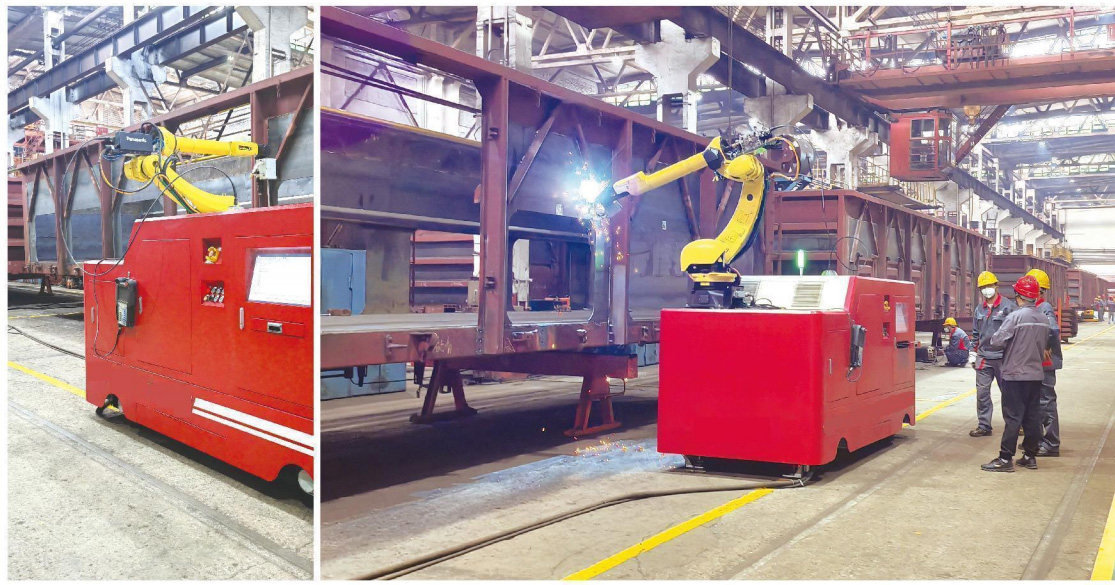
The railway industry has made great strides to improve efficiency and safety in the world of industrial automation. This is especially true when it comes time to repair and maintain freight carriages. One of these breakthroughs is the integration EVS Welding Workstation a robotic welding system that automates the process of weld open-top rail cars. This article examines problems with traditional railway maintenance. It also explores accomplishments that automation has brought about, and solutions offered by the EVS Welding Robot.
Traditional challenges in Railway Freight Car Maintenance
The transportation industry relies on open rail freight cars, but they are subjected harsh operating conditions which can lead to deformations. In order to maintain the safety and longevity of these vehicles, it is necessary to perform extensive repairs. The traditional manual welding techniques used to make these repairs can be inefficient and produce inconsistent welds. Manual welding also generates hazardous gases which pose a significant health risk to workers.
- Manual Welding Drawbacks:
- Variable quality: Human error and fatigue can lead to a variation in the quality of welds, which could cause safety concerns.
- Health Hazards: When welding, toxic gases are produced. This exposes workers in hazardous environments and compromises their health.
- Inefficiency in labor: Manual welds are labor-intensive and require a lot of time and effort. This affects productivity.
