The use of visual sensing has revolutionized welding in industrial settings. This innovation in China has made the automatic welding machines that are so well-known to the Chinese people smarter and more efficient. Visual sensing, which allows for precise detection of the weld seam size, shape and location, has improved quality control.
This technology has revolutionized the global welding industry. Modern welding operations are characterized by improved precision, higher safety standards and reduced environmental impact. These improvements not only increase productivity, but also reduce production costs. Automation is now more affordable than ever.
It is impossible to deny the role played by Chinese manufacturers in bringing about this transformation. China’s innovations in visual sensors have cemented its position as the leader of the global welding automation industry.
Impact Area | Description |
---|---|
Labor Productivity | Increased productivity of workers and lower labor intensity. |
Quality Control | Ability to detect the shape, size and position of weld seams. |
Production Efficiency | Better quality control can increase production efficiency and reduce production costs. |
The Key Takeaways
- Visual Sensing helps machines locate weld seams immediately. This increases quality and decreases errors.
- increases output by automating welding. While machines handle the tough jobs, workers can concentrate on more important tasks.
- The real-time system changes the welding settings automatically. This reduces the need for manual adjustments and keeps results consistent.
- By keeping workers safe, visual sensing can make work easier. Protect people by letting machines handle dangerous jobs.
- China is a leader in the welding industry due to its progress in visual sensors. These new ideas will make welding cheaper and faster.
Understanding Visual Sensing in Welding Automation
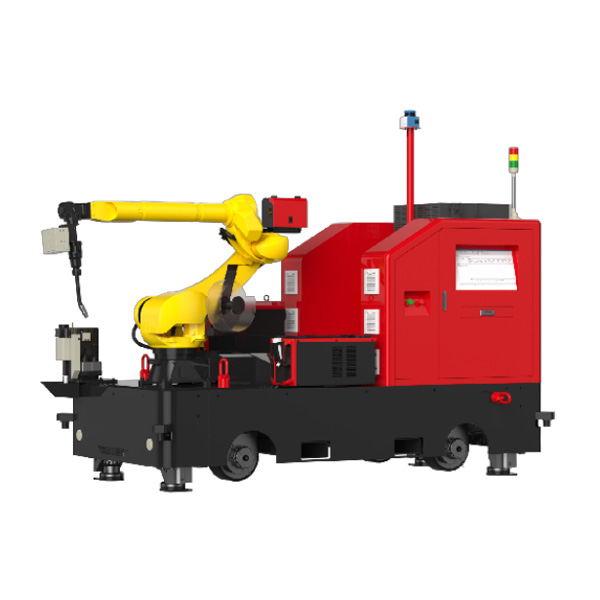
What is Visual Sensing Technology (VST)?
Visual Sensing Technology allows machines “see” their environment and interpret it. It uses imaging and advanced sensors to collect data on weld seams. These sensors use images to calculate objects’ characteristics such as their shape and location. This system is typically composed of graphic sensor and auxiliary equipment that work together to produce original images for machine-vision processing.
Laser-line-structured light, a component of the technology, is an important part. This technology is used extensively in robotic operations because of its reliability. The system improves accuracy by projecting laser fringes in linear or multilinear patterns. Visual sensing is a cornerstone in modern welding automation because of its precision.
Core Principles | Description |
---|---|
Intelligent Welding Robot Workstation | Structure and functionality of a workstation system |
Visual Sensing Technologies | There are many methods, such as line structure light (also called point structure light), surface structure light and surface structure light. |
Apps | Welding seam tracking, positioning and quality detection. |
Visual Sensing and Automatic Welding
Visual sensing is crucial to improving the performance and reliability of automatic welding machines. It allows for seam tracking and correcting, which ensures precise alignment while welding. Robotic systems that use laser technology, for example, can achieve error corrections of less than 0.06 mm. This level of precision improves the quality and durability of welds in even challenging environments.
This technology is also seamlessly integrated with robotic systems. Modules for image processing and communication with robots are included in dedicated vision sensors. These modules enable the system to track and identify welding seams in real-time. Visual sensing provides consistent results even in challenging scenarios.
