Source: Pixabay
Welding robots are among the most important industrial robots in the manufacturing space. They handle welding, which is essentially the one thing that holds machines together, cars included. Robotics in automotive manufacturing highly depends on automated welding, replacing human labor in almost all car manufacturing plants across the globe. Of all industrial robot applications in manufacturing, robotic welding is the most recent, having been introduced less than 20 years ago.
Types of Robotic Welding Processes
There are about six automated welding processes that are widely used in industrial manufacturing. Each process serves a unique function and has a special robot designed to execute that function.
Resistance Spot Welding
Resistance spot welding is a process where heat from electrical resistance is applied with force to weld metallic materials together. This concentration of pressure and electricity on one point causes the metal to melt and coalesce while they are in their molten state. The metal is then left to cool off and becomes permanently joined at that spot, hence the name Spot Welding.
The advantages of using a spot welding robot are many; one is that it is seamless; it does not leave any marks of welding having taken place. Another one is that it is much stronger compared to other types of welding; once two parts melt into each other, there are weak points left. The automotive industry relies heavily on spot welding robots, with the average car having over 5000 spot welds.
Laser Welding
This Is another advanced form of joining metals that focuses heat on one point using laser beams. The technology has been around for over 30 years. Laser welding works by putting together two metal sheets into contact with each other. This is followed by the concentration of the laser beam on their edges of the metal sheets. The intense heat makes them melt at the same time, mixing them up completing the joint. Once they cool down, they become one.
Some of the advantages of laser welding include high precision since a laser beam can be controlled easily. The speed of welding is also very high; the intense heat causes any type of metal to melt into each other, forming a joint instantly. The consistency is also high, which makes it the ideal method if you are looking to create uniformity.
Gas Metal Arc Welding
This is a type of a robotic welding process where the source of the heat is an arc formed between a consumable metal electrode and the workpiece with an externally supplied gaseous shield of gas that is usually an inert gas. This causes a weld pool to be formed between the two materials, which now join after cooling off.
There are two types of a gas metal arc welding robot. The first one is called Metal Inert Gas Welding (MIG welding robot) that uses an inert gas like Argon or Helium; then, there is the Metal Active Gas Welding (MAG) that makes use of an active gas that is usually a mixture of oxygen, carbon dioxide, and argon.
The main advantage of gas metal arc welding is that there is no splatter of molten materials, as is usually the case with other welding techniques; the shielding gas protects the weld pool until it cools off.
Gas Tungsten Arc Welding
This is a type of welding that passes electricity between the electrode and the material to be welded. The weld is shielded from the atmosphere by a shielding gas that envelopes the weld area. The electrode used in this process is made out of tungsten. The reason why this metal is chosen is the fact that it has the highest melting temperatures of any metal at 6,170 degrees Fahrenheit.
The three main tungsten alloys that are used in this welding process are Zirconiated tungsten, which is used for non-ferrous metals and uses higher AC currents. There is Thoriated tungsten, which is used on carbon and stainless steel, and lastly Pure tungsten, which is used on aluminum and magnesium.
Thin Gauge Arc Welding
This is a robotic welding process that is used on thin materials that require delicate welding. Anyone well versed with welding will attest to the fact that welding thin sheets of metals is a huge challenge. If you use too much force or a very extreme kind of welding, it may change the entire nature of the materials involved. Thin gauge arc welding works by minimizing the burn through which may make the molten weld to collapse, disfiguring the materials. There are two inert gases that are used with this process to minimize splatter; Tungsten Inert Gas (TIG) and Metal Inert Gas (MIG).
Plasma Welding
Plasma welding is an arc welding process that works in a similar fashion to thin gauge arc welding; the only difference here is that the plasma arc can be separated from the shielding gas envelope. The plasma is then squeezed through a fine-bone copper nozzle, which then constricts the arc. The process can be conducted through three main ways; Microplasma welding that is used for thin sheets as small as 0.1mm thick.
The second one is called Medium Current Welding that uses between 15-200A of current; it has deeper penetration. The last method is called Keyhole Welding, which is used on metal sheets up to 10mm thick.
Pros and Cons of using Robots for Welding
There is no denying the fact that robots are becoming more involved in the manufacturing process as time progresses. In some countries, they have replaced human labor entirely. There are advantages and disadvantages of using robots for welding, and they include the following.
The Pros
There is increased efficiency and productivity: Welding robots are precise in their work as they are programmed that way; there is very little room for errors. Their ability to do repetitive tasks over and over again without tiring increases productivity.
Shorter cycle times: As manufacturing becomes efficient, cycle times become shorter, which in turn means that more can be produced within that time frame compared to what was being made when relying on human labor.
