Feeding System
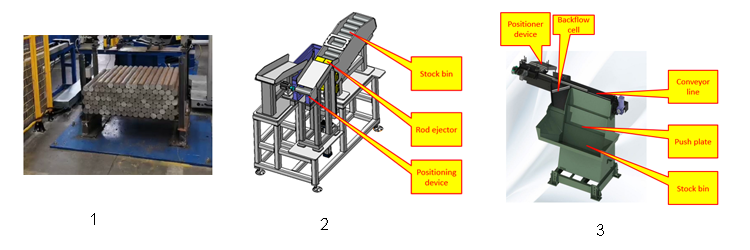
This first way is with no positioning for each round bar, so it needs positioning before loading to the CNC lathe. The second and the third feeding ways are using a ejector or push plate, along with a positioning device so the subsequent process can be easier than the first way.
Loading System
Everyone knows automation is key to profitability, motor shaft machining is no exception. Using automatic loading system is the mainstream for motor shaft machining because it’s not a cutting-age technology any more. Anyone who want to reduce the labor cost and improve efficiency will choose to automate the loading process in the motor shaft machining production line. Automatic loading system offers 30 to 50 percent faster loading times than manual loading, enable the lathes to operate without operator attention for long periods of time and combine more consistent production with more accurate scheduling. There are two main method for motor shaft automatic loading: Gantry Loading System and Robotic Loading System.
1. Gantry Loading System
Gantry loading system consists of 2-4 aixs linear motion, each shaft runs in a straight line at a very high speed and can be quickly responded by a servo motor, it is stable and accurate (up to 0.02mm). It is very easy to use and maintenance.
Gantry System Advantages: compact layout, small floor area, high precision, high efficiency, stable operation, convenient maintenance.
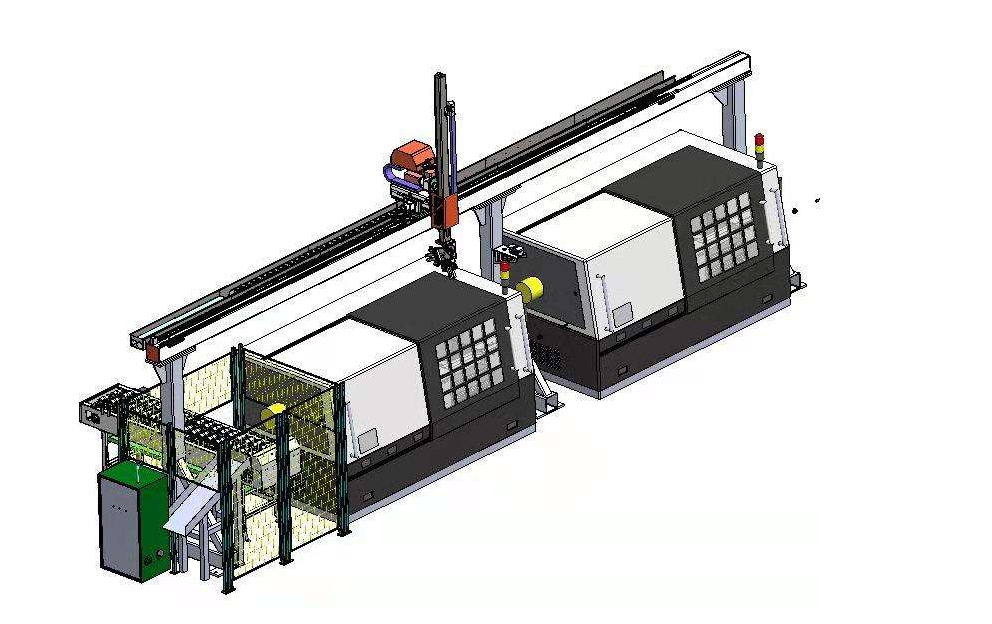
2. Robotic Loading System
Space is already at a premium in most motor shaft production facilities, while robots have a small footprint and cables routed through the wrist with 6 movable axis, so robotic loading system is more flexible than any other loading system. It is less expensive and easier to use than you might imagine, robotic loading system offers you considerable benefits even on small production runs. The 6-Axis robot’s speed and degrees of freedom allow it to accomplish many tasks that would be impossible for the 2-4 Axes available on a traditional gantry.
Robotic Loading System Advantages: compact layout, multi-style, high precision, high efficiency, smooth operation, convenient maintenance, high flexibility.
Grinder Clamping System
Because the accuracy requirement of the motor shaft is very high, only the top positioning can be used to clamp the motor shaft. When using double tops to install the workpiece, the front and rear tops cannot drive the workpiece to rotate, and other mechanisms must be used to transmit power. There are 3 methods for motor shaft clamping: lathe carrier, centrifugal clamping and chuck.
