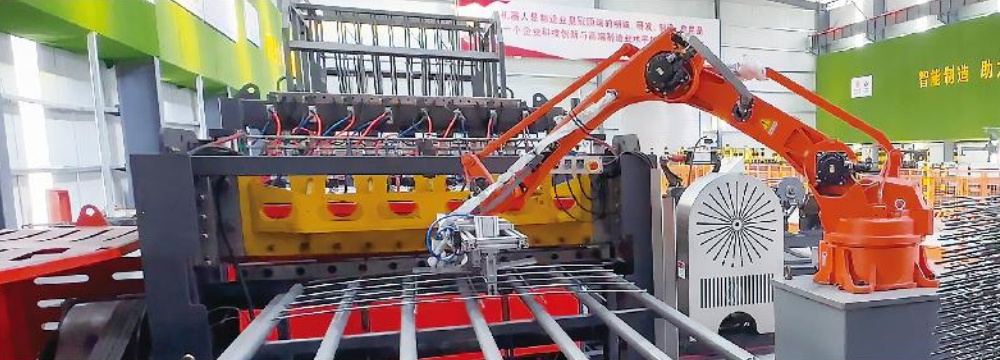
Mesh Panel Automatic Production Line

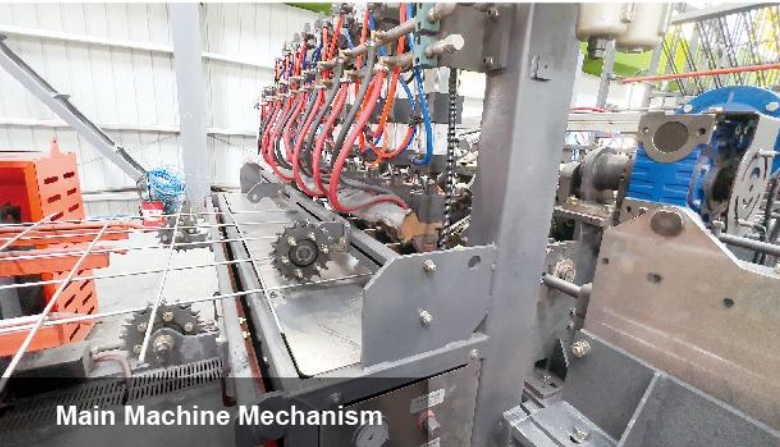
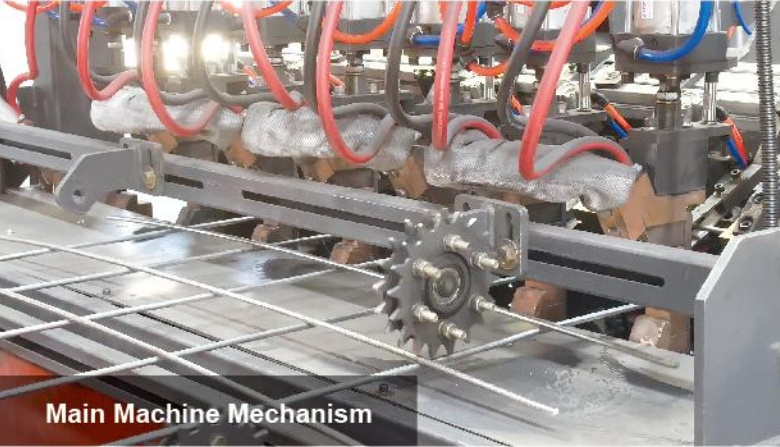
Core Advantages
Fully automatic design, equipped with robotic material picking and stacking operations, significantly enhancing production efficiency.
GLOBAL TOP 500 CASE
Electrical Equipment
Manufacturer’s Robotic
3D Flexible Cutting Innovation
A leading company within the Global Top 500,this electricalequipment manufacturing giant specializes in the R&D,design, manufacturing, and sale of power generation equip-ment. The enterprise adeptly addresses the complex cuttingneeds of various components, including hydro turbine-gener-ating units, steam turbines, wind turbine units, nuclear powerunits, and auxiliary equipment.
