Dual-arm collaborative welders are robots with two working arms. These robots help make work faster, more accurate, and flexible. For example, Han’s Robot’s Elfin robots can position within ± 0.02 mm. This accuracy ensures steady, high-quality welding and solves worker shortages. Also, systems like the Dobot X-Trainer have a 25Hz motion interface. This makes them 150% faster than similar machines. With these features, dual-arm welders boost productivity and handle tough tasks with great precision.
Key Takeaways
- Dual-arm collaborative welders have two arms to work at once. This helps increase speed and efficiency in welding tasks.
- These robots use smart sensors and AI for better accuracy. They make high-quality welds and reduce mistakes in many jobs.
- Safety features let these welders work safely with people nearby. This makes them perfect for today’s factories.
- Buying dual-arm welders can save money over time. They lower labor costs and make production faster.
- They can switch tasks quickly, so they work well in many industries. These include car-making, airplanes, and electronics.
What Are Dual-Arm Collaborative Welders?
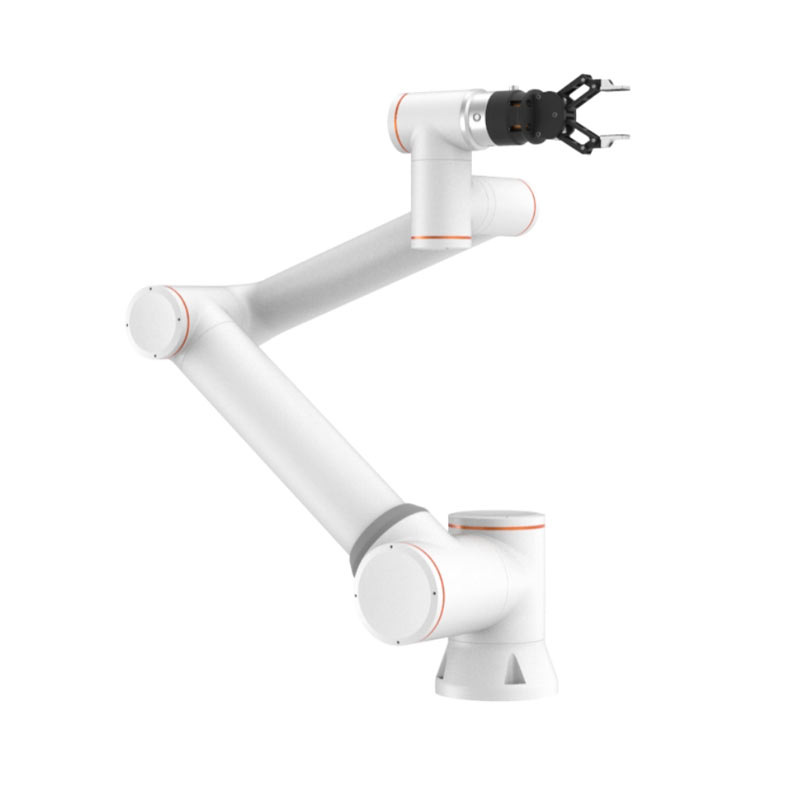
Definition and Overview
Dual-arm collaborative welders are robots with two arms for welding. These robots copy human movements to do precise, complex tasks. Unlike single-arm robots, they can work on two parts at once. This saves time and boosts productivity. For example, CoWelder has six movement axes for nonstop welding. This feature ensures accuracy and works well in many industries.
Key Features of Dual-Arm Collaborative Welders
Dual-arm collaborative welders have unique features that make them special:
- Two-Hand Operation: They use both arms to do tasks at the same time.
- Improved Cycle Times: They finish jobs faster by doing multiple tasks together.
- Flexibility: They can reach tricky spots from different angles easily.
- Integration with AI and Sensors: Smart sensors and AI help them weld precisely.
- Safety Features: Built-in safety allows them to work safely with people.
Manufacturer | Model | Description |
---|---|---|
Yaskawa Motoman | DIA10 | Handles materials automatically. |
ABB | YuMi | First-ever dual-arm collaborative robot. |
Kawasaki | duAro | Two-armed robot for many types of tasks. |
FANUC | Arcmate 120ic | Popular for dual-arm welding jobs. |
How They Differ from Traditional Welding Robots
Dual-arm welders are different from older welding robots. Older robots have one arm and need repositioning often. Dual-arm robots do two tasks at once, saving time and working faster. They are flexible and handle tough shapes better. Unlike older robots, these cobots work safely near humans. This makes them great for modern factories.