Why visual sensing is crucial for modern welding machines
Visual sensing is used by modern welding machines to ensure high-quality production. This technology increases accuracy by automatically identifying seams of weld and adjusting parameters. This technology reduces the need to manually adjust parameters, saving time and minimizing errors.
Laser welding is also supported by visual sensing, which is important for industries that require precision, like automotive and aerospace. It ensures quality by allowing real-time feedback and monitoring. This translates into increased productivity and lower costs for manufacturers.
China’s advances in visual sensing has further enhanced the capabilities of automatic welding machines it produces. These machines deliver precision and reliability unmatched in the welding industry.
The Latest Advances in Visual Sensing Technology

Real-time Monitoring and Feedback System
The use of real-time monitoring has revolutionized the way you manage welding processes. These systems use advanced imaging algorithms for instant identification of welding seams. The Visionary system, for example, continuously tracks the position of the seam and adjusts welding torch trajectory. It reduces the need to manually intervene, minimising errors and increasing efficiency.
Modern welding machines collect information on parameters as critical as voltage, current and temperature. Sensors send this data to central systems or clouds, allowing you to remotely monitor and adjust your operations. IoT enabled machines go one step further and predict maintenance requirements. It reduces downtime, and increases the life of your equipment. These innovations will help you achieve higher productivity and consistent quality.
Enhanced precision through high-resolution imaging
It is essential to achieve precision when welding. This allows a detailed view of the heat affected zone and the weld pool. You can make adjustments immediately and avoid defects such as keyhole collapse or insufficient fusion.
The laser is also perfectly aligned with the joint. This maximizes the strength and minimizes waste of material. High-resolution images help you to detect defects early and ensure that each weld meets high standards. This level of accuracy is especially beneficial to industries that rely on laser welding, like automotive and aerospace.
AI and Machine Learning Integration
AI and machine-learning are revolutionizing welding automation. These technologies optimise welding parameters in real-time depending on the material type, thickness and joint configuration. AI, for example, monitors the weld process by using cameras and sensors. It can adjust temperature, speed and arc length in order to maintain quality.
AI-powered machine vision systems can detect imperfections such as cracks and misalignments. Machine learning algorithms become more accurate over time. AI also analyzes data in order to predict possible defects and ensure proactive quality control. System like NovEye can even make adaptive welding decisions, improving precision and efficiency.
China is now a leader in the world of welding innovation thanks to these advancements.
Adaptive welding based on visual data
The adaptive welding process represents a major leap in the automation of welding. Modern welding machines are able to adjust their operation in real-time by using visual data. This ensures that even under challenging conditions, every weld will meet the highest quality and precision standards.
Visual sensing systems provide detailed information on the welding environment. These systems examine weld seam characteristics such as size, shape, and position. This data is used to automatically adjust parameters such as speed, temperature and arc length. This adaptability allows for consistent results when working with materials that are complex or surfaces with irregularities.
The ability of adaptive welding to adapt to unexpected changes is one of its most impressive features. If, for example, a piece of work moves slightly during the welding process, the machine will detect the change and adjust its movements. The weld will remain accurate without the need for manual intervention. This technology can reduce errors and increase efficiency.
Adaptive welding is a great asset to industries such as aerospace and automotive. This technology is able to deliver the precision and consistency that these sectors require. These industries are setting new standards with machines equipped with adaptive welding capability, such as the automatic welding machine China produces. They use AI and advanced visual sensors to optimize the entire welding process.
Adaptive welding can increase productivity and maintain strict quality standards. This technology is not only time-saving but also reduces waste material, making it a vital tool for modern manufacturing.