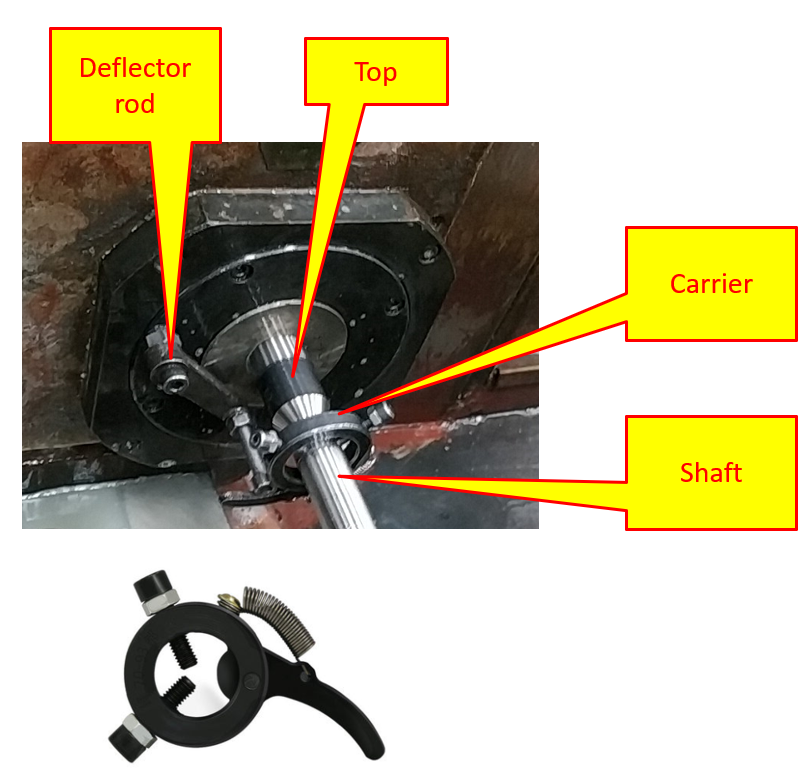
Disadvantages: Low efficiency, low compatibility
2. Centrifugal clamping mechanism
When the grinding machine is rotating, the clamping block rotates around the rotation axis under the action of centrifugal force and then clamps the motor shaft. When the grinding machine stops, the clamping block returns to its original position under the action of spring.
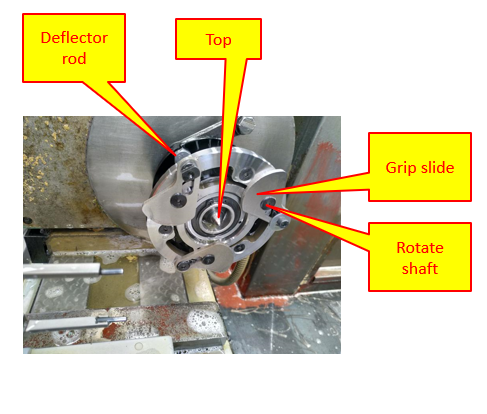
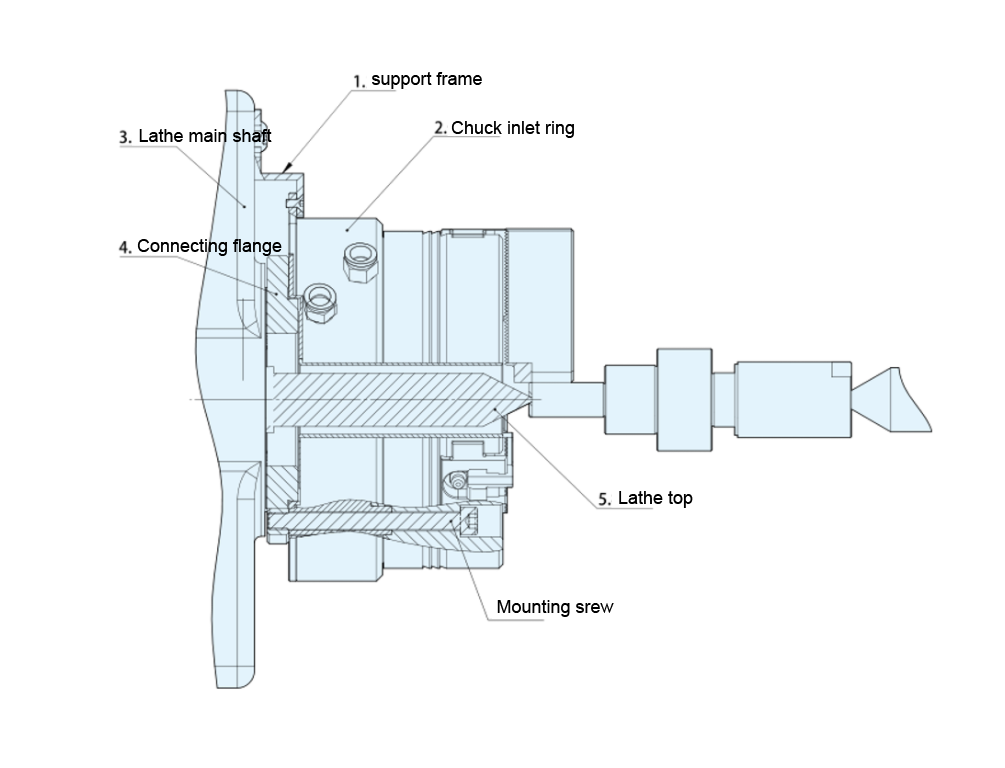
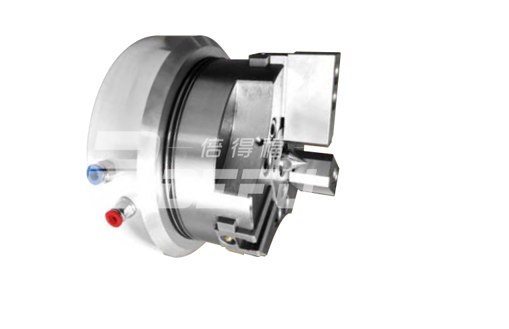