In industries like aerospace, where accuracy is key, these robots shine. Studies show 55% of manufacturers think automation can raise productivity by 20%. This proves how useful these robots are for meeting industry needs.
How Do Dual-Arm Collaborative Welders Work?
How the Two Arms Work Together
Dual-arm welders copy teamwork by using two robotic arms. Each arm can do its own job or work with the other. For example, one arm might hold a part steady while the other welds it. This teamwork saves time and avoids moving parts around too much.
These robots are great for jobs needing accuracy and multitasking. They can work on different parts of a project at the same time. This makes them very useful in car factories where speed and precision matter. By working together, these robots make tasks faster and more efficient.
Using Sensors and AI for Better Welding
Sensors and AI help dual-arm welders work more accurately. Sensors check things like heat and pressure to adjust welding settings right away. For example, touch sensors make sure the welding angle is correct. Cameras check the welds and spot mistakes. These tools keep the welds neat and reduce errors.
AI uses sensor data to make smart choices during welding. It finds problems early and fixes them to avoid defects. Cameras give location details, helping the robot adjust while working. Sensors and AI make welding better and speed up production by over 25%.
Keeping Workers Safe Around Robots
Safety is very important when robots work near people. Dual-arm welders have safety features to protect workers. Sensors watch for danger and stop the robot if needed. For example, if a person gets too close, the robot slows down or stops.
These robots are made to work safely with humans. Their smooth movements and smart controls lower the risk of accidents. This focus on safety builds trust between people and robots. It makes these welders a good choice for modern factories.
Metric | What It Means |
---|---|
Precision | Robots make welding more accurate by controlling speed and angle. |
Consistency | They keep welds the same quality, cutting down on mistakes. |
Safety | Safety features protect workers and prevent accidents. |
Efficiency | Robots can work all day, making more products faster. |
Productivity | Robots handle repeat tasks, boosting productivity and saving time. |
Flexibility | Robots can quickly switch to new tasks when needed. |
Benefits of Dual-Arm Collaborative Welders
Better Efficiency in Welding
Dual-arm collaborative welders make welding faster and smoother. They can do two jobs at once, like holding a piece steady while welding it. This saves time by reducing the need to move parts around. For example, in car factories, these robots weld car frames quicker than older methods, speeding up production lines.
These robots can work nonstop without breaks, unlike people. They keep producing the same quality all day and night. Their smart systems handle boring tasks, letting workers focus on harder jobs. This mix of multitasking and nonstop work makes them perfect for factories needing fast production.
Higher Precision and Steady Results
Welding robots are great at being precise and consistent. They use smart sensors and AI to check their work as they go. For instance, the SevenAxis TrackWeld Station scans 2000 frames per second. This helps it find gaps and join parts with amazing accuracy. It works well with different shapes like butt joints and T-joints.
These robots are very accurate, often within 0.5mm. This reduces mistakes and saves materials. They also track seams intelligently, making them good for tricky shapes. Their precision ensures top-quality welds, which is important in industries like aerospace and electronics.
Evidence Description | Measurement Data |
---|---|
Scanning frame rate | 2000 frames per second |
Precision | ≤0.5mm |
Real-time adjustments | Continuous monitoring |
Adaptability | Seam tracking for various geometries |
Flexible for Hard Welding Jobs
Dual-arm welders are very flexible for tough welding tasks. Their two arms can reach tight spots and handle tricky parts. This makes them useful in industries like construction and aerospace, where welding is often hard.
These robots can quickly switch between jobs. For example, in electronics, they can go from welding circuit boards to assembling parts. This quick change saves time and boosts efficiency. With their flexibility and accuracy, these robots solve many modern factory problems.
Tip: Using dual-arm collaborative welders can help your business work faster, make better products, and adapt to different tasks easily.
Cost-Effectiveness in Long-Term Operations
Dual-arm collaborative welders save money over time. They are a smart choice for businesses. The upfront cost may seem high, but they pay off fast. These robots boost productivity and lower running costs. For example, studies show they pay for themselves in two years with one shift. With three shifts, the payback time is just one year. This shows how cost-effective they are.
