Heavy-duty industrial welding robots have transformed how factories operate today. These robots enhance productivity and precision, enabling factories to expand. In 2023, the global market for arc welding robots was valued at $5.3 billion. By 2032, it is projected to increase to $10.8 billion. Companies that manufacture heavy-duty industrial welding robots are empowering factories to implement superior automation across the board.
Key Takeaways
- Strong welding robots help factories work faster and better.
- Big companies like ABB, FANUC, and KUKA are top makers.
- Using smart welding robots lowers mistakes and improves product quality.
ABB Robotics
History and role in the industry
ABB Robotics started in 1988 after two companies joined together. Since then, it has become a top name in industrial robots, owning about 14% of the global market. Their robots are used in industries like cars, electronics, and shipping. Many big companies trust ABB because their robots are accurate and long-lasting.
Main welding robot models
ABB makes robots that handle tough welding jobs easily. Their robots are great for spot and laser welding, especially in car factories. They also use AI to check welds for mistakes, keeping quality high. ABB’s mix of smart tech and dependability makes them a leader in welding robots.
Special features and new ideas
ABB Robotics stays ahead with new ideas. Here are some of their latest:
Feature | What It Does |
---|---|
AppStudio | A tool that cuts setup time by 80%, making it easier to customize. |
AI Item Picking | Uses AI to improve speed in warehouses and online shopping. |
Smart AI Tools | Helps robots work better in changing environments. |
These updates show ABB’s focus on improving automation.
Why ABB leads in 2025
ABB Robotics is known for accuracy, new ideas, and flexibility. Their robots can repeat tasks with a tiny error of ±0.02mm, better than many rivals. KUKA Robotics can lift heavier loads, but ABB’s focus on precision and smart AI gives them an edge. Their advanced features keep them a top pick for welding and other factory tasks.
FANUC Corporation
History and worldwide presence
FANUC Corporation began in 1956 and is now a global leader. It focuses on making welding robots and other automation tools. Over time, FANUC has grown its market reach a lot. The table below shows how the robotics market has expanded:
Year | Market Size (USD Billion) | CAGR (%) |
---|---|---|
2019 | 1.2 | N/A |
2024 | 3.3 | N/A |
2032 | 6.5 | 15.8 |
This growth proves FANUC’s big role in the industry and its ability to meet changing factory needs.
Top welding robot models
FANUC’s CRX series is popular for tough welding jobs. These robots are strong, precise, and long-lasting. Key features include:
- The CRX-25iA cobot, which can carry 30 kg (66.1 lb.) and reach 1,889 mm (74.3 in.).
- No maintenance needed for up to eight years.
- Smart tools like iRVision, Touch Sensing, Servo Torch, Thru Arc Seam Tracking (TAST), and Multi Pass (MP).
These features help factories work faster and solve worker shortages.
New automation technologies
FANUC keeps improving with advanced technology. Its food-safe robots meet strict cleanliness rules with special coatings and oils. These robots are safe and accurate for food production. FANUC also leads in North America with great service and new ideas. This focus on tech makes it a top choice for factory automation.
FANUC’s success in 2025
FANUC’s strong finances show its success. In 2022, it earned $5.7 billion and had a profit margin over 42%. It spends 10.3% of sales on research, showing its focus on new ideas. FANUC’s reliable and high-quality welding robots keep it a leader in 2025.
KUKA Robotics
Company background and expertise
KUKA Robotics is a leader in industrial automation. They offer advanced training and smart technologies. Their training helps workers learn 40% faster than usual methods. Factories with KUKA-trained workers see a 35% boost in robot use. KUKA’s systems also cut unexpected downtime by 75%. These successes show why KUKA is trusted for welding robots.
Heavy-duty welding solutions
KUKA makes robots for tough welding jobs in many industries. Their robots are precise and dependable for hard tasks. They work well in car, airplane, and building industries. KUKA robots use smart sensors and controls for perfect welds. These systems improve work speed and reduce mistakes. That’s why they are a top choice for welding.