Better floor Utilisation: Automating the workplace has reduced human footprint and, in turn, created more floor space for other things. One welding robot is able to do work that used to be handled by a group of people. With more space means there is more room for movement as well as the addition of new robotic welding machines.
Safety is increased: Human beings cannot maintain focus for too long; the more they work, the higher the lapse in concentration; this is what leads to accidents in places that use heavy machinery. Welding robots, on the other hand, can run for days without putting a single foot wrong. Accidents are no longer common in manufacturing factories due to this.
Reduced wastage: The high level of accuracy exhibited by robots is so efficient that there is very little left to be discarded. Human eros is the biggest contributor to waste in most manufacturing plants. With robots, however, most of the raw materials are utilized to the maximum.
The Cons
The initial cost of automation is very high: Considering the amount of industrial robot programming that goes into making robots coupled with the intricate tools needed for them to function properly, the cost of automating your plant is very high in the initial phase.
Training is necessary: As much as robots have taken over human positions, most still need to be operated and supervised by people. Training humans to operate these robots can be a very expensive affair that takes time given how sophisticated industrial robots can be. The same also applies to repairs and maintenance, only specialized experts can handle that type of work and they are limited in the market.
Decision making is limited: Sophisticated as they may be, robots lack the ability to make decisions, they simply operate based on the set of instructions fed into them by programmers. There are countless decisions that need that human factor at the workplace, something that current robots lack. With AI development picking up pace, there is hope that in the future robots will have that ability to think things through first.
Limited flexibility: Unlike humans who can be trained to handle two different roles in succession, most welding robots are too specialized for them to pull this off. They are programmed to satisfy the one niche they are dedicated to without any deviation. The only way a welding robot can switch roles is when they are deliberately re-programmed to do that.
The implementation period is long: Switching to robots does not happen with a wave of a hand. You first need to restructure your plant to accommodate them, then there is the issue of their delivery to the premise considering how heavy they are. You will also need expert help to set them up, all this followed by a trial period to make sure they are working as expected before production is resumed. You are looking at 20 weeks minimum before you go fully operational.
Robotic Welding Systems and Programming
Welding robots require specific software for them to execute their roles. This software is created by independent companies which then sell them to robot manufacturers. The following are some of the most popular robotic welding systems software.
Verbotics
Source: verbotics.com
Verbotics Weld is a simple but powerful welding software that can be run from any desktop. It is an offline setup that makes robotic welding an easy affair. It has a user interface that gives you a preview of how the welding robot can be controlled by the program. Verbotics is not free but it has a trial version that allows you to test-drive the software before making the final decision.
Almacam Weld
Source: almacam.com
Amalacam Weld is an offline welding robot software that allows manufacturers to optimize their welding robots to increase their efficiency. Almacam Weld has been in use for over 20 years and has improved over the years to become one of the most sought after welding software. One of the advantages of the software is that it is easy to install and does not require too much training for the operator to get the hang of it.
ABB
Source: new.abb.com
ABB is another offline welding software that is easy to use and implement at any workplace. It increases productivity on top of reducing risks while maximizing investments on all your robot systems. ABB is compatible with many welding robots and can be operated by anyone who can be trained to understand how it works.
Areas where Robotic Welding is Applied
Robotic welding is mostly used in manufacturing plants that deal with heavy machinery. Some of these industries include the following.
Automotive Industry
Source: Pixabay
The average car has over 5000 welded parts, that’s proof enough of how important automated welding systems are vital. The work used to be handled by humans but that resulted in uneven welding that made cars less efficient on the road. Modern car manufacturers cannot do without welding robots. The technology behind robotic welding is expected to improve further in the future.
Electronics Industry
Source: Pixabay
Computer motherboards are made of very tiny components that cannot be welded by hands. Robotic welding involved in the making of such items is highly advanced with the ability to weld even the tiniest thing that the naked eye will have trouble discerning. The use of robotic welding is the only way that can produce electronics as fast as their demand.
Oil Industry
Source: Pixabay
The huge pipes that are used to transport crude oil across huge distances rely on robotic welding to link them up since they have to be manufactured in sections. Another reason why robots are involved in welding the pipes has a slot to do with safety. The pipes have to be leak-proof to avoid explosions or leaks that may cause harm to people and the environment.
Aerospace Industry
Source: Pixabay
More than cars, airplanes require the most attention when manufacturing their parts considering the fact they have to stay airborne. To reduce errors, all the welding of airplane parts are done by highly advanced welding robots that are programmed to cover all parts. They are equipped with vision technology that they can use to detect any flaw.
Guide to Buying a Welding Robot
Source: Pinterest
The hardest part of automating your manufacturing business is deciding the right robot to go for. There are countless robot manufacturers in the world, each with unique products that promise the best results. Deciding what to go for requires a lot of research since robots cost a lot. It is the kind of investment you make once in a lifetime, therefore it has to be done right. The following is a guide on buying welding robots for your manufacturing plant.