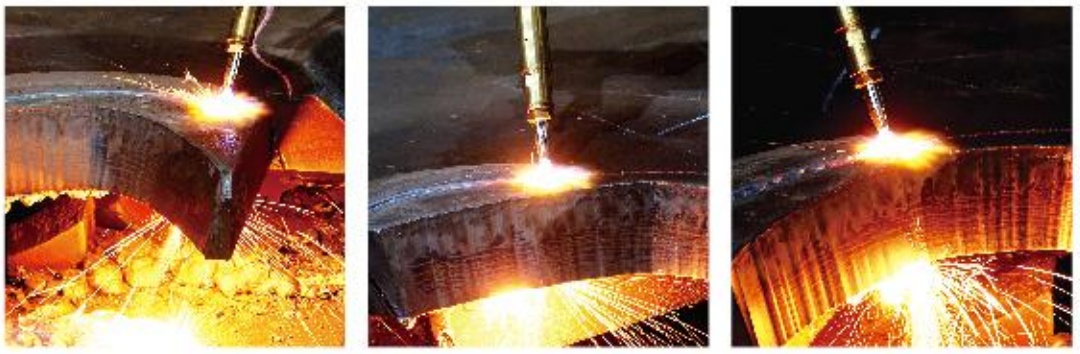

Project Pain Points
- Traditional CNC cutting methods are challenged by spatially complex surfaces, often requiring manualintervention from skilled workers, leading to inefficiencies and inconsistent precision.
- Manual cutting is constrained by the operator’s skill level and susceptible to environmental and emotionalinfluences, heightening the risk of safety incidents.
- Existing cutting technologies fall behind in achieving refined, automated, and intelligent management,hindering further advancements in technical processes.
Project Achievements
The system excels in meeting the cutting requirements for a variety of uniquely-shaped workpieces, includingcircular, fan-shaped structures, conical tanks, and cylinders. This not only enhances cutting efficiency andaccuracy but also significantly reduces labor intensity and operational costs. Moreover, the system incorpo-rates automation and intelligence, fulfilling cutting needs in various scenarios.
Solution Highlights
- Integration of a six-axis robot, known for its high precision, speed, and reliability.
- This robot can flexiblyadjust its posture and cutting paths, effectively handling the cutting of complex-shaped workpieces.
- Development of a dedicated thick-plate flame cutting system that enables digital management of cuttingparameters, characterized by rapid cutting, high efficiency, and low cost.Implementation of a 3D vision system for quick acquisition of the workpiece’s 3D model, removing theneed for original blueprints and enabling full computerization from workpiece identification to robot cuttingtrajectory programming and parameter matching.
- Designing a cross-arm manipulator as an external axis for the robot, which expands the robot’s workingrange, allowing it to perform extensive, continuous cutting of large workpieces.
- Developing an in-house software control system featuring an intuitive interface and an extensive expertprocess library.
- This system integrates control over the robot, flame cutting system, 3D vision system, andelectrical system, achieving a fully automated and intelligent cutting process.
GLOBAL TOP 500 CASE
Heavy Equipment
Manufacturing Enterprise
EVS Welding Workstation
A major company within the Global Top 500 specializing inheavy equipment manufacturing, with products ranging fromlifting equipment, mining equipment, wind power equipment,marine equipment, rail transit, to construction machinery.
Thisenterprise has integrated EVS programming-freerobotic welding stations in their production, significantlyreducing labor intensity and operation difficulty for workers,and enhancing production management efficiency.