Integration with Industry 4.0
KUKA connects welding robots with Industry 4.0 technology. They focus on custom products instead of mass production. Simon Whitton, a KUKA leader, says their KUKA Connect software links robots to many tools on one platform. This system uses data and cloud tech to improve factory work. It helps predict problems and boost quality and flexibility.
KUKA’s role in shaping the future of welding robotics
KUKA Robotics leads the future of welding with new ideas and trust. Their focus on custom solutions keeps them ahead in the industry. By using Industry 4.0, KUKA helps factories work better and faster. Their dedication to innovation makes them a top welding robot maker in 2025.
Yaskawa Motoman
History and focus on robotics
Yaskawa Motoman has been making robots since 1915. It is now a top welding robot maker, known for new ideas and great support. They created the Motoman Academy to teach people about their robots. This program includes lessons, online tools, and training with experts. These resources help users avoid mistakes and use the robots well. Their focus on teaching shows they care about customer success.
Welding robot models
Yaskawa Motoman has many welding robots for different industries. The AR-series is great for arc welding jobs. These robots are small, quick, and very accurate. The GP-series is another favorite. It works for welding and moving materials. All their robots are built to give steady, high-quality results every time.
Precision and speed
Yaskawa Motoman designs robots to be precise and fast. Their advanced controls make welding smooth and accurate. This lowers mistakes and boosts efficiency. Their robots also work quickly without losing quality. This mix of speed and accuracy helps factories work better and faster.
Yaskawa’s success in 2025
In 2025, Yaskawa Motoman stays a leader in welding robots. They focus on teaching, accuracy, and speed, which makes them stand out. Their reliable and flexible robots help factories stay competitive. By improving technology and supporting users, Yaskawa remains a top choice for welding automation.
Panasonic Welding Systems
Background in welding technology
Panasonic Welding Systems is known for its great welding robots. They make high-quality machines that fit different factory needs. Their Integrated Welding Management System (iWNB) is a big example. It uses digital tools to track machine work and quality. This system helps factories work faster and better. Panasonic is a top name in welding robots because of this. The robotic welding market is growing fast, from $5.45 billion in 2018 to $10.78 billion by 2026. Panasonic is ready to meet this growing need for smart machines.
Advanced robotic welding systems
Panasonic builds advanced welding robots for many factory problems. Their machines are precise, fast, and flexible. This makes them perfect for industries like airplanes, buildings, and electronics. These robots handle hard tasks and keep quality steady. They also lower mistakes and save time. Panasonic’s focus on new ideas keeps their robots ahead of others.
Unique features and applications
Panasonic’s welding robots are special because they work well in many areas. The table below shows how they help different industries:
Industry | How Panasonic Helps |
---|---|
Aerospace | Makes strong welds for safety and tough structures. |
Construction | Cuts down worker needs and errors, saving time and money. |
Electronics | Handles tiny parts with care, helping with small designs. |
These features make Panasonic a top pick for factories needing reliable robots.
Panasonic’s contribution to the industry
Panasonic leads the way in robotic welding with smart solutions. Their machines help factories work faster and make better products. They focus on solving problems for different industries. This keeps Panasonic important in today’s manufacturing world. Their dedication to new ideas makes them a trusted name in welding robots.
Lincoln Electric
History and expertise in welding
Lincoln Electric has been trusted in welding for over 100 years. It started in 1895 as a small electric motor company. Over time, it became a top welding robot maker known for smart ideas and quality. By 2023, Lincoln Electric showed strong results:
Metric | 2023 Score |
---|---|
Total Sales Vitality Index | 42% |
Equipment Sales Vitality Index | 57% |
These numbers show its big role in welding technology and growth.
Robotic welding solutions
Lincoln Electric makes many tools for different factory needs. One is the RANGER® AIR 260MPX™, which welds, generates power, and compresses air while saving fuel. Another is the MAGNUM® PRO FUME GUN, which reduces harmful fumes. The FRONTIER® 400X is small but powerful for welding jobs. These tools are safe, reliable, and help factories work better.
