Enter the era of robotic glass handling, where precision meets persistence. These tireless workers are redefining what’s possible in glass logistics, offering a tantalizing glimpse into a future of zero breakage and zero downtime. It’s a game-changer that’s not just transforming operations but also safeguarding human workers and dramatically boosting efficiency. As we dive into the world of robotic glass handling, prepare to discover how this technology is shattering expectations and crafting a new paradigm for the industry.
In this post, we’ll explore the glass logistics revolution, unveiling how robots are bringing unprecedented precision to handling, eliminating downtime, enhancing safety, and driving productivity to new heights. We’ll also delve into the impressive cost savings and return on investment that make this technology a must-have for forward-thinking businesses. So, let’s embark on this journey to understand how robots are not just handling glass—they’re reshaping the very future of logistics.
The Glass Logistics Revolution
A. Traditional challenges in glass handling
Glass handling has long been a delicate and risky operation in the logistics industry. The fragile nature of glass products presents unique challenges that have plagued manufacturers and distributors for decades. Here are some of the key issues faced in traditional glass handling:
-
High breakage rates
-
Worker safety concerns
-
Inconsistent handling techniques
-
Limited productivity due to careful manual processes
Challenge | Impact |
---|---|
Breakage | Increased costs, waste, and customer dissatisfaction |
Safety | Potential injuries, higher insurance premiums |
Inconsistency | Quality control issues, customer complaints |
Low productivity | Reduced output, longer lead times |
B. Enter the robotic workforce
The introduction of glass handling robots has revolutionized the industry, addressing many of the traditional challenges. These sophisticated machines are designed specifically for the precise and delicate task of handling glass products. Key benefits include:
-
Precision movements
-
Consistent handling techniques
-
24/7 operation capability
-
Reduced human error
C. Zero breakage: A new industry standard
With the implementation of glass handling robots, the industry is now moving towards a zero-breakage standard. This paradigm shift is transforming glass logistics in several ways:
-
Virtually eliminated product damage during handling and transportation
-
Significant reduction in waste and associated costs
-
Improved customer satisfaction due to perfect product delivery
-
Enhanced reputation for reliability in the supply chain
The zero-breakage standard is not just a lofty goal but a achievable reality with robotic systems. As we explore further, we’ll see how these robots maintain continuous operations, eliminating costly downtimes in glass logistics.
Precision and Consistency in Robotic Handling
Advanced sensors and computer vision
Robotic systems in glass logistics leverage cutting-edge sensors and computer vision technology to achieve unparalleled precision. These advanced systems enable robots to accurately detect, analyze, and handle various glass types with exceptional consistency.
Sensor Type | Function | Benefit |
---|---|---|
3D Cameras | Depth perception | Precise positioning |
Infrared Sensors | Edge detection | Accurate glass sizing |
Force Sensors | Pressure monitoring | Gentle handling |
Customized end-of-arm tooling
Glass handling robots utilize specially designed end-of-arm tools to cater to different glass shapes, sizes, and weights. These customized tools ensure:
-
Optimal grip strength
-
Even pressure distribution
-
Minimal risk of scratches or breakage
Adaptive gripping technologies
Modern glass handling robots employ adaptive gripping mechanisms that adjust in real-time to the specific characteristics of each glass piece. This adaptability allows for:
-
Secure handling of various glass thicknesses
-
Compensation for different surface textures
-
Adjustments for weight distribution
Real-time adjustments for varying glass types
The integration of AI and machine learning enables glass handling robots to make split-second adjustments based on the unique properties of each glass item. This capability ensures:
-
Consistent handling across diverse glass products
-
Reduced risk of errors or mishaps
-
Optimized workflow for different glass types
With these advanced features, glass handling robots offer unmatched precision and consistency, significantly reducing the risk of breakage and improving overall efficiency in glass logistics operations.
Continuous Operations: The End of Downtime
24/7 robotic performance
Glass handling robots are revolutionizing the industry by providing uninterrupted operations. Unlike human workers, these tireless machines can work around the clock without breaks, fatigue, or shift changes. This continuous performance translates to significant productivity gains and ensures a steady flow of production.
Aspect | Human Workers | Glass Handling Robots |
---|---|---|
Working Hours | 8-12 hours/day | 24 hours/day |
Breaks | Regular breaks needed | No breaks required |
Fatigue | Increases over time | Consistent performance |
Shift Changes | Necessary | Not applicable |
Predictive maintenance strategies
To maintain the 24/7 operation of glass handling robots, implementing predictive maintenance strategies is crucial. These advanced techniques use data analytics and machine learning to:
-
Monitor robot performance in real-time
-
Detect potential issues before they cause breakdowns
-
Schedule maintenance during planned downtimes
-
Extend the lifespan of robotic equipment
By adopting predictive maintenance, glass manufacturers can minimize unexpected disruptions and optimize their maintenance schedules.