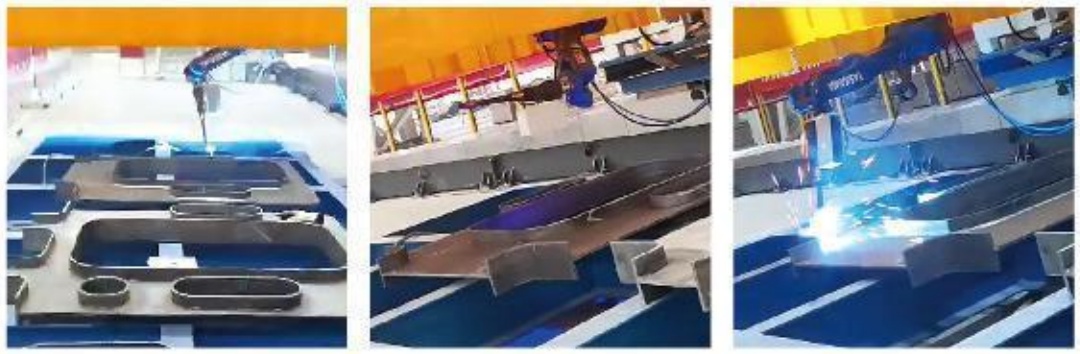
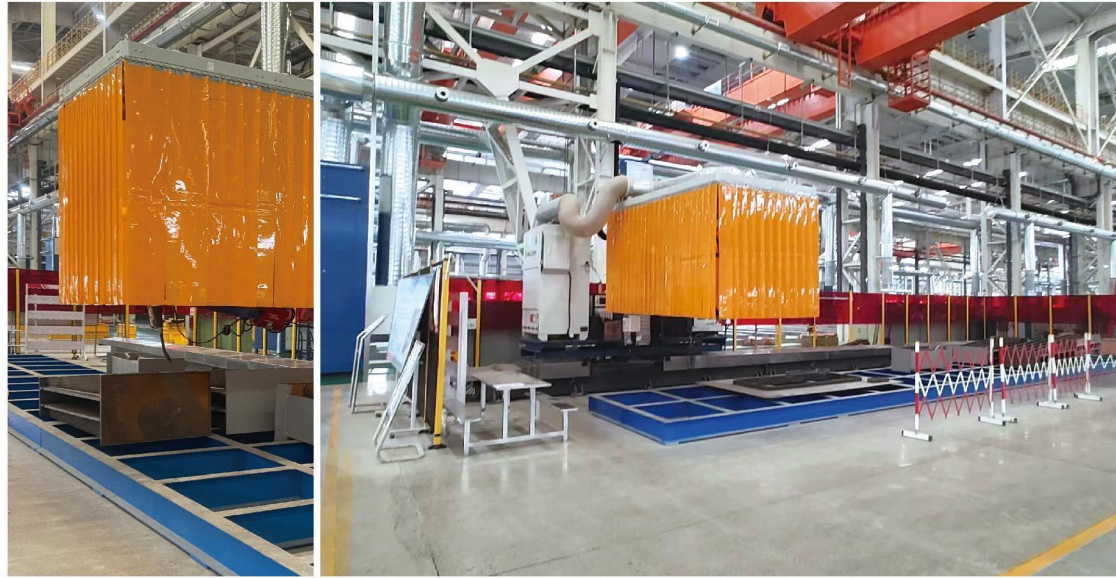
Project Pain Points
- The main beam rebar plate components of cranes are diverse, consisting of rebar plates, reinforcing rings,wire loops, etc.
- Traditional manual welding methods are inefficient, with long production cycles, demand-ing high skill levels from workers, prone to errors, and unable to guarantee consistent welding quality.
- In the client’s existing production process, the welding of rebar plates was manually operated, posingsafety risks and resulting in inconsistent welding quality, thus affecting the product quality.
Project Achievements
- The implementation of the EVS Welding Workstation has realized intelligent production for theproduction line, greatly enhancing production efficiency and reducing production cycles.
- Reduced labor intensity and operational difficulty for workers, minimized safety hazards, and enhancedwelding quality stability.
- Achieved equipment informatization and visualization, improving the efficiency and precision of productionmanagement.
- Met customer demands, enabling customized production of small batches of various products, enhancingmarket competitiveness.