Benefits of visual sensing in automatic welding machines
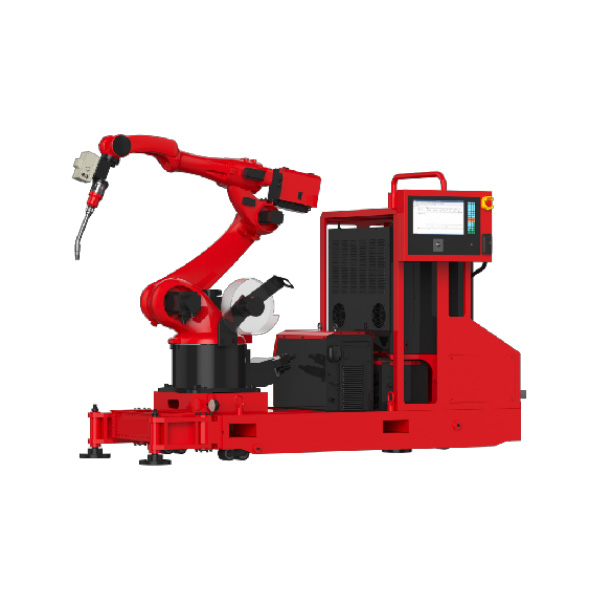
The Quality and Accuracy of Welding Has Improved
Visual sensing technology improves the accuracy and quality of welding. By using advanced imaging system, you can capture weld pools in detail while reducing the arc interference. This improves image matching which is crucial for high-quality welding.
Visual sensors give detailed information about the molten pools. This allows you to monitor welding processes with high accuracy. These sensors allow for closed-loop controls, which allows real-time adjustments in order to maintain consistency. A binocular system, for example, can automatically optimize parameters by tracking weld seams.
Approval | Description |
---|---|
Intelligent Welding Robot Workstation | How visual sensing helps in seam positioning and quality determination. |
Line Structure Light Method | This technique is widely used to improve welding accuracy. |
Multi-line Structure Lighting Method | Offers unique advantages for specific welding scenarios. |
Even in industries such as automotive and aerospace, this level of precision will ensure that each weld is up to the highest standard.
Reduced downtime and increased efficiency
Visual sensing technology can transform the way you manage your welding operations. It reduces downtime while increasing efficiency. Modern image processing systems can identify welding seams instantly, ensuring precise alignment. The system can adjust the trajectory of the torch instantly due to continuous monitoring, which minimizes errors and improves productivity.
Sensors and machine vision improve robotic performance through , enhancing quality, and timely maintenance. These capabilities ensure uninterrupted operations by reducing unnecessary delays. This reduces the chance of human error by reducing manual intervention.
- Real-time seam identification improves accuracy.
- Continuous monitoring ensures quick adjustments.
- Reliability is improved by reducing manual intervention.
Integrating visual sensing allows you to maintain consistency in production and minimize disruptions.
Cost-Effectiveness of Large-Scale Manufacturing
Visual sensing is a cost-effective technology for large-scale production. It minimizes the amount of material wasted by ensuring that welds are precise and reduces the need for rework due to defects. Automating welding tasks reduces labor costs and maintains high standards.
Laser welding combined with visual sensors, for example, ensures alignment and reduces the amount of material used. This is especially beneficial for industries that require high precision such as aerospace. This cost-effectiveness is exemplified by the automatic welding machines that China produces, which deliver reliable performance on a large scale.
Visual sensing can help you streamline production, reduce costs, and improve profitability.
Safety for Operators
Visual sensing has revolutionized operator safety for welding environments. It reduces the risk of exposure by automating key tasks. Welding is often associated with high temperatures, intense lights, and hazardous fumes. Visual sensing machines can handle these hazards, so you can focus on supervision instead of direct involvement.
Did You Know?
Visual sensing systems detect hazards in real-time, making your workplace safer for you and the rest of your team.
This technology is a safety enhancement:
- Reduced Exposure to Hazards : Automated weld systems equipped with visual sensors eliminate the need to work near hot zones or harmful UV radiation. This reduces your risk of eye and burn injuries.
- Real Time Hazard Detection : Advanced sensors continuously monitor the environment. They can detect issues such as overheating and equipment malfunctions to enable quick correction.
- Less Manual Intervention: Machines can adjust parameters automatically using visual sensing. It reduces the need for manual intervention during operation, which lowers the risk of accident.
- Improved Ergonomics By automating repetitive task, this technology reduces physical stress. Avoid fatigue and long-term muscular-skeletal problems.