These robots cut labor costs by doing repetitive jobs nonstop. Workers can focus on harder, creative tasks instead. This lowers labor expenses and makes workers happier. Dual-arm welders also reduce waste by making precise welds. This saves money on materials.
Did you know? The Net Present Value (NPV) of dual-arm welders is €56,400 for one shift and €218,000 for three shifts. This proves their long-term value.
Maintenance costs for these robots are low. They are built to last and need fewer repairs. When repairs are needed, they are simple and cheap. Over time, these savings grow, making them a great choice for factories.
By using these robots, you save money and improve efficiency. They give steady results and lower costs, making them a key tool for modern factories.
Industrial Applications of Dual-Arm Collaborative Welders
Automotive Industry: Welding Car Frames and Components
The car industry uses welding cobots to meet high production needs. Dual-arm collaborative welders are key for building car frames and parts. These robots can hold and weld pieces at the same time. This ensures accurate and consistent results. For example, they weld tricky joints in car doors or frames with few mistakes. They work nonstop, making assembly lines faster.
Car makers gain a lot from these robots. They reduce the need for people to do repetitive tasks. Workers can then focus on harder jobs. Also, the safety features of these robots keep workers safe. By using dual-arm robots, car companies improve quality and work faster.
Manufacturing: Assembly Line Welding and Fabrication
In factories, welding cobots make assembly lines more efficient. These robots are great for welding metal parts and building complex items. Their two arms let them do more than one job at once. For example, one arm holds a part while the other welds it. This saves time during production.
These robots are flexible and fit many factory needs. They can easily switch between different tasks without much reprogramming. This helps factories keep up with changing demands. Their accuracy also reduces wasted materials, saving money and improving product quality.
Construction: Structural Welding for Buildings and Infrastructure
Dual-arm collaborative welders are changing how construction projects are done. They make structural welding faster and better. These robots handle tough jobs like joining steel beams or strengthening concrete. They can reach tight spots and keep welds consistent, which is great for big projects.
Safety is very important in construction. These robots lower risks by working in dangerous places. They can weld on high platforms or in small spaces, keeping workers safe. Their automation also speeds up projects, helping builders finish on time without losing quality.
Key Insight: The global market for dual-arm robots may pass $15 billion by 2030. The car industry could make up about 35% of this growth. This shows how more industries are using these robots.
Sector | Market Share by 2030 | Key Insights |
---|---|---|
Automotive | ~35% | Main reason for robot use is high automation in car assembly. |
Electronics | N/A | Important for precise tasks and assembly line work. |
Logistics | N/A | Growing use for sorting and moving materials efficiently. |
Overall Market | >$15 billion | Growth driven by better robotics and automation technology. |
Aerospace: Precision Welding for Aircraft Components
In aerospace, accuracy is very important. Dual-arm collaborative welders are great at this. They handle tricky jobs like welding lightweight metals or complex shapes. These robots keep welds even and meet strict aerospace rules. For example, TIG systems are perfect for delicate welds, making them essential in this field.
These robots also make welding safer. They have features like force sensors and collision detectors to protect workers and tools. They can do many tasks, like building fuselages or fixing turbine blades. This makes them very useful in making aircraft parts.
Benefit | Description |
---|---|
High precision for tricky welds | TIG systems give the accuracy needed for aerospace welding. |
Uniform quality for tough materials | Automation keeps welds even, meeting aerospace standards. |
Better safety | Sensors and collision detection keep workers and tools safe. |
Versatile for many tasks | These robots can handle different welding jobs in aerospace. |
Boosted productivity | Automation speeds up work while keeping welds strong. |
Electronics Industry: Welding Circuit Boards and Components
In electronics, welding cobots are key for making circuit boards. They are fast and precise, perfect for soldering tiny parts or delicate connections. With two arms, they can do more than one job at once. This saves time and makes work faster.
These robots work quickly and use energy efficiently. For example, they speed up production lines while keeping energy use steady. By automating simple tasks, they ensure quality and let workers focus on harder jobs.