Complexity
A good welding robot should be one that is easy to understand. Getting a welding robot that is too complicated may stop your production once they run into problems as it would require an expert to be brought in from the manufacturer to get it going on again. When selecting a welding robot, first ensure that it is simple enough for your in-house technician to handle it to save costs on repairs in the future.
Peripherals
Source: Pinterest
Some welding robots need add-ons for them to work, this is an added cost that should be avoided if you can. Go for a welding robot that comes in a whole package, with the ability to handle a myriad of functions without the need to spend more on buying other parts. If you have to buy one that needs accessories, make sure the parts in questions are easy to find locally.
Space Availability
Source: Pixabay
The number and the size of the welding robots you intend to acquire depend on the space available at your plant. When replacing human labor with robots, you will be forced to clear the floor in advance. The bigger space, the more the number of welding robots that can be fitted in and vice versa. If you were running a small factory and you intend to automate you will need bigger floor space.
Nature of Work
Source: Pinterest
Some manufacturing processes do not require advanced welding processes, but if you are in the kind of manufacturing that involves heavy metallic parts then robotic welding would be the most sensible route to take. Automotive manufacturing involves the use of heavy car parts that cannot be handled well by human labor, welding robots are the only option left in that industry.
Your Budget
Source: Pixabay
The cheapest heavy-duty industrial robot goes for about $50,000, you could get a used one for slightly less but the bottom line is, robots are expensive. As much as the end justifies the means in the long run, the initial welding robot cost of automating a manufacturing plant will run you into debts if you are not cautious. Besides the cost of purchasing them, you will also need money for training people, setting them up in the factory, and future repairs. It will be a while before you are able to return all the initial investment.
Flexibility
Most robots involved in manufacturing are task-oriented, i.e they are designed to handle a specific role. As much as this makes them efficient, it does limit their range and when you consider their cost, it would really help you a lot if you can get a factory robot arm that can handle more than one role. A welding robot that can also handle picking and placing would be a better investment compared to one that can only handle welding.
Availability
It will cost you more to import a specific type of welding robot if it cannot be found locally. If you happen to live near a major robot manufacturer you may be lucky enough to even place special orders for customized robots. The use of industrial robots is not as widespread in all areas, this makes industrial automation manufacturers to be concentrated in specific areas that may be located too far from where your plant is. Consider the cost of importing welding robots before making a choice.
Support
Source: Pinterest
After-sale support is vital when it comes to handling robots. They are machines like any other, only highly advanced. Regardless, they will eventually break down or malfunction after prolonged use. When this happens you will require help with them without having to fork out crazy amounts of money. Go for industrial robot manufacturers that are able to offer warranties as well as dedicated technical hope for a specific amount of time.
Spare Parts Availability
Source: Pinterest
Overused welding parts like end effectors are most likely to break down as they do most of the work. Any movable part is prone to the friction of some kind and even though it takes time, they will need replacements along the way. Select a welding robot whose spare parts are readily available at a moment’s notice. Lack of spare parts may bring production to a halt and that is one interruption you do not want to deal with.
Software Upgrades
Source: Pinterest
The availability of software upgrades is also another big factor that should help you narrow down on the type of welding robot you would want for your factory. Upgrades make the robots become more efficient, being stuck with a robot that is using software that is overdue may start affecting the quality of production. Go for robots that have constant software support all through with upgrades at least once a year.
Conclusion
Welding robots are among the most important industrial robots in the manufacturing space. Owing to the high heat involved in the process, the role is best executed by welding robots as they are able to handle and withstand heat more than people. If you plan to buy a welding robot for a manufacturing plant, pay a visit to the nearest welding robot manufacturer and get the best automated welding machine for your enterprise.
Also Read:
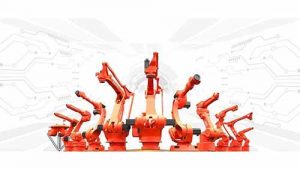
Welding Robot: A List of Best 10 Robotic Welding Company Brands
July 14, 2021
Read More »
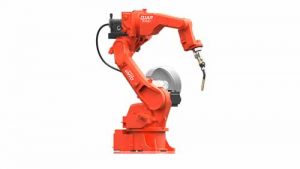
Robotic Welding Cell: What It Is and Where to Buy It
March 29, 2021
Read More »
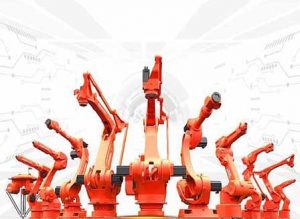
Best Welding Machine Manufacturers in Italy
October 20, 2020
Read More »