Focus on durability and performance
Lincoln Electric designs products to last and perform well. The WELD-PAK® 180i and Laser-Pak® PPL™ save energy and are built tough. The POWER WAVE® R450 RAPID has modes that lower fumes, showing care for the environment. These features make Lincoln Electric a trusted choice for strong and efficient welding tools.
Lincoln Electric’s standing in 2025
In 2025, Lincoln Electric stays a top name in welding. Its focus on new ideas and customer needs keeps it ahead. By making reliable tools, it helps factories work faster and better. Whether you need smart robots or energy-saving systems, Lincoln Electric has what you need.
Kawasaki Robotics
Company overview and innovation
Kawasaki Robotics is part of Kawasaki Heavy Industries. It started as a shipbuilding company in 1878. Later, it grew into making trains, motorcycles, and airplane parts. By the 1980s, Kawasaki became a leader in robots and factory tools. Today, it works in car-making, electronics, and welding. These skills make Kawasaki a trusted name in welding robots.
Year | Important Event |
---|---|
1878 | Started as a shipbuilding company |
1907 | Made Japan’s first train |
1960 | Began making motorcycles |
1980 | Expanded into airplane technology |
Kawasaki’s focus on new ideas helps its robots meet factory needs. Its welding robots set high standards in the industry.
Heavy-duty welding robot models
Kawasaki makes strong welding robots for tough jobs. These robots are great for industries needing precise and reliable work. The BA Series robots are fast and accurate for arc welding. The RA Series robots are perfect for spot welding and can lift heavy loads. Each robot is built to give steady results, making them popular for factories wanting advanced tools.
Integration with smart manufacturing
Kawasaki Robotics uses smart technology to improve factory work. Systems like SAP S/4HANA PEO help factories use real-time data. This makes production faster and better. Factories can quickly change how they work using feedback from these systems. The Kawasaki Corleo robot also boosts speed and quality in production lines.
Feature Description | How It Helps Factories |
---|---|
Real-time data sharing | Makes products better and faster |
Feedback between design and production | Helps factories adjust quickly |
Kawasaki Corleo robot | Improves factory speed and efficiency |
Kawasaki’s impact on the industry
Kawasaki Robotics has changed welding with smart and reliable robots. Its machines help factories work faster and more accurately. By using advanced technology, Kawasaki keeps factories competitive in today’s fast-changing world. As a top maker of welding robots, Kawasaki leads the way in factory automation.
Universal Robots
Background in collaborative robotics
Universal Robots started in 2005 and changed collaborative robotics. They make cobots that safely work with humans on tasks like welding. These robots don’t need big safety barriers, making them easy to use. Their small size and ability to move around help smaller factories improve production. Universal Robots is known for creating smart and helpful welding robots.
Welding robot offerings
Universal Robots makes cobots for many types of welding. They can do arc, TIG, MIG, and laser welding. These robots work in industries like cars and electronics. Their welding system uses an app, so programming is simple. Even beginners can set them up quickly. These cobots save space and make high-quality welds, helping factories work better.
Flexibility and ease of use
Universal Robots are easy to set up and use. You can get them running in hours, not days. They are portable, so you can move them to different tasks easily. One user said they started using their cobot just 20 minutes after opening the box. You can quickly change tools to fit different projects. This makes them great for small and medium-sized factories.
Universal Robots’ position in 2025
In 2025, Universal Robots is still a top name in cobots. Their easy-to-use and flexible robots help factories meet changing needs. Whether your business is small or large, their cobots help you stay competitive. Universal Robots gives manufacturers the tools to succeed in fast-moving industries.
OTC Daihen
History and focus on welding
OTC Daihen has been making welding tools since 1919. They are experts in creating advanced welding robots for today’s industries. Their work is built on years of innovation, especially in arc welding and automation. OTC Daihen is known for making reliable and precise robots. Many companies in cars, airplanes, and heavy machines trust their products. Their focus on quality has made them a respected name worldwide.