- Faster work
- High speed
- Quick acceleration
- Steady energy use
Welding cobots can also adjust to different designs. Whether making phones, laptops, or other devices, they deliver great results. Their accuracy reduces mistakes, saving materials and cutting costs.
Medical Industry: Precision Welding for Medical Devices
The medical field needs accurate and reliable welding for tools like implants. Dual-arm collaborative welders meet these needs with steady, high-quality welds. They work well with delicate materials like titanium, ensuring strong and safe devices.
These robots are great for small, detailed welds. For example, they join tiny parts in pacemakers or build surgical tools with few mistakes. Their smart sensors and AI make real-time changes for better accuracy.
Safety is another big benefit. These robots have features like collision detection to keep workers safe. They also reduce human mistakes, improving the quality of medical tools. By using these robots, factories can work faster and meet strict medical standards.
Note: Dual-arm collaborative welders are changing industries by being precise, safe, and efficient. Their use in aerospace, electronics, and medical fields shows their value and flexibility.
The Future of Dual-Arm Collaborative Welders
New Trends in Robotics and Welding
Welding is changing with new technology. Automation is replacing old welding methods. Robots like welding cobots are solving problems like accuracy and speed. They also make welding better for the environment, which helps modern factories.
AI and machine learning are big trends in robotic welding. These tools help robots work smarter and do different jobs. For example, AI robots can check their work and fix mistakes fast. Collaborative robots are also making factories safer. They work with people to make production quicker and safer.
Industry 4.0 is another trend shaping welding. Smart sensors and IoT let robots talk to each other and make decisions. These technologies are changing how welding and manufacturing are done.
Growing Use in Different Industries
Dual-arm robots are becoming popular in many fields. They can do hard jobs with little help from people. Industries like healthcare, construction, and manufacturing are using these robots more. For example, in healthcare, they weld medical tools with great accuracy.
The market for welding robots is growing fast. It is expected to grow from $626 million in 2024 to $3.23 billion by 2033. This shows a 20.5% yearly growth from 2026 to 2033. This rise shows how much businesses want automated welding solutions.
These robots are also getting cheaper to use. Their ability to do many tasks makes them a smart choice for companies wanting to save money and work faster.
Smarter Robots with AI and Machine Learning
AI and machine learning are making welding robots better. These tools help robots learn and improve over time. For example, AI robots can find mistakes while welding and fix them. This keeps welds neat and reduces waste.
Machine learning also helps robots switch tasks quickly. You can reprogram them to do new jobs without long delays. This is helpful for industries that need to change tasks often.
AI combined with sensors is another exciting update. Sensors give real-time data like heat and pressure, helping robots adjust perfectly. This is very useful in fields like aerospace and electronics.
The future of welding robots looks bright. These robots will keep getting smarter, safer, and more useful in the years ahead.
Dual-arm collaborative welders are a big step in automation. They are precise, fast, and flexible for tough welding jobs. These robots copy teamwork to work better and give steady results. With AI and sensors, they are accurate and safe for many industries.
They are used in fields like cars, planes, and electronics. These robots help make more products while saving money. As technology grows, dual-arm welders will change welding. They will make factories smarter and more eco-friendly.
FAQ
1. How are dual-arm collaborative welders different from single-arm robots?
Dual-arm welders can do two jobs at once. For example, one arm holds a piece while the other welds it. This teamwork saves time and makes work faster. They are great for hard industrial tasks.
2. Are dual-arm collaborative welders safe to use near people?
Yes, they are built with safety in mind. Sensors notice when people are close and stop the robot if needed. Their smooth moves and collision detection keep the workspace safe. You can work with them without worry.
3. Can dual-arm collaborative welders do different welding jobs?
Yes, they are very flexible. You can program them to switch tasks easily. They can weld car parts, assemble electronics, or join medical tools. This makes them useful for many industries.
4. How do sensors and AI make welding more accurate?
Sensors check things like heat and pressure. AI uses this data to make smart changes during welding. For example, the robot can fix its angle or speed right away. This reduces mistakes and improves weld quality.
5. Are dual-arm collaborative welders worth it for small businesses?
Yes, they are a good investment. They may cost a lot at first, but they save money over time. They cut labor costs, waste less material, and work faster. Many businesses see savings in one or two years.
Tip: Try one robot first to see how it helps before buying more.