Rapid changeovers for different product lines
Glass handling robots excel in their ability to quickly adapt to different product lines. This flexibility allows for:
-
Reduced setup times between production runs
-
Increased product variety without compromising efficiency
-
Seamless integration of new product specifications
With rapid changeovers, glass manufacturers can respond swiftly to market demands and maintain a competitive edge. The adaptability of these robots ensures that production lines remain operational with minimal interruptions, further contributing to the concept of continuous operations.
Safety First: Protecting Human Workers
Reduced workplace injuries
Glass handling robots have revolutionized workplace safety in the glass logistics industry. By taking on the most hazardous tasks, these robots significantly reduce the risk of injuries to human workers. Here’s how robotic systems are making a difference:
-
Elimination of heavy lifting
-
Prevention of cuts and lacerations
-
Reduction in repetitive strain injuries
-
Minimized risk of falls and slips
Injury Type | Reduction Rate |
---|---|
Back strains | Up to 80% |
Cuts | Up to 95% |
RSI | Up to 70% |
Falls | Up to 60% |
Collaborative robots in shared spaces
Modern glass handling robots are designed to work alongside humans safely. These collaborative robots, or cobots, use advanced sensors and AI to detect human presence and adjust their operations accordingly. This enables:
-
Flexible workspace arrangements
-
Enhanced human-robot teamwork
-
Improved overall productivity
-
Safer interactions between humans and machines
Enhanced safety protocols with robotic integration
Integrating glass handling robots into existing workflows necessitates a comprehensive review and upgrade of safety protocols. This process leads to:
-
Implementation of advanced safety barriers and zones
-
Regular safety audits and risk assessments
-
Improved emergency stop mechanisms
-
Continuous monitoring and data analysis for proactive safety measures
By prioritizing safety through robotic integration, glass logistics companies not only protect their workers but also create a more efficient and productive work environment. The reduction in workplace injuries translates to lower insurance costs, decreased downtime, and improved employee morale, making the adoption of glass handling robots a win-win solution for both employers and employees.
Boosting Efficiency and Productivity
Increased throughput rates
Robotic systems in glass logistics significantly boost throughput rates, revolutionizing the industry. These automated solutions can handle glass products with unparalleled speed and precision, far surpassing human capabilities. A single glass handling robot can process up to 1000 units per hour, depending on the size and complexity of the glass items.
Optimized warehouse space utilization
Glass handling robots excel at maximizing warehouse space efficiency. Their ability to stack items higher and closer together allows for a more compact storage arrangement. This optimization can lead to:
-
30-40% increase in storage capacity
-
Reduced need for warehouse expansion
-
Lower operational costs
Streamlined inventory management
Robotic systems bring a new level of accuracy to inventory management in glass logistics. They eliminate human errors in stock counting and tracking, resulting in:
Benefit | Impact |
---|---|
Reduced inventory discrepancies | Up to 99% accuracy |
Improved order fulfillment | 25-30% faster processing |
Lower carrying costs | 15-20% reduction |
Real-time tracking and reporting
Glass handling robots equipped with advanced sensors and IoT technology provide real-time data on inventory levels, product movement, and operational efficiency. This continuous flow of information enables:
-
Proactive maintenance scheduling
-
Instant identification of bottlenecks
-
Data-driven decision making for process improvements
By leveraging these capabilities, companies can achieve unprecedented levels of efficiency and productivity in their glass logistics operations. The integration of robotic systems not only accelerates processes but also enhances overall supply chain visibility and control.
Cost Savings and ROI
Reduced product loss and waste
Implementing glass handling robots significantly reduces product loss and waste in the logistics process. These precision-engineered machines minimize breakage, resulting in substantial cost savings. Here’s a breakdown of the benefits:
-
Consistent handling: Robots maintain a steady grip, reducing drops
-
Precise movements: Programmed paths eliminate accidental collisions
-
Gentle placement: Controlled force prevents chips and cracks
Traditional Method | Robotic Handling |
---|---|
5-10% breakage rate | <1% breakage rate |
High waste disposal costs | Minimal waste management |
Frequent reorders | Optimized inventory |
Lower insurance premiums
Glass handling robots lead to fewer accidents and claims, resulting in lower insurance premiums. Insurance companies recognize the reduced risk and offer more favorable rates to businesses using robotic systems.
Long-term labor cost reduction
While the initial investment in glass handling robots may be significant, the long-term labor cost reduction is substantial:
-
Reduced workforce needs
-
Elimination of overtime during peak periods
-
Lower training and turnover costs
-
Consistent productivity without fatigue
Improved quality control
Robotic systems enhance quality control in glass logistics:
-
Integrated sensors detect defects
-
Consistent handling preserves product integrity
-
Automated tracking and reporting
-
Reduced human error in inspection processes
By implementing glass handling robots, companies can expect a significant return on investment through reduced losses, lower insurance costs, labor savings, and improved product quality.