Safety Features | Benefit |
---|---|
Automated Hazard Detection | Identifying risks such as overheating and misalignment, before they escalate. |
Remote Monitoring | Allows you to supervise operations from a distance. |
Reduced Physical Stress | Reduces the risk of injury caused by repetitive work. |
Remote monitoring is also supported by visual sensing. You can monitor operations in a control center, away from any potential danger. This feature is particularly useful in industries such as automotive and aerospace where safety standards can be very strict.
Integrating visual sensing in welding machines creates a safer working environment. This technology protects not only you, but also ensures that safety regulations are met. This is a win for both productivity and health.
Chinese manufacturers are driving innovation in visual sensing
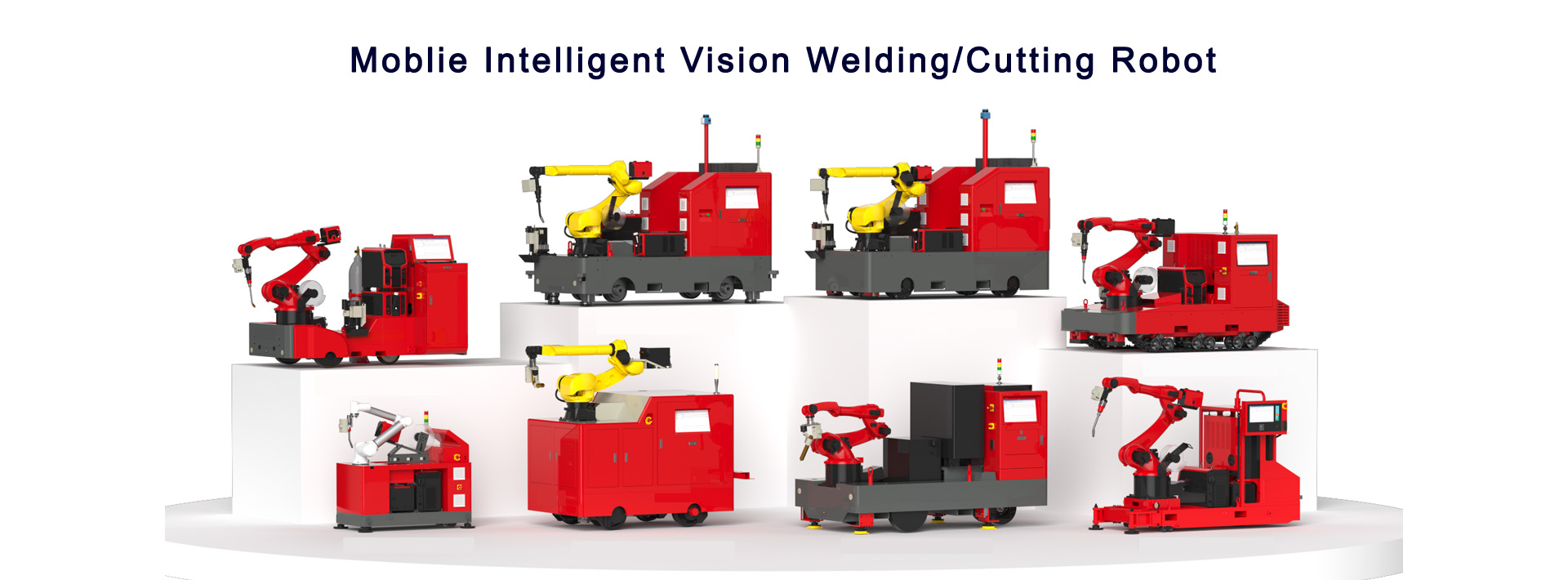
EVS Robotics Mobile Vision Welding Robot
EVS Robotics is a leader of visual sensor innovation, with its Mobile Intelligent Vision Welding & Cutting Robot. This robot is a combination of mobility and intelligent vision systems that delivers exceptional results. You can maximize your resource usage by navigating through different work environments with its mobility. Vision systems on the robot ensure precision alignment and high-quality welding. Businesses who adopt this technology experience productivity increases of up to 20.
Robots use cutting-edge technologies such as point structure and line structure lights to track and position welding seams. These methods improve quality control, detecting defects in welding early and improving production efficiency. The robot also reduces production costs through the optimization of welding processes.