Solution Highlights
- Utilize a rebar plate welding robot workstation: Comprising an inverted 6-axis welding robot system, a2-axis mobile (X-axis walking and Z-axis lifting using an external robotic axis) inverted single-robot cantile-ver slide system, a horizontally fixed working platform (provided by the client, 200-400mm above ground),a 3D vision scanning system for robots, and a centralized welding smoke purification system.Adopt programming-free design, allowing users to simply place the workpiece in position.
- The system willautomatically scan the workpiece, generate scanning trajectories, and automatically match weldingprocesses for multi-station, multi-workpiece automated operation.
- The workstation features equipment informatization and visualization with MES interface, enabling inter-connection with production management systems to enhance efficiency and precision.
- Comprehensive service support is provided, including research, experimental validation,installation,debugging, and training, to assist clients in effectively utilizing and operating the product.
GLOBAL TOP 500 CASE
Rail Transit Enterprise
EVS Welding Workstation
Aleading enterprise within the Global Top 500, specializing inrail transit, has integrated the EVS welding worksta-tion for welding the side and end walls of various open-top railfreight cars.
This integration has significantly advanced weld-ing practices in terms of precision, efficiency, and automation,enhancing welding quality and efficiency, while reducing laborintensity and health hazards for workers.
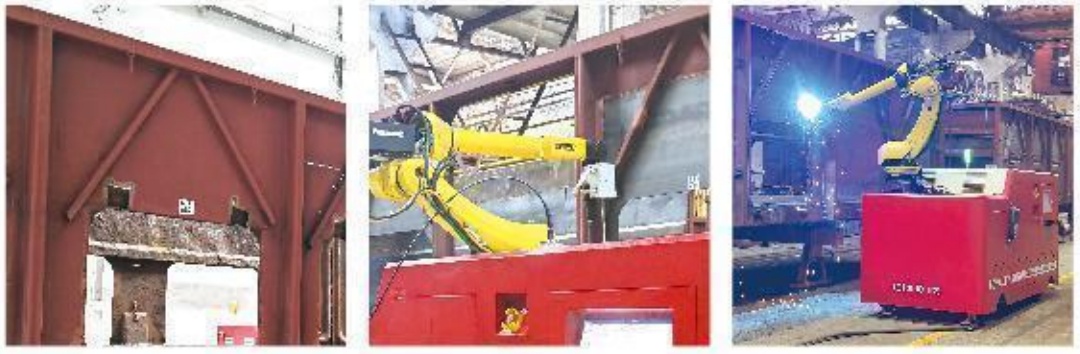
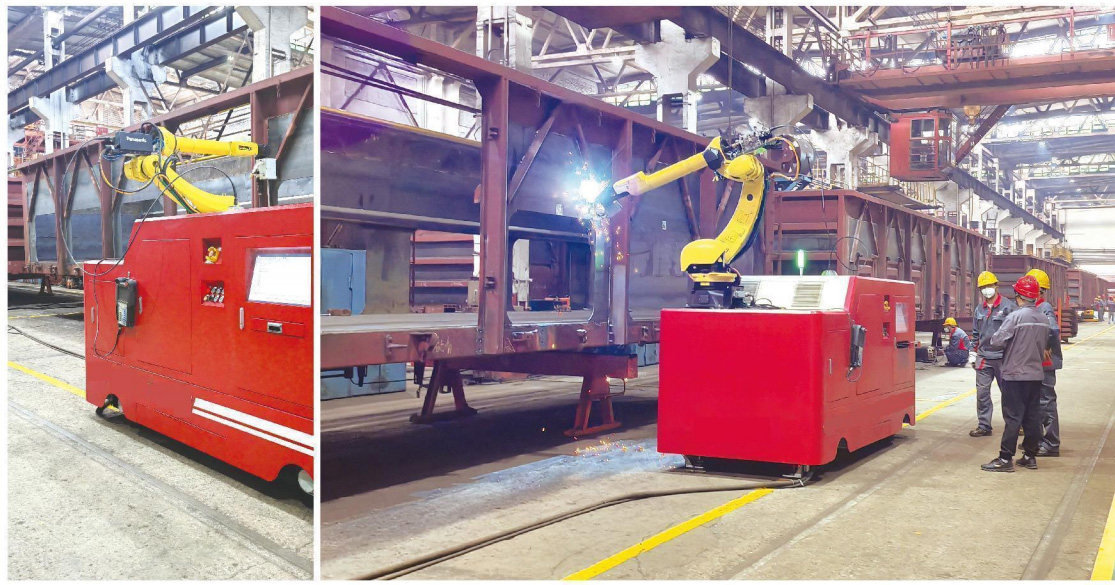
Project Pain Points
- In the maintenance of open railway freight cars, extensive repair welding work is required due to severe defor-mation of carriages.