Future-Proofing Glass Logistics
Scalable robotic solutions
Robotic systems in glass logistics offer unparalleled scalability, adapting seamlessly to fluctuating production demands. These flexible solutions can be easily expanded or reconfigured to accommodate changes in glass types, sizes, or production volumes.
Scalability Feature | Benefit |
---|---|
Modular design | Easy expansion of robotic systems |
Programmable logic | Quick adaptation to new glass products |
Cloud connectivity | Remote monitoring and updates |
Integration with Industry 4.0 technologies
Glass handling robots are at the forefront of Industry 4.0, integrating seamlessly with advanced technologies:
-
IoT sensors for real-time monitoring
-
AI-driven predictive maintenance
-
Big data analytics for process optimization
-
Augmented reality for enhanced operator training
This integration ensures that glass logistics operations remain cutting-edge and continuously improve over time.
Adapting to changing market demands
As market demands evolve, robotic systems in glass logistics can swiftly adjust:
-
Rapid reprogramming for new glass products
-
Flexible end-of-arm tooling for diverse handling needs
-
Machine learning algorithms for optimizing handling strategies
Environmental benefits of robotic efficiency
Robotic efficiency in glass handling contributes significantly to environmental sustainability:
-
Reduced energy consumption through optimized movements
-
Minimized waste due to precise handling and reduced breakage
-
Improved material utilization through data-driven processes
By future-proofing glass logistics with robotic solutions, companies can ensure long-term competitiveness, adaptability, and sustainability in an ever-changing market landscape.
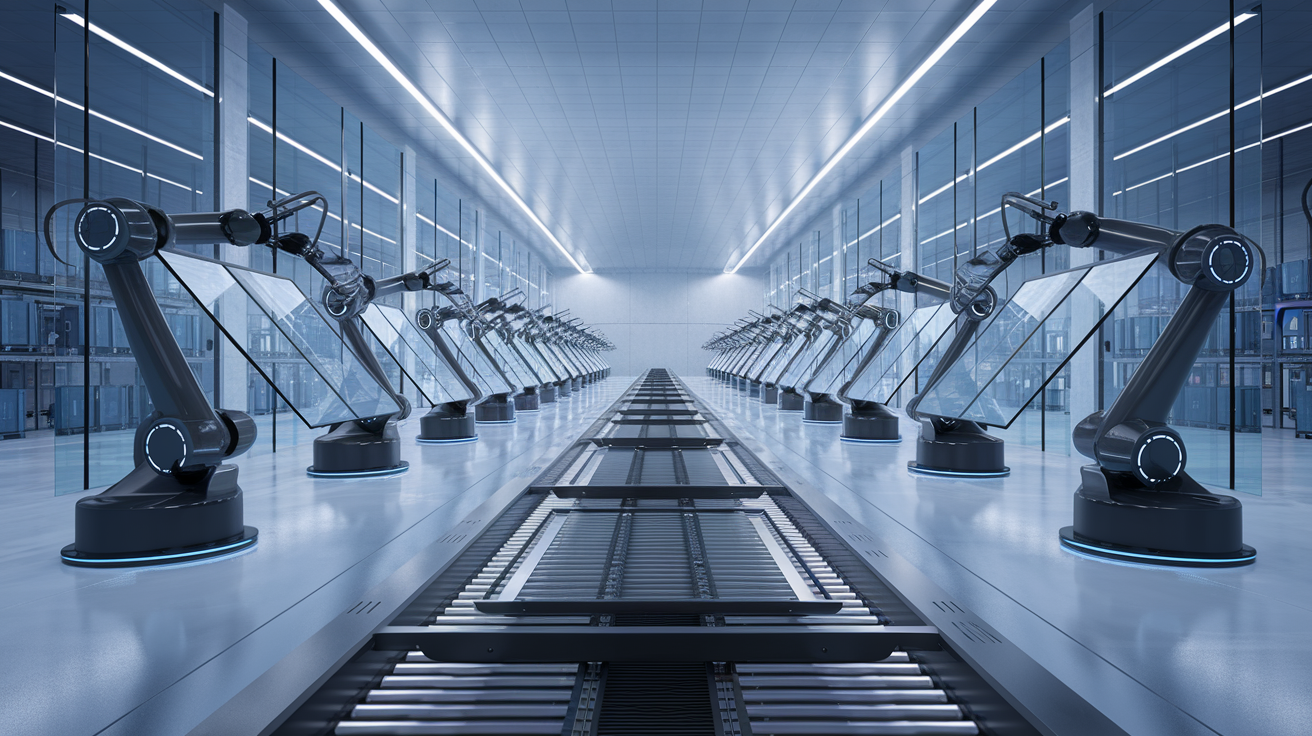
As the glass industry continues to evolve, embracing robotic solutions is no longer just an option—it’s a necessity for staying competitive. By future-proofing their operations with advanced robotics, companies can ensure they remain at the forefront of innovation, meeting the ever-increasing demands of the market while maintaining zero breakage and zero downtime. The time to act is now; invest in robotic glass logistics to secure your company’s place in the industry’s future.