Project Achievements – Automation in Action
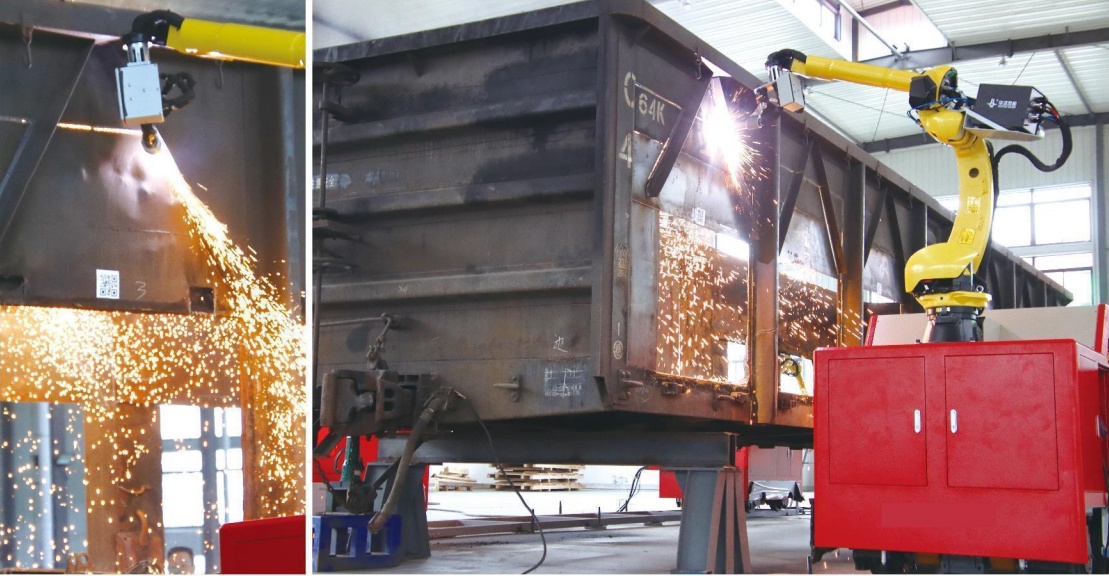
In order to address these problems, a global leader in rail transit implemented the EVS Welding Station. This successfully automated the welding process on various seams of open-top freight wagons. This innovative solution offers several benefits:
- Automating Multiple Welding Seams: With the EVS system, four different types of seams can be welded on the outside of freight carriages. This dramatically improves the speed and consistency in repairs.
- Improved Welding: The system integrates automation with high precision welding technology to ensure that each weld is performed flawlessly. This reduces errors and improves the durability of repairs.
- Reduced Labor Intensity By automating welding tasks, workers can focus on strategic roles that are less physically demanding.
- Safety and Health Improvements: By automating the welding process, it reduces exposure to hazardous gases.
Advanced EVS Welding Robot – A solution for precision and efficiency
The EVS Robot is the heart of this solution. It’s an advanced robotic system that can handle the most difficult aspects of welding. The robot integrates cutting edge technologies including vision scanning, and robotic controls to achieve the highest level of precision and autonomous.
- Visual Scanner Technology: This robot is equipped with an system of visual scanning, which allows it to identify accurately the location and shape the weld seams. This allows the robot to adjust its trajectory and posture to meet the specific requirements of welding tasks.
- Full-Range Mobility and Autonomous Navigation: EVS Welding Robot is equipped with autonomous positioning and autonomous guidance . This allows it to work across the carriage and ensure that welds, regardless of complexity, are placed in the right places.
- High Precision Welding Parameters After the visual scanning system has identified the weld seams and the robot has matched its movements with the optimal welding parameters to ensure flawless execution and consistent outcomes every time.
Benefits of Robotic Welding for Railway Freight Maintenance
Robotic welding systems, such as the EVS Welding Robot, represent a significant leap forward for the quality, efficiency and safety of rail freight carriage maintenance. Take a look at the benefits of robotic welding systems.
- Improved Welding Consistency and Quality: Automated weld systems eliminate inconsistencies in manual welding. They produce high-quality, precise welds.
- Increased worker safety: By minimizing the human involvement in welding’s hazardous process, robotic systems reduce workers exposure to toxic gasses and physical strain.
- Faster repair processes: Automation accelerates the repair cycle allowing freight wagons to be returned to service faster, minimising downtime and increasing operation efficiency.
- Labor efficiency and cost savings: By reducing labor intensity and improving welding speed, businesses can reduce labor costs and increase productivity.
Conclusion: Future-oriented Railway Maintenance
The integration of the EVS Welding Workstation in the railway maintenance industry represents a significant leap forward in automation and safety. This robotic welding system addresses the pain points associated with manual welding such as inconsistency, safety concerns and labor inefficiency.
Robotic welding will become more important as automation advances. This will ensure that railways are efficient, reliable, and safe. The future of railway maintenance is bright with companies adopting this technology around the globe. efficiency , safety and accuracy are leading the way.