- Traditional manual welding methods are inefficient and produce inconsistent quality, withthe generation of harmful gases during welding posing health risks to workers.
Project Achievements
- The project has successfully automated the welding of four different types of seams on the exteriors of freightcarriages.
- This system features high precision, efficiency, and a high degree of automation,significantlyimproving welding quality and efficiency, reducing labor intensity, and minimizing the hazards involved in thewelding process.
Solution Highlights
- The advanced EVS Welding Robot, integrated with visual scanning technology and a roboticcontrol system, has enabled efficient and precise automated welding.
- The robotic welder boasts full-range mobility, autonomous navigation, and precise positioning.
- Utilizingvisual scanning technology, the robot accurately identifies the location and shape of the weld seams,autonomously generating the robot’s posture and trajectory, and matching welding parameters to flawless-ly execute the repair welding process for freight carriages.
GLOBAL TOP 500 Rail Transit Enterprise EVS Cutting Station
An influential company within the Global Top 500 specializingin rail transit, focuses on the repair and remanufacturing ofvehicles, mechanical components, and structural construc-tions. To enhance efficiency, precision, and reduce costs, thecompany has integrated the EVS Cutting Station, auto-mating the robotic cutting of railway gondola side and endwalls. It stands out for its efficiency, accuracy, and cost-savingbenefits, ensuring longer service life, and enhanced perfor-mance and safety for vehicle components.
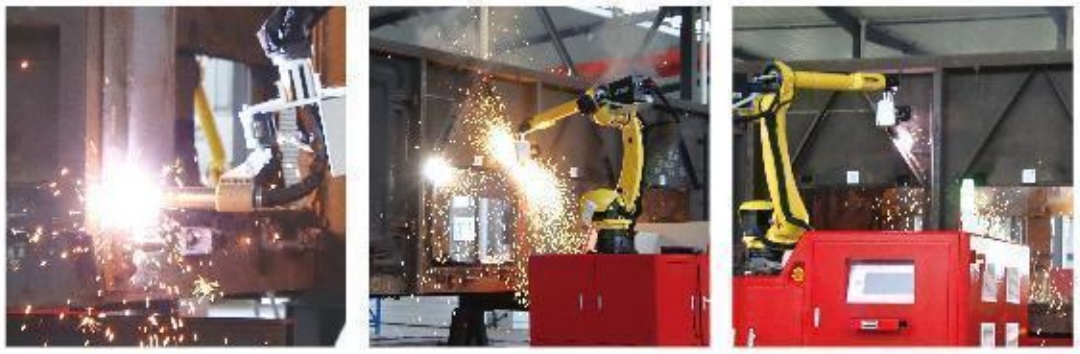
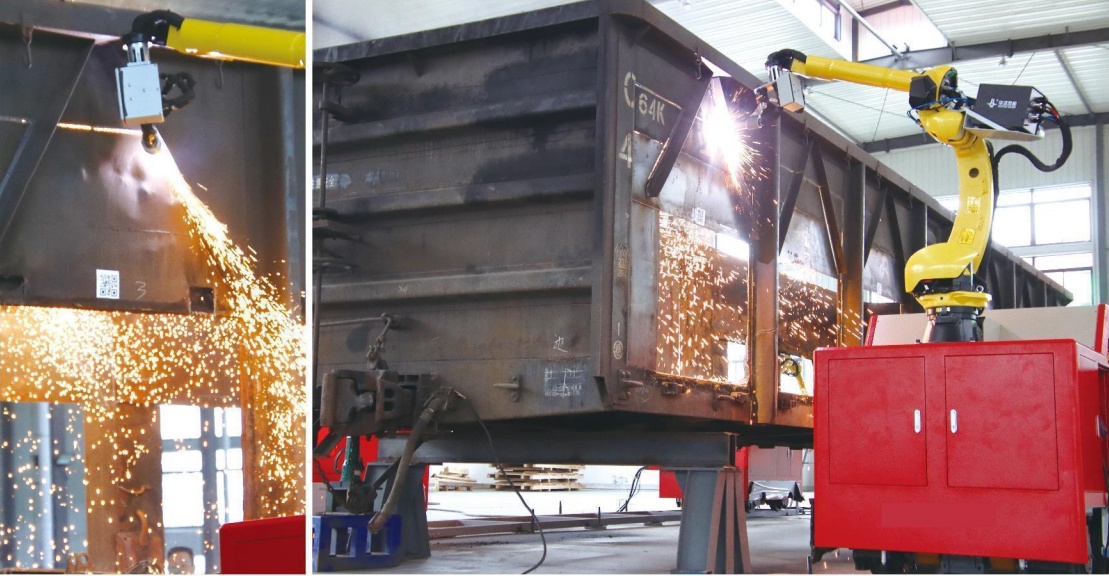
Project Pain Points
In traditional cutting and repair processes, workers manually operated cutting equipment, leading to inefficien-cies, poor cutting accuracy, and high costs. For large vehicles or structures, multiple workers needed to collab-orate, facing a significant workload and challenging working conditions. Improving the automation and preci-sion of the cutting process became a pressing issue for the enterprise.
Project Achievements
The introduction of the EVSCutting Station led to significant achievements: Firstly, it innovativelyapplied robotic cutting across the industry, automating the cutting process for freight carriages and significantlyenhancing technology equipment and production management levels.
Secondly, the application of machinevision technology introduced new methods for enhancing traditional processes, laying the groundwork for thecomprehensive implementation of robotic maintenance processes.
Solution Highlights
- EVS Cutting Station employs advanced plasma cutting equipment, robotic control technology,3Dvision, and computer control technology, achieving a highly automated and intelligent cutting process.
- The workstation includes five automatic plasma cutting devices, a central control system, and a rail-mount-ed platform for movement. The central control system coordinates and controls the entire workstation,including the movements of cutting devices and robots.
- The robot system executes the central controlsystem’s commands, accurately completing the cutting trajectories.The system features high cutting precision, a wide working range, and advanced technology.
- The position-ing accuracy for the vehicle body is ±30mm, with a maximum movement range of 6 meters.
- The maximumtargeted cutting area is 2000mm x 2000mm. The system operates fully automatically, with the entirevehicle cutting process completed in less than 45 minutes.
GLOBAL TOP 500 Intelligent and Flexible Production of Energy Enterprises
In the production of drilling equipment for petroleum machin-ery, there are numerous types and complex structures ofdrilling rig frame components. The integration of the EVSwelding machine has significantly enhanced productionefficiency, making it a benchmark case for welding operationson drilling rig frame components.
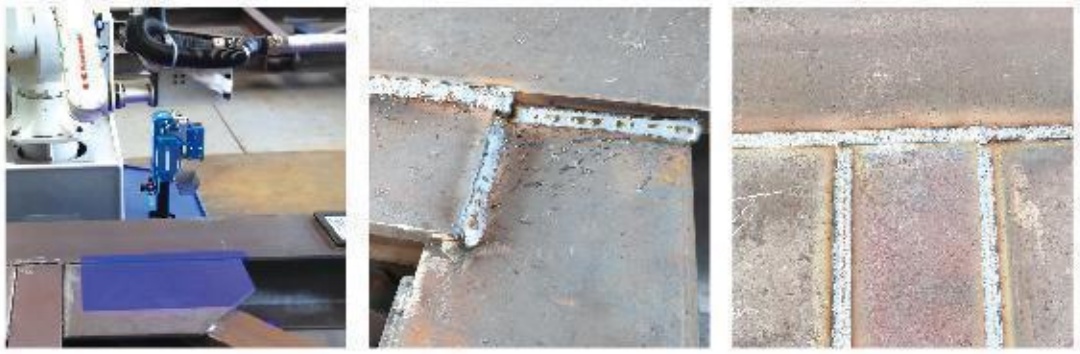
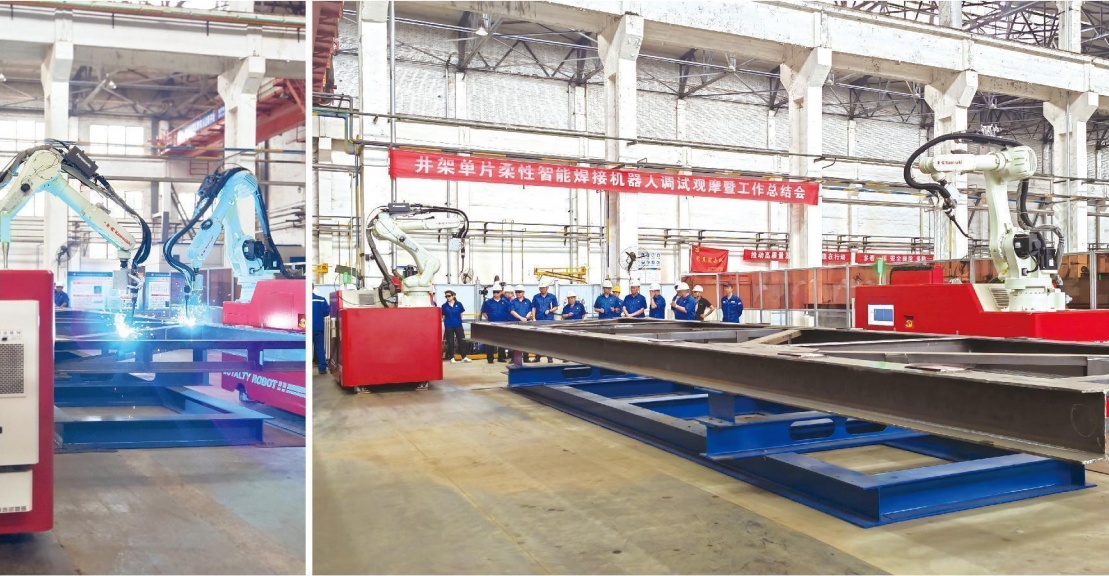
Project Pain Points
In the production of drilling rig frames, the manufacturing process involves various welding methods, such asT-joint vertical welding seams, plate butt joint vertical welding interlayer seams, plate butt joint horizontal weld-ing seams.
These diverse and complex welding operations are constrained by the instability and inefficiencyof manual operations, making it difficult to ensure welding quality and failing to meet the stringent efficiencyand quality requirements of modern drilling projects.
Project Achievements
Robotic welding technology has substantially improved welding accuracy and efficiency, far exceedingindustry standards in welding reach rates.
Significantly reduces the labor intensity of workers, optimizes welding quality, lowers operational risks,enhances productivity, and reduces production costs.
Has profoundly impacted the production efficiency and welding operation quality in the entire petroleummachinery production industry.
Solution Highlights
- Employing the EVS”Navigator Welder” welding robot integrated with intelligent 3D vision and flexible weld-ing technology.
- The robot is equipped with mecanum wheels, providing omnidirectional movement, intelligent walking, andautonomous navigation to meet flexible operational needs.
- The robot autonomously performs welding operations, with easy one-click start-up, eliminating the needfor manual programming and welding process formulation.
- During operations, it can automatically adjust the welding gun’s position and posture, achieving workpiecepositioning, seam tracking, and precise seam tracking capability (less than 1mm accuracy).
- The “Navigator Welder” also enables remote monitoring and multi-device management, enhancingefficiency and reducing reliance on manual labor.