Robotic welding systems
OTC Daihen makes many robotic systems for tough welding jobs. Their FD Series robots can do arc welding, spot welding, and move materials. These robots use smart controls to make sure welds are always good. The FD-V8 robot is small but strong, perfect for tight spaces. These robots are easy to use and keep work moving fast. OTC Daihen designs their systems to meet the needs of industries that require accuracy and speed.
Focus on precision and dependability
OTC Daihen builds robots to be precise and dependable. They use ideas from Shigeo Shingo to avoid mistakes and improve results. Their smart controls include checks like source inspection to catch errors early. These features help factories make better products with fewer problems. OTC Daihen’s focus on precision helps companies get great results, even in hard conditions.
OTC Daihen’s success in 2025
In 2025, OTC Daihen stays a leader in welding robots. Their focus on avoiding mistakes and improving controls makes them stand out. By using advanced technology, they help factories work better and faster. OTC Daihen’s ability to change with industry needs keeps them a top choice. Whether you work in cars, planes, or heavy machines, their robots are reliable and precise to help you stay ahead.
EVS Robotic Welding Station
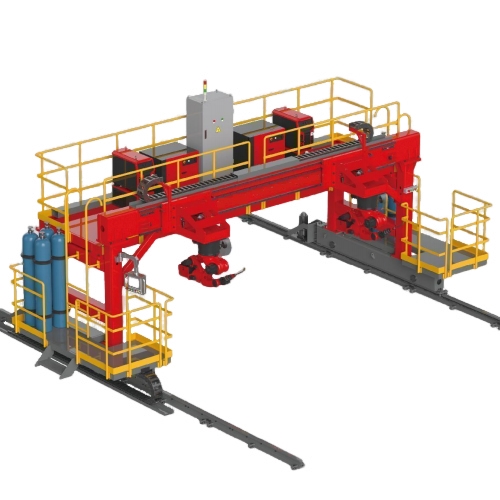
Introduction to EVS and its market presence
EVS is a well-known name in industrial automation. It creates smart welding robots for modern factory needs. The company has grown a lot, especially in car-making. In car factories, over 70% of body assembly uses robotic welding. EVS helps make sure these processes are high-quality. Its focus on new ideas and trustworthiness makes it popular worldwide.
Robotic Welding Station series
EVS’s Robotic Welding Station series offers advanced tools for factories. This includes the Gantry Rail Dual Welding Station, Nine-Axis Cantilever Weld Station, and Seven-Axis Track Weld Station. Each tool is made for tough welding jobs. The Gantry Rail Station works well for flexible setups. The Nine-Axis Station handles detailed welding tasks. The Seven-Axis Station is great for versatile operations. These tools give steady results, making them useful in car-making, medical tools, and metalwork.
Innovations like 3D vision technology and intelligent control
EVS uses smart tech like 3D vision and intelligent controls in its robots. These features make production faster and more accurate. Car factories, where 19.5% use AI-based 3D vision, benefit a lot. As electric cars grow, precise welding is more important. EVS adds real-time checks and data tracking to its systems. This improves safety, cuts costs, and speeds up production.
Why EVS is an emerging leader in 2025
In 2025, EVS is a rising star in welding robots. Its Robotic Welding Station series shows it can meet many factory needs. By using 3D vision and smart controls, EVS stays ahead in automation. With 95% of car factory spot welding done by robots, EVS plays a big role. These strengths make EVS a top choice for future factory automation.
The best heavy-duty welding robots in 2025 are smart and precise. Pick robot makers that focus on safety, flexibility, and automation. The market, worth $7.99 billion, is growing with new tech. As factories use AI and 3D vision, welding robots will improve work speed and quality in many industries.
FAQ
What do heavy-duty welding robots do?
Heavy-duty welding robots join metal parts in factories. They are used in car-making, airplanes, and building projects. These robots make work faster and more accurate.
How do makers keep welding robots dependable?
Makers use strong materials and smart sensors in their robots. These features help the robots work well for a long time, even in tough jobs.
Can small factories use welding robots?
Yes, small factories can use welding robots. Many robots are small and easy to set up. They give great results without needing much space.