Contribution | Description |
---|---|
Visual Sensing Technologies | Use advanced methods to track and position seams. |
Quality Control | Improves defect detection, ensuring consistent production quality. |
Cost Reduction | Reduced production costs by improving process control. |
Visual Sensing and Welding: The Future
Visual Sensing Technology: Emerging Trends
Visual sensing continues to develop, bringing exciting advances to welding automation. Future systems will be smarter, more efficient and more reliable. These systems will likely use computer vision to monitor weld seams in real time. The machines will be able to adjust and track with more precision.
AI and deep-learning will improve accuracy. These technologies can help to identify complex shapes of welds and increase stability in operations. You will also see less errors and better-quality welds.
Here’s an overview of what’s to come:
- Welding automation will be more accurate and stable with intelligent systems.
- The systems can be adapted to handle different welding processes and materials.
- By identifying the size, shape and location of weld seams, a better quality production can be achieved.
Aspect | Description |
---|---|
Intelligent Systems | Visual sensing technology enables intelligent welding automation , improving accuracy and stability . |
Adaptability | The systems can be adapted to different welding processes and materials including manual and automatic welding. |
Quality Detection | It is capable of detecting the shape, size, location, and quality weld seams. This improves overall production. |
Other Applications of Welding
Visual sensing technology is capable of much more than welding. It can be used in industries such as construction to monitor structural integrity. It can be used to inspect manufacturing products for defects and ensure consistent quality.
Visual sensing in the medical field could be used to assist with robotic surgery. By providing real-time imaging, it ensures precision during complex procedures. This technology is also useful in agriculture. It can be used to monitor crop health, and automate harvesting.
Tip : Explore these applications to open up new opportunities for innovation in your industry.
The Industry’s Challenges and Opportunities
The adoption of visual sensing technology is not without its challenges. System stability can be affected by complex welding environments and materials. The high cost of these systems may be a barrier for smaller enterprises. The lack of standardization makes it difficult to implement technology consistently.
Challenge Type | Description |
---|---|
Technical bottlenecks | System stability and reliability are affected by complex welding environments and materials. |
Costs | The high cost of these systems limits their use by smaller businesses. |
Standards and regulations | Standardization is needed to promote technological development and unify industry practices. |
Safety and reliability | For welding to be safe, it is important that the safety and stability of the process are high. |
The opportunities, despite these challenges, are vast. You can unleash the full potential of vision sensing by addressing these challenges. It will result in safer, more cost-effective, and efficient solutions for your company.
Visual sensing technology has transformed welding automation by enhancing precision, efficiency, and safety. It identifies and tracks weld contours in real time , ensuring accurate adjustments during operations. You can rely on this technology to improve quality control and streamline production processes.
The development of visual sensors has made it possible to adapt welding systems to a variety of materials and processes. These innovations improve productivity and reduce errors and hazards. These systems will provide you with higher reliability and more consistent results.
China is a global leader in the welding industry, with its cutting-edge technologies. You can access advanced and cost-effective automation technologies thanks to its focus on innovation.
The FAQ
What is visual sensor technology in welding?
Visual Sensing Technology allows machines “see” weld seams. Sensors and imaging systems are used to collect data on the size, shape and location of welds. These data help machines to adjust their operation for better accuracy.
Visual sensing can improve the accuracy of welding.
Visual tracking tracks seams in real-time. It automatically adjusts parameters such as speed and temperature. It ensures accurate alignment and reduces mistakes, even when performing complex welding tasks.
Why is it important to have visual senses for safety?
Visual sensing can reduce your exposure to hazardous fumes and high temperatures. Sensors detect dangers while automated systems perform dangerous tasks. This creates a safer workplace for operators.
What industries are most likely to benefit from the use of visual welding sensing?
Automotive, aerospace and manufacturing industries are the biggest beneficiaries. Visual sensing is a powerful tool for industries that require precision and consistency.
How can automatic control technology improve welding automation?
Visual sensing and automatic control technology are combined to optimize the welding process. It automatically adjusts parameters to ensure consistent quality, and reduces the need